The practice of ergonomics as a design discipline in the basic design of oil platforms
Abstract
BACKGROUND:
Ergonomics is increasingly gaining ground in projects in the energy sector, as well as in the continuous process industry, although the discipline is still framing its space in this milieu. This issue emerges from the designers’ lack of familiarity with ergonomics work, especially in engineering design projects, combined with the usual expectations of organizations regarding the participation of ergonomists and the deliverables they ought to develop throughout the project.
OBJECTIVE:
This study aims to report the participation of a team of ergonomists in an oil platform basic design, discussing ergonomics structuring as an emerging design discipline.
METHODS:
This qualitative study used participant observation as a methodology approach aligned with the theoretical framework of Activity Ergonomics (AE). The data collection occurred between October 2018 and June 2020 in Rio de Janeiro, Brazil.
RESULTS:
The results show the challenges faced by the ergonomics team and strategies adopted in order to create technical specifications (TS), which will determine the work conditions in the future platforms. An evolution in relation to the practice of Ergonomics during this project can be pointed out, even though part of its scope of action remains to be better understood among the design team.
CONCLUSION:
Considering oil platform project contexts, this work highlights how ergonomics can help integrate the different rationalities that compose the design process.
1Introduction
Industrial design processes, such as those of oil platforms or power plants, were structured over time following a mainly techno-centric approach [1]. The increasing rigor of government inspections regarding work facilities in the energy sector in Brazil has contributed to enhance the emphasis on ergonomics in the energy industries.
Concomitantly, the emergence of new technological resources has also been transforming design dynamics. Within that context, ergonomics faces the challenge of building its own space in the project organization.
In a design process, one of the main contributions of ergonomics is to generate and disseminate knowledge about the work to be performed in the future situation, in a way that it can be applied to enrich design specifications [2–8]. This contribution is possible through the performance of reference situations’ analyses, which provide inputs for discussion with designers and, thus, allow them to make design decisions that foster both the health of workers and the productivity goals [9–12].
The Ergonomics Work Analysis (EWA) is a French-speaking ergonomics approach and is based on the identification of the nuances that differentiate the work as perceived by the designers and by the organization and what takes place in reality, or, in other words, between prescribed work and real work [4, 13]. The understanding of such differences brings a more realistic perspective of the activity to be performed by workers, as well as of the technical-organizational systems to be operated by them [12, 14].
This paper discusses the participation of an ergonomics team in an oil platform basic design. Preliminary results of these studies were previously presented at the IEA 2021 congress [15, 16]. This project differed from similar projects developed by the same company in the past by adopting a new design organization. Besides centering design activities on the 3D model, the company established ergonomics as an independent design discipline for the first time.
The premises of ergonomics participation accommodated a double ambition: the platform design was conceived with the purpose of being a benchmark project for platforms in the future, and; as for ergonomics, the project would be a benchmark for the discipline, with the purpose of generating documents, which would also serve as grounds for future projects.
This study aims to discuss the structuring of ergonomics actions, as well as the challenges faced in this project.
2Method
This study was conducted using a single case study involving the basic design of an oil platform, which took place between October 2018 and June 2020 [15, 16]. This qualitative research had its procedures for collecting and analyzing data guided by the theoretical framework of AE [9].
Participation in this project was possible through a cooperation agreement between the company and the university, linked to a research project. This partnership constituted an opportunity for the research team to actively participate in the project, whereas providing support to the company’s ergonomics team, and to collect data for developing doctoral theses by the researchers involved. The researchers adopted participant observation as methodology approach, which allowed us to monitor and participate in the activities as members of the project’ ergonomics team [17, 18].
The company’s goal was to develop a reference project for future platform construction demands. For that purpose, technical characteristics of an oil exploration field in an exploratory evaluation phase were considered, and the company’s platforms already in operation were used as a reference. For this reason, this stage was named Reference Basic Design (RBD). The basic design is the second stage of the project, after defining the concept study and preceding the detailed design and execution stages, respectively.
As discussed by Daniellou [12, 13], a great part of the work of ergonomics in a design process relates to the generation of knowledge about the work activity, seeking to bring the conception closer to the execution. For that purpose, 12 visits were made to 4 platforms identified as reference situations in order to better understand the real work performed in such units. The units were chosen for having similar characteristics - in relation to the process, exploratory field characteristics, etc. - to the ones proposed for the project.
More specifically, the reference situations analyzed were FPSO-type platforms (Floating Production Storage and Offloading), which started their operations from 2017 onwards. Like other platforms in the pre-salt area, these units have high production wells and gas with contaminants requiring different gas treatment systems.
