Structuring the simulation for participation during design: Designing integrated operations centers in the oil industry – A case study1
Abstract
BACKGROUND:
The need for participative approaches in design is a key concern for Ergonomics. There exists a vast array of philosophies and techniques which may come under the heading of participation, but several of these methods are indeed not really participatory in the real sense of the concept.
OBJECTIVE:
The aim of this study is to reveal the elements that allow an ergonomic simulation approach to be applied as a design process method centered on the work perspective and anchored on the participation concept.
METHODS:
This study is centered on the subsequent analysis of a case study: the design of an Onshore Collaborative Center (OCC), in the context of Integrated Operations (IO) of the oil industry. The simulation sessions were filmed and recorded, and a logbook of the progress of the design process was produced daily in order to preserve the memory of the case.
RESULTS:
The main result of the research highlights that simulation is a method capable of presenting work as an important factor in the transformation of the project, as well as in technical choices, in addition to opening space for different participants and their various perspectives. However, for it to be an effective method of participation, there is the need for a “back and forth” process between work analysis and simulation during the ergonomic simulation approach.
CONCLUSION:
This study showed which elements support the construction of ergonomic simulation as a method capable of structuring the participation in design process. For this, the simulation must be based on work analysis and articulate the knowledge of different actors for decision-making to allow for new developments while promoting the vision of work as an important decision variable in the design process.
1Introduction
The need for participative approaches is a key concern for Ergonomics, especially related to workplace health and safety, seeking more effective, well-thought-out, and widely acceptable design solutions [1]. Participatory approaches in ergonomics have been broadly discussed [2–5]. The methods could be consultative in nature, with the opinion being requested from the operators by designers or by the ergonomists themselves [5, 6].
However, as Wilson [2] highlights, there exists a vast array of approaches, philosophies and techniques which may come under the heading of participation, but several of these methods are indeed not really participatory in the real sense of the concept. We share Wilson’s consideration when he argues that, rather than involving training, meetings, and consulting, “participation is seen as providing the opportunity for real, early, and full involvement of the people involved (operators, supervisors, etc.) in the decision-making about their jobs, systems, workplace, and organization” [2].
In participatory design domain, design processes demand approaches that allow the participation of different actors in structuring the conditions for carrying out the work in the future situation. As examples, several ergonomics studies have shown the importance of involving workers (final users) in the participatory design process [7–9].
Our main hypothesis is that, during design processes, simulation is a method that can be mobilized to discuss future work through the full involvement of the people involved, taking into account the concept of participation mobilized by Wilson [2].
According to Daniellou [10], simulation methods can be classified by distinguishing: (i) methods where the workers are not present but modeled (by means of a manikin or a computer program, etc.); (ii) methods where workers, individuals, or collectively, are requested to take part in a controlled experiment and their behavior is analyzed; and (iii) methods where the users take part in a participatory ergonomic process.
In this last approach, simulation may be understood as one of the components of a more global involvement of different actors (workers, managers, designers, and other stakeholders), and as a method that puts the dialogs between workers, designers and other participants at the center of the design process [10–15].
This type of work simulation method, which we will call “ergonomic simulation” in this article, is essentially participatory and questions the way in which simulations are understood, and their role during the design process. It also questions how the actors of the design project should be structured, and the elements that need to be promoted in order to identify knowledge about work in a future setting and, consequently, decision-making during the design process.
Thus, the aim of this study is to reveal the elements that allow an ergonomic simulation approach to be applied as a design process method centered on the work perspective and anchored on the participation concept.
To achieve this objective, this study is based on the subsequent analysis and reflection on the practical case of the project of an Onshore Collaborative Center (OCC) within the oil industry, which aimed to use ergonomic simulation in the design process of the future installation, in order to promote dialogue between workers (end users), managers and designers around future work.
This article is organized as follows: section 2 describes our understanding of the design process and to what extent the ergonomic simulation can support participatory processes; section 3 presents the context of the case study; section 4 describes the methods used to analyze the research data; section 5 provides the main results from the case study analysis; section 6 discusses the achieved results; and section 7 draws the relevant conclusions.
2Theoretical framework: Participation and simulation within the design process
2.1Design process characteristics
A design process can be characterized as a finalized process, replete with uncertainties, moving back and forth as regards choices and decision-making, with restricted temporal dimensions that involve a wide range of interdependent actors [16].
Béguin [17] proposes a model that characterizes the path of the project as a process of tension between two places, which must converge for its achievement and finalization. On one hand is the plane that refers to the construction of the problem to be treated, that desired and/or its representation, while on the other is the plane that refers to the possible, to the concrete resolution of a problem, to the action, and to the work.
The metaphor of a “conversation with the situation,” proposed by Donald Schön [18], can exemplify the planes of the desired and of the possible. According to this author, the design process can be described as an open-ended heuristic moment during which the designer, striving to reach a goal, projects ideas and knowledge. However, the situation then “replies” and “surprises” the designer by presenting unexpected resistances, which serve as a learning basis for the designer.
It is clear that the “reflexive conversation with the situation” takes place in a “dialog” with what is being specified: what seems initially desired appears as more or less possible. But within such a process, the other actors “reply” and “surprise” as well [19]. In that case, the designer, striving to reach a goal, projects ideas and knowledge that will be validated, refuted, or set in motion based on actions and learning performed by another actor involved in the design process.
Such a process can be understood as a “dialogical process of mutual learning” mediated by intermediary production [20]. It is a mutual learning process where what appears as being desirable by some is possible or impossible to others. These dialogs are mediated by “intermediary production” in the sense that an intermediary object (a plan, a diagram, a prototype, etc.) [21] supports and guides the dialogs between the actors of the design process. The proposal of this design model is to enable this dialog within the project process so that the learning achieved during the project helps to guide design decisions [14].
2.2Participation in the design process
Such a dialogical process is of great value, since the design is a collective working process, where the coordination between different perspectives, experiences, and interests must be supported. No individual participants of the design process have any representation of all issues nor the skills to solve them entirely [22]. This complexity means that problem-solving requires several skills that must be coordinated [23].
Darses and Reuzeau [24] emphasize, however, that participation cannot be reduced to a design technique: the organizational and social components must be explicitly taken into account and must lead to the development of operating rules that secure people’s involvement in the process. Thus, the way in which players are mobilized in performing the project reveals, or not, the presence of a participatory process.
