Are current shipbuilding cost estimation methods ready for a sustainable future? A literature review of cost estimation methods and challenges
Abstract
In the fiercely competitive shipbuilding industry, precise cost estimates must be considered as they serve as a critical input for determining market prices effectively and ensuring a small profit for the shipyard. In Western Europe, where most projects are Engineering-To-Order (ETO), cost estimations are extra challenging, due to lack of similarity between projects. On top of this, cost estimations are becoming increasingly difficult in a market confronted by mounting challenges related to safety regulations, cost-effectiveness, and the pressing need to address energy conservation and environmental protection. New technologies introduce changes in nearly all aspects of shipbuilding design and construction. This article conducts a literature review, to present the state-of-the-art methods for estimating man-hours, explicitly focusing on man-hours for shipyard production, excluding overhead costs and challenges the suitability of existing systems for ETO and especially for the changes caused to ships by the energy transition. An indication is given of the practicality of each method as outlined in the literature. A solution direction, incorporating the construction process, is proposed to improve cost estimations for ETO projects in pre-contract phase.
1.Introduction
The profit margins in the European shipbuilding industry are really low. The most recent competitiveness study [25] from 2009, indicating a 2–6% profit margin. According to the research of Kamola-Cieślik [39], concluding that the shipbuilding industry in Europe is having difficulties staying in business, and the profit margins have not increased since. Therefore, correct, and accurate cost estimation techniques are vital for a company to do sustainable business. Considering that European shipbuilders are increasingly focusing on innovative and highly complex ships [73], the risk of making no revenue increases.
In the fiercely competitive arena of shipbuilding [45], swift adaptation to an ever-changing market becomes a vital necessity [74,78]. In addition to the imperative of improving production efficiency, in an effort to improve profits, the sector is confronted with mounting challenges related to safety regulations, cost-effectiveness, and the pressing need to address energy conservation and environmental protection [77]. All of this adds to the challenges associated with estimating costs, not only for Engineering-To-Order projects.
The likelihood of generating no revenue is particularly accentuated for projects requiring Engineering-To-Order services. By Engineering-To-Order (ETO), we refer to the process that leads to designing and constructing a customer-specific product. Hence, it is necessary to carry out design and engineering activities to meet a customer’s requirements. In the pre-contract phase of an ETO project, customer requirements and specifications still need to be discovered in detail, resulting in an immature design. This dilemma is found in every ETO construction project [22,85], but it is even stronger in a shipbuilding ETO situation, mainly because of the high engineering complexity and the long lead time [85]. For a yard, an ETO project means they must deal with several challenges arising from applying new systems and technologies, changes in the construction process and supply chain, and dealing with the chance of significant design changes during the project. Design changes often arise from customer involvement [17,22,42] and introduce waste in engineering design [37]. Design changes that occur during a project impact on previously established cost estimates. This is primarily because the design is a foundation for building and calculating cost estimates.
Nowadays, the maritime industry is confronted with an energy transition. This transition is an approach to ensure that the latest advancements in clean power sources, technology, and operational efficiency are utilized to decrease the industry’s environmental footprint [6]. The energy transition, involving the introduction of new systems and new regulations, presents an extra challenge when it comes to cost estimations.
Another crucial aspect is that the available design information is limited before signing the contract. And because of the uniqueness of an ETO project, only a few useful past performance product information is available [4,56]. Therefore, a comparison and extrapolation of known product data from previous projects cannot be made straightforward. Despite the uncertainties mentioned above, the cost estimate must be accurate. Accuracy is of importance for both shipyards and clients.
The level of information at the contract stage, available for cost estimation, depends on how much effort shipyard’s decision makers are willing to put into issuing a tender. The design information available in the contract is generally limited to a general layout drawing, the so-called general arrangement. They cover information about the hull shape, number and heights of decks, locations of rooms, and type and location of the main equipment.
Information on the weight distribution and further functional and technical requirements are also available. The contract also contains delivery planning, implying that a shipyard construction strategy is known. That means dividing the design into building blocks and manufacturing main processes is known [4]. Figure 1 illustrates that the available design information increases as the project progresses.
Fig. 1.
The dotted line is the moment of signing the ETO contract. At that moment design information is limited. When moving from concept design to eventually constructing a ship, available information increases. When a contract is signed information is available on the level of a general arrangement. After the contract is signed the basic design starts and more information becomes known about e.g., components and construction elements. In the next phase, detailed design, and detailed construction information is produced.
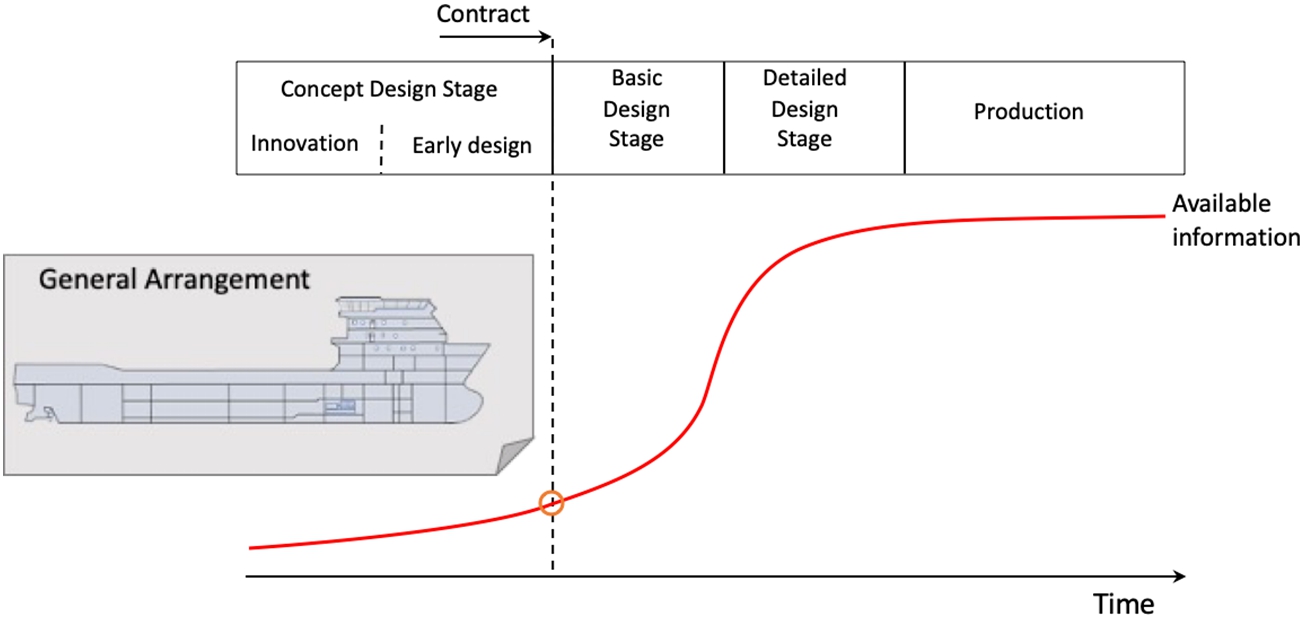
In an ETO project, customer involvement begins with signing the order and continues through the design phase. Given that multiple companies collaborate in an ETO shipbuilding project, from design to commissioning [4], the suppliers’ composition varies for each ETO project, and the supply chain process is customized accordingly.
The systematic review of Fatouh and Rego [29] showed that, despite the high-risk profile, research addressing ETO in shipbuilding is scarce. This also applies to research addressing cost estimation specifically for ETO projects in other industries, as concluded by Kjersem [42]. Of course, cost estimations are made for ETO projects, but a substantiated development direction of cost estimation methods is not found in the present review.
All cost estimation methods found in the literature aim to produce an accurate and correct estimation. They are using design information, construction techniques, and past performance information. The cost estimation methods used often differ per project phase [63]. As a result, accurately calculating the cost implications becomes a daunting task when design changes occur. As mentioned, design changes during a project are widespread in ETO projects.
Furthermore, the lack of a reference base, which is the case for ETO projects, presents an additional challenge for known cost estimation methods. It becomes extra challenging when introducing new systems requires another construction procedure.
Hence, the research question posed: “What cost estimation methods are currently available and capable of estimating accurately Engineering-To-Order projects in the pre-contract phase?”
In this review, our focus is on estimating methods related to man-hours needed for projects. Man-hours are something that shipyards can directly control, unlike material and component costs, which are governed by external market prices. Although, commonly, many sub-contractors are involved, labor costs under the direct control of the shipyard still account for roughly 20% of a ship’s construction [10,51]. Additionally, 50%-60% of the labor cost is directly related to the cost of constructing a ship’s hull [15].
