Occupational health and safety division of responsibility: A conceptual model for the implementation of the OHSAS 18001:2007 standard1
Abstract
BACKGROUND:
The recent COVID-19 pandemic has brought Occupational Health and Safety (OHS) to the forefront of governmental and organizational preoccupations. Empirical research has pointed that OHS responsibility is diffused within organizations, and there is no apparent reference on whom it falls upon; even the OHSAS 18001:2007 (OHSAS 18001, 2007) standard framework generates the same confusion among organizational stakeholders.
OBJECTIVE:
When constituting an internal chain of responsibility, which organizational stakeholder should be responsible for each item of the OHSAS 18001:2007? The article considers how OHS tasks can be addressed from the perspective of stakeholder management. The objective is to consider the internal division of OHS responsibility between the hierarchical strata and to introduce an OHS Responsibility Multilevel Model for an organization’s internal responsibility system for the implementation of the OHSAS 18001:2007 standard.
METHODS:
The paper presents a qualitative assessment of the literature on the concepts of responsibility and accountability regarding OHS. First method applied was the literature review on the concepts of responsibility and accountability regarding OHS, while briefly discussing their impacts on the voluntary implementation of OHSAS 18001:2007 standard. Second, the OHS and the conditions of the COVID-19 period were synthesised to underline the research motivation and importance. Further the conceptual framework for the internal division of OHS responsibility based on a Multilevel Model for OHS stakeholders was developed based on a creative designed approach considering recent conclusions on safety leadership (OHS being situated at the confluence of top-down and bottom-up approaches in organization).
RESULTS:
The research results underline the relative complexity of the items in the OHSAS 18001:2007 framework; from the 68 items that are comprised under the six themes, the authors have identified 304 distinct actions. The application of the proposed OHS Responsibility Multilevel Model to the OHSAS 18001:2007 supports the interest that research literature has had for the role of top management in OHS.
CONCLUSIONS:
Overall, the research results propose a novel approach for improving stakeholders’ involvement (commitment) and responsibility regarding OHS practices in organization. The research findings highlight that the OHSAS 18001:2007 standard proposes the organization as primary repository of OHS responsibility.
Corina DUFOUR is PhD Student in the Engineering and Management field at Politehnica University of Timisoara, Romania, studying aspects of Occupational Health and Safety (OHS) infrastructure that could enabler sustainability-oriented innovation (having also, several years’ experience in different foreign companies).
Anca DRAGHICI is full Prof. and PhD supervisor in the field of Engineering and Management at Politehnica University Timisoara, Romania. Her research fields of interest are Human Resource Management, organizational dynamics and new business models; she published in the top international journals and conference proceedings having more than 130 papers index in Clarivate Analytics database.
Larisa IVASCU is Assoc. Prof. at Politehnica University Timisoara, Romania. Her research fields of interest are organization’s sustainable development, strategic management, organizational dynamics, and new business models; she published in the top international journals and conference proceedings having more than 100 papers index in Clarivate Analytics database.
Muddassar Sarfraz is Assistant Professor at Binjiang College, Nanjing University of Information Science & Technology, Wuxi, Jiangsu, PR China. His research direction is Human Resource Management and Organizational Behaviour. He has been dedicating himself to the teaching and research of Human Resource and Organizational Management. He has published tens of papers in foreign authoritative journals and academic conferences at home and abroad.
1Introduction
The recent worldwide events resulting from the appearance and the spread of coronavirus at the end of 2019 and throughout 2020 have brought Occupational Health and Safety to the forefront of governmental and organizational preoccupations. Although during past decades, new paths for improving OHS have been explored, with an increased focus on organizational stakeholders and their management, at an operational level, OHS has been lagging both in terms of investment and result improvement. It should be reminded that workplace fatality rate has reached a frightening point [1]: approximately, 2.3 million employees lose their lives and more than 1.9 million face severe injuries because of uncertainty and lack of safety procedures [2]. These figures show accidents still happen in workplaces, and a significant cause is a human error [3]. In the extreme circumstances that the world is facing today, the impact of OHS on the worldwide economic system is poignantly visible. The numerous and costly measures taken by governments and industry to preserve human life and to implement safe work conditions have made OHS the envied princess of organizational concerns. “Cinderella is finally being undusted”
If the consequences of OHS management are important for the health and safety of employees and consequently for achieving organizational goals, OHS responsibility within organizations is at the crossroads of multiple stakeholders’ responsibility (in and outside the context of coronavirus). There is a residual perception that OHS management is the responsibility of the Safety Officer and/or of upper management. Surprisingly, confusion around OHS responsibility also prevails among upper management as underlined by a survey conducted by the British Safety Council on 102 of the most senior directors in Britain. It revealed that when asked who is legally responsible for OHS in their organization, 29% pointed the CEO, 15% the managing director, 13% another board director, 20% to another manager, 5% to a safety manager and 9% did not know [4]. This dispersion of answers at senior management level reinforces the idea that even from a legal standpoint, OHS responsibility is diffused within organizations, and there is no apparent reference on whom it falls upon. We can only infer that any non-mandatory initiatives for OHS, such as those proposed by the OHSAS 18001:2007 (OHSAS 18001, 2007), generate the same confusion among organizational stakeholders.
According to the Merriam-Webster dictionary, responsibility is “the quality or state of being responsible”[5], which means liable to be called on to answer. On the other hand, the same source defines accountability as “the quality or state of being accountable”, which is defined as answerable [6]. The two definitions point out to a relationship between responsibility as included in accountability. In this regard, the OHSAS 18001:2007 standard, states in chapter 4.4 Implementation and operation that “The top management appointee (e.g. in a large organization, a Board or executive committee member) may delegate some of their duties to a subordinate management representative(s) while retaining accountability”. As such, responsibility can be delegated to lower levels of management, whereas accountability remains with the upmost stakeholder.
Although considerable effort has been undertaken to democratize OHS, the complexity and the intertwining of OHS at the operational level make it difficult to circumscribe stakeholder range of action and inherent responsibility. Process charts address the flow of information and/or specific tasks but track insufficiently OHS items at a detail level that is coherent with that of the OHSAS 18001:2007 standard. Furthermore, the research literature is also oriented on responsibility as a matter of compliance with the minimum legal requirements of national context or industry sector and lags in proposing an approach for stakeholder responsibility. To bridge this gap, the present research proposes to design and implement a conceptual canvas for attributing OHS responsibility compatible with the OHSAS 18001:2007. By coupling items of the OHSAS 18001:2007 standard to organizational stakeholders, the present research answers the question: When constituting an internal chain of responsibility, which organizational stakeholder should be responsible for each item of the OHSAS 18001:2007 standard?
Firstly, the authors review the concepts of responsibility and accountability regarding OHS, while briefly discussing their impacts on the voluntary implementation of the British Standard OHSAS 18001:2007. The literature on OHS responsibility is scarce and focused on specific industries and/or legal contexts, with most focus on the responsibilities of upper management, while less attention has been paid to the division of responsibilities among organizational stakeholders.
Organizations implementing voluntary OHS standards already respond to the minimum legal requirements of the national context and industrial sector. As such, this research intends to facilitate the implementation of such standards by proposing a conceptual model for the division of responsibilities. Thus, for the OHSAS 18001:2007, the items of the standard were reviewed with the purpose of identifying the responsible organizational stakeholder. It was concluded that the standard clearly pinpoints top management responsibilities while attributing the responsibility for most items to the whole organization. A possible explanation can be that the OHSAS 18001:2007 was conceived with a broad spectrum of application – SMEs and multinationals, mature or emerging OHS organizations etc. Therefore, the authors shall propose a conceptual framework for the internal division of OHS responsibility based on a Multilevel Model for OHS stakeholders which structures responsibilities as cascading among organizational stakeholders. The conceptual model considers recent conclusions on safety leadership regarding OHS being situated at the confluence of top-down and bottom-up approaches [7–9].