In a participatory design process, workers officially endorse the role of co-designers, as their contributions are recognized and validated by the company as influencing factors in design choices [24].
From an ergonomics point of view, a participatory approach to workplace assessment and design will seek to modify the representations of work that are involved in the design and not simply bring new bricks of knowledge to the designers [6]. According to the authors, introducing a participatory approach in the design process requires a social construction for clear negotiation between the parties, as well as a technical construction consisting of the definition of methods that enable a confrontation between different types of knowledge.
2.3Ergonomic simulation as part of the participatory design process
Ergonomic Simulation appears to be a promising and key method to answer the question of the worker’s place in the design process, which involves dealing with unpredicted variability, mobilizing staff and collective resources, experiencing contradictions, and conducting debates on the values among the participants [25].
The goal of ergonomic simulation is not to prescribe the correct way to perform tasks [10]: it is impossible to fully anticipate the future, for the activity is constructed by a given worker as a response to a given context [25]. However, ergonomic simulation brings about the possibility to act out and manipulate certain elements that are considered significant in order to achieve a goal and to discard other less interesting objectives [26].
Different frameworks for ergonomic simulation lead to progress regarding how to structure one’s participation in the project, bringing the point of view of work [11–13], but still lacking depth referent to the development of real work in the future environment, which includes the knowledge of variabilities, strategies, and logics that are revealed by the work activity analysis.
Activity-centered ergonomics has proposed the ergonomic simulation framework [27, 28] by structuring the design to include the perspective of work through activity analysis and simulations. The concept of activity is the mobilization of individuals, in all their physical, cognitive, and subjective functions, to carry out tasks, which is the key to activity-centered ergonomics in the individuals’ approach to work and how to change it [29].
This ergonomic approach to design is typically based on an analysis of the project; on an analysis of the work activities (with existing situations or other reference situations); on the establishment of a structured, participatory, and collaborative approach; on the execution of work simulations that enable the design of the probable future activity; on the formalization of the results of the simulations for the design actors (workers, designers, decision-makers, etc., carried out by ergonomists in collaboration with these participants); and on the follow-up of the project until the startup of operations [28].
Based on this framework, Bittencourt et al. [14], considering ergonomic simulations made with LEGO during the design of a new laboratory complex for biotechnology research, made progress in the development of a simulation as a participatory method insofar as it emphasizes that a simulation allows one to formulate project solutions in parallel with a collective construction of the future work through the mobilization of past work experience.
Thus, a simulation is a method that can be used to contribute to a “dialogic learning process” between users and designers [20], where a novelty designed by the designers may lead to learning on the part of workers during simulation. However, the worker can validate or invalidate the hypotheses produced by the designer and create new solutions. There is, therefore, a mutual learning process mobilized by participatory simulations that should be supported and supervised by the ergonomist. The knowledge of future work will serve to question and redirect objectives and technical project solutions. This dynamic involves a mutual rearrangement between developed solutions and objectives that will be transformed during the project [14].
3Context of the case study: Integrated Operations (IO)
The context of Integrated Operations (IO) in the oil industry has led to requirements for low offshore staffing and a high degree of sensor-based monitoring, combined with support and management from collaborative environments [30], which has the role of increasing integration between teams.
Thus, the collaborative environments or Onshore Collaborative Centers (OCC) aim to make operations and maintenance work more feasible between the onshore-based operation unit and the offshore operations, with the objective of expanding cooperation and real-time team integration [31–33].
In the Brazilian context, there is an unstated expectation that the integration of different teams on land will occur, based on the occupation of the same workplace [34]. Nevertheless, according to Moltu [35], neither room nor technology determinism is sufficient to comprehend the successful development of IO. Moltu [35] highlights that work processes and ways of working in an IO context are what underlie and constitute the characteristics and need for a collaborative environment and, despite stressing that final users (workers) need to participate in the IO design process, the way in which t0his participation can be accomplished is unclear.
Cordeiro et al. [34] and Maia et al. [36], based on a participatory ergonomic intervention in the design of a subsea OCC, demonstrated that these workplace designs require the understanding and reflection of how future teams can work, cooperate, and coordinate their actions, because what is at stake is the design of a new work system.
4Materials and methods
The research question was investigated using a case study of the offshore oil company, where an ergonomics team organized an Ergonomic Simulation Approach [27, 28] in the project of a new Onshore Collaborative Center. According to Yin [37], the case study method investigates a contemporary phenomenon within its real-life context, especially when the boundaries between phenomenon and context are not clearly evident.
This method was adequate since we wanted to investigate which elements of an ergonomic simulation should be considered to allow participation in factual projects. The subsequent data analysis of the case study sought to understand how Ergonomic Simulations can be structured to contribute as a participatory method in the design process, such as in collaborative environments of IO projects.
4.1Case setting
The study case was conducted in one of the oil production units of the oil company under study, which operates in the exploration of the pre-salt area. With the expansion of the pre-salt operation and the delivery of new platforms in 2021, the production unit began the OCC restructuring project so as to expand its capacity to support offshore operations.
The design of the new OCC would move its operating location, currently in separate rooms, to one large center located in a vacant restaurant facility in the same building. The goal was that the new OCC would accommodate increased staffing and allow for enhanced interactions between teams, thus making the integrated support character more effective.
The ergonomic simulation approach carried out in the OCC was divided into three stages: (i) the work study; (ii) the environment study and layout proposals, and (iii) three simulations cycles. These stages were not sequential and had overlapping activity points.
(i) The work study
The first stage sought to understand the work in a comprehensive manner, its main attributions, as well as the main interactions between the teams, both inside and outside the OCC. The objective was to build the integration hypotheses among the OCC teams, represented by an integration scheme among the teams, which would guide the construction and simulation of the layout proposals. This scheme represents the intensity of work interactions between the teams and was built from the diagnosis of the Ergonomic Work Analysis [38] with the OCC teams.
The ergonomics team, based on the validation of integration hypotheses conducted with managers and workers, created the first layout proposals (detailed in the next item). Parallel to the first discussions around the layout, the ergonomics team returned to the field to deepen the Ergonomic Work Analysis and create the scenario with elements of typical work situations for the simulation stages.
(ii) The study of spaces and layout proposals.
The second stage concentrated on mapping the available spaces and understanding their physical characteristics. With the data from the work study, the first layout proposals were designed for the simulations in the third stage of the project.
(iii) The simulations stage.