To explore this, we provide a brief historical overview of how cost estimation methods have evolved. In the following chapters, we first give a justification of the literature review followed by a description of ETO characteristics, and after that, based on a literature review, we go into the different cost estimation methods used in the shipbuilding industry and their application for the pre-contractual stage of Engineering-To-Order projects. The review concludes with a direction for future research and avenues to follow.
2.Short history of cost estimation methods
During the 19th and first half of the 20th centuries, ships were constructed directly on the slipway, starting with the keel laying and constructing the ship from the bottom up as an ongoing process. Cost estimates for the significant labor processes – plate and profile preparation, riveting, caulking, and drilling – were based primarily on informal, personal cost engineering techniques. These estimates were usually generated by the yard manager using formulae derived from the main dimensions of the vessel, including its total weight, length, width, and height [50].
In the second half of the 20th century, new cost estimations emerged forced mainly by the increasing competition, and several fundamental changes. One of the reasons that changed the estimation approach was the change in the construction method made possible by, among other things, improved welding techniques.
From roughly 1930 until 1960, riveting was replaced by welding. The cost calculation parameters, like the number of rivets and meters of caulking, were no longer helpful. Cost estimators had to modify their cost calculation according to the welding of structures, using welding length as a determining factor.
After the late 1960s, not only construction techniques but also construction methods transformed. In 1969, Myers [58] introduced the modular construction concept in the US. This technique, also known as block construction, is now widely used when constructing large seagoing vessels [58,76].
The modular construction method revolutionized how work was organized. This ushered in the use of Work Breakdown Structures (WBS) to track and manage expenditure in terms of man-hours [62]. Estimations of effort also shifted from estimations for a particular profession to estimations about a specific group of tasks [1]. To ensure accurate cost estimations based on past performance, an activity-oriented time registration became necessary to be linked with the WBS. This practice is commonplace today, making it possible to refine man-hour estimations.
The increasing availability of structured information, mainly caused by the emergence of Computer-Aided Design (CAD) in the 1980s, triggered the search for method improvements. Among them, the Product Work Breakdown Structure (PWBS) stands out by allowing costs to be broken down into modular construction elements. A comprehensive review of the WBS initiatives commonly used for estimating man-hours in shipbuilding is provided in the work of Abd Rahman, Zaki and Husain [1]. In this work, they concluded that the Product Work Breakdown Structure is the best methodology for scheduling and cost estimation because man-hours are easy to identify.
A driving force behind the development of new cost estimation methods is the increasing computer power. Storage and processing capacity are no longer obstacles to introducing new estimation algorithms [51]. It enables the integration between design and Computer Aided Manufacturing [68,76] which can be used in cost estimations.
The combination of improved hours administration and increased computer power made it possible to determine and include other parameters in the cost estimates. Cost estimation methods were developed based on static analyses of previously completed projects. This has led to one of the commonly used parameters for steelwork, namely the weight of a ship or parts of the ship. The productivity figure man-hours per ton was expressed. The production factor inch/meter for piping has also emerged based on static analyses. Production factors based on static analyses are based on the principle that previously realized similar (partial) products have the same costs.
A force, that also influences the way a ship is going to be built, is the chosen ship systems. Nowadays, new energy systems are introduced, mainly as a result of new challenges related to sustainability [78]. This introduces changes in the shipbuilding design and construction process and, thus, how costs are estimated and how costs are recorded.
Changing a cost estimation method has many consequences and can be challenging to implement. First of all, when changing from a method, new experience-based estimator knowledge must be built, new cost recording and cost control methods must be introduced, and historical performance information must be re-engineered or barely usable. Barely usable because historical performance information is based on requirements coming forth from the previously used estimation method. Of which the cost recording is based on different data and data structures than what is required by a new method.
3.Literature review method
The primary objective of the literature review is to identify publications over the last 20 years concerning cost estimation methods. And to uncover the latest trends and future directions in cost estimation methods for Engineering-To-Order projects in the shipbuilding industry and discuss their ability to deal with new or out-of-experience inputs.
The first selection is based on the criteria “Cost estimation” AND (“shipbuilding” OR “ship building” OR “Vessel construction”). Using the Scopus database, this resulted in a set of 207 documents. Many shipbuilding innovations are not published in regular academic sources but often only at conferences, a broader search was preferred. Therefore, Google Scholar was used with the same selection criteria resulting in a set of 1920 publications. These publications included the set that was found using Scopus.
In Fig. 2, it is shown that the number of new publications over the last two decades, which refer to cost estimation, has increased significantly. This statement illustrates the ever-growing relevance of the subject, underscoring its status as a vibrant and important field of study.
Fig. 2.
Number of new publications that refer to cost estimation in shipbuilding per year since 2003.
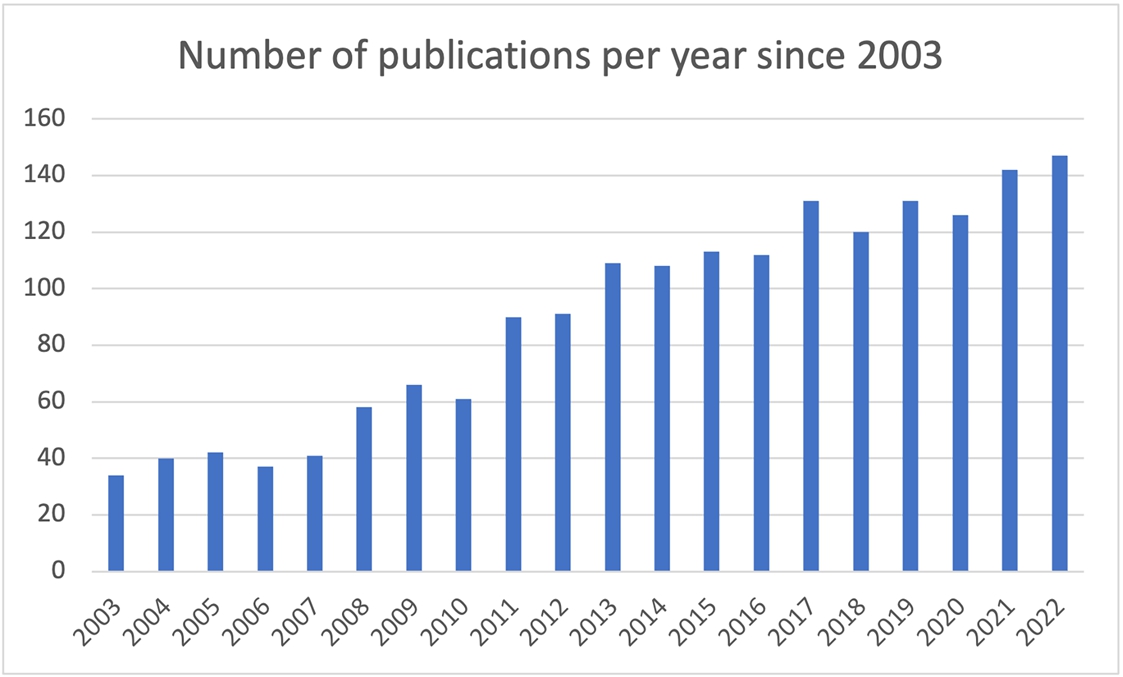
The review focuses on cost estimation methods; therefore, the selection criteria were narrowed down by adding the criteria “cost estimation method”, resulting in a set of 80 relevant publications. Figure 3 illustrates the publication selection flow.
Fig. 3.
Publication selection flow.