The paper is structured around two major research parts: the chapters dedicated to the review of the specialized literature and the chapters dedicated to the creative design of the OHS Responsibility Multilevel Model together with its application (testing). The review of the literature (chapter 2) includes considerations on responsibility in OHS management system and the organizations’ stakeholders. In addition, will be pointed some aspects on the OHS in the context of the COVID-19 pandemic to underline the motivation and importance of the presented research approach. Chapter 3 presents the theoretical Multilevel Model which structures OHS responsibility as cascading among organizational stakeholders, while chapter 4 discusses the application of this internal chain of responsibility for the OHSAS 18001:2007 adoption. In the final chapter of the paper are presented the final conclusions, limitations, and future research.
2Literature review
2.1Considerations on responsibility in OHS management systems
OHS events are under a lot of scrutiny from both internal and external stakeholders, having significant impacts on reputation, employees’ morale, relation to regulative bodies, not to mention legal consequences.
Under most legal frameworks, accountability lies with the head of the organization [7, 10–16], but the distance between senior and frontline management, makes it impossible for an appropriate monitoring of the system [14]. As shown by [17], authors voiced the confusion of top, middle and front-line managers in Finnish public sector service organizations regarding their responsibilities and their duties, whereas the research presented in [18] that has been developed in the case of construction industry, has shown the contextual influences on safety leadership and pointed that the issue of who is responsible for safety is perceived as acutely needing an answer. Understanding the framework in which each level must operate for the common goal of safety is a resource facilitating decision-making and action.
Employees engagement is an important aspect is safety management. Thus, important findings on this behaviour dimension were presented through the study of the role that trust plays in moderating the relation between employee engagement and fairness, in service enterprises in [19] and by [20] where research findings demonstrate the importance of workplace well-being in promoting work engagement.
Furthermore, the guidelines for the Australian mining industry presented by [11] proposed a Safety Culture Maturity Model which considers the importance of frontline staff and develops personal responsibility. These findings are echoed by the works presented in [21] who showed that the less mature the OHS organization, the smaller the part played by employees and line-managers and less attention is given to it by top-management, as stated also, by [4]. The research presented by [22], focused on the chain of responsibility at a macro, i.e. national, level and in the context of Chinese regulation and underlined the complexity of the governmental chain of responsibility. If upper management clearly bears the legal responsibility for OHS (CEO, chairman, OHS-managing director), lower-level managers and OHS officers are concerned with managerial aspects of OHS (planning, organizing, directing, control and coordination). It is fascinating to note that in Chinese Law (Trade Union Law of the People’s Republic of China’s, 3rd April 1992, amended on 27th October 2001), trade unions are bearers of the crucial role of both technical and scientific training. Equally, specific safeguards have been ordered by the Chinese law under the form of separate in-company safety-inspectorates, without a link to production or management.
The division of responsibilities throughout the organization has a three-fold purpose: accountability in case of OHS occurrence, empowering employees to be OHS actors in their work environment and continuously improved risk management.
Rules represent a fundamental building-block of Occupational Health and Safety management as they “provide accountability and predictability by defining responsibilities for tasks and help in achieving a common understanding by developing an agreement between organizational actors” [23]. Rules can take the form of legal requirements, as defined by international or national frameworks, international conventions, European directives or regulations (in the European Union), national laws, decrees, codes [24], sectorial laws and conventions. These sets of texts mainly refer to the duty of care shared between the employer (as primary repository) and the employees. Secondly come internal policies, which are defined internally by the organization, and which, although do not have an initial legally binding character by themselves, are mandatory for application in the organization. They cannot contain dispositions opposite to legal requirements, but in case of accident or incident, the courts can consider such documents as proof of implementation of OHS. Finally, frameworks or guidelines are documents written by external bodies (with or without the input of the organization and the implementation of which is subject to the will of top management). Conformity to such documents can give a competitive advantage [25] and when adopted and implemented, they become part of company policies and therefore adopt the characteristics of these rules. Moreover, rules represent an ever-changing body, in constant search of the balance between too many and too few rules as between blind application of the rules and workers’ common sense. Thus, a viable OHS system requires the participation of the entire organization because of the intricate relationship between those who generate risk and those who are exposed to it. In this respect, the research presented in [25] proposed, in the case of the production environment, a macro-ventilation of a series of roles and responsibilities between top-management, production manager, hierarchical strata, employees, OHS delegate and employee constituted OHS committees. This proposal remains, a starting point for considering OHS roles, especially as the item “structure and responsibilities” is pinned under top management.
Other studies [11, 26–29] proposed changing the rules to match reality and considering that the workforce is an important part of the expertise of the organization, thus researchers proposed a classification of rules in action rules (small granularity procedure), process rules (decision-making models) and goal rules (defining desired states, not practices) [4, 24, 30]. The OHSAS 18001-2007 is an example of goal-setting rules, which has achieved consensus from numerous certification institutions, national bodies and expertise bodies. The document is a framework for OHS management systems that set out several requirements and best practice for organizations that were grouped in six themes: general requirements, OHS policy, planning, implementation, and operation, checking and management review. The OHSAS 18001:2007 implementation is a voluntary approach to OHS which needs to be tailored to the organization [27].
2.2Considerations on responsibility and organizational stakeholders
The mere existence of OHS rules is not equivalent to an efficient OHS management system; knowledge, tailoring and understanding of OHS rules are pre-requisites to their implementation. As these prerequisites are intertwined, one of the main difficulties in tailoring an OHS management system is managerial failure to know all OHS obligations and subsequent changes [31]. What is more, the implementation of voluntary management systems such as the OHSAS 18001 can induce unexpected risks within the organization [32]. Consequently, “the sustainable prevention of worker’s health should take into account: management responsibility, workers responsibility [ ... ] clear roles for stakeholders” [32].
From the perspective of rulemaking, in [12] is stated that organizational safety compliance means that legal and/or regulatory requirements are met through practices and procedures that the safety leaders define, and the others enact. On the other hand [23], proposes that from an organizational perspective, “rules made at the top level can be written less strictly, covering only the minimally required safety level. Sub-divisions of the organization can then be authorized to issue stricter rules in their specific tasks, or its context requires them” This is reinforced through examples of practices in Norway oil and gas industry where the internal control of regulations is part of the line organization, “i.e. everyone at his/her level has a particular responsibility to improve and safeguard the OHS quality of the workplace. The overall responsibility, however, rests with the employer, who will seek support both form his professional staff and from the participants in the OHS organization” [26].
When rules are modified, generally middle-managers and team-leaders are consulted on the modification before implementation. The expected gain is that the rule makers can filter the new rule through an operational lens which is beneficial for eliminating mistakes and facilitates future implementation [23].
Empowering employees to be actors of OHS in their work environment is a crucial task that relies on direct management [14] who must be trained accordingly [33] and finally, on the employees themselves [13]. Employees are the first who can help risk identification, minimization and/or elimination becoming the first beneficiaries of the implemented measures. For this to occur, any employee must have appropriate training for the work to accomplish but also relative to the operating environment. To this end, for instance, front-line supervisors in construction industries, as described in [33], are considered motors for recognizing safe work behaviour, and thus the minimal legal training requirements seem insufficient compared to the real OHS needs of their work environment.
Literature still debates middle-managers’ role in OHS on account of their proximity to information, their capacity to make financial decisions in safety issues, their role in motivating personnel [13] within a limited action span [29, 34, 35]. Their role in OHS has been less researched. Parallelly, employees are viewed as a group of stakeholders that have essential knowledge of the workplace and the risks related to it and consequently, are considered as having a paramount role in hazard mitigation.
Within the EU Framework Directive 89/31, Article 11, it is specified that all discussions regarding safety and health at work should involve either workers or their representatives. In the research study [35] is re-examined the modern role of the safety representative (on a general basis) and three categories of them are defined: safety committee with representation from all parties, safety representatives elected by the employees and safety experts representing the management. Regardless of the form, the safety representative’s functions include representation of the employees on OHS matters with the employer and the enforcing authorities, with the objective of complying with OHS requirements and protecting employee interest. This can be achieved through the investigation of hazards or complaints, inspections, attendance in committees and specific training. If the employee representatives are partial participators to OHS as the final decision lies with the employer, the latest research tends to confirm the need for a more precise definition of their rights and duties. The consensus among managers and safety representatives’ points to satisfaction with the legal and regulatory framework but dissatisfaction with its operational application. Building on these findings, we can infer that the managerial job needs support in dealing with the bulk of information, and such a transversal aid could be the safety representative.