This phase was organized in three cycles. The first began discussions with teams and managers about two layout alternatives generated by the ergonomics team based on the work study. The main objective was to select one of the two proposals for discussion in the next simulation sections. The resources included schematic paper plans and pens for interventions by workers and managers.
The second step was carried out on site, which would be modified to accommodate the new OCC. The objective was to discuss the typical work situations and the proposed space organization for layout development. The resource included the “game board,” which is a rigid board with a schematic plan printed on vinyl for writing and erasing, with pieces representing the workstations, which could be moved around. The board was used as a support for the discussion about the organization of the spaces.
As a result of the second cycle of simulation meetings, an ergonomics team reproduced the layout associated with a three-dimensional (3D) package for use in the third cycle of simulation meetings, which were held 20 days later. The objective was to discuss the typical work situations and the proposed space organization for layout detailing. As occurred in the second step, the meeting was held in the room to be modified and the game board, the printed plans, and the 3D mockup images were used as supports. A summary of the organization of the simulation, based on Andersen and Broberg [13], is shown in Table 1.
Table 1
Organization of the simulation steps (based on Andersen and Broberg [13])
First cycle of simulations | Second cycle of simulations | Third cycle of simulations | ||
1st meeting | 2nd meeting | |||
Duration | 10 to 20 min/participant or group for 2 weeks | 1h20/group – 2h40 min total | 1 h/group – 2 h total | 1h20/group – 2h40 min total |
Simulation support | Paper schematic floor plan | Game board and paper floor plan | Game board and paper floor plan | Game board, projected image of 3D mockup and paper floor plan |
Teams/participants | - 10 operators of process plant monitoring - 3 operators of large machine monitoring - 2 operators of safety equipment monitoring - 1 monitoring team manager - 4 operators of integrated logistics - 1 manager of integrated logistics - 11 operators and the manager of operational support - 4 operators and the manager of gas extraction mesh - 6 operators of infrastructure support - 1 manager of infrastructure support - 4 engineers of IO Management team | Group 1: - 1 operator of process plant monitoring - 1 operator of large machine monitoring - 2 operators of safety equipment monitoring - 1 monitoring team manager - 1 operator of infrastructure support - 2 engineers of IO Management Group 2: - 1 manager of integrated logistics - 3 operators and the manager of operational support - 1 manager of operational support - 4 operators and the manager of gas extraction mesh - 2 engineers of IO Management | Group 1: - 1 operator of process plant monitoring Group 2: - 1 operator of large machine monitoring | Group 1: - 1 operator of process plant monitoring - 1 operator of large machine monitoring - 2 operators of safety equipment monitoring - 1 monitoring team manager - 1 operator of infrastructure support - 2 engineers of IO Management Group 2: - 1 manager of integrated logistics - 3 operators and the manager of operational support - 1 manager of operational support - 4 operators and the manager of gas extraction mesh - 2 engineers of IO Management |
Purpose | Present and discuss the ergonomic project to select one of the layout alternatives | Discuss the typical situations and the proposed space organization for layout development | Discuss the typical situations and the proposed space organization for layout development | Discuss the typical situations and the proposed space organization for layout development and detailing |
During the simulations, the ergonomists presented the developed project and asked questions about the room and the work activity to be performed therein. The questions were based on typical work situations, structured in the drill-down stage of study of the teams’ work. The main role of the team of ergonomists was to mediate the meetings, and their main goal was to encourage the participants to think about their own work and to present their proposals for the organization of the room.
The mediation by the ergonomists had to be adapted to different situations during the simulations upon each new layout proposal put forward by the participants. Information concerning work situations were again “put into the game” for discussions, such as the suggestions for thinking about the work without the influence of technical devices and about how emergency situations would be conducted.
4.2Participants
The participants in the study were workers and managers of the existing OCC teams, namely: three predictive monitoring teams for offshore platform equipment and systems; one logistics support team; one operational support team, which controls the gas network and provides emergency support for offshore operations; one support team for planning and optimization of the gas pipeline network; one infrastructure support team for the OCC itself; and the IO management team, the project’s requestingparty.
4.3Procedures for data collection and analysis
This research is based upon the afterthought from the construction of the OCC project’s log, whereby all intervention traces, such as reports, field notes, work analyses, meeting notes, and audio and video recordings of the simulations were systematically stored during the intervention and organized chronologically. Moreover, the project’s log was validated by another ergonomist in the project.
The records of the meetings in the first simulation cycle included the ground plans drawn by the workers and notes taken in the ergonomists’ field notebooks. The data were gathered and analyzed with the intention of developing the layout selected by the teams for the ensuing simulations.
The second and third simulation cycles were videos, recorded using cameras, and audios, recorded using two recorders placed near the participants. At every change in the organization promoted by the workers, the ergonomists also took pictures of the game board. In the last two stages of simulations, the ergonomics team was made up of four researchers, split in pairs during the simultaneous meetings.
Audio and video records were transcribed to identify layout changes and discussions during the modifications proposed by the workers and managers in the second and third simulations. From a qualitative viewpoint, the objective was to identify, along with the analysis of layout evolution, to what extent the ergonomic simulation highlights the perspective of work for decision-making during projectdevelopment.
5Results
The results of the ergonomic simulation approach to the OCC design process are presented in this section and are divided into three parts. First, the place where the work analysis was conducted in this process, leading to the generation of the first layout alternatives and the mapping of the work situations used in the simulations is discussed. Next, the thoughts on the development of the layout in the different stages of the simulations are presented, which are contextualized by the analysis of the discussions amongst the participants. Here, the example of monitoring teams is used to illustrate this development. Finally, the characteristics of the ergonomic simulation approach structured by the ergonomics team in the OCC design process are presented.
5.1The role of work analysis
First, through Work Analysis, it is possible to characterize the existing integration between the OCC teams. The creation of a scheme of interactions (Fig. 1) allowed one to view the relations and communication intensity within the team and with other teams.
Fig. 1
Scheme of the integration relationships among OCC teams.