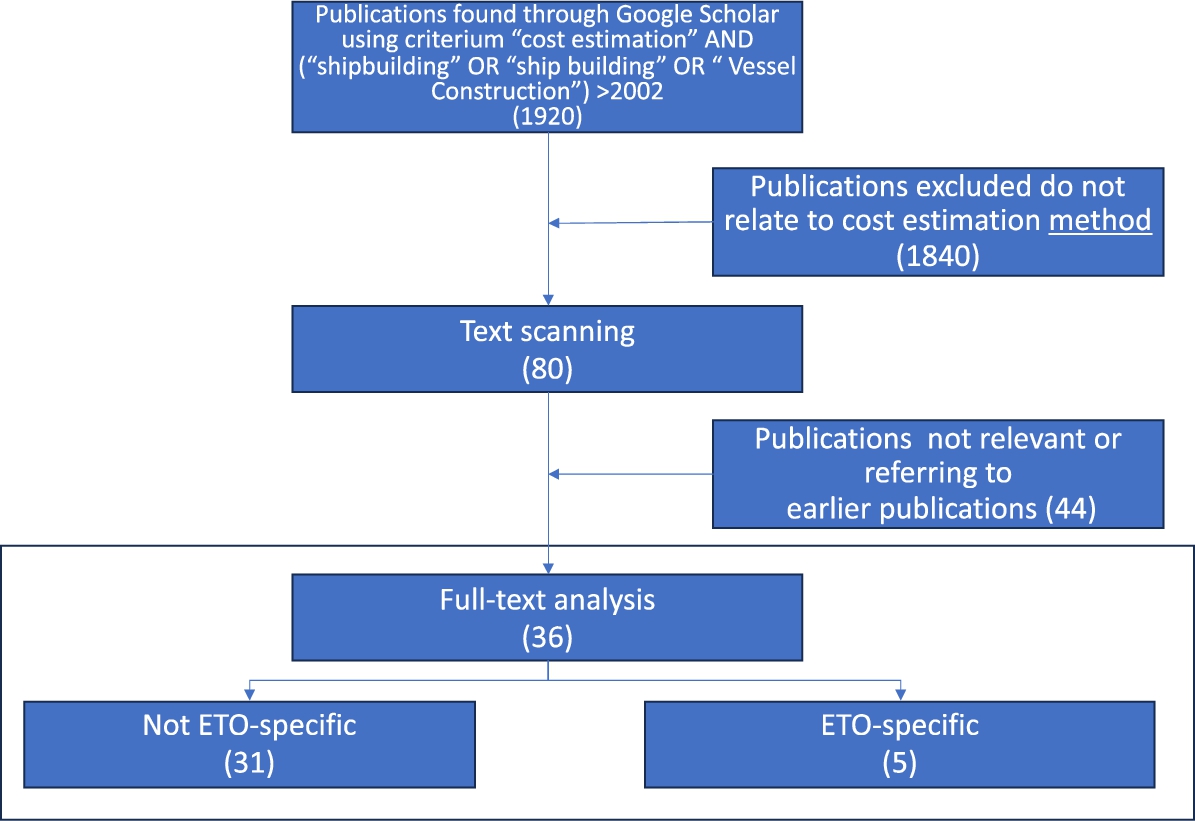
The analysis of 80 publications was focused on evaluating their relevance in cost estimation methods. Relevance was determined by carefully examining the abstract, discussion, and conclusion paragraphs. Out of the 80 publications, 44 of them are deemed irrelevant for a variety of reasons. Among these, 14 publications merely mentioned another publication from the same set of 80 as a reference without providing any substantial additional information or content. The other 30 publications were irrelevant because they focused on other aspects of the Shipbuilding industry. Aspects like maritime market development, slipway development, cost management process, and manufacturing software. As a result, a subset of 36 publications was identified. This subset was then subjected to further study. The main objective of this study was to analyze the improvement direction of known cost estimation methods and the application domain of the methods. The findings from the analysis of the 36 publications have been incorporated into Table 1. This table gives the publication, the publication source, the type of publication, and a short description of the direction for improvement.
Table 1
Publication overview containing publication year, publication source and type, improvement direction and applicability
Year | Title-[ref] | Source and publication type | Improving cost estimation method | Applicability |
2003 | Activity-based cost management for design and development stage. D. Ben-Arieh and L. [5] | International journal of production economics | Incorporating design | General shipbuilding, manufacturing |
2004 | Cost estimation of functional and physical changes made to complex systems. P. N. Jeziorek [36] | Massachusetts Institute of Technology, master thesis | Incorporating requirements | General shipbuilding |
2004 | A practical approach for ship construction cost estimating. J. M. Ross [66] | COMPIT’04 2004, proceeding | Improving cost estimation process using SWBS as structure | General shipbuilding, cost estimation software |
2005 | Weight-based cost estimating during initial design, J. Ross [65] | COMPIT’05 2005, proceeding | Improving weight estimation | General shipbuilding |
2006 | Cost assessment at concept stage design using parametrically generated production product models. M. Bole [9] | International Conference on Control, Automation and Systems, proceeding | Incorporating SWBS | General shipbuilding |
2006 | Estimation of ship construction costs, A. Miroyannis [55] | Naval Architecture and Marine Engineering, master thesis | Improving complexity measurements | General shipbuilding |
2008 | Cost management in shipbuilding. J. O. Fischer and G. Holbach [30] | COSTFACT GmbH, book | No method improvement mentioned | General shipbuilding, cost estimation software |
2008 | Steel Hull Shipbuilding Cost Structure. M. Leal [47] | Universidade tecnica de lisboa Portugal, master thesis | Practical application. No method improvements | General shipbuilding |
2008 | A simple model for estimating newbuilding costs. R. F. Mulligan [57] | Maritime Economics & Logistics, journal | Improvement of cost model figures per ship type | General shipbuilding |
2008 | Updating MIT’s cost estimation model for shipbuilding. M. B. Smith [72] | Massachusetts Institute of Technology, master thesis | Combining two cost models | Naval |
Table 1
(Continued)
Year | Title-[ref] | Source and publication type | Improving cost estimation method | Applicability |
2009 | Multi-criteria decision support for cost assessment techniques in shipbuilding industry. J.-D. Caprace and P. Rigo [14] | COMPIT’09, proceeding | Selection of appropriate cost estimation-method | General shipbuilding |
2010 | Cost Effectiveness and Complexity Assessmentin Ship Design. J. D. Caprace [15] | Université de Liège, doctoral thesis | Improving complexity measurements and incorporating design in cost estimation. | General shipbuilding |
2011 | An application of data mining algorithms for shipbuilding cost estimation. B. L. Kaluzny, S. Barbici, G. Berg, R. Chiomento, D. Derpanis, U. Jonsson, et al. [38] | Journal of Cost Analysis and Parametrics, proceeding | Improving by using data mining principles | General shipbuilding |
2011 | Configuration estimation method for preliminary cost of ships based on engineering bills of materials. M.-j. Son, S. C. Lee, K.-c. Kwon, T.-w. Kim and R. Sharma [74] | Journal of marine science and technology | Improving by introducing configuration estimation | Based on ship types |
2012 | A case of cost estimation in an engineer-to-order company moving towards mass customisation. D. Brunoe and P. Nielsen [11] | International Journal of Mass Customisation | Focus on Engineering-To-Order. Improvements by introducing backward elimination of variables with least impact. | General shipbuilding |
2012 | Towards a short time “feature-based costing” for ship design. J.-D. Caprace and P. Rigo [13] | Journal of marine science and technology | Improvement cost effectiveness by incorporating cost consequences in design | General shipbuilding |
Table 1
(Continued)
Year | Title-[ref] | Source and publication type | Improving cost estimation method | Applicability |
2013 | Cost engineering and costing in Hawthorn Leslie Shipbuilders, 1886–1915. T. McLean [82] | The British Accounting Review | No improvement, historical description | A specific shipyard |
2014 | Cost prediction via quantitative analysis of Complexity in US Navy shipbuilding. A. T. Dobson [23] | Massachusetts Institute of Technology, master thesis | Focus on Engineering-To-Order. Refining cost estimation for US Naval | Naval |
2014 | A building cost estimation method for inland ships. R.G. Hekkenberg [33] | European inland waterway navigation conference, proceeding | Introduces PM rules of thumb for inland ships | Inland ships |
2014 | Improving the parametric method of cost estimating relationships of naval ships. U. J. U. Lee [34] | Massachusetts Institute of Technology, master thesis | Improvement cost effectiveness by quantifying density factors | Naval |
2014 | Shipbuilding Cost Estimation: Parametric Approach. H. Shetelig [70] | Norwegian University of Science and Technology. Department of Marine Technology, master thesis | Improvement cost estimations by introducing the relative change Cost Estimating Relationship variable | General shipbuilding |
2015 | A study on the man-hour prediction system for shipbuilding. M. Hur, S.-k. Lee, B. Kim, S. Cho, D. Lee and D. Lee [34] | Journal of Intelligent Manufacturing | Improvement cost estimation results by looking at period of production | General shipbuilding |
2016 | Early estimation of work contents for planning the one-of-a-kind production by the example of shipbuilding. J. N. Sikorra, A. Friedewald and H. Lödding [71] | MATEC Web of Conferences, proceeding | Focus on Engineering-To-Order. Improvement by generating bill-of-material | General shipbuilding, |
Table 1
(Continued)
Year | Title-[ref] | Source and publication type | Improving cost estimation method | Applicability |
2016 | Sandwich construction for ship superstructure: cost estimation and failure prediction. P. Yu [87] | Memorial University of Newfoundland, master thesis | Improvement by refinement of formulas based on material type | Construction material |
2017 | Hull’s manufacturing cost structure. M. Leal and J.M. Gordo [48] | Brodogradnja: Teorija i praksa brodogradnje i pomorske tehnike, journal | Improvement cost structure for hull manufacturing | General shipbuilding |
2017 | Feature-based estimation of preliminary costs in shipbuilding. [49]C.-K. Lin and H.-J. Shaw, Ocean Engineering 2017 Vol. 144 Pages 305–319 | Ocean Engineering, journal | Improvements by introducing additional cost items | General shipbuilding |
2018 | Similarity-based Cost Estimations for. G. Alblas, J. CoenenETO-Products [2] | Advances in Manufacturing Technology, proceeding | Focus on Engineering-To-Order. Improvement suggested by taking construction process form into account | General shipbuilding |
2019 | A review of work breakdown structure and man-hours estimation method used in shipbuilding production. W. W. Abd Rahman, N. M. Zaki and M. A. Husain [1] | International Journal of Mechanical Engineering and Technology | Improvement suggested by using PWBS for cost estimation | General shipbuilding, work breakdown structure |
2019 | An Expert System for Cost Estimation of Shipyard Steel Assembly. M. Deul, B. Hoek, S. Moussault, A.-L. Nijdam, G. Alblas and R. Hekkenberg [21] | ResearhGate, proceeding | Improvement suggested by introducing expert system for hull assembling | General shipbuilding |
2019 | Research on Labor Cost Control in Shipbuilding Process. H. Wu [86] | International Conference on Social Science and Education, proceeding | Saving labour cost by intelligentization | Chinees shipbuilding industry |
Table 1
(Continued)