The complexity of these platforms is mainly due to the high pressure of the collected gas. Therefore, the process area has more modules than other platforms. In the PBR, there are 17 modules with process systems, 8 of which are dedicated only to the production and treatment of gas. Hence, the composition of teams and activities developed in these reference units are also similar to those foreseen in the PBR and the information collected in these visits fostered discussions throughout the whole duration of the project.
The data gathered by the researchers during the 20 months of the project were organized into two categories for analysis: primary and secondary sources.
Primary sources included the field notebook, meeting minutes, records of events and interviews made by the researchers. The field notebook contained records of observations related to the project work dynamics, as well as records of dialogues between designers and actions developed. Independent documents were developed separately to record specific events such as meetings, design review sessions and workshops to anticipate construction and assembly issues. All records were in digital format and files were shared from the cloud among all members of the research team.
Secondary sources consisted of documents provided by the company, such as technical specifications from other disciplines, reports, plan views and 3D models.
The university’s main research team consisted of:
- 1 research coordinator: postgraduate professor of production engineering/ergonomics;
- 3 researchers: PhD students in production engineering (1 researcher with a degree in industrial design, 1 researcher with a degree in occupational therapy and 1 researcher with a degree in chemical engineering); and
- 1 intern: production engineering graduate student.
The group of professionals from the company who worked directly or indirectly on the project’s ergonomics team included:
- 1 internal Ergonomics consultant: the company professional responsible exclusively for Ergonomics on the project;
- 1 architect and 1 building technician: both worked on the architecture part of the project and supported the internal consultant;
- 1 production engineer: from the company’s research center;
- 2 HFE engineers: responsible for issues related to Ergonomics on platforms in operation in 2 regions (Rio de Janeiro and Espírito Santo).
In total, this basic design involved teams from 20 disciplines, listed in Table 1, where each discipline had a person in charge, called discipline representative (DR). The DRs were the key people for interlocution among teams. All teams worked simultaneously, according to the overall project schedule, sharing information and documents through the company’s internal online network.
Table 1
Basic design disciplines
Basic design - disciplines | ||
1. Architecture | 8. Commissioning | 15. Processes |
2. Arrangement | 9. Electric | 16. Safety |
3. Automation | 10. Ergonomics | 17. Naval Systems |
4. Design Automation | 11. Hull Structures | 18. Telecommunications |
5. Reliability | 12. Topsides Structures | 19. TBM (turbomachines) |
6. Constructability | 13. Mechanics/ Heating, Ventilating and Air Conditioning (HVAC) | 20. Cost engineering |
7. Weight control | 14. Naval |
The participation of the research team can be divided into two main periods: the first comprising the initial five months and the second comprising the remaining fifteen months.
Over the first period, the participation of researchers was limited, depending on the invitation of project coordinators to attend specific meetings involving issues related to ergonomics. In addition to participating in the meetings, this period included the beginning of analysis in reference situations, as well as the development of preliminary versions of reports and technical specifications addressing ergonomics. Even though those were not final versions of the documents, they were developed to serve as a basis to discuss the work characteristics, based on observations made previously, in different reference situations.
More specifically, in this initial stage, the ergonomics team used guidelines developed in 2009 - also based on a partnership between the company and the university - as a starting point for the new documents. These guidelines have been developed for application at broader levels of generality, such as design guidelines, basic design orientations, planning and organization of design activity.
In the second period, from the fifth month onwards, the three researchers had easier access to the project site, no longer depending on invitation for each visit. This was a turning point for the researchers, as it allowed us to better monitor and participate in design activities. This fact also favored to conduct interviews with specific stakeholders, from which we highlighted: members of the arrangement, automation, architecture, and ergonomics teams. Interviews were short and semi-structured, lasting approximately 10 to 15 minutes. The purpose of these interviews was to gather information on new work practices in design, considering this changing context.
Updated versions of the technical reports and technical specification documents were afterwards used to support the development and validation of final recommendations [7].
These documents were structured according to a predefined scope, which defined the deadlines and deliverables of each discipline. Table 2 presents Ergonomics-related activities planned by the company.
Table 2
Ergonomics team activities foreseen in the project schedule
Task | Discipline | Start | End |
Ergonomics Requirements for Hull | Ergonomics | 07/16/18 | 12/21/18 |
Ergonomics Report for Hull | Ergonomics | 12/18/18 | 03/21/19 |
Descriptive Memorandum - Ergonomics | Ergonomics | 07/11/19 | 09/30/19 |
Comments on documents from other disciplines | Ergonomics | 07/16/18 | 02/10/20 |
Ergonomics Requirements for Hull | Ergonomics | 07/16/18 | 10/01/18 |
Ergonomics Report for Topsides | Ergonomics | 10/30/18 | 05/08/19 |
The research team monitored the project throughout 20 months, including the following actions: observation, meetings, and assistance with demands from other disciplines, project documentation development, events, and interviews.