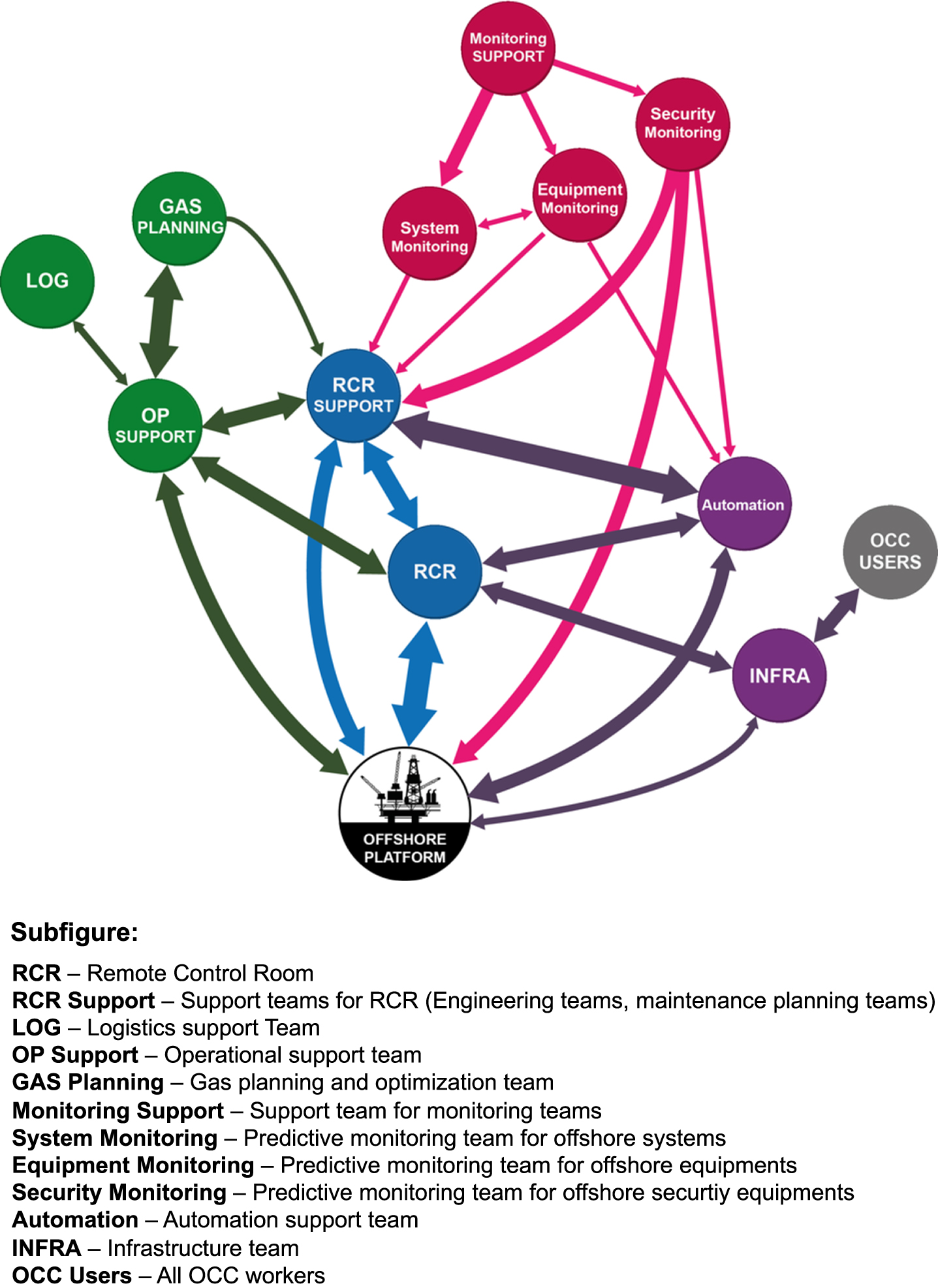
The data from the different frequencies of interaction among the teams (e.g., the greater the interaction among the teams, the thicker the arrow in the figure’s schematics) guided the grouping and the required proximity among the teams in designing the space. The nature of the integrated work guided the discussions with the project managers to validate the integration scheme. Based on the analyzed work and the identified integration groups, the ergonomics team started the first layout studies for the OCC.
Subsequently, with an understanding of the team’s functioning, data analysis strategies, and integration with other teams through further work analysis, the ergonomics team compiled the typical team situations for scenario building at the final simulation meetings, thus adding to reflections on future work and the design of the intended environment with elements of the actual work.
5.2The role of simulations
The three simulation cycles show how innovative proposals were created at each stage. The first simulation cycle in the monitoring team brought a new element into the discussion. In the proposed layout, it was not possible to hold quick meetings with team members. In the current team layout, these meetings were held in the corridor between workstations (Fig. 2). This work situation was further explored in the work analyses that were being conducted in parallel, to be discussed in the following simulations.
Fig. 2
Location where the monitoring team meetings were held.
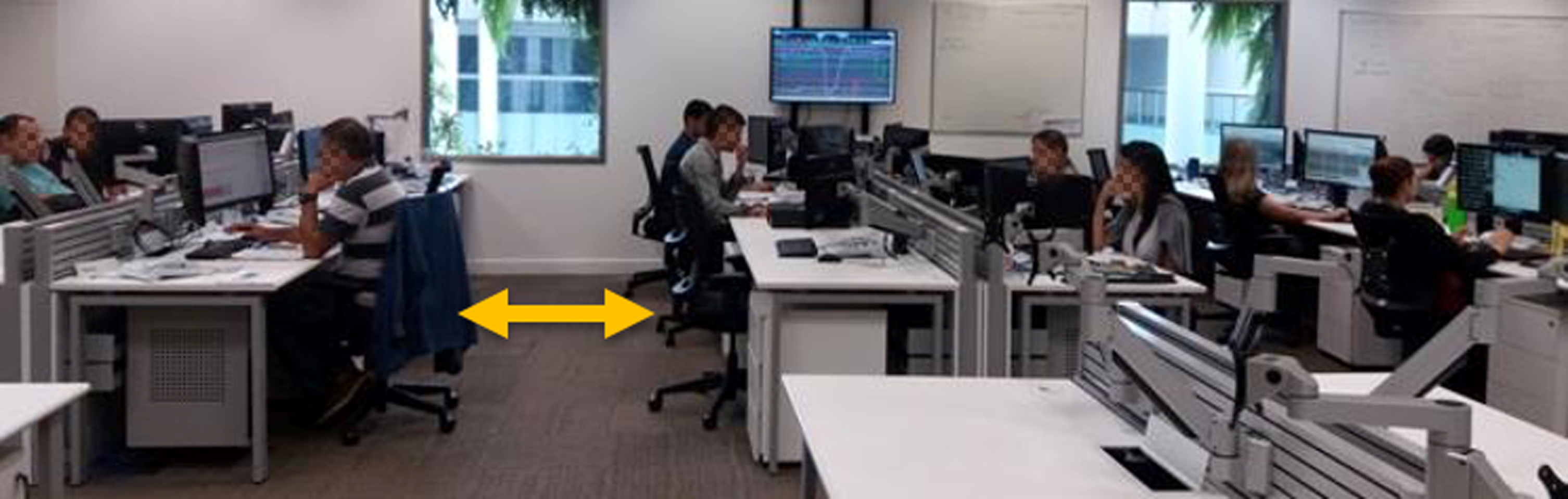
For the second and third simulation cycles, the use of a game board and a virtual mockup enabled a reflection on the layout of the workstations, as it was possible to study new possibilities and modify the layout during discussions about the space in different work situations.