Year | Title-[ref] | Source and publication type | Improving cost estimation method | Applicability |
2020 | Data driven performance evaluation in shipbuilding. U. Bilen and S. Helvacioglu [7] | Brodogradnja: Teorija i praksa brodogradnje i pomorske tehnike, journal | Improvement clarification of cost estimation formulas by introducing step-by-step guideline | General shipbuilding |
2020 | A computing model: the closed-loop optimal control for large-scale one-of-a-kind production based on multilevel hierarchical PERT-Petri net. Y. Mei, Z. Zeng and J. Ye [52] | IEEE Transactions on Engineering Management, journal | Focus on Engineering-To-Order. Improvement by proposing a cost dynamic control and optimization method based on process results | General shipbuilding, interim products |
2020 | A practical approach for decision-making on preliminary naval ship cost estimating using multiple cost estimation methods. K. E. Patrón, L. D. Leal and O. D. Vasquez [63] | International Ship Design & Naval Engineering Congress, proceeding | Improvement of decision-making process, which cost estimation-method applies best | Naval |
2022 | A strategic decision support tool for shipyard production performance evaluation and support in budgeting for performance improvement. X. Cui [20] | Naval Architecture, Ocean and Marine EngineeringUniversity of Strathclyde, Glasgow, doctoral thesis | Suggests improvement of performance management strategy | General shipbuilding |
2022 | Method for Estimating Cost of New Ship Building with Linear Regression. A. Azhar and T. A. Kristiyono [3] | OP Conference Series: Earth and Environmental Science | Improvement how to speed up cost estimating process | Indonesian ferry shipbuilding industry |
In this study, we focus on the application of the mentioned methods for Engineering-To-Order during in pre-contract phase. As presented in Table 1 a set of 5 publications containing relevant cost estimation method information concerning ETO-projects.
The existing methods have been discovered based on published scientific literature. Because if something is of value, it is also described in a publication. Looking at the available literature, we must also realize that cost estimation methods and their results are seen as competitive information, yards do not like to share all details usually. This was also noted during Caprace’s research [15], where only 2% of the 1250 shipyards, shipowners, and research centers contacted responded to his survey regarding cost estimation methods and results used. More accurate methods may be available but are not available for study. As a result, we had to limit ourselves to the broader Google Scholar search for this subject.
In the next section, we discuss the properties and limitations of estimation methods identified in the selected papers in the context of ETO projects in the pre-contract phase.
4.Cost estimation methods for Engineering-To-Order
The literature review results can be grouped on their approach to the problem. A method for cost estimation is either top-down, bottom-up, or computer-based reasoning. The latter refers to the digitalization of expert knowledge. The first two are named after the starting point of the estimation.
Although methods can be divided into these categories, shipyards cannot. To minimize errors, shipyards usually employ at least methods from two categories [15,49]. The cost estimation approaches utilized during a project depend on the design maturity and available cost information from past performances.
4.1.Top-down
Methods classified as top-down use a higher level of design information instead of detailed information. Top-down methods are based on the comparison and extrapolation of known product data from ships built earlier and with satisfying similarity. Similarities such as (sub)product type, (sub)product dimension, and production techniques used. They are using the implicit assumption that similar products have similar costs.
The evaluation of similarity is often done by experts with extensive historical and technical knowledge [49], and who can bind that with the yard limitations and possibilities.
4.1.1.Intuitive method
A cost estimation method based on the collective expertise and wisdom of experienced estimators is called the Intuitive Method (IM) [15]. Involved employees have the capability to oversee the entire construction process. They can address construction bottlenecks and risks for a specific ETO project, using their experience to consider the overall building process, yard capabilities, and available techniques [9,34] and translating this with knowledge of their individual model, containing empirically derived factors to a cost estimation. For outsiders, this is often a magical process that can hardly be verified [28].
A cost estimation based on IM can be performed quickly and is often the only available approach for an ETO assignment. However, the reliability and reproducibility are usually low [15]. Additionally, this approach relies heavily on the experience and skills of the estimator, which can take time to impart to a new employee quickly [41].
Such an approach results in an uncertain estimate because one can never be sure whether all knowledge has been contributed and whether the expert estimate is correct. Moreover, such an approach is not reproducible. So, when changes occur in design, which is often the case for ETO projects, they can hardly be traced back to the original estimate.
4.1.2.Parametric method
Cost estimation methods that use the statistical relationship between one or more parameters that affect costs are called Parametric Methods (PM). These methods rely on analyzing data from past projects to identify the key relationships, called cost estimation relationships, between various input parameters and the respective costs of the projects, resulting in the commonly used key figures like man-hour per ton [83] for steel and man-hours per inch-meters for piping. The last represents the diameter of a pipe in inches and the length of the pipe in meters. An extensive description of the parametric method is given by Shetelig [70]. The research of Caprace [15] shows that the PM is often used in the pre-contract phase.
The identified cost estimation relationships are based on the regression of historical data, using the implicit assumption that the same forces that affected the cost in the past will affect cost in the future [59]. However, this assumption does not automatically apply to ETO projects. To address this, complexity correction factors are usually introduced in the PM [48]. Factors which are mostly based on the knowledge of experts. The introduction of these correction factors makes it hard to automatically trace back the effect of a design change on the original estimate.
4.2.Bottom-up
Estimating cost by using a bottom-up approach comes down to summarizing the assembly cost of every (sub) product to a total shipbuilding cost. To perform a bottom-up estimation the design must be of significant maturity. A bill of material and his maturity must be known [49]. This approach is in its essence more an accounting process than an estimation.
It was Cooper and Kaplan [19] who proposed an Activity-Based Costing (ABC) method as an alternative to the traditional accounting process. ABC assigns overhead and indirect costs to products. For ABC activities are the cost drivers. The Generative Costing method [28] is basically the same as ABC. It assigns cost to the process involved in product creation.
The bottom-up approach makes it possible to consider changes in the production process and manufacturing techniques, unlike the top-down approach, which is not sensitive to those changes. Effects of changes are in a top-down approach reflected in the breakdown of the total work process into its individual components.
4.2.1.Feature-based costing
Feature-Based Costing (FBC) is a well-known and widely used bottom-up method. This method integrates CAD/CAM with cost information [60,84]. It is based on the idea that a ship can be described as a number of associated features such as rooms, tanks, decks, inner and outer contours, welding length, etc. By analyzing these features, cost estimations are made in combination with past performance information.
Group Technology offers a system that is also based on FBC principles [15,46]. It allows engineered ship systems to be broken down into definable units of construction called intermediates. Using Group Technology, intermediate products are grouped into groups with similar design and manufacturing characteristics, known as part families. By combining past performance information of a product family, a cost estimate can be made.
One of the enablers for using FBC in the earlier stages of a project is the increasing use of 3D modeling, the ongoing integration of CAD/CAM integration, and the automatic generation of design information [9,28,49,68,74].