As emphasised by [36], in an integrated safety culture organization, top-down and bottom-up approaches coexist among management strata: upper management decisions are efficient for rapid implementation and change, but procedure maintaining should be a bottom-up approach in which lower management and workers can voice their own conclusions. The responsibilities of middle and frontline managers include implementing relevant safety training, establishment and dissemination of experience feedback (including analysis of incidents and accidents), communicating safety rules, checking subsequent application, proposing discussions on rule formalizing, implementing and finally, arbitrating on contradictions [8].
All in all, research on a holistic approach of stakeholder responsibility in the field of OHS remains scarce, approaches focusing on specific industries and/or legal contexts. If leadership, roles, culture are discussed, the matter of responsibility is mainly dealt within the context of a legal framework and with an important focus on the responsibilities of top management. One of the few attempts linking voluntary management systems to the leader-follower dyad is that presented in [12], who coupled leader practices for safety and aligned them to macro requirements of the OHSAS 18001:2007. Among the reviewed studies, none had a holistic approach regarding all the items of the OHSAS 18001, while through the sampled population, the focus was on the front-line supervisors and workers, and thus safety compliance was oriented on implementation [37].
External (governments, NGOs, work inspectors, work doctors, audit organizations) and internal (top, middle and front-line managers, employees, trade unions) gravitate around OHS, and consent seems to be achieved on the role played by top management (as an employer) who define policies in coherence with the strategy of the company, and bear the accountability for OHS, middle management (as representatives of the employer) who ensure follow-up and regular application of company policy, but without any clear responsibility associated, yet having decisional capacity, front-line managers (as representatives of the employer) who ensure the day-to-day implementation of OHS policies, governments (as a legislator) who define the minimum legal OHS requirements and standards-issuing/audit organizations (as control organizations), who can exercise a form of control on the way in which OHS is implemented [30, 38].
Main divergence of opinion occurs around the following stakeholders: employees, targeted by the OHS policies and the core of its application and trade unions (as representatives of employees), the existence of which seems to depend on statutory and historical inputs [8, 9, 30].
In conclusion, the few studies tackling responsibility and OHS deal with high-risk industries or specific legal frameworks and do not bridge the gap of how the internal chain of responsibility can be implemented in the organization. If national legal frameworks seem to agree on the general duties of the employer and consequent legal accountability, the way in which subsequent responsibility is cascaded within the organization and among the internal stakeholders remains an understudied field.
Based on the literature review and ILO Guidelines (2001), Table 1 summarizes the stakeholders that influence OHS responsibility (considered also the synthesis of relevant studies as [10, 12, 39, 40]).
Table 1
OHS stakeholders
Position | Type | Role | Example |
External | Legal and paralegal | Propose the legal framework and/or follow-up its implementation | Governments, NGOs, work inspectors, work doctors etc. |
External | Non-binding organizations | Propose standards, norms or frameworks (with or without certification) that can be voluntarily implemented by the organization | e.g., British Standards |
Internal | Decision-makers | Ensure that minimum legal standards are met and could promote OHS through voluntary standards | Generally, top-management and middle-management; The employers |
Internal | Proposal makers | Apply daily the requirements imposed (legal or voluntary), and who can signal actions that can be implemented regarding OHS | Generally, employees and/or frontline managers |
2.3OHS in the COVID-19 workplace
Coronavirus (COVID-19) infection disease was reported in Wuhan (China) on December 31st, 2019, and subsequently spread around the world within the next few months. Currently, there are more than 200 countries that are confronting this pandemic. Compared to the Severe Acute Respiratory Syndrome (SARS), COVID-19 is more contagious, which has indicated a different fatality rate. The recent emergence of COVID-19 has devastated not only countries’ economies but also tarnished the image of health mechanisms among advanced and developing countries. The industries are confronted with the severe challenge of corona pandemic and face severe challenges of OHS Management Systems implementation. The primary objective of the OHSAS 18001 standard is to establish the business managerial measures relative to OHS [17]. A secondary objective of OHSAS 18001 implementation relates to its contribution to sustainable development through the preservation of human life and of the environment.
Occupational injuries and frequency of accidents can wreck both the organizational structure and employees’ perception. Occupational injuries are one of the foremost by-products of organizations and economies alike [41]. A staggering number of people faces preventable occupational injuries and fatalities around the globe. Occupational injuries are particularly perceived as an unintended event which affect working abilities of the workforce, damage equipment and interruption in daily activities [42]. To the staggering figures relative to employee safety [43], new concerns are added due to the physiological and psychological impacts of COVID-19 on workers. In this situation, both employers and employees should play their role to prevent the spread of the disease. The current situation is more challenging for organizations from moral, economic, and legal stand points. It is the responsibility of the organization to ensure a strict and efficient implementation of the OHSAS-18001 during the current pandemic situation. The importance of infection control plan can be neglected in the present scenario. Organizations can implement several measures in the workplace such as providing hand sanitizers/washing facilities, proper ventilation systems and cleaning those objects that are commonly touched. Occupational health and safety measures should be monitored and checked regularly [44].
The implementation of OHS within organizations must also consider current conditions. The implications of OHS and COVID-19 are presented in Table 2 (as a synthesis of [45–47]). An evaluation of the basic conditions related to OHS in the COVID-19 conditions was performed, followed by an attribution of responsibility for OHS directions to specific stakeholders.
Table 2
OHS and the conditions of the COVID- 19 period
Direction of OHS | Administrative control for COVID-19 | Level of the organization |
Identification of risk exposure | Using current methods and tests to identify critical cases | Safety Representative – SR |
Occupational risk assessment and treatment accordingly | Personnel protection equipment depending on the type of organization | Safety Representative – SR |
Organizing employees according to organizational activities | Reorganization of the number of employees on shifts | Top Management – TMMiddle Manager – MM |
Efficiency of working methods by using appropriate methods | Reducing contact with customers and intensifying the use of online contact methods (email, phone, video meeting, call meeting etc.) | Frontline Manager – FLM |
Efficient use of work areas | Designing a buffer zone of at least 2 meters for the inevitable meetings between the employee and the client. | Middle Manager – MM |
Providing optimal working conditions | Creating the opportunity to work from home for people who are vulnerable to COVID-19 or over 60 years of age. | Top Management – TM |
Own cleanliness and safety of employees | Increasing the level of cleaning and disinfection of objects by employees (handles, railings, workstations, parts, equipment) | Frontline Manager – FLM |
Proper collection of hazardous waste for employees and the environment | Providing boxes for collecting masks, gloves and other equipment used for COVID-19 protection. | Safety Representative – SR |
Correct information of stakeholders | Removing magazines from waiting rooms, customer catalogues and other documents that can be accessed by many people. | Frontline Manager – FLM |
Employee hygiene | Frequent cleaning and washing of work equipment. | Safety Representative – SR |
Proper use of workspace doors | Existence of at least two doors for rooms with several employees. | Middle Manager – MM |
From a historical perspective, the OHS directions in COVID-19 environment are neither new nor innovative measures, but specific OHS issues that are derived from more global OHS considerations. The particularity of the COVID-19 work environment is that is shifts focus on specific preventive behaviours of more global OHS themes. For example, the OHS direction “Proper collection of hazardous waste for employees and the environment” is derived from the chapter “4.4.6 Operational control” of the OHSAS 18001(as supported also by [43, 48–50]).
In conclusion, the COVID-19 work environment makes OHS considerations more stringent and reinforce the need of a clear definition of OHS responsibility.