Among the events foreseen in the project, the Design Review (DR) sessions stood out from the perspective of the possibility of integrating Ergonomics into the design solutions.
The DR are meetings where designers from different disciplines propose points relevant to their area in advance, which shall be analyzed and discussed by the interdisciplinary group using the 3D model as a reference.
Such events are part of the control points foreseen in the project, and are articulated around 3 main control phases, which correspond to the completeness percentages of 30%, 60% and 90% of the 3D model.
As a result of the basic design stage, all documents generated are passed on to the designers - and ergonomists - involved in the detailing design and execution.
3Results
The participation of the ergonomics team in a more autonomous way in this oil platform basic study was one of the factors that contributed to the transformation of the ergonomics practice in this context. In this company’s previous oil platforms design processes, ergonomics was not considered a design discipline. Ergonomics studies and guidelines were included only in documentation from other disciplines – mainly in architecture – and, in addition, the studies were carried out mostly in the final stages of the project, such as in detail studies or at the shipyard, during the construction and assembly stage.
Even though ergonomics was considered as an independent discipline in the basic design, in the internal document that defines the bases of the oil platform design, references to ergonomics attributions appeared distributed in chapters of other disciplines, such as:
- In the Arrangement chapter, it was requested that “ergonomic aspects be considered, such as adequate access to equipment and valves, according to the frequency and specific use (emergency, normal operation, maintenance, etc.)";
- In the chapter related to the Health area, it was required the “carrying out of ergonomic studies in the project, in order to identify, in advance, the conditions for performing future tasks, observing the inadequacies of working conditions for operation and maintenance of machinery and equipment, taking into account the possible problems and difficulties that could result for the workers/users in the project";
- Still in the Health chapter, other demands included: that the EWA should be based on a similar situation, that an ergonomics report should be developed with a synthesis of information and proposals for improvement, adequate sizing of furniture and equipment in the accommodation module and area recommendations minimum to be analyzed for the Topsides area project.
As previously mentioned, as this was the first time that ergonomics has participated in the basic design as a discipline, there was no specific chapter for ergonomics in the design basis document, as well as there was no clear scope for sizing the team or for the activities planned for it.
Thus, the discipline was officially composed only by one internal Ergonomics consultant, who received support from researchers, in addition to other company designers, technicians and engineers. This joint work allowed the ergonomics team to interact with the other actors involved in the design.
3.1Dynamics of the participation of ergonomics in the design
Considering the aforementioned context, ergonomics practice had to be structured during the course of its actions in the project. To that effect, the meetings held in the early months of the project helped define design objectives and dynamics, as well as the demands related to ergonomics as a discipline. Even so, the development of Ergonomics deliverables demanded a flow of (inter) actions from the team beyond the prescription of the design basis. A summary of the articulation of the ergonomics team to meet the demands of the basic design is described below.
The first TS were generated based on documents from previous designs developed by the company. These, in turn, were written using as reference the results of a research project developed in 2009, on the integration of ergonomics to the project addressing offshore platforms (also a result of a research project in partnership with the university). The content of this document has been revised and amended, as deemed relevant to the new design. Aspects related to the platform production characteristics and other aspects defined in the conceptual design were reviewed to verify similarities or differences between the previous projects and the RBD.
In parallel, embarquements of the ergonomics team were scheduled on platforms selected as reference situations. The embarquements provided the ergonomics team with information to develop technical specifications that considered as much as possible the specifics of the activity carried out in a real context, in a way that this knowledge could be integrated into the project from the basic design stage.
As the embarquements took place in reference situations, the Ergonomics team was able to verify, in the field, whether the initial premises for preparing the TS remained applicable. On these occasions, the researchers monitored the activities considered most critical for each system and discussed the TS proposals with users, articulating new proposals for improvement, when possible.
However, before making changes to existing documents, the ergonomics team discussed the proposed changes with other disciplines that could be affected by the modification.
It was noticed that, in certain situations, the demands had specific technical character, where the ergonomist acted as a facilitator of communication between users, who reported difficulties and proposed practical solutions; and designers, who retained the decision-making power and technical knowledge needed to assess the feasibility of changes. For some of these discussions, the 3D model was used as a resource to facilitate the dialog between designers and ergonomists.
This process of development and justification of the guidelines proposed in the Ergonomics TS resulted in the content of two reports: related to Hull and Topside aspects. In this way, the team’s cycle of activities was constantly feedback.
Simultaneously to these activities (which were predominantly internal to the discipline), other design disciplines had access to the ergonomics design documents through the internal network and were encouraged to make comments, such as doubts, changes or, mainly, indications of discrepancies or interferences with their own scopes and design documents.
The same activity was carried out by the ergonomics team, in order to frequently check the documentation of the other teams for comments. Figure 1 illustrates the dynamics of the main activities of the Ergonomics discipline.