To determine the cost of a product or service, FBC uses an analytical approach by identifying and analyzing its key features [49]. Although highly accepted by many shipyards for cost estimation in detailed design and production design phases, FBC is seldom used in a pre-contract for ETO projects due to the lack of similarities and detailed design information required for an accurate estimate.
4.3.Computer-based reasoning
The increasing computer power in the last decades has made it possible to introduce more intelligent cost estimation methods [40]. Elmousalami [27] gives a recent and extensive overview of computational intelligence techniques for cost modeling. In the context of the present review, in which we focus on ETO shipbuilding projects, we give a short description and background of the following techniques:
Neural networks (NN), also called Artificial Neural Networks (ANN)
Case-Based Reasoning (CBR)
Fuzzy logic (FL)
4.3.1.Neural networks
Neural networks were applied for cost estimation in the nineties [8]. The appropriateness of neural networks for cost estimation is based on the condition that there is a large case base for which cost-driving attributes are known. Neural networks simulate human thoughts, and by linking this with historical cost information, it can be used for cost estimation purposes. This is done by bringing together a large amount of historical cost and design information. Based on the provided data, the system discovers and learns the functional relationship between design attribute values and cost [51,67]. Once the system is trained, it provides a cost estimation based on the attribute values of a new design.
The literature on cost estimation of Engineer-to-order (ETO) projects utilizing Neural Networks (NNs) in shipbuilding is scarce. This is because Neural Networks tend to be most effective when the learning database used is large and contains similar products. However, this is not the case for industries that offer limited product ranges, like shipbuilding. Furthermore, for reliable cost estimates, NNs need a high level of digitalization. However, shipbuilding lags behind many other manufacturing industries in terms of adopting digital solutions [78]. Finally, neural networks are very sensitive good within the sampled range but often lack accuracy outside of the sampled range, making them less suited for dealing with innovative situations [61].
4.3.2.Case-based reasoning
Case-Based Reasoning (CBR) is based on the idea that a reasoner remembers a previous situation like the subject at hand and uses that to solve a new problem. The method was introduced at the Georgia Institute of Technology [43]. CBR implies that old situations meet new demands [44]. This is done by adapting information from previous products which closely match the attributes of the new product. CBR enables cost estimation by combining past results of existing products with modifications referring to the newly designed components and/or assemblies of a new product. This approach is particularly advantageous when one has to deal with limited adjustments [64]. The literature research of Burggräf, Wagner and Weißer [12] states that CBR approaches are becoming less popular in the area of physical product development.
Using CBR during the pre-contract phase of an ETO project can reduce uncertainties in cost estimations by finding similarities and differences between previously constructed units. Exactly how much the estimated cost can be improved depends on how closely the new unit resembles existing units and, thus, the degree of similarity. In most cases, the degree of (sub)product similarity is determined by an expert who is knowledgeable in this area.
4.3.3.Fuzzy logic
Fuzzy Logic (FL) methods aim to capture human expertise and know-how [18,69] and use this knowledge to support cost estimations. The theory behind fuzzy logic was proposed in 1973 by L.A. Zadeh [88]. It is based on the notion that each variable of consideration belongs partially or gradually to a defined fuzzy set. The theory of fuzzy sets enables the possibility of transcribing the knowledge of designers into software applications. Mendel [53] provides a detailed explanation of the operation and application of fuzzy logic-based systems.
The variables of consideration are called cost drivers. The knowledge of experts, which must exist, is used to determine those cost drivers and to which product property they are related. For this determining process, the fuzzy Delphi method, as developed by Ishikawa et al. [35], and the fuzzy analytical hierarchical process [81] are often used. With the fuzzy Delphi method, the degree of consensus within an expert panel is determined using triangulation statistics. The fuzzy analytical hierarchical process is an extension of the standard analytic hierarchy process (AHP). This is done by setting the AHP scale into the fuzzy triangle scale to support the determination process [24].
The literature on cost estimation approaches also mentions the development of hybrid intelligent models [51], addressing combinations of the mentioned computational intelligent methodologies. Combining these methodologies can enhance the computational model such that the limitations of any single method can be compensated by other methods [27]. Application of the hybrid model can be found in the area of construction projects [26]. The use of hybrid intelligence models in the shipbuilding industry has not been found during the literature review.
4.4.Methods summary
Table 2 provides an overview of the general advantages and limitations of cost estimation methods and their specific usability for Engineering-To-Order (ETO) projects during the pre-contract phase. The general advantages and limitations mentioned here are derived from the research conducted by Caprace [15].The evaluation of usability for Engineering-To-Order (ETO) projects during the pre-contract phase is based on the performed literature study.
Table 2
Overview of advantages and limitations of the cost estimation methods in general and ETO pre-contract specific
General | ETO pre-contract specific | ||
Methods | Advantages | Drawback and limitations | Usability |
Intuitive method | - Quick to produce- Flexible | - Susceptible to bias - Unstructured, not reproducible, untraceable- Different experts use different mechanisms | - Unreliable and poorly verifiable outcome- No traceback when design change occur |
Case based reasoning | - Can offer a solution rapidly- Good logical visibility- Avoid previously committed errors- Implicit storage of company knowledge | - A reliable case base is needed- Cannot deal with an introduction of new technologies- Doesn’t handle innovative solutions | - Not useful in the absence of similarities- Cannot handle new technologies |
Parametric method | - Quick to produce- Repeatable and objective | - Parameters not included may be important- Logic not visible- Cannot deal with an introduction of new technologies | - False sense of security (black box)- Unsecure outcome- Traceback limited applicability |
Feature based method | - Possibility of integrating CAD/CAM with cost information- Got the protentional to be automated- Link between design choices and cost consequences | - Requires large resources to implement- No consensus on what features are- Detailed design information is needed | - Not applicable, no detail design information and no past performance information available |
Fuzzy logic method | - Goof logic visibility- Integration of the imperfection of the model | - Human expertise and know-how is needed | - Unreliable, outcome depends on variables considered- Limited traceback when design change occur- Cannot deal with new technologies or new systems, no experience |
Neural network method | - Accurate estimates are possible- Can be updated and retrained | - Logic not visible (black box)- Complex- Requires a large sample database- Cannot handle innovative solutions | - Not applicable, a sufficiently usable example database is missing |
5.Discussion
This literature review focuses on cost estimation methods capable of estimating cost accurately for Engineering-To-Order (ETO) projects in the pre-contract phase. Criteria for making a cost estimation method capable for ETO projects in the pre-contract phase are:
∙ A breakdown of scope, activities, and deliverables.
∙ Traceability to first principles.
∙ Utilizing historical data from past projects.
∙ Accommodate changes in project scope and design revisions.
The literature review indicates that existing cost estimation methods used in shipbuilding rely mainly on available product specifications, which include shape, dimensions, and material specifications. Furthermore, these methods rely heavily on historical data, assuming similar products have similar costs. The most suitable method is chosen based on the details of the product information.
The use of product specifications as the sole basis for ETO project cost estimates does not consider the uniqueness of the construction and supply chain processes. To cover that the knowledge of experts is used to substantiate the cost estimate. Not least because the design information is limited in the pre-contact phase. Estimates based on professional knowledge mean there is no traceability to the first principles, and the professional knowledge gained based on experience is challenging to transfer to new employees. In essence, this means that all described methods fail to provide a good answer in the current situation. They fail for ETO projects in the pre-contract phase because:
The parametric Method is unable to deliver accurate results due to the introduction of expert-based correction factors, which introduce sources of error that cannot be accounted for.
Feature-Based Costing method lacks product similarities and detailed design information required for an accurate estimate.
Neural Network approaches are not effective due to the limited size and scope of the sample database; if the data volume is too small or covers too limited a range, the model may not be able to accurately identify patterns and trends.
Case Based Reasoning the mechanism of (sub)product similarity can hardly be used and discovering similarities depends on expert knowledge.
Fuzzy Logic leans heavenly on expert opinion; if new techniques or new systems are introduced these opinions cannot be verified.
The literature review triggers the question: how are cost estimation methods used in other industries for ETO projects, and can these methods be effectively implemented in the shipbuilding sector? The next phase of our research will delve deeper into this issue. For now, however, we limit ourselves to finding that the construction and manufacturing sectors use techniques identical to those used in shipbuilding. See for example [16,31,54,80]. This suggests that cost estimates for ETO projects formulated during the pre-contract phase are based on the same underlying principles.
The findings of the literature study call for a development that considers the construction processes and techniques used while also considering the criteria for creating a cost estimation method suitable for ETO projects in the pre-contract phase. This is illustrated in Fig. 4.
Fig. 4.
Current cost estimation methods are limited to product specifications supplemented by expert knowledge. One direction in which improvement of the estimation method can be achieved is to include how (sub)products are built.