3The OHS responsibility multilevel model
Considering the arguments provided by the literature review, the authors propose that responsibilities within an organization can be consolidated in an internal chain of responsibility like that of the hierarchical organization, based on top, middle and lower management, workers and transversal bodies. The proposed model draws on Safety-II considerations, in which people within the organization are part of the solution to improve OHS [35]. Like the research approaches of [27 and 51], the authors consider that the internal chain of responsibilities does not influence the accountability of the head of the organization but clarifies individual responsibilities. Based on the literature review, the head of an organization must establish an organization that will allow a clear and distinct definition of roles and responsibilities. By analogy to the organization chart of a company and coherent with the research presented in [52], we propose a division of responsibilities throughout the hierarchical levels of the company (multi-level approach). Thus, the proposed conceptual framework for the internal division of OHS responsibility is a Multilevel Model for OHS stakeholders which structures responsibilities as cascading among the organizational stakeholders.
Responsibilities are corollaries to any task. When achieving a task, an employee must accomplish it on time, on scope and within quality expectations, while also respecting the safety and health of both himself and others.
If we compare the OHS responsibility of an organization to a square, each stakeholder that interacts with the organization (internally or externally), does so within a certain area of the square, which corresponds to his share of responsibility. Ideally, each stakeholder operates within the boundaries that are set for him. In order to operate within this set perimeter, the first condition is knowing the limitations of the perimeter; it is completed by having the necessary knowledge regarding the work environment, the tasks, having had proper training and clear feedback on how tasks should be accomplished and what are the risks incurred. Therefore, individual responsibility is defined so as everyone can understand the limits of what one can do without damage to human or property. OHS events are facilitated when dysfunctionalities appear either through: a) overlapping same level responsibility of two or more stakeholders, meaning that the stakeholders have concurrent responsibility with equal decision-making latitude or b) absence of attributed responsibility, meaning that OHS items exist outside any stakeholder perimeter.
From a legal standpoint the head of the organization bares ultimate accountability for OHS, whereas from a managerial standpoint he/she cannot create, implement, and maintain alone the OHS system of the organization. Thus, from a managerial perspective, each member of thetop-management team can be attributed a series of ensued responsibilities that are sub-responsibilities of those of the head of the organization. Through iteration, each hierarchical level is associated to an ensued responsibility, directly linked to and ensued from that of its immediately superior hierarchical level. Further, is obtained a theoretical internal chain of responsibilities under the form of an OHS Responsibility Multilevel Model that is presented in Fig. 1.
Fig. 1
OHS Responsibility Multilevel Model.
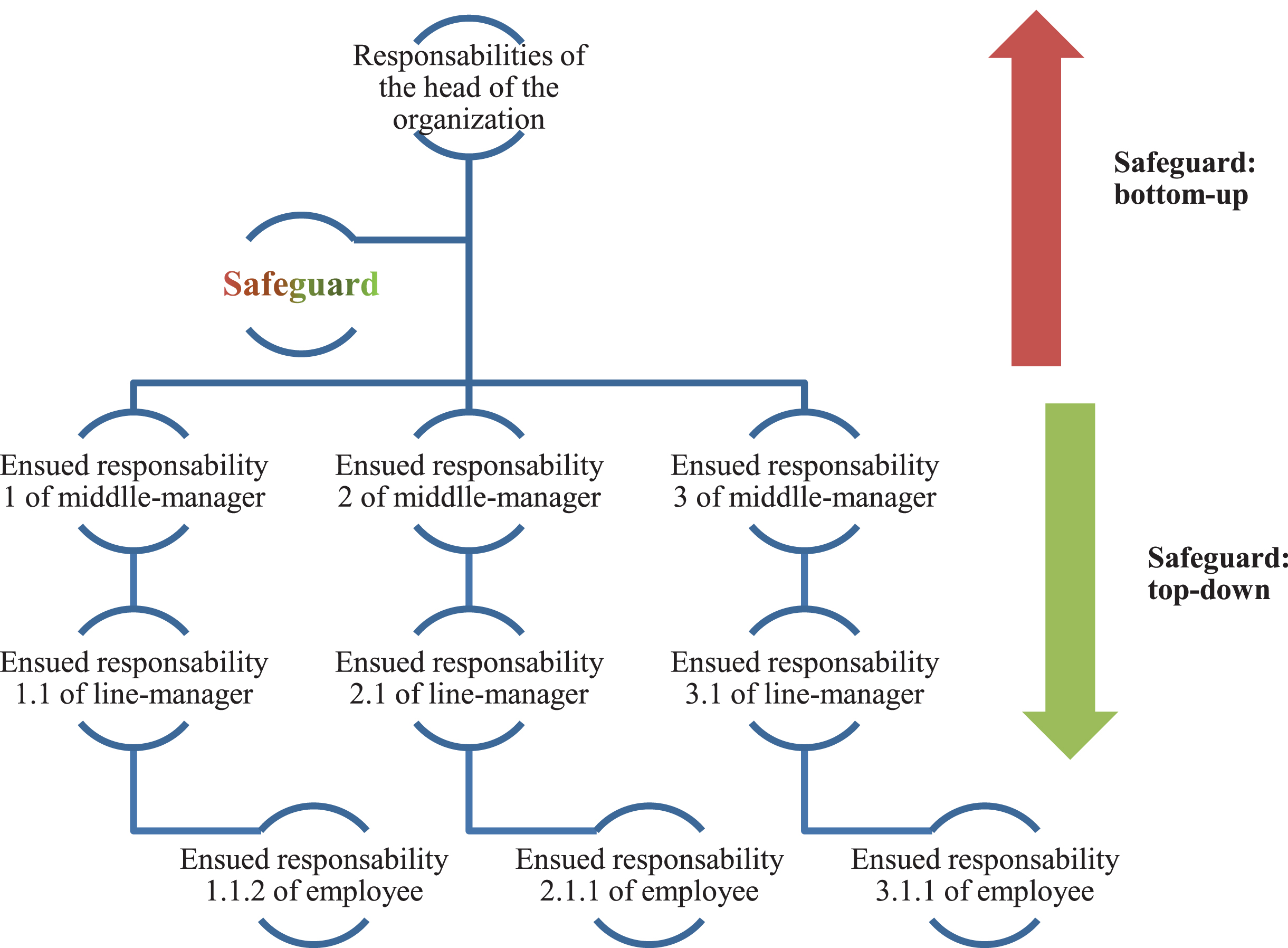
In constituting the chain of responsibility, we shall consider that an ensued responsibility is a shared responsibility of the upper and lower hierarchical level, but with different decision spans for each hierarchical level. The model structures the stakeholders of an organization so that they can each contribute to OHS at their own level of intervention, to the extent of their capabilities and the resources at their disposal. This approach aims at avoiding situations where front-line managers are designated as work environment responsible, without appropriate means for reducing or diminishing risks [46]. The working hypothesis is anchored in literature findings considering that one duty can be owned simultaneously by one or more parties [39], as managers, at all levels, are representatives of the employer [17].
In the proposed Model, certain stakeholders act as Safeguards, among which the internal Safeguards are the OHS representatives and/or the trade unions, whereas external Safeguards are the regulatory bodies. Thus, Safeguards can be either: top-down, initiated by the superior hierarchical levels or by binding external actors (such as legal enforcement on company management) or bottom-up, where information springs from the lower hierarchical levels or non-binding outside actors (as in the case of the certification companies’ interactions with organizations). For the OHS Responsibility Multilevel Model, the authors have considered only the internal Safeguards as these pertain to the internal organization.
4Application of the OHS responsibility multilevel model
4.1The research method
The present chapter shall present the method for the implementation of the proposed OHS Responsibility Multilevel Model with respect to the OHSAS 18001:2007.
The implementation of OHS Management Systems, specifically in the framework of OHSAS 18001:2007 standard, demonstrate a strong organizational commitment to OHS [51]. The literature review brought forward the existence of numerous OHS stakeholders, but also pointed out a real concern regarding the clear definition of their roles and responsibilities in OHS implementation within “the internal responsibility system” [53]. As presented in [50], authors have one of the rare research efforts addressing the research gap of “who is responsible for this OHS dimension within the organization?” through a case study of a growing global organization in the steel industry. Unfortunately, this research is contextualized to a specific moment of the lifecycle of an organization (reorganization following the integration of new units worldwide) [50].