Fig. 1
Dynamics of ergonomics activities.
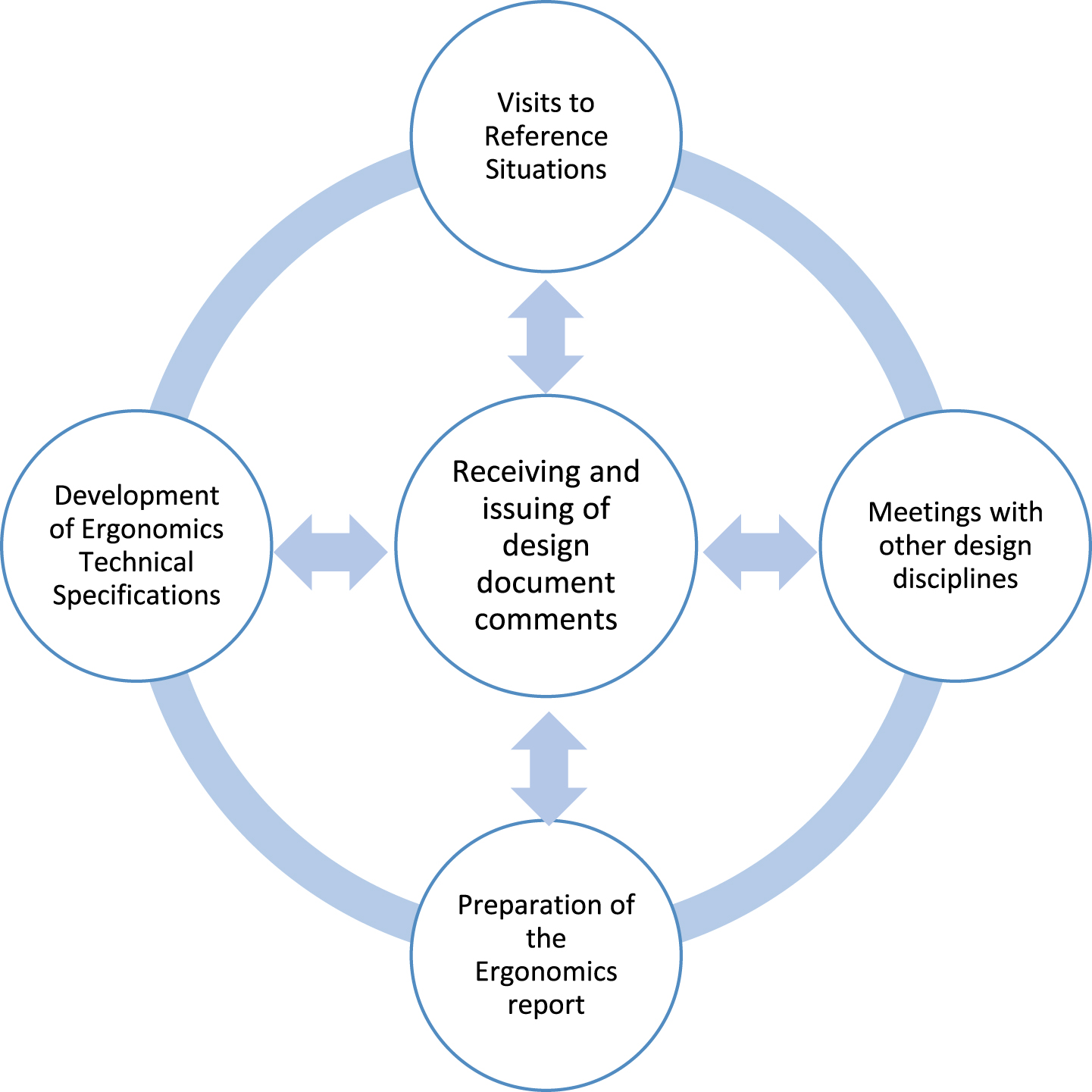
In the project site, teams from all disciplines worked on the same building floor. The proximity of the teams provided by this organization encouraged and facilitated exchanges and interactions throughout the project’s progression. The researchers’ access to this environment – which was facilitated from the fifth month onwards – allowed us to monitor and participate more actively in this dynamic, especially in ergonomics-related subjects. The ergonomics team was often asked to provide support or participate in the resolution of demands originating from other teams.
Thus, in addition to the meetings that included the participation of the ergonomics team, we were also able to engage in spontaneous discussions related to the design. This closeness also favored the conduct of interviews, which helped researchers grasp the perception designers had of the new design dynamics and the role of ergonomics.
It was perceived as a common practice for designers to circulate around the floor to ask questions or discuss design solutions, especially when they were simple doubts. Spontaneous meetings were also common, at the workstations, involving 2, 3, or more disciplines.