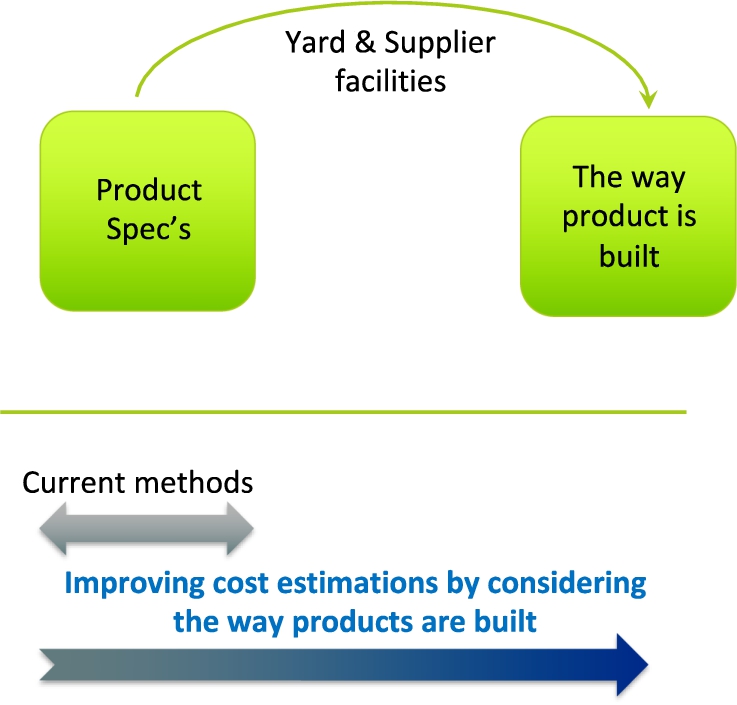
The first step in that direction is to capture the process of constructing products.
By capturing the construction process, for cost estimation purposes, the possibilities of the yard and suppliers can be considered. Using the assumption that the same forces that previously affect the costs will also affect costs in the future a record of past construction processes and the associated costs must be created.
Taking construction processes into consideration requires that the estimation method be adjusted accordingly. To make accurate comparisons with previously constructed products, we must look beyond the final result and evaluate the processes and techniques employed during production. This includes such factors as the order of the construction steps, the tools used, and the techniques adopted during the manufacturing process. Further research is needed to determine how to effectively compare present (sub)products to those of the past including the way they were built.
Estimating the cost of an ETO project, including the construction process, in the contracting phase is challenging because there is only limited insight into the expected detailed construction process in the pre-contractual phase. The construction strategy, block divisions and block assembly sequence have been identified as this is necessary to demonstrate that the ship can be delivered on time according to requirements. This information can serve as a basis for defining the construction process in such a way that it can be used for cost estimation. The work of Son and Nam [75], Taraska et al. [79] and Deul et al. [21], which describe concepts to automatically generate a construction process for hull blocks, can be a starting point for this.
Further research is necessary to create an adequate format to capture process and output details for cost assessment. Garcia-Lopez NP’s [32] approach of utilizing activities as a basis can prove to be beneficial, as well as Zheng Y, Törmä S, Seppänen O’s [89] research involving objects as a starting point. These developments give valuable insight for improving the estimation method.
Although not in use now, a suitable cost estimation method is badly needed by the shipping sector to deal with the energy transition and to prevent a wave of bankruptcies in shipyards at a moment when every yard will be needed.
6.Conclusion
The research is limited to the cost estimation methods currently known in the shipbuilding industry, which are now published in some form. Scientific databases were consulted first while performing the literature review. The amount of literature found that way was limited. A wider range of publications was found through Google Scholar.
Looking at the available literature, we must realize that applied cost estimation methods and their results quickly become competitive information, as experienced in Caprace’s [15] survey. Consequently, the availability of real practical figures is limited.
The research focuses on methods for estimating the costs for realizing an ETO project in the pre-contract phase. The relative lack of literature on this topic illustrates that estimating costs for an ETO project in the pre-contract phase presents a significant challenge.
Current cost estimation methods used in the pre-contract phase depend heavily on expert knowledge, making it difficult to manage cost control, reproduce estimates, and share estimation knowledge.
The performed literature review shows that several estimation methods have emerged over time, taking advantage of new opportunities, and adapting to technological advancements in construction. Still, there is currently no method capable of producing a substantiated accurate cost estimation for ETO projects in the pre-contract phase.
With the shift towards energy transition, which lacks a clear direction, the shipbuilding industry requires a novel cost estimation method – one that can withstand the dynamic changes in construction technology and construction processes it is applied to.
To achieve that further research is necessary by improving the connection between cost estimation and implementation of construction processes and new technologies. This research should start by creating an information structure that bridges the gap between cost estimation and the construction processes.
Acknowledgements
N/A
Funding
The authors report no funding.
Conflict of interest
The authors have no conflict of interest to report.
Author Contributions
Gerrit Alblas has been responsible for Conceptualization, Investigation, Methodology, and Writing the original draft. Jeroen Pruijn has been responsible for the Conceptualization, Supervision, Writing – Review, and Editing.
References
[1] | W.W. Abd Rahman, N.M. Zaki and M.A. Husain, A review of work breakdown structure and man-hours estimation method used in shipbuilding production, International Journal of Mechanical Engineering and Technology. 10: (01) ((2019) ), 1141–1158, https://iaeme.com/Home/search?article_id=1&string=IJMET_10_01_117. |
[2] | G. Alblas and J. Coenen, Advances in Manufacturing Technology XXXII: Proceedings of the 16th International Conference on Manufacturing Research, Incorporating the 33rd National Conference on Manufacturing Research, September 11–13, University of Skövde, Sweden, IOS Press, (2018) , p. 6. doi:10.3233/978-1-61499-902-7-279. |
[3] | A. Azhar and T. Kristiyono (eds), Method for Estimating Cost of New Ship Building with Linear Regression, IOP Conference Series: Earth and Environmental Science; 2022 November 27, IOP Publishing, (2021) . doi:10.1088/1755-1315/972/1/012014. |
[4] | J. Bäckstrand and D.J. Powell, Enhancing supply chain capabilities in an ETO context through “Lean and Learn”, (2021) . doi:10.31387/oscm0460308. |
[5] | D. Ben-Arieh and L. Qian, Activity-based cost management for design and development stage, International Journal of Production Economics. 83: (2) ((2003) ), 169–183. doi:10.1016/S0925-5273(02)00323-7. |
[6] | J.M. Bergsma, J. Pruyn and G. van de Kaa, A literature evaluation of systemic challenges affecting the European maritime energy transition, Sustainability 13: (2) ((2021) ), 715. doi:10.3390/su13020715. |
[7] | U. Bilen and H.S. Data, Driven performance evaluation in shipbuilding, Brodogradnja: Teorija i praksa brodogradnje i pomorske tehnike 71: (4) ((2020) ), 39–51. doi:10.21278/brod71403. |
[8] | J. Bode, Neural networks for cost estimation, Cost engineering 40: (1) ((1998) ), 25. |
[9] | M. Bole (ed.), Cost assessment at concept stage design using parametrically generated production product models, in: International Conference on Computer Applications in Shipbuilding, Portsmouth, UK, 2007 September 18–20, (2007) . |
[10] | G. Bruce, Shipbuilding Management, 1e edn, Springer Nature, (2020) . doi:10.1007/978-981-15-8975-1. |
[11] | T.D. Brunoe and P. Nielsen, A case of cost estimation in an engineer-to-order company moving towards mass customisation, International Journal of Mass Customisation 4: (3–4) ((2012) ), 239–254. |
[12] | P. Burggräf, J. Wagner and T. Weißer, Knowledge-based problem solving in physical product development – a methodological review, Expert Systems with Applications: X. 5: ((2020) ), 100025. doi:10.1016/j.eswax.2020.100025. |
[13] | J.-D. Caprace and P. Rigo, Towards a short time “feature-based costing” for ship design, Journal of marine science and technology. 17: (2) ((2012) ), 216–230. doi:10.1007/s00773-012-0163-4. |
[14] | J.-D. Caprace and P. Rigo (eds), Multi-Criteria Decision Support for Cost Assessment Techniques in Shipbuilding Industry, Budapest, Hungary, 2009 May 10–12, COMPIT’09. |
[15] | J.D. Caprace, Cost effectiveness and complexity assessment in ship design within a concurrent engineering and “Design for X” framework. PhD thesis, Université de Liège, (2010) . |