Consequently, the present research explores the question: When constituting an internal chain of responsibility, which organizational stakeholder should be responsible for each item of the OHSAS 18001:2007? In our research vision, the result is a conceptual canvas for attributing internal OHS responsibility, without bias of sectorial or geographical considerations. This internal chain of responsibility is achieved by linking the items of the OHSAS 18001:2007 standard to organizational stakeholders identified through the literature review.
From the methodological perspective, in the first stage, the authors reviewed all the items of the OHSAS 18001:2007 standard to establish if the document specifies whether responsibility for an item is attributed:
• Implicitly, i.e. inferred, based on related items that responsibility falls upon a stakeholder;
• Explicitly, i.e. when the item names the stakeholder within the organization upon whom the responsibility falls upon.
It was observed that there are few responsibilities that are namely attributed to a hierarchical or functional level, but mainly to the organization. In addition, during this first assessment of the OHSAS 18001:2007 standard, it was observed that items are composed of several individual actions.
Consequently, in the second stage of the approach, all items were decomposed into individual actions, based on the expressions “someone verb something” or “something verb”. If an item included any combination of verbs, the item was divided into as many individual actions as verbs present; for instance, an item including “establish, implement and maintain”, was divided into three separate individual actions: one around “establish”, one around “implement” and one around “maintain”. This decomposition has led to a total of 304 individual actions.
Following, in the context of the third stage of the present research approach, the authors attributed to each of the OHSAS 18001:2007 standard individual actions an internal stakeholder based on the OHS Responsibility Multilevel Model. By integrating these responsibilities in the hierarchical Multilevel Model of the organization, the authors defined an internal chain of OHS responsibility. The purpose of this association was to bridge the gap of responsibility attribution in the implementation of the OHSAS 18001:2007 standard.
4.2Results and discussions
The present chapter will discuss the practical implications and the utility of the designed Multilevel Model for OHS stakeholders’ responsibility.
The first step of the research consisted in reviewing the OHSAS 18001:2007 standard items with the purpose of identifying the prescribed organizational stakeholder responsible for each item (completed with a quantitative approach). The identification of the responsible stakeholder was based on implicit or explicit designation in the standard, according to the previous methodological explanations.
Three stakeholders were identified for 68 items: the organization, top-management, and management. If the standard clearly attributes responsibility for 10% of its items to top-management, around 89% are attributed to the whole organization without any further detail regarding hierarchy or function (Table 3, Fig. 2, and extended results are shown in Appendix A). This is hypothesised to be due to the wide application spectrum intended for the standard and is coherent with the findings of the literature review, which considered top management as owners of general duty.
Table 3
Implicit and Explicit attribution of responsibilities
Responsibility is attributed to | Number of OHSAS Items |
Management – Explicit | 1 |
Organization – Explicit | 44 |
Organization – Implicit | 16 |
Top Management – Explicit | 4 |
Top Management – Implicit | 3 |
Fig. 2
Implicit and Explicit attribution of responsibility in the OHSAS 18001:2007.
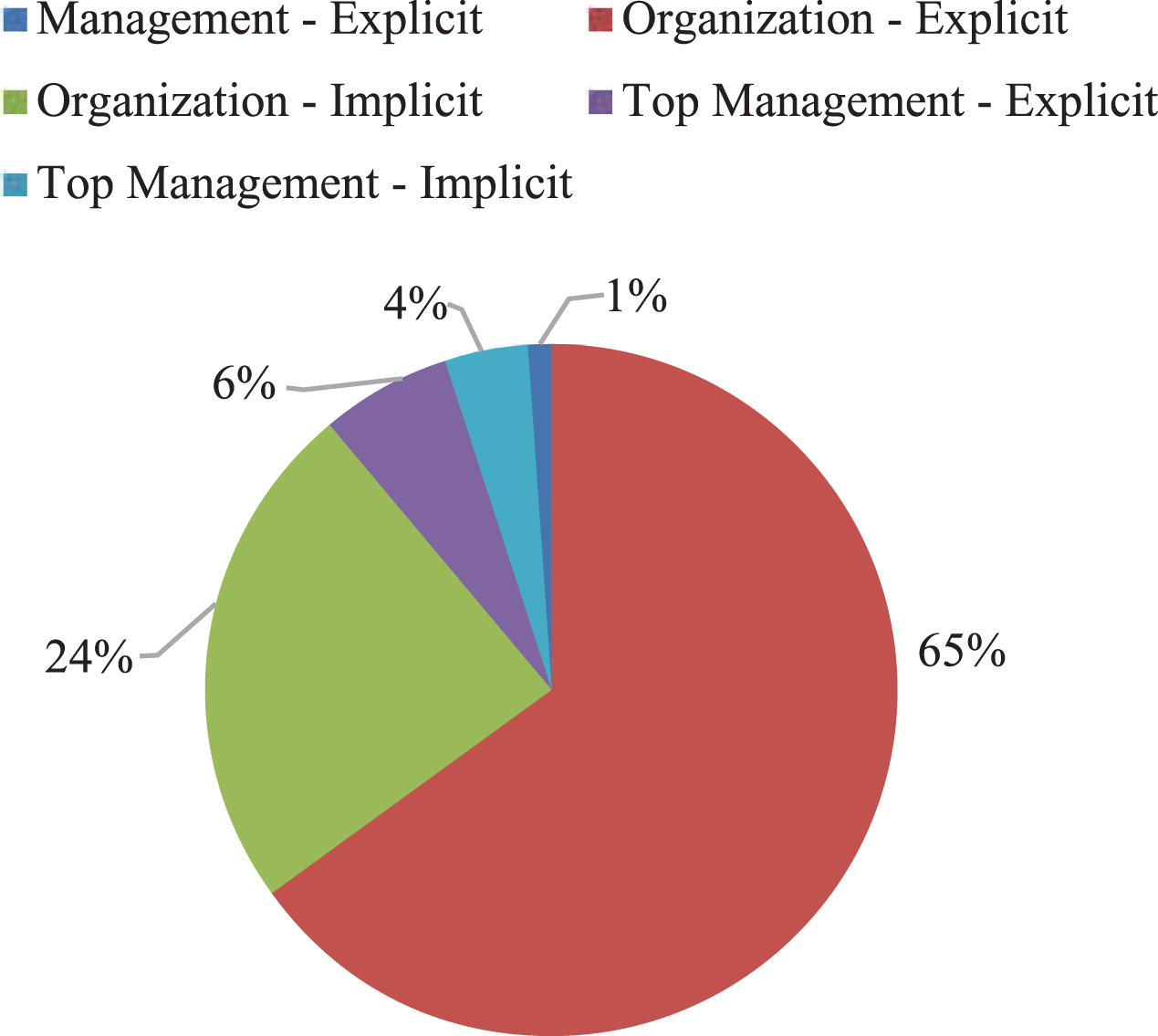
During this first analysis, it was concluded that numerous items of the OHSAS 18001:2007 standard are compounds of several actions. The authors thus considered it appropriate to divide the items into individual actions (according to the methodological approach), which led to the identification of a total of 304 actions. Following, actions were reviewed and associated with an internal stakeholder based on the findings of the literature review. A detailed quantitative synthesis is presented in Table 4 (graphical representation in Fig. 3). Extended results of the association are given in Appendix B.
Table 4
Responsibility attribution according to the OHS Responsibility Multilevel Model
Level of the OHS Responsibility | Number of actions for which the |
Multilevel Model | stakeholder is responsible |
Frontline Manager – FLM | 37 |
Middle Manager – MM | 51 |
Safety Representative – SR | 97 |
Top Management – TM | 119 |
Total | 304 |
Fig. 3
Responsibility attribution according to the OHS Responsibility Multilevel Model.