This practice was considered positive from the perspective of the social construction of the project as a whole, allowing actors from different teams to establish a good flow of communication and integration. However, at times, the procedures and formal records lost their dynamics in their updating.
This means that, although the project documents were stored in the internal data system, the versions made available in the system were not always updated. In most cases, when a team needed information from another discipline, it was unreliable to go directly to the system to obtain the data, and it was necessary to contact the discipline’s team to confirm the reference to be used.
Nevertheless, the ergonomics team participation made it possible for other teams to better understand the discipline’s scope of action, which went beyond the six assignments initially attributed to ergonomics, shown in Table 2.
3.2Ergonomics, 3D model and design review
One of the basic design assumptions, described in the TS of the design basis, established that the studies should be directed to develop the process plant arrangements in 3D. Thus, as mentioned previously, this type of organization encouraged new work dynamics, with more integration around the aforementioned resource.
As this was the first time that the company was developing the basic design internally and directly on the 3D model, it was also the first time that design review sessions were held in the basic design stage.
In the previous platform designs developed by the company, before the RBD, the disciplines of arrangement and structures were the main users of the 3D model. However, at least in the basic design stage, there was no systematic verification procedure for the 3D model. Basic Design Review sessions were held using traditional 2D blueprints.
The 3D model was used only in the verification of the detailing stage, but with less possibility of alterations, since a modification in this stage is more likely to result in alteration of other parameters already established and to increase costs.
As there was no systematic verification of the 3D model in the basic design stage before, it was necessary to create a Design Review pattern for this stage, which was based on the existing model for the detailed design of previous projects.
According to the company’s internal procedure, which provided guidelines for conducting design review on basic surface projects, the following parameters should be considered:
- Design Review sessions should be prepared using visualization files in CAD/CAE 3D tool format used throughout the project;
- Checklists (CL) should be applied as the scope of the Design Review sections. Additional checks could be performed, especially related to the disciplines of ergonomics, operation, accessibility, constructability and maintainability, among others. In these cases, the notes made should be registered in additional lines of the CL used in the verification;
- Design Review sessions should be held in a room equipped with adequate resources for viewing the 3D model;
- Design Review events should be mandatory multidisciplinary, involving all disciplines of basic design.
The first general CL made available in the system for the 30% DR, which, in turn, was developed based on DR carried out in previous projects, did not present any specific ergonomics item. The only two ergonomics check items were generic, as shown in Table 3.
Table 3
Items for ergonomics’ verification in the preliminary CL of the 30% DR
Ergonomics |
Hull ergonomics |
Topsides Ergonomics |
The ergonomics team first action in relation to the DR was, therefore, to analyze the list received, seeking to verify items from other disciplines that were related to Ergonomics. For example: the item “Integration between cranes and main access ways (longitudinal and transverse)” was inserted in the ergonomics CL for verification, relating to the disciplines of cargo handling and arrangement. Additionally, items for verification from the content of the Ergonomics TS were also inserted.
However, after the team developed a first version of the list with approximately 100 items (listing the item to be checked, the disciplines involved and the corresponding work situation), the team spoke with the DR coordinator, who requested that the list were modified, in order to have more “direct” items to be verified. As a result, the ergonomics CL for the 30% DR, for example, had 20 items for verification, as shown in Table 4.
Table 4
Ergonomics CL items (DR 30%)DR
Ergonomics |
1. Integration between cranes and main access ways |
2. Integration between the interior of modules and main access ways for cargo handling. |
3. Compatibility of the tracks (dimensioning) with the heaviest loads (ET handling). |
4. Cargo handling devices or mobile device space for loads above the recommended weight for manual transport (assessing frequency) |
5. Check access (platforms, stairs) to overhead cranes for maintenance |
6. Check balustrades in cargo areas |
7. Check metal guardrails and handrails near cargo areas |
8. Check the location of the chemical deck (it must be accessed by the main crane and allow movement of liquids by gravitational force) |
9. Check layout of chemical storage area to ensure space for cribs and connection station |
10. Check crane access ladders and alternative access to adjacent modules |
11. Check the route of diving equipment from the cargo area to the location of use (consider diving bell for two divers / dimensions and facilities) |
12. Has interconnection between modules and via pipe rack been provided for at all possible times? |
13. Check access (platforms, stairs) to elevated maintenance equipment |
14. Check for spiral ladders (should not be used, except in tanks or metallic structures with a diameter greater than 2.4 m) |
15. Laboratory - Check location (located in the production area or between the accommodation module and the production area) |
16. Laboratory - Check possibility of two accesses |
17. Laboratory - Check proximity of toilet for technician |
18. PIG Launchers/Receivers - Check free space in front of chambers |
19. Vessels - Check accessibility of manholes |
20. Heat exchangers - Check the area and route for removing the beams from the exchangers (or from the exchanger itself in case of fixed mirror), checking the interferences |
4Discussion
The early stages of the design process, such as the basic design, often offer greater possibilities for change, as this is a stage when guidelines, specifications and basic concepts are still being defined. The participation of ergonomists from this stage of the design process is an opportunity for the discipline to participate in discussions and changes in relation to the environment and working conditions of future units [8].