In terms of results, the first simulations served to equalize the knowledge on the project among the participants (OCC operators and managers) and provoked a return to work analyses in order to understand the questionings regarding the development of future work. The second simulation cycle allowed the participants, mainly the operators, to be equipped so as to effectively suggest changes based on the reflection about the work that will be performed in the future space. By contrast, the third cycle allowed these proposed changes to be defended and incorporated within the project.
By taking the case of the predictive monitoring team as an example, the first and second simulation cycles are influenced by technical devices in most of the dynamics. The videowall guided the layout by the monitoring team operators and manager. The occupation is discussed more in terms of a technical layout than in terms of the work, even with the work situations brought into discussion. To stimulate a change in logic, the ergonomists requested that only the work be considered, thus excluding the concern with adapting the layout according to a technical device.
Thus, the monitoring team operators reported how information was exchanged to analyze a possible deviation, how data searches were conducted in different systems, the possibility of grouping two operators around a monitor to discuss cases, and training sessions. These typical work situations occurred mainly in informal meetings in the corridor between workstations.
For the manager, all information searches could be shared by the videowall, which could also indicate offshore production indicators. For operators, understanding a problem of an onboard system requires a search on different systems and a sharing of information with teammates, who may have data from related systems that would help to better understand the situation.
In the third simulation cycle, the monitoring team operators proposed a new layout, which was discussed among the three monitoring teams: “(...) The videowall is impacting what the [monitoring] team is most important for today: interaction!” This discussion among the operators occurred temporally between the two simulation cycles and without the presence of the ergonomics team.
The operators’ proposal was to arrange the workplaces in half circles so that they could hold meetings in the center of the workstations and still watch the videowall as needed. This way, from the operators’ viewpoint, they would be able to meet the needs of the integrated team work and the requirements to concentrate information on large screens provided by the management and the IO team. Figure 3 shows the results of layout development in the second and third simulation cycles.
Fig. 3
Layout results developed with the participation of operators in the second and third simulation cycles.
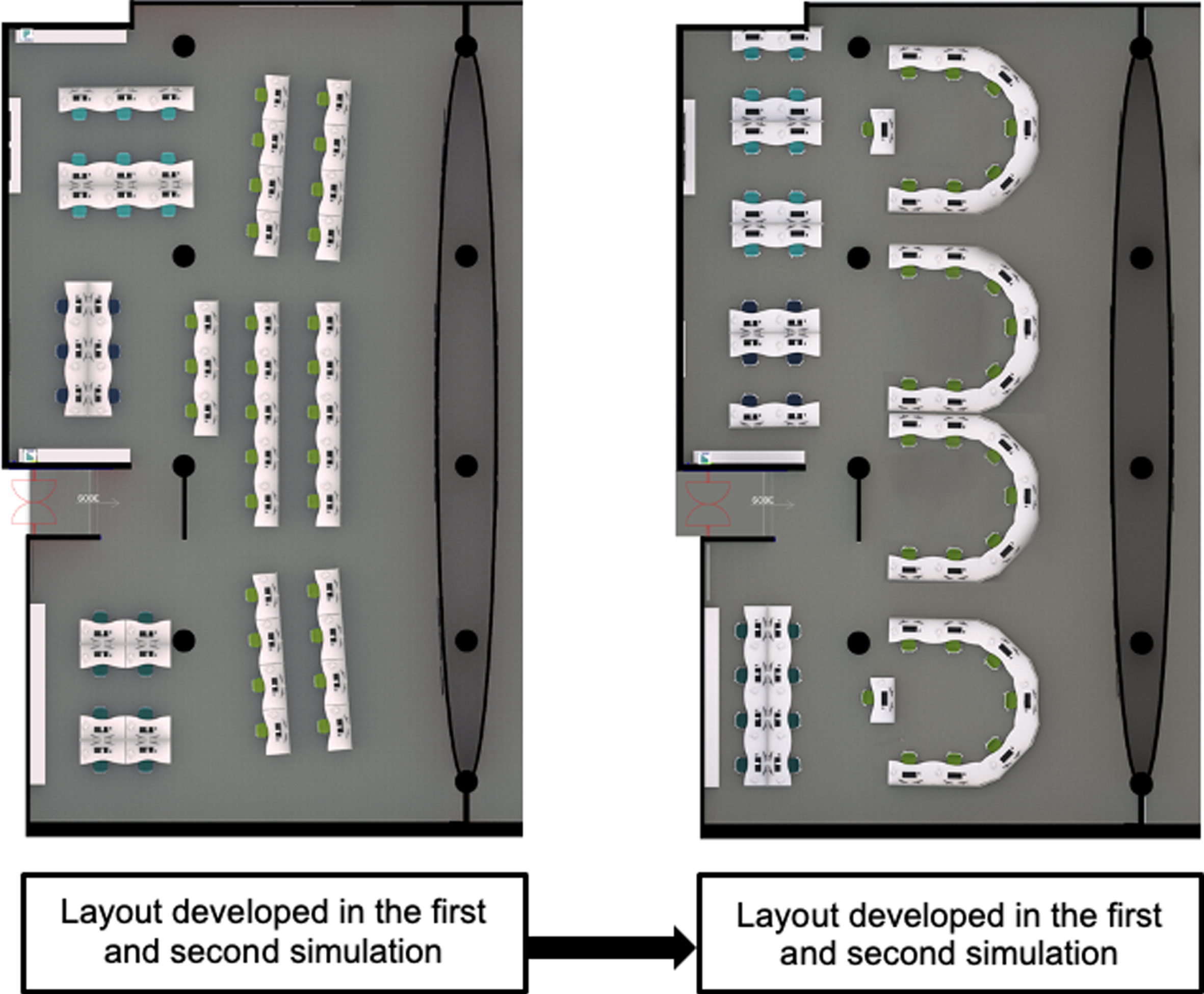
5.3The ergonomic simulation approach in OCC design process
The ergonomics team was formulated in the early stages of the OCC project, where the level of uncertainty and doubt regarding the project is high. Thus, the ergonomic intervention steps sought to promote discussions on the work early in the project. The objective was for the work to be able to guide the project decisions in the stage in which the possibilities of change are higher.