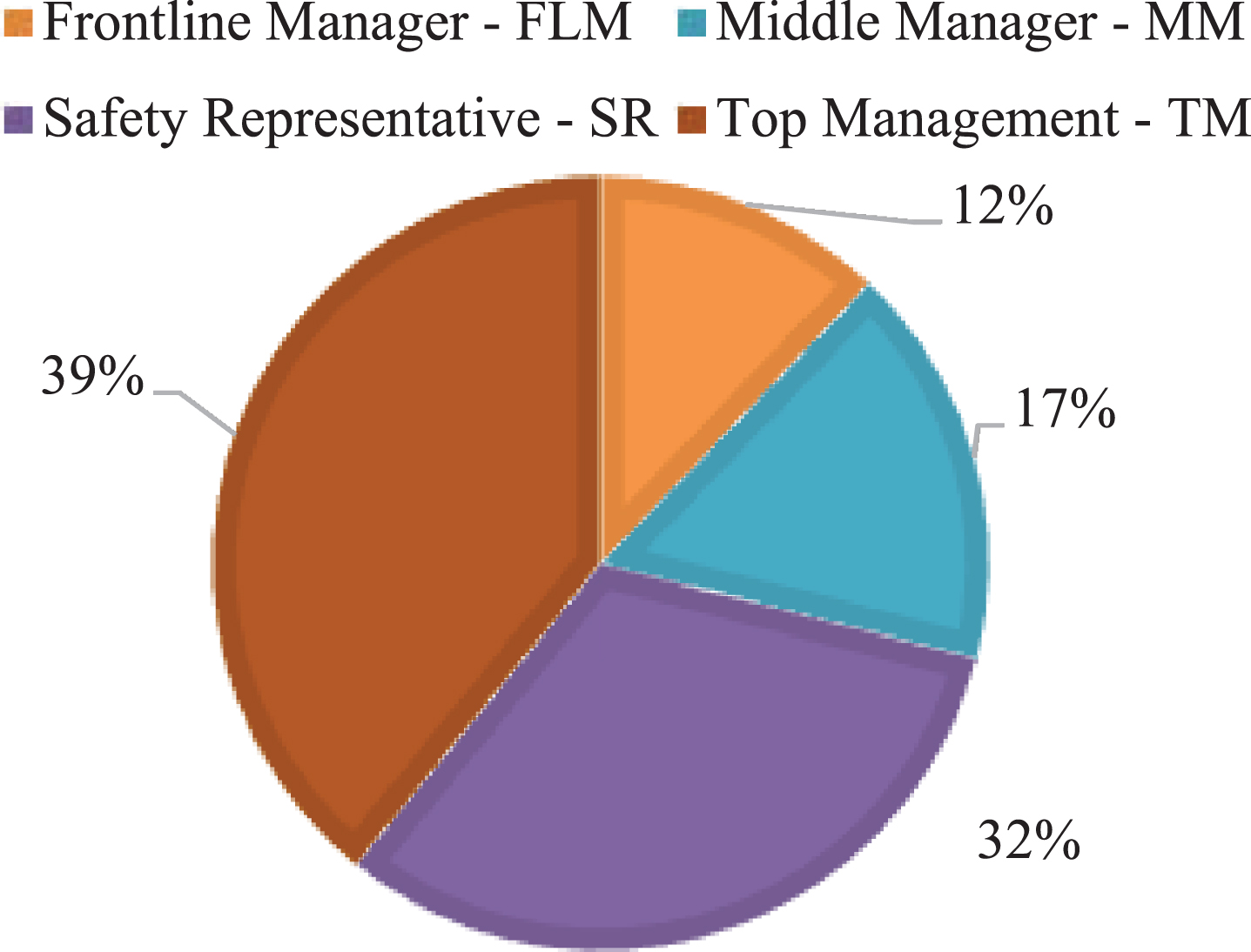
Regarding the correlation between the literature review and the responsibilities stemming from the OHSAS 18001:2007, it is to be noted that the literature review demonstrated that OHS issues transcend industrial contexts (including healthcare or education) rendering the coupling stakeholder - OHSAS 18001:2007 standard robust to sectorial considerations.
In coherence with the conclusions of the literature review, it was considered that the responsibilities of the employer are transferred upon top management. This hypothesis is based on an organizational perspective and does not include legal considerations which are out of the scope of the present work. Furthermore, this hypothesis is anchored in the conclusions that employer and/or top management responsibilities are mostly the same across countries and industries. Moreover, as the OHSAS 18001:2007 standard requires compliance with minimum legal requirements applicable in the organization’s industrial sector and stemming from the different regulatory frameworks, it is considered that the internal chain of responsibility developed for the OHSAS 18001:2007 respects all external responsibilities.
As the literature review concluded to a decline of the role of trade unions in the OHS problematics, but a more favourable position for the safety representative, the internal Safeguard stakeholder that was considered in this analysis was the safety representative. Considerations regarding the nomination of the safety representative were set aside to favour wide applicability of our findings (across industries or company sizes or legal requirements).
The coupling of responsibilities stemming from the OHSAS 18001:2007 standard to organization’s stakeholders allows us to conclude, as presented in Fig. 3, that top management (TM) is responsible for 39% of the identified actions, their responsibilities including policy definition and policy guardianship. Middle managers (MM) and frontline mangers (FLM) are responsible for a total of 29% of the identified actions. The responsibilities of middle managers (17% of identified actions) gravitate around their role as: implementers and communicators. The analysis of the actions for which they are responsible confirms their role as link between top-management as policy establishers and frontline managers as operational implementers on the sharp-edge. Finally, the front-line managers (12% of actions) are responsible for policy implementation and they act as communicators towards workers. They seem to play a small role in policy establishment, which seems coherent with their proximity to employees/workers and being distanced to upper-management strata. Nonetheless, they have a responsibility in signalling incoherencies between the rules established and the real working processes and environment in a bottom-up approach.
Concurrent with the literature review, the application of the OHS Responsibility Multilevel Model shows that the responsibility of the safety representative (SR, 32% of identified actions, Fig. 3), is very complex and widespread, including the traditional prevention role through conformity and hazard analysis and audits, but also policy contributor (he/she contributes to the policies established by top- management as expert on OHS problems), policy maintenance officer (maintains policies established by top-management), training contributor (assesses training needs as regard to OHS problems in the organization) and document guardian (insures the whole process documentation of the OHS system). Thus, the safety representative’s role is extended to that of a transversal manager (outside hierarchical strata) as also accountable for actions in accordance with provisions stipulated by OHSAS 18001:2007 standard, such as:
• The participation of workers (under 4.4.3.2 Participation and consultation);
• Monitoring and measuring performance (under 4.5.1 Performance measurement and monitoring);
• Dealing with nonconformities, accidents/incidents (under 4.5.3.1 Incident investigation and 4.5.3.2 Nonconformity, corrective action and preventive action).
It is to be noted that although the proposed conceptual model considers that employees can have responsibilities ensued from those of frontline managers, no such responsibility was defined among the individual actions identified in the OHSAS 18001:2007. This is also coherent with previous research which showed that employees’ primary responsibility is playing by OHS rules as induced by frontline managers.
Depending on the size of the company, the proposed model can be customized. Due to the fact that within the model different levels of organization have been identified, it is clear that the size of the organization can be from small and medium enterprises to large enterprises (in accordance with the organization of enterprises, depending on the number of employees).
As with operational responsibilities, it can be observed for the OHS chain of responsibilities that was obtained by applying the Multilevel Model to the OHSAS 18001:2007 standard, that there is a diminishment of the number of responsibilities throughout the hierarchical strata, in accordance with the stated hypothesis and findings of the literature review (responsibility is concentrated on top-management and is then cascaded on the lower hierarchical level). Simultaneously, any responsibility hinging on a lower- level is also included in the responsibilities of a superior level. In these regards, the proposed model is a response to performance variability, in which each hierarchical level can compensate or take necessary measures for the improvement or the fluctuation of its lower levels but also point-out anomalies or gaps in the performance of higher-levels, thus engaging a continuous improvement approach for OHS.