It is acknowledged that the early participation of ergonomics in the design process provides greater potential to influence design decisions that will reflect in the work environment in a cost-efficient way [4, 5, 7], however, studies addressing this issue involving oil platforms projects are less frequent. Among the contributions of the ergonomics team to transformations in the project, we can highlight the following: changes related to cargo handling resources and routes, access between modules (for circulation of workers) and access to equipment for operation and maintenance, layout of internal environments such as workshops, control room, infirmary and galley / messroom, among others.
Indeed, especially when it comes to engineering designs, the role of ergonomists does not yet seem to be well defined. Also, the scope of action of ergonomics does not seem to be clearly understood at this point, which means that some teams still have questions as to how, or even to which extent, ergonomics can contribute to other disciplines.
In certain cases, ergonomists can be seen as experts who contribute to the project by offering support through their knowledge of ergonomics practice and methodology. In others, they may be requested as facilitators, as a means of communication between managers, designers and workers, or users [19]. In many situations, engineers and ergonomists lack experience in working together [20, 21].
Creating deliverables for ergonomics discipline requires its own specific development process, which involves, among other actions, understanding the real work by analyzing reference situations.
Time and resource constraints are challenges shared by many disciplines involved in the design process. As discussed by [20], in the insertion of ergonomics in projects, these difficulties are translated, for example, in the difficulty of vacancies for visiting reference situations, in the synchronization of the timing of embarquements with the project schedule or demands, etc.
Ergonomics practice in projects involves hard-to-quantify actions. This relates to the difficulty of anticipating the demands directed at the ergonomics team throughout the project and the process of treatment that each type of demand requires. This can sometimes be misunderstood as an inability of ergonomists to follow the structure (planning, delivery and evaluation) of the design process [22].
An example is the case of the batteries handling study, which arose from the identification of an issue raised by the ergonomics team during the Design Review 30%. Discussions on batteries usage, maintenance, and handling needs generated a succession of ergonomics actions and interactions with different teams:
- With the users, in the reference situation, to understand the specifics of the real work;
- With the electrical design team to discuss technical specifications of equipment and manufacturers’ requirements;
- With the architecture design team to discuss battery rooms layout;
- With the cargo handling design team to define the handling resources for the equipment.
The translation of this ensemble of knowledge into project actions is difficult to be acknowledged and quantified. This issue is also made evident when we assess the number of design actions attributed to the discipline. Among over three thousand actions in the general schedule for the basic design phase, ergonomics was effectively responsible for six items. Even though this number might seem small when compared to the whole, these attributions represent a step forward when we consider the participation of ergonomics in this type of project. Furthermore, the number of 6 seems small as it does not consider all the development steps necessary to complete them.
It is worth mentioning that, in addition to the fact that the recognition of the ergonomics team’s work is related to deliverables, social construction was a resource which brought visibility to ergonomic actions [13]. Space given for discussions intended to develop technical specifications ensured the alignment and validation of information and solutions between different teams.
Regarding the resources for storing and sharing design documents, throughout the project, the researchers understood that the company’s system was designed to be a database and not a communication tool. The main communication and updating resources between disciplines was excel spreadsheets shared in the company’s internal network, whose information was updated daily by the disciplines. These spreadsheets were not official project controls, but rather informal resources adopted by the teams. However, the official system interface was not considered suitable for this purpose, as each inserted update required new approvals, entailing additional tasks for the other teams.
As for the Design Review, the initial idea was that the sessions would provide an environment conducive to work-related discussions, with the use of the 3D model as an intermediary object [23, 24], in addition to the participation of designers and specialists. Although future users did not participate in the sessions, some designers had already worked in similar situations. In addition, the ergonomists saw the opportunity to bring the dimension of real work to the project, through the discussion of data collected in the reference situations.
However, the Design Review sessions did not end up being favorable opportunities for carrying out those discussions, since such events had their own objectives and dynamics, which must be respected and did not have a time frame for activities beyond their initial scope. Despite this, within the context of Design Reviews, it was possible to propose a few reflections on the work to be developed in the future situation, through discussions generated by the verification of the CL items.
One of the main limitations of the research is related to the fact that ergonomists were both observers and observed in the study. Nonetheless, this bias was mitigated because the team was made up of three ergonomists-researchers who mutually validated design records [25].