[16] | S.L. Castro Miranda, E. Del Rey Castillo, V. Gonzalez and J. Adafin, Predictive analytics for early-stage construction costs estimation, Buildings 12: (7) ((2022) ), 1043. doi:10.3390/buildings12071043. |
[17] | S.L. Chan and M. Park, Project cost estimation using principal component regression, Construction Management and Economics. 23: (3) ((2005) ), 295–304. doi:10.1080/01446190500039812. |
[18] | M.-Y. Cheng, H.-C. Tsai and E. Sudjono, Conceptual cost estimates using evolutionary fuzzy hybrid neural network for projects in construction industry, Expert Systems with Applications. 37: (6) ((2010) ), 4224–4231. doi:10.1016/j.eswa.2009.11.080. |
[19] | R. Cooper and R.S. Kaplan, Measure costs right: Make the right decisions, Harvard business review 66: (5) ((1988) ), 96–103. |
[20] | X. Cui, A strategic decision support tool for shipyard production performance evaluation and support in budgeting for performance improvement. PhD thesis, University of Strathclyde, (2022) . |
[21] | M. Deul, B. Hoek, S. Moussault, A.-L. Nijdam, G. Alblas and R. Hekkenberg, An expert system for cost estimation of shipyard steel assembly, in: COMPIT’19: 18th Conference on Computer Applications and Information Technology in the Maritime Industries; March 25–27, Tullamore, Ireland, (2019) , pp. 213–223. |
[22] | V. Dixit, A. Chaudhuri and R.K. Srivastava, Assessing value of customer involvement in engineered-to-order shipbuilding projects using fuzzy set and rough set theories, International Journal of Production Research 57: (22) ((2019) ), 6943–6962. doi:10.1080/00207543.2019.1572928. |
[23] | A.T. Dobson, Cost prediction via quantitative analysis of complexity in US Navy shipbuilding. PhD thesis, Massachusetts Institute of Technology, (2014) . |
[24] | M.S. Dwi Putra, S. Andryana and A. Gunaryati, Fuzzy analytical hierarchy process method to determine the quality of gemstones, Advances in fuzzy systems 2018: ((2018) ), 6. doi:10.1155/2018/9094380. |
[25] | ECORYS SCS Group, Study on competitiveness of the European shipbuilding industry within the framework contract of sectoral competitiveness studies-ENTR/06/054 [pdf]. Rotterdam, pp. 239, (2009) . Available from: https://ec.europa.eu/docsroom/documents/10506/attachments/1/translations/en/renditions/native. |
[26] | A.O. Elfaki, S. Alatawi and E. Abushandi, Using intelligent techniques in construction project cost estimation: 10-year survey, Advances in Civil Engineering 2014: ((2014) ). doi:10.1155/2014/107926. |
[27] | H.H. Elmousalami, Artificial intelligence and parametric construction cost estimate modeling: State-of-the-art review, Journal of Construction Engineering and Management. 146: (1) ((2020) ), 03119008. doi:10.1061/(ASCE)CO.1943-7862.0001678. |
[28] | D.K. Evans, D.J. Lanham and D.R. Marsh, Cost estimation method selection: Matching user requirements and knowledge availability to methods, in: International Cost Engineering Council: The Singapore Institute of Surveyors and Valuers, (2006) . |
[29] | T. Fatouh and R.N. Shipbuilding, Engineer-to-order supply chain: A systematic literature review, Procedia Computer Science 219: ((2023) ), 1868–1876. doi:10.1016/j.procs.2023.01.485. |
[30] | J.O. Fischer and G. Holbach, Cost Management in Shipbuilding, GKP Publishing, Kőln, Germany, (2008) , pp. 196. |
[31] | A.B. Ganorkar, R.R. Lakhe and K.N. Agrawal, Cost estimation techniques in manufacturing industry: Concept, evolution and prospects, International Journal of Economics and Accounting. 8: (3–4) ((2017) ), 303–336. doi:10.1504/IJEA.2017.092279. |
[32] | N.P. Garcia-Lopez, An activity and flow-based construction model for managing on-site work. PhD thesis, Stanford University, (2017) . |
[33] | R.G. Hekkenberg, A building cost estimation method for inland ships, in: European Inland Waterway Navigation Conference, Budapest, Hungary, September 10–12, (2014) , pp. 13. |
[34] | M. Hur, S.-K. Lee, B. Kim, S. Cho, D. Lee and D. Lee, A study on the man-hour prediction system for shipbuilding, Journal of Intelligent Manufacturing. 26: ((2015) ), 1267–1279. doi:10.1007/s10845-013-0858-3. |
[35] | A. Ishikawa, M. Amagasa, T. Shiga, G. Tomizawa, R. Tatsuta and H. Mieno, The max-min Delphi method and fuzzy Delphi method via fuzzy integration, Fuzzy sets and systems 55: (3) ((1993) ), 241–253. doi:10.1016/0165-0114(93)90251-C. |
[36] | P.N. Jeziorek, Cost estimation of functional and physical changes made to complex systems. MSc thesis, Massachusetts Institute of Technology, (2004) . |
[37] | G. Jünge, E. Alfnes, B. Nujen, J. Emblemsvag and K. Kjersem, Understanding and eliminating waste in Engineer-To-Order (ETO) projects: A multiple case study, Production Planning & Control. 34: (3) ((2023) ), 225–241. doi:10.1080/09537287.2021.1903279. |
[38] | B.L. Kaluzny, S. Barbici, G. Berg, R. Chiomento, D. Derpanis, U. Jonsson et al., An application of data mining algorithms for shipbuilding cost estimation, Journal of Cost Analysis and Parametrics. 4: (1) ((2011) ), 2–30. doi:10.1080/1941658X.2011.585336. |
[39] | M. Kamola-Cieślik, Changes in the global shipbuilding industry on the examples of selected states worldwide in the 21st century, European Research Studies Journal 24: (2B) ((2021) ), 98–112. |
[40] | G.-H. Kim, S.-H. An and K.-I. Kang, Comparison of construction cost estimating models based on regression analysis, neural networks, and case-based reasoning, Building and environment. 39: (10) ((2004) ), 1235–1242. doi:10.1016/j.buildenv.2004.02.013. |
[41] | S. Kivrak, G. Arslan, I. Dikmen and M.T. Birgonul, Capturing knowledge in construction projects: Knowledge platform for contractors, Journal of Management in Engineering. 24: (2) ((2008) ), 87–95. doi:10.1061/(ASCE)0742-597X(2008)24:2(87). |
[42] | K. Kjersem, Contributing to resolving a project planning paradox in ETO: From plan to planning. PhD thesis, Molde University College, Norway, (2020) . |
[43] | J.L. Kolodner, Reconstructive memory: A computer model, Cognitive science. 7: (4) ((1983) ), 281–328. |
[44] | J.L. Kolodner, An introduction to case-based reasoning, Artificial intelligence review. 6: (1) ((1992) ), 3–34. doi:10.1007/BF00155578. |
[45] | Z. Kunkera, N. Tošanović and N. Štefanić, Improving the shipbuilding sales process by selected lean management tool, Machines. 10: (9) ((2022) ), 766. doi:10.3390/machines10090766. |
[46] | T. Lamb, Ship Design and Construction, 1e edn, Society of Naval Architects and Marine Engineers, (2003) , pp. 883. |
[47] | M. Leal (ed.), Steel hull shipbuilding cost structure, Mechanical Engineeringm Universidade tecnica de lisboa Portugal, (2008) . https://api.semanticscholar.org/CorpusID:35202213. |
[48] | M. Leal and J.M. Gordo, Hull’s manufacturing cost structure, Brodogradnja: Teorija i praksa brodogradnje i pomorske tehnike 68: (3) ((2017) ), 1–24. doi:10.21278/brod68301. |
[49] | C.-K. Lin and H.-J. Shaw, Feature-based estimation of preliminary costs in shipbuilding, Ocean Engineering 144: ((2017) ), 305–319. doi:10.1016/j.oceaneng.2016.11.040. |
[50] | E. Matel, An artificial neural network approach for cost estimation of engineering services: Enhancing cost estimation efficiency. MSc thesis, University of Twente, (2019) . |
[51] | E. Matel, F. Vahdatikhaki, S. Hosseinyalamdary, T. Evers and H. Voordijk, An artificial neural network approach for cost estimation of engineering services, International journal of construction management 22: (7) ((2022) ), 1274–1287. doi:10.1080/15623599.2019.1692400. |
[52] | Y. Mei, Z. Zeng and J. Ye, A computing model: The closed-loop optimal control for large-scale one-of-a-kind production based on multilevel hierarchical PERT-Petri net, IEEE Transactions on Engineering Management. 68: (6) ((2020) ), 1637–1649. doi:10.1109/TEM.2020.3035230. |