Consequently, the project was structured in a non-linear manner. Many “moves back and forth” between the work analysis and the simulations were necessary. Two dynamics were identified. The first is related to the specification of the spaces: the relationship between the work and simulation allowed for a reduction in uncertainty as regards the technical objects to be designed. More specifically, the questions that arose during the first cycle of simulations served as incentives to return to the work analysis to solve them, as in the example of analyzing and sharing information among monitoring team operators through informal meetings in the corridor between workstations.
The second dynamic refers to the construction of the participative process to bring the work point of view to the OCC project. If initially the teams only mentioned the technical aspects, the references relative to the work mobilized by the operators during the simulations takes on an ever-increasingly important role. In this process, the ergonomist is not neutral and contributes to the creation of a space for dialog focused on work.
6Discussion
Understanding simulation as an individual and collective resource among heterogeneous actors engaged in developing their knowledge and experience into designing something provides the opportunity to develop simulation as a method for a participatory ergonomics process [25]. For this, it is necessary that a simulation is structured from some basic components. Based on OCC case, three points can be highlighted.
The first refers to structuring a simulation as a participatory approach in an ergonomic intervention for design. The results show that simulation is a method capable of presenting work as an important factor in the transformation of the project as well as in technical choices, in addition to opening space for different participants and their various perspectives. However, for it to be an effective method of participation, coordination with work and project analysis is necessary.
According to Maline [27] and Barcellini et al. [28], the participatory approach is based on: (1) the analysis of the project and the work activities; (2) work simulations; and (3) the formalization of simulation results and on-project follow-up.
The approach conducted in the OCC project also uses these steps, but it is possible to observe two processes that were conducted by means of simulation: a process of reducing uncertainty and a process of dialog and learning from the point of view of the future work, as shown in the structure in Fig. 4.
Fig. 4
Structure of the participatory ergonomic approach.
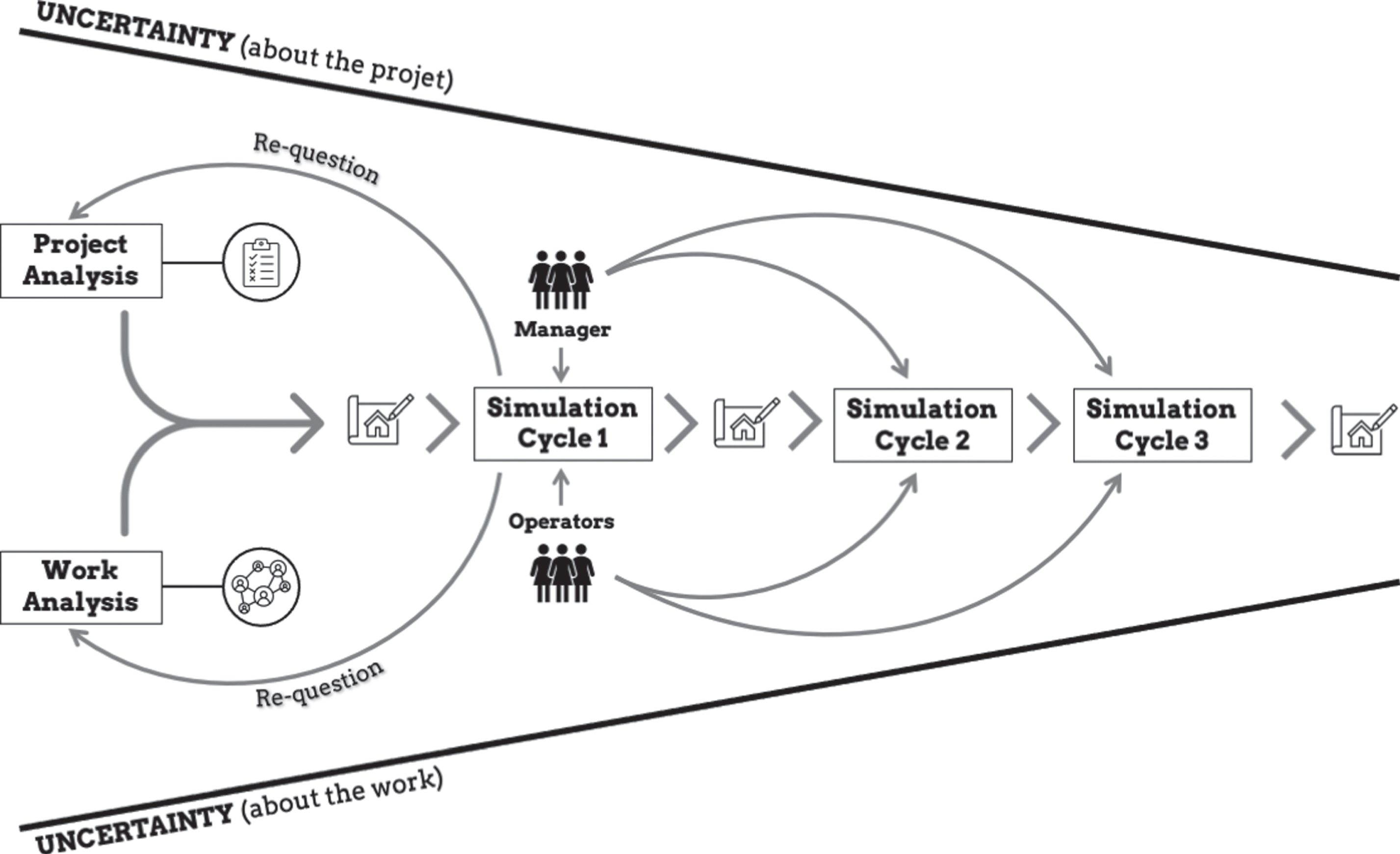
The simulations contribute to reducing uncertainty in the design process in the early stages, as the process brings, in each stage, more elements to understand in the design, such as (i) the technical aspects, insofar as it can anticipate data (on the characteristics and limits of architectural change, for example) and teams (future team of engineers responsible for carrying out the construction, for example), which would only be available later in the project; and (ii) the aspects of work, as it develops future activity situations with the simulations, as well as reflections on the future organization of work (as shown in the example of monitoring teams).