In addition, constraints on accessing the project development site in the first months, the difficulty in scheduling visits to reference situations (which depended on the availability of places on the platforms for researchers) and the few opportunities for discussion with the workers of the future platform throughout the design process also represented limitations to the research.
It should also be noted that this is a qualitative research in ergonomics, and one of the premises of activity’s ergonomics is that each intervention is unique. Therefore, during participation in the project, particular interpretations were produced aiming at solving the problems addressed to the ergonomists. However, based on the data collection and after a reflective analysis of the intervention, research in ergonomics can build generalizable interpretations, which contribute mainly to the discussion with other members of the professional community [25, 26].
For future studies, we suggest the continuation of this theme, in order to seek ways to better translate the participation of ergonomics in evidence in an engineering project. Recent studies assess the contribution of the use of ergonomic tools and methods to increase the ability to incorporate user requirements into the project, in addition to helping ergonomists in communicating with other stakeholders in the process [22]. The use of such tools and methods in an oil platform design could represent a possibility to improve interactions between ergonomics and engineering in the design process. Another possibility would be to monitor corresponding studies in another design stage, such as the conceptual or detailed design phases.
5Conclusion
Ergonomists’ approaches and strategies depend on the context in which they are called to act upon. Dissimilar to a diagnostic situation, in a design process, the ergonomist has less autonomy and must find his place among other design disciplines. In the design process situation presented, although receptivity was perceived by all teams, it is noticeable that Ergonomics still does not have a clearly understood scope of action.
Finally, some difficulties were also identified in the work of the ergonomics discipline in this project, such as the fact that the ergonomics discipline was composed of only one professional from the company dedicated exclusively to the project. Other professionals from other areas (not all ergonomists) provided support, but did not have ergonomics as their main focus of work.
In addition, the intersection of the scope of ergonomic technical specifications with that of other disciplines was also an obstacle, and it was necessary to establish the limits of performance of each discipline.
The results obtained from this study lead to a hypothesis that ergonomics can play a fundamental role in the integration of different design specialties, since its object of study - the work itself - permeates the scope of most of the design disciplines. However, ergonomics still “seeks” more than it “is sought”, that is, it is more likely for ergonomics teams to reach out to other disciplines to align content and, somehow, offer their contribution.
This study provided a reflection on how the participation of ergonomics in projects takes place, taking into consideration the company’s initial perspective on similar projects.
Ethical approval
Not applicable.
Informed consent
Not applicable.
Conflict of interest
None to report.
Funding
This study was financed in part by the Coordenação de Aperfeiçoamento de Pessoal de Nível Superior – Brasil (CAPES) – Finance Code 001, and by the Conselho Nacional de Desenvolvimento Científico e Tecnológico (CNPq), both entities linked to the Ministry of Science, Technology and Innovation that foster research in Brazil.
This study has also benefited from resources provided by CAPES/PRINT 41/2017 public notice, throughout the research project “Management and Innovation for Sustainability”.
References
[1] | Duarte F . Complementaridade entre ergonomia e engenharia em projetos industriais. In: DuarteF, editor. Ergonomia e Projeto na Indústria de Processo Contínuo. Rio de Janeiro: Lucerna; (2002) , pp. 11–21. |
[2] | Cordeiro CVC , Oggioni B , Duarte F , Lima FPA . From the ergonomic guidelines to the configuration of use in the offshore platforms design context. Production [Internet]. 2015[cited 2021 Dec 23];25: (2):298–309. Available from: https://www.scielo.br/j/prod/a/vwPMfxfwzRmDjgBkmpKgh7y/?format=html&lang=en DOI: 10.1590/0103-6513.149913 |
[3] | Duarte F , Lima FPA . Anticiper L’activité par les configurations d’usage: Proposition méthodologique pour conduite de projet. Activités. (2012) ;9: (2):22–47. DOI: 10.4000/activites.314 |
[4] | Conceição CS , Broberg O , Duarte F . A six-step model to transform an ergonomic work analysis into design guidelines for engineering projects. Work. (2020) ;66: (3):699–710. DOI: 10.3233/WOR-203212 |