From the literature review perspective, in coherence with the results presented in [34] there have been stressed the need for guidelines on management responsibilities which would complete OHS standards, although ultimate legal accountability lies with the employer. Furthermore, the current context of COVID-19 work environments has stressed further the need of clarification regarding OHS responsibilities among organizational stakeholders.
In comparison with other research results or approaches achieved by other authors, most of them do not offer concrete solutions or a framework for defining responsibility in OHS, considering the stakeholders’ management, too. Even the ILO Guidelines in 2001 and other researchers [11, 14, 15, 28, 37, 50, 54] have considered and operate with ideas that OHS accountability lies with the head of the organization (top management), and the hierarchy distance and the defined responsibilities of senior and frontline management and also, of the top, middle and low level managers create an organizational model with an appropriate monitoring of the OHS system. Thus, the proposed OHS Responsibility Multilevel Model together with the discussions on its application have offer a feasible solution for the creation of a practical internal chain of OHS responsibilities. In addition, the creation position of a Safeguard (perceived as an internal or external stakeholder acting in the field of OHS as a “guardian”, depending on the company’s type and stakeholders’ power and interests) is considered an innovative solution for responsibility in OHS (not identified in the literature), supporting the practical application of the OHSAS 18001:2007 standard.
In addition, the presented research is aligned with the conclusions of [15], regarding the middle managers crucial and multiple roles in the OHS management. Despite the research conclusions and debates on the impact and capacity of middle managers (actions and behaviours) supporting safety management into organization, the proposed approach is based on the concept of the diffusion of OHS responsibility by different hierarchy managers and stakeholders. These create the premise of the safety and prevention culture development.
5Conclusions, limitations, and future research
The present research firstly underlines the relative complexity of the items in the OHSAS 18001:2007 framework; from the 68 items that are comprised under the six themes, the authors have identified 304 distinct actions. The application of the proposed OHS Responsibility Multilevel Model to the OHSAS 18001:2007 supports the interest that research literature has had for the role of top management in OHS. To apply the Model within organizations, they do not have to have certain characteristics; most important is the commitment of the organization’s management, as specified in Table 3. In addition, from the praxiological point of view and the OHS managerial perspective, the present research has offer two valuable tools for supporting organizational improvements (in the framework of the OHS Responsibility Multilevel Model adoption):
• Appendix A: OHSAS 18001:2007 Checklist of Safety Management System requirements and correspondent implicit or explicit responsibilities;
• Appendix B: OHSAS 18001:2007 Checklist of Safety Management System requirements - Division of responsibilities according to proposed model.
In addition, the presented Model was developed in the context created by the internal environment of a methane gas distribution company, in which the processes of assurance, evaluation-audit, monitoring and control of OHS activities could be observed together with the responsibilities, involvements of different managers and the commitment of different stakeholders. Indeed, the model is relevant and representative for large, even medium-sized companies, which have at least three levels or managerial hierarchies that are also associated with OHS responsibilities. In the case of small companies, the Model must be considered in its simplified, one-level way, and also, the compliance with the responsibilities of the OHSAS 18000 : 2007 standard is much simpler; but the safety issue is higher with decreasing company size, due to the lack of exemption of responsibility, regardless of prevention investments made. Only the assurance of exemption of responsibility can drastically improve OHS management (similar with the conclusions of [54].
Furthermore, there have been underlined by the literature that since its publication the OHSAS 18001 standard has gained considerable acceptance worldwide [55], and a large number of companies of various sizes and from different economic sectors have implemented it [55, 56]. The OHSAS 18001 standard aims to support and promote good practices in OHS through a systematic and structured management [56]. to protect workers’ health and safety. Thus, the designed and proposed OHS Responsibility Multilevel Model is following the statements on the OHSAS 18001 standard. One of the weaknesses of the proposed model, stems from its generality, as it may need to be adapted further for companies without intermediate hierarchical levels in cascading the responsibilities on the ones present in the organization.
Finally, it must be pointed out that the model considers only Safeguards that are internal to the organization and as such further research should consider the inclusion of external stakeholders. By adopting and applying the OHS Responsibility Multilevel Model, companies can register the following long term improvements: improving safety and health at work, increasing employees’ motivation, improving working conditions, reducing the number of accidents at work, preventing injuries and health problem of all categories of employees, reducing the levels of organizational risks, improving norms and legal commitment of organization’s management including the improvement of the OHS management system.
Further research areas can propose an empirical application of the theoretical findings, overview the integration between the internal and the external responsibility chain or undertake the exploring of OHS responsibility in the context of the supply chain. Thus, future research should consider the empirical study of different stakeholders’ involvement, interest, and commitment to the OHS management, but most how they support the investments in prevention activities in the field. Furthermore, future research in connections with other fields or OHS research areas could be dedicated to external stakeholders’ management, OHS costs (how investment in prevention activities could affect the accident costs), managers behaviour on supporting safety culture and safety leadership.
In conclusion, findings from this study aim at proposing a conceptual for cascading OHS responsibilities between the different hierarchical levels of an organization. The proposed OHS Responsibility Multilevel Model, which considers top, middle, and front-line managers, as well as the safety representative (Safeguard), provides guidance in the application of the OHSAS 18001:2007. The proposed Model is a first step in the direction of clarifying the responsibilities of stakeholders regarding OHS, an issue that is recurrently raised in research and industry and even more stringent in COVID-19 work environments.
Author contributions
CONCEPTION: Corina Dufour and Anca Draghici
METHODOLOGY: Corina Dufour and Anca Draghici
DATA COLLECTION: Corina Dufour, Anca Draghic, Larisa Ivascu and Muddassar Sarfraz
PREPARATION OF THE MANUSCRIPT: Corina Dufour, Anca Draghic, Larisa Ivascu and Muddassar Sarfraz
REVISION FOR IMPORTANT INTELLECTUAL CONTENT: Corina Dufour, Anca Draghic, Larisa Ivascu and Muddassar Sarfraz
SUPERVISION (cross-supervision): all authors and final validation Anca Draghici
SUPPLEMENTARY MATERIAL
[1] The Appendices are available in the electronic version of this article: https://dx.doi.org/10.3233/HSM-201060.