However, since the stages were concomitant, questions that arose with the first simulations could be addressed in a more in-depth analysis of the work. Therefore, there was a path in which the stage of simulation re-questioned what is known about the work, causing a “move back and forth” between these stages. The implementation of the method shows that questions arise during the simulation that require the production of knowledge about work and demand a more in-depth analysis of the work.
While the simulation is normally used to make decisions, here it is used for learning, dialoguing with the situation [18]. The situation (that is, the simulation situation) answers, and to understand and interpret this answer, a process to reveal the work and its depth is necessary.
The second point is related to the status of knowing the work in order to create the physical arrangement hypotheses (layout) and enable production the knowledge of the work for simulation. Therefore, work analysis and simulation maintain dialectical ties while the project is performed. Work analysis allows one to produce the knowledge of the work, which guides the choices made during the project. The detailed analysis of the activity promotes debates about work in the simulations to concretely contribute to the transformation of working conditions.
The relevance point for the OCC project was integration. Thus, the creation of the scheme of interactions amongst teams guided the ergonomics team to define the first arrangements and initiate discussions with the different project participants. Likewise, gathering typical work situations allowed for the work to be put on the scene, even when managers insisted on a vision of integration from large screens, such as videowalls.
The third point is clearly related to the previous one. It highlights that without a scenario setting mainly sourced by the elements of the activity, the discussion about the work concerns and matters would not take place. The dialogs between the actors (including the workers) stay mainly centered on technical devices.
As an example put forward by the monitoring team, operators organize small meetings to build a shared context about the state of the platform in their daily work. This was a different view from that of the managers. The different simulation cycles also allowed for reflection on future ways of working and alternative layout adjustments even when the ergonomics team was not present, thus making project workers equipped to actively take part in projectdecisions.
Based on these reflections, the solution found by the monitoring operators, which aimed to meet both the technological demands of managers and the interaction through the meetings among workers, demonstrates how it is possible to deal with the differences among such diversified participants in the same project and create innovative solutions.
7Conclusion
This study showed which elements allow the construction of ergonomic simulation as a method capable of structuring the participatory design process. For this, the simulation must be based on work analysis and articulates the knowledge of different actors for decision-making. Its contribution was to highlight the dialog and the learning between different participants in the joint construction of design solutions.
Regarding the OCC project in the IO context, the real work reveals strategies among workers that are important for the consolidation of integration among teams in the future environment. The IO literature recognizes that the contribution of workers (final users) is important to the OCC design (and to the IO project), but it lacks data on how to structure it. The case of the OCC project provides the elements to structure a simulation approach that allows for these workers to participate and for the work to be considered from the earliest stages of the design of the future environment.
However, based on the simulation steps mobilized in the practical case of the OCC project, this ergonomic simulation approach to design can be generalized beyond the context of the oil industry. Accordingly, we can include some conditions on how to structure an ergonomic simulation, anchored in participation, to allow the consideration of future work:
1. Workers who will have their work affected by the changes proposed by the project must participate as design actors, with the possibility of influencing decisions in the design process;
2. To enable the participation of actors with different knowledge about the activity of design in the simulation, different intermediate objects can produce a better understanding of the project, helping the actors to reflect and propose design solutions;
3. The structuring of the method should allow for interaction between simulation cycles and work analysis, given that, during the simulation, questions arise that need to be further investigated through a return to the work situation.
Therefore, knowledge of the work situation, different simulation cycles and the use of intermediary objects, as elements of a participation-based simulation approach in design process, allow for new developments while promoting the vision of work as an important decision variable in the designprocess.
Ethical approval
Not applicable.
Informed consent
Not applicable.
Conflict of interest
The authors declare that they have no conflict of interest.
Acknowledgments
The authors would like to thank to Leopoldo Américo Miguez de Mello Research & Development Center (Cenpes) – Petrobras and National Agency of Petroleum, Natural Gas and Biofuels (ANP) for their support with the case study of this research. They would also like to thank Luciano do Valle Garotti, PhD, for assistance with this research.
Funding
This study was financed in part by the Coordenação de Aperfeiçoamento de Pessoal de Nível Superior – Brasil (CAPES) – Finance code 001 and Fundação de Amparo à Pesquisa do Estado do Rio de Janeiro (FAPERJ) – Finance code E-26/210.621/2019.