[53] | J.M. Mendel, Uncertain Rule-Based Fuzzy Systems Introduction and New Directions, 2e edn, Springer International Publishing, (2017) . doi:10.1007/978-3-319-51370-6. |
[54] | O. Mesa and J.E. Cost, Estimation of construction projects using 5D BIM: Integrating the cost engineer in BIM-based processes through activity theory. MSc thesis, Delft University of Technology, (2021) . |
[55] | A. Miroyannis, Estimation of ship construction costs. PhD thesis, Massachusetts Institute of Technology, (2006) . |
[56] | J. Montali, M. Overend, P.M. Pelken and S.M. Knowledge-Based, Engineering in the design for manufacture of prefabricated façades: Current gaps and future trends, Architectural Engineering and Design Management. 14: (1–2) ((2018) ), 78–94. doi:10.1080/17452007.2017.1364216. |
[57] | R.F. Mulligan, A simple model for estimating newbuilding costs, Maritime Economics & Logistics. 10: (3) ((2008) ), 310–321. doi:10.1057/mel.2008.8. |
[58] | R.A. Myers, Inventor; Google patents, assignee. Method and apparatus for modular construction of a ship patent 3,447,503, 1969 June 3. |
[59] | NASA, 2008 NASA Cost Estimating Handbook, National Aeronautics and Space Administration, Washington, DC, (2008) , pp. 1–19, 11–57. |
[60] | F. Ning, H. Qu, Y. Shi, M. Cai and W. Xu, Feature-based and process-based manufacturing cost estimation, Machines 10: (5) ((2022) ), 319. doi:10.3390/machines10050319. |
[61] | K. Odendaal, Enhancing early-stage energy consumption predictions using dynamic operational voyage data. MSc thesis, Delft University of Technology, (2021) . |
[62] | M. Pal (ed.), Ship work breakdown structures through different ship lifecycle stages, in: International Conference on Computer Applications in Shipbuilding, Bremen, Germany, 2015 September 30–October 2, The Royal Institution of Naval Architects. |
[63] | K.E. Patrón, L.D. Leal and O.D. Vasquez, A practical approach for decision-making on preliminary naval ship cost estimating using multiple cost estimation methods, in: Proceeding of the VI International Ship Design & Naval Engineering Congress (CIDIN) and XXVI Pan-American Congress of Naval Engineering, Maritime Transportation and Port Engineering (COPINAVAL), March 13–15, 2019, Springer International Publishing, (2020) , pp. 223–232. doi:10.1007/978-3-030-35963-8. |
[64] | M. Relich and P. Pawlewski, A case-based reasoning approach to cost estimation of new product development, Neurocomputing. 272: ((2018) ), 40–45. doi:10.1016/j.neucom.2017.05.092. |
[65] | J. Ross (ed.), Weight-based cost estimating during initial design, in: COMPIT’05 4th International Conference on Computer and IT Applications in the Maritime Industries, Hamburg, 2005 May 8–11. |
[66] | J.M. Ross, A practical approach for ship construction cost estimating, COMPIT’04 ((2004) ), 98–110. |
[67] | R. Roy, Cost Engineering: Why, What and How? Cranfield University, (2003) . |
[68] | Y. Sasaki, M. Sonda and K. Ito, Development of a computer-aided process planning system based on a knowledge base, Journal of marine science and technology. 7: (4) ((2003) ), 175–179. doi:10.1007/s007730300008. |
[69] | E. Shehab and H. Abdalla, An intelligent knowledge-based system for product cost modelling, The international journal of advanced manufacturing technology 19: (1) ((2002) ), 49–65. doi:10.1007/PL00003967. |
[70] | H. Shetelig, Shipbuilding cost estimation: Parametric approach. MSc thesis, Trondheim: Institutt for marin teknikk, (2014) . |
[71] | J.N. Sikorra, A. Friedewald and H. Lödding (eds), Early estimation of work contents for planning the one-of-a-kind production by the example of shipbuilding, in: MATEC Web of Conferences, Chongqing, China, 2016 June 15–17, EDP Sciences. doi:10.1051/matecconf/20167701025. |
[72] | M.B. Smith, Updating MIT’s cost estimation model for shipbuilding. MSc thesis, Massachusetts Institute of Technology, (2008) . |
[73] | M.Z. Solesvik, International cooperation on technology innovation development: A case study from the maritime industry, in: Research Handbook on Innovation in International Business, Edward Elgar Publishing, (2022) , pp. 264–274. doi:10.4337/9781800882942.00019. |
[74] | M.-J. Son, S.C. Lee, K.-C. Kwon, T.-W. Kim and R. Sharma, Configuration estimation method for preliminary cost of ships based on engineering bills of materials, Journal of marine science and technology. 16: (4) ((2011) ), 367–378. doi:10.1007/s00773-011-0139-9. |
[75] | Y.-B. Son and J.-H. Nam, Creation of hierarchical structure for computerized ship block model based on interconnection relationship of structural members and shipyard environment, International Journal of Naval Architecture and Ocean Engineering. 14: ((2022) ), 100455. doi:10.1016/j.ijnaoe.2022.100455. |
[76] | M. Soori and M. Asmael, Classification of research and applications of the computer aided process planning in manufacturing systems, Independent Journal of Management & Production. 12: (5) ((2020) ), 1250–1281. doi:10.14807/ijmp.v12i5.1397. |
[77] | V. Stanić, M. Hadjina, N. Fafandjel and T. Matulja, Toward shipbuilding 4.0-an industry 4.0 changing the face of the shipbuilding industry, Brodogradnja: Teorija i praksa brodogradnje i pomorske tehnike 69: ((2018) ), 111–128. doi:10.21278/brod69307. |
[78] | J.W. Strandhagen, S.-V. Buer, M. Semini, E. Alfnes and J.O. Strandhagen, Sustainability challenges and how industry 4.0 technologies can address them: A case study of a shipbuilding supply chain, Production Planning & Control. 33: (9–10) ((2022) ), 995–1010. doi:10.1080/09537287.2020.1837940. |
[79] | M. Taraska, R. Iwańkowicz, T. Urbański and T. Graczyk, Review of assembly sequence planning methods in terms of their applicability in shipbuilding processes, Polish maritime research 25: (s1) ((2018) ), 124–133. doi:10.2478/pomr-2018-0033. |
[80] | S. Tayefeh Hashemi, O.M. Ebadati and H. Kaur, Cost estimation and prediction in construction projects: A systematic review on machine learning techniques, SN Applied Sciences 2: (1703) ((2020) ), 1–27. doi:10.1007/s42452-020-03497-1. |
[81] | P.J. Van Laarhoven and W. Pedrycz, A fuzzy extension of Saaty’s priority theory, Fuzzy sets and Systems. 11: (1–3) ((1983) ), 229–241. doi:10.1016/S0165-0114(83)80082-7. |
[82] | I. Vanderfeesten, H.A. Reijers and W.M. van der Aalst (eds), Case handling systems as product based workflow design support, in: Enterprise Information Systems: 9th International Conference, ICEIS 2007, Funchal, Madeira, 2008 June 12–16, Springer-Verlag, Berlin Heidelberg. |
[83] | D.G. Watson, Practical Ship Design, 1e edn, Elsevier, (2002) . |
[84] | L.S. Wierda, Linking design, process planning and cost information by feature-based modelling, Journal of Engineering Design. 2: (1) ((1991) ), 3–19. doi:10.1080/09544829108901667. |
[85] | O. Willner, D. Powell, M. Gerschberger and P. Schönsleben, Exploring the archetypes of engineer-to-order: An empirical analysis, International Journal of Operations & Production Management. 36: (3) ((2016) ), 242–264. doi:10.1108/IJOPM-07-2014-0339. |
[86] | H. Wu, in: Research on Labor Cost Control in Shipbuding Process. International Conference on Social Science and Education (ICSSAE 2019), Canberra, Australia, December 28–29, (2019) , pp. 325–329. doi:10.25236/icssae.2019.060. |
[87] | P. Yu, Sandwich construction for ship superstructure: Cost estimation and failure prediction. PhD thesis, Memorial University of Newfoundland, (2016) . |
[88] | L.A. Zadeh, Outline of a new approach to the analysis of complex systems and decision processes, IEEE Transactions on systems, Man, and Cybernetics ((1973) ), 28–44. |
[89] | Y. Zheng, S. Törmä and O. Seppänen, A shared ontology suite for digital construction workflow, Automation in Construction 132: ((2021) ), 103930. doi:10.1016/j.autcon.2021.103930. |