[5] | Lima FPA , Duarte F . Integrando a ergonomia ao projeto de engenharia: Especificações ergonômicas e configurações de uso. Gestão & Produção. (2014) ;21: (4):679–90. |
[6] | Bittencourt JM , Duarte F , Béguin P . From the past to the future: Integrating work experience into the design process. Work. (2017) ;57: (3):379–87. DOI: 10.3233/WOR-172567 |
[7] | Conceição CS , Silva G , Broberg O , Duarte F . Intermediary objects in the workspace design process: Means of experience transfer in the offshore sector. Work. (2012) ;41: :127–35. DOI: 10.3233/WOR-2012-0146-127 |
[8] | Oggioni B , Duarte F , Cordeiro CVC . Ergonomics in projects of oil platforms in a change context. Work. (2012) ;41: (1):107–13. DOI: 10.3233/WOR-2012-0143-107 |
[9] | Guérin F , Laville A , Daniellou F , Duraffourg J , Kerguelen A . Compreender o trabalho para transformá-lo: A prática da ergonomia. São Paulo: Edgard Blücher; (2002) , p. 224. |
[10] | Béguin P . Prendre en compte l’activité de travail pour concevoir. Activités. (2007) ;4: (2):107–14. DOI: 10.4000/activites.1719 |
[11] | Maline J . Simuler le travail. Une aide à la conduite de projet Lyon-Montrouge (FR): ANACT; (1994) . |
[12] | Daniellou F . L’ergonomie dans la conduite de projets de conception de systèmes de travail. In: FalzonP, editor. Ergonomie. Paris: Presses Universitaires de France; (2004) , pp. 359–73. |
[13] | Daniellou F . The French-speaking ergonomists’ approach to work activity: Cross-influences of field intervention and conceptual models. Theoretical Issues in Ergonomics Science. (2005) ;6: (5):409–27. DOI: 10.1080/14639220500078252 |
[14] | Daniellou F , Laville A , Teiger C . Ficção e realidade no trabalho operário. Revista Brasileira de Saúde Ocupacional. (1989) ;17: (68):7–13. |
[15] | Marins CP , Leite PBC , Mercado MP , Garotti L , Duarte F . Constructing the Place of Ergonomics as a Design Discipline: The Case of the Basic Design of Basic Design of Oil Platforms. In: BlackNL, NeumannWP, NoyI, editors. Proceedings of the 21st Congress of the International Ergonomics Association (IEA 2021). Volume I: Systems and Macroergonomics. Cham (CH): Springer International Publishing. (2021) , pp. 196–200. DOI: 10.1007/978-3-030-74602-5_30 |
[16] | Mercado MP , Leite PBC , Marins CP , Tinoco F , Duarte F . The Practice of Ergonomics in the Creation of Technical Specifications for Offshore Platform Projects. In: BlackNL, NeumannWP, NoyI, editors. Proceedings of the 21st Congress of the International Ergonomics Association (IEA Volume I: Systems and Macroergonomics. Cham (CH): Springer International Publishing. (2021) , pp. 217–22. DOI: 10.1007/978-3-030-74602-5_33 |
[17] | Minayo MCS . Trabalho de campo: Contexto de observação, interação e descoberta. In: MinayoMCS, organizer. Pesquisa social: Teoria, método e criatividade. 34a ed Petrópolis (BR): Vozes; (2015) . |
[18] | Patton MQ . Qualitative research and evaluation methods. 3rd ed. London: Sage Publications; (2002) . |
[19] | Broberg O . Integrating ergonomics into engineering: Empirical evidence and implications for the ergonomists. Human Factors and Ergonomics in Manufacturing. (2007) ;17: (4):353–66. DOI: 10.1002/hfm.20081 |
[20] | Hall-Andersen LB , Neumann P , Broberg O . Integrating ergonomics knowledge into business-driven design projects: The shaping of resource constraints in engineering consultancy. Work. (2016) ;55: (2):335–46. DOI: 10.3233/WOR-162400 |
[21] | Sørensen LB , Broberg O . Integrating ergonomics in design processes: A case study within an engineering consultancy firm. Work. (2012) ;41: :949–55. DOI: 10.3233/WOR-2012-0268-949 |
[22] | Punchihewa HKG , Gyia DE . Reducing work-related Musculoskeletal Disorders (MSDs) through design: Views of ergonomics and design practitioners. Work. (2016) ;56: :127–42. DOI: 10.3233/WOR-152126 |
[23] | Vinck D , Jeantet A . Mediating and Commissioning Objects in the Sociotechnical Process of Product Design: A Conceptual Approach. In: MacleanD, SaviottiP, VinckD, editors. Management and New Technology: Design, Networks and Strategies. Bruxelles: COST Social Science Series; (1995) , pp. 111–29. |
[24] | Jeantet A . Les objets intermédiaires dans la conception. Éléments pour une sociologie dês processus de conception. Sociologie du Travail. (1998) ;40: (3):291–316. DOI: 10.3406/sotra.1998.1333 |
[25] | Jackson M . Entre situations de gestion et situations de délibération. L’action de l’ergonome dans les projets industriels. [thesis] Bordeaux (FR): Collection Thèses et Mémoires Laboratoire d’Ergonomie des systèmes complexes. Université Victor Segalen Bordeaux 2-ISPED éditions; (1998) . |
[26] | Daniellou F . Peut-on être chercheur en ergonomie? In: DaniellouF, editor. Proceedings of the conference Recherche et Ergonomie. Toulouse (FR), (1998) , pp. 216–24. |