References
[1] | WilsonJR. Solution ownership in participative work redesign: The case of a crane control room. Int J Ind Ergon. (1995) ;15: (5):329–44. |
[2] | WilsonJR. Participation - A framework and a foundation for ergonomics? J Occup Psychol. (1991) ;64: (1):67–80. |
[3] | Hignett S , Wilson JR , Morris W . Finding ergonomic solutions - participatory approaches. Occup Med Maio de. (2005) ;55: (3):200–7. |
[4] | Haines H , Wilson JR , Vink P , Koningsveld E . Validating a framework for participatory ergonomics (the PEF). Ergonomics. (2002) ;45: (4):309–27. |
[5] | Burgess-Limerick R . Participatory ergonomics: Evidence and implementation lessons. Appl Ergon. (2018) ;68: (February):289–93. |
[6] | Garrigou A , Daniellou F , Carballeda G , Ruaud S . Activity analysis in participatory design and analysis of participatory design activity. Int J Ind Ergon. (1995) ;15: (5):311–27. |
[7] | Lipovaya V , Duarte F , Béguin P . The work activity as an interface among different logics: The case of distributing food in a university restaurant. Work. (2019) ;61: (4):647–60. |
[8] | Judon N , Galey L , de Almeida VS-D , Garrigou A . Contributions of participatory ergonomics to the involvement of workers in chemical risk prevention projects. Work. (2019) ;64: (3):651–60. |
[9] | Alonso CM do C , Lima AN , Oggioni BP , Teixeira MR , Oliveira EP , Couto MCV , et al. Contributions of activity ergonomics to the design of an electronic health record to support collaborative mental care of children and youth: Preliminary results. Work. (2020) ;65: (1):187–94. |
[10] | Daniellou F . Simulating future work activity is not only a way of improving workstation design. Activites. (2007) ;4: (2):84–90. |
[11] | Andersen SN , Broberg O . A framework of knowledge creation processes in participatory simulation of hospital work systems. Ergonomics. (2017) ;60: (4):487–503. |
[12] | Broberg O , Conceicao C . A Framework of Participatory Ergonomics Simulation. In Proceedings of the 20th Congress of the International Ergonomics Association (IEA 2018). Springer International Publishing; (2018) , pp. 391–5. |
[13] | Andersen SN , Broberg O . Participatory ergonomics simulation of hospital work systems: The influence of simulation media on simulation outcome. Appl Ergon. (2015) ;51: :331–42. |
[14] | Bittencourt JMJM , Duarte F , Beguin P , Béguin P , Beguin P . From the past to the future: Integrating work experience into the design process. Work. (2017) ;57: (3):379–87. |
[15] | Béguin P . Learning during design through simulation. In 11th International Symposium on Human Factors in Organisational Design and Management & 46th Annual Nordic Ergonomics Society Conference. Copenhagen; (2014) , pp. 867–72. |
[16] | Béguin P . O ergonomista, ator da concepção [The ergonomist, a design actor]. In: FalzonP, Ergonomia. São Paulo: Blucher; (2007) , pp. 317–30. |
[17] | Béguin P . Conduite de projet et fabrication collective du travail: Une approche développementale (HDR) [Project management and collective production of work: A developmental approach]. [Bordeaux, France]: Université Victor Segalen Bordeaux 2; (2010) . |
[18] | Schön D . The Reflective Practitioner – How Professionals Think in Action. 1 ed. New York: Basic Books; (1983) . |
[19] | Granath JÅ . Architechure, Technology and Human Factors. Design in a Socio-Technical Context. [PhD Thesis, Göteborg, Sweden]: Chalmers University of Technology; (1991) . |
[20] | Béguin P . Design as a mutual learning process between users and designers. Interact Comput. (2003) ;15: (5):709–30. |
[21] | Vinck D , Jeantet A . Mediating and comissioning objects in the sociotechnical process of product design: A conceptual approach. In: Management and new technology: Design, networks and strategies Proceedings from COST A3 workshop. Grenoble: COST Social Sciences Serie; (1994) , pp. 111–29. |
[22] | Duarte F , Conceiçao C , Cordeiro C , Lima FDPA . A integração das necessidades de usuários e projetistas como fonte de inovação para o projeto [The integration of the needs of users and designers as a source of innovation for the project]. LaboReal. (2008) ;4: (2):59–71. |
[23] | Darses F , Détienne F , Visser W . A atividade de concepção e sua assistência [The design activity and its assistance]. In: FalzonP, Ergonomia. São Paulo: Editora Blucher; (2007) , pp. 469–84. |
[24] | Darses F , Reuzeau F . Participação dos usuários na concepção dos sistemas e dispositivos de trabalho [User participation in the design of work systems and devices]. In: FalzonP, Ergonomia. São Paulo: Blucher; (2007) , pp. 343–56. |
[25] | Béguin P , Duarte F , Bittencourt JMJ , Pueyo V . Simulating work systems: Anticipation or development of experiences? An activity approach. In: S. B, R. T, S. A, T. A, Y. F, Proceedings of the 20th Congress of the International Ergonomics Association (IEA 2018) Advances in Intelligent Systems and Computing. Cham: SPRINGER; (2018) , pp. 494–502. |
[26] | BéguinP. Une approche opérative de la simulation. Education permanente. (2006) ;166: :59–74. |
[27] | MalineJ. Simuler le travail: Une aide à la conduite de projet [Simulate work: An aid to project management] Montrouge: ANACT; (1994) . |
[28] | Barcellini F , Van Belleghem L , Daniellou F . Design projects as opportunities for the development of activities. In: FalzonP, Constructive Ergonomics. Boca Raton, Florida: CRC PRESS-TAYLOR & FRANCIS GROUP; (2015) , pp. 187–204. |
[29] | Daniellou F . The French-speaking ergonomists’ approach to work activity: Cross-influences of field intervention and conceptual models. Theor Issues Ergon Sci. (2005) ;6: (5):409–27. |
[30] | HaavikTK. Remoteness and sensework in harsh environments. Saf Sci. (2017) ;95: :150–8. |
[31] | Moltu B , Nærheim J . IO design gives high efficiency. SPE Econ Manag. (2010) ;2: (1):774–84. |
[32] | Edwards AR , Roberts S . iValue, An Intelligent Energy Strategy for an Integrated Gas Major. In SPE Intelligent Energy Conference and Exhibition. Society of Petroleum Engineers; (2008) , pp. 25–7. |
[33] | Lima CBDC , Lima GBA , Quelhas OLG , Ferreira RN . Integrated operations: Value and approach in the oil industry. Brazilian J Oper Prod Manag. (2015) ;12: (1):74–87. |
[34] | Cordeiro CVC , Maia NDC , Duarte FJ de CM . The Workplace Role in Integrated Operations: Contributions and Limits of a Collaborative Environment. In: BlackNL, NeumannWP, NoyI, Proceedings of the 21st Congress of the International Ergonomics Association (IEA 2021) Volume I: Systems and Macroergonomics. . SPRINGER; (2021) , pp. 96–105. |
[35] | Moltu . Good IO-Design is More than IO-Rooms. In: RosendahlT, HepsøV, Integrated Operations in the Oil and Gas Industry: Sustainability and Capability Development. 1o ed Hershey, Pa: IGI Global; (2013) . |
[36] | Maia N de C , Duarte FJ de CM , Cordeiro CVC , Castro IS , Oggioni B de MP . Lições aprendidas de um projeto de ambientes colaborativos: O caso do Centro Integrado de Operações Submarinas [Lessons learned from a collaborative environment project: The case of the Integrated Center for Submarine Operations]. In: Rio Oil & Gas Expo and Conference, IBP 1960_16. Rio de Janeiro; 2016. |
[37] | YinRK. Case Study Research - Design and Methods. Thousands Oaks, California: SAGE PUBLICATIONS INC; (2003) . |
[38] | Guérin F , Laville A , Daniellou F , Duraffourg J , Kerguelen A . Compreender o trabalho para transformá-lo: A prática da ergonomia [Understanding work to transform it: The practice of ergonomics]. São Paulo: Blucher; (2001) . |