References
[1] | Fontaneda I , López MAC , Alcántara OJG , Ritzel DO . Gender differences in lost workdays due to occupational accidents. Saf Sci. (2019) ;114: :23–9. |
[2] | Nenonen N , et al. Global estimates of occupational accidents and fatal work-related diseases in 2014. Singapore: Workplace Safety & Health Institute. 2014. |
[3] | Fernández-Muñiz B , Montes-Peón JM , Vázquez-Ordás CJ . The role of safety leadership and working conditions in safety performance in process industries. J Loss Prev Process Ind. (2017) ;50: :403–415. |
[4] | Smallman C , John G . British directors perspectives on the impact of health and safety on corporate performance. Saf Sci. 2001. |
[5] | Webster, No Title. [Online]. Available: https://www.merriam-webster.com/dictionary/responsibility |
[6] | Webster, No Title. [Online]. Available: https://www.merriam-webster.com/dictionary/accountability |
[7] | Shah SGM , Tang M , Sarfraz M , Fareed Z . The aftermath of CEO succession via hierarchical jumps on firm performance and agency cost: Evidence from Chinese firms. Appl Econ Lett. 2019. |
[8] | Sarfraz M , Qun W , Shah SGM , Fareed Z . Do hierarchical jumps in CEO succession invigorate innovation? Evidence from Chinese economy. Sustain. 2019. |
[9] | Sarfraz M , Qun W , Abdullah MI , Tahir S . Authentic Leadership, Hope, Work Engagement and Creativity. J Appl Manag Investments. (2019) ;8: (1):19–31. |
[10] | Machida S . Guidelines on occupational safety and health management systems (ILO-OSH 2001). African Newsl Occup Heal Saf. (2001) ;11: :68–9. |
[11] | Cliff D . The management of occupational health and safety in the Australian mining industry. Int Min Dev Cent. 2012. |
[12] | Pilbeam C , Doherty N , Davidson R , Denyer D . Safety leadership practices for organizational safety compliance: Developing a research agenda from a reviewof the literature. Safety Science. 2016. |
[13] | Jamieson S , Reeve B , Schofield T , McCallum R . OHS prosecutions: Do they deter other companies from offending? J Heal Saf Environ. (2010) ;26: (3):213–231. |
[14] | Rezvani Z , Hudson P . Breaking the clay layer: The role of middle management in the management of safety. J Loss Prev Process Ind. 2016. |
[15] | Sarfraz M , Qun W , Abdullah MI , Alvi AT . Employees’ perception of Corporate Social Responsibility impact on employee outcomes: Mediating role of organizational justice for Small and Medium Enterprises (SMEs). Sustain. (2018) ;10: (7). |
[16] | Tan H , Wang H , Chen L , Ren H . Empirical analysis on contribution share of safety investment to economic growth: A case study of Chinese mining industry. Saf Sci. 2012. |
[17] | Tappura S , Syvänen S , Saarela KL . Challenges and Needs for Support in Managing Occupational Health and Safety from Managers’ Viewpoints. Nord J Work Life Stud. 2014. |
[18] | Conchie SM , Moon S , Duncan M . Supervisors’ engagement in safety leadership: Factors that help and hinder. Saf Sci. 2013. |
[19] | Abbas W , Wu W . Employee engagement, fairness and trust: An empirical assessment. Hum Syst Manag. (2018) ;37: (3):287–97. |
[20] | Koon V-Y , Ho T-S . Authentic leadership and employee engagement: The role of employee well-being. Hum Syst Manag. no. Preprint, pp. 1-12. |
[21] | Sarfraz M , Qun W , Shah SGM , Fareed Z . Do Hierarchical Jumps in CEO Succession Invigorate Innovation? Evidence from Chinese Economy. Sustainability. (2019) ;11: (7):2017. |
[22] | Pringle TE , Frost SD . ‘The absence of rigor and the failure of implementation’: Occupational health and safety in China, International Journal of Occupational and Environmental Health. 2003. |
[23] | Weichbrodt J . Safety rules as instruments for organizational control, coordination and knowledge: Implications for rules management. Saf Sci. (2015) ;80: :221–32. |
[24] | Wang L , Zeng J , Strohmaier D , Salam S , Shahzad K . Toward a service-innovation ecosystem of enterprises in China. Hum Syst Manag. 2019. |
[25] | Gey J-M , Courdeau D . Pratiquer le management de la santé et de la sécurité au travail: maîtriser et mettre en oeuvre l’OHSAS 18001. AFNOR, 2002. |
[26] | Hovden J , Lie T , Karlsen JE , Alteren B . The safety representative under pressure.Astudy of occupational health and safety management in the Norwegian oil and gas industry. Saf Sci. 2008. |
[27] | Arntz-Gray J . Plan, Do, Check, Act: The need for independent audit of the internal responsibility system in occupational health and safety. Saf Sci. 2016. |
[28] | Battaglia M , Passetti E , Frey M . Occupational health and safety management in municipal waste companies: A note on the Italian sector. Saf Sci. 2015. |
[29] | Bhattacharya S , Tang L . Middle managers’ role in safeguarding OHS: The case of the shipping industry. Saf Sci. 2013. |
[30] | Shahriari M , Abzari M , Nasr Isfahani A , Kianpour M . Learning, innovation and high performance in knowledge-based firms. Hum Syst Manag. (2017) ;36: (4):285–95. |
[31] | Makin AM , Winder C . A new conceptual framework to improve the application of occupational health and safety management systems. Saf Sci. 2008. |
[32] | Caroly S , Coutarel F , Landry A , Mary-Cheray I . Sustainable MSD prevention: Management for continuous improvement between prevention and production. Ergonomic intervention in two assembly line companies. Appl Ergon. (2010) ;41: (4):591–9. |
[33] | Hardison D , Behm M , Hallowell MR , Fonooni H . Identifying construction supervisor competencies for effective site safety. Saf Sci. 2014. |
[34] | Bluff L , Gunningham N . Principle, process, performance or what? New approaches to OHS standards setting. The Federation Press, (2003) . |
[35] | Hollnagel E , Wears RL , Braithwaite J . From Safety-I to Safety-II: a white paper, resilient Heal. care net Publ. simultaneously by Univ. South. Denmark, Univ. Florida, USA, Macquarie Univ. Aust., 2015. |
[36] | Daniellou F , Simard M , Boissière I . Human and organizational factors of safety: state of the art. FonCSI, 2011. |
[37] | Ranka S , Quigley J , Hussain T . Behaviour of occupational health services during the COVID-19 pandemic. Occup Med (Lond). 2020. |
[38] | Schmidt L , Sjöström J , Antonsson A-B . Is ownership the decisive factor in collaborations between occupational health services and client companies? Work. (2017) ;56: (2):309–18. |
[39] | Johnstone R . The legal framework for regulating road transport safety: chains of responsibility, compliance and enforcement. Compliance Enforc. 2002. |
[40] | Oldham K , Stanton J , Bilderbeck M , Spinetto J . Case study of a voluntary aviation safety and environmental accreditation programme. Saf Sci. 2017. |
[41] | Tan H , Wang H , Chen L , Ren H . Empirical analysis on contribution share of safety investment to economic growth: A case study of Chinese mining industry. Saf Sci. (2012) ;50: (7):1472–9. |
[42] | İnce H , İnce N , Ozyildirim BA . Occupational accidents and forensic medicine in Turkey. J Clin Forensic Med. (2006) ;13: (6-8):326–30. |
[43] | Chughtai AA . Creating safer workplaces: The role of ethical leadership. Saf Sci. (2015) ;73: :92–8. |
[44] | Seenivasan M , Arularasu M , Thirumalai R , Kumar KM . Implementation of Occupational Health and Safety Analysis in Manufacturing Industries. Asian J Res Soc Sci Humanit. (2017) ;7: (1):384–91. |
[45] | Fontaneda I , Camino López MA , González Alcántara OJ , Ritzel DO . Gender differences in lostworkdays due to occupational accidents. Saf Sci. 2019. |
[46] | Frick K . Work environment dialogue in a Swedish municipality-strengths and limits of the Nordic work environment model. Nord J Work Life Stud. (2013) ;3: (1):69. |
[47] | Garcell HG . Revista Habanera de Ciencias Médicas. 2020. |
[48] | Blin-Franchomme M-P , Desbarats I . Droit du travail et droit de l’environnement: regards croisés sur le développement durable (dir.), 1. Lamy, 2010. |
[49] | Ejdys J , Lulewicz-Sas A . An OH&S management system as a source of information. Int J Occup Saf Ergon. (2010) ;16: (4):445–54. |
[50] | Koivupalo M , Sulasalmi M , Rodrigo P , Väyrynen S . Health and safety management in a changing organisation: Case study global steel company. Saf Sci. (2015) ;74: :128–39. |
[51] | Bevilacqua M , Ciarapica FE , De Sanctis I . How to successfully implement OHSAS 18001: The Italian case. J Loss Prev Process Ind. 2016. |
[52] | Lingard H , Cooke T , Blismas N . Do perceptions of supervisors’ safety responses mediate the relationship between perceptions of the organizational safety climate and incident rates in the construction supply chain? J Constr Eng Manag. (2012) ;138: (2):234–41. |
[53] | Gillet-Goinard F , Monar C . La Boîte à outils en Santé-Sécurité-Environnement-2e éd. Dunod, 2013. |
[54] | Bianchini A , Donini F , Pellegrini M , Saccani C . An innovative methodology for measuring the effective implementation of an Occupational Health and Safety Management System in the European Union. Saf Sci. (2017) ;92: :26–33. |
[55] | Chang JI , Liang CL . Performance evaluation of process safety management systems of paint manufacturing facilities. J Loss Prev Process Ind. 2009. |
[56] | Chen C-Y , Wu G-S , Chuang K-J , Ma C-M . A comparative analysis of the factors affecting the implementation of occupational health and safety management systems in the printed circuit board industry in Taiwan. J Loss Prev Process Ind. (2009) ;22: (2):210–5. |