“Looking for the defect”: The emerging frontiers between the work activity and automation in a cork industrial district
Abstract
BACKGROUND:
The division of labour between workers and machines is the motto for the current debate on the future of work, as the number of tasks that can potentially be automated increases. Despite receiving significant interest, to date, this debate has focused on forecasts that estimate the potential for machine substitution and thus overshadow the activity perspective.
OBJECTIVE:
This study aims to address the frontiers between human operators and automation in a Portuguese industrial district and to understand how the embodied know-how of expert workers is used when they face the requirements of automated machines.
METHODS:
A qualitative approach to ergonomic analysis was employed in two cork companies, including exploratory interviews with managerial staff; work activity observations (combining observations with video recordings); collective interviews with the workers; and collective meetings to validate our results and conclusions.
RESULTS:
The workers revealed operating modes related to sensory aspects to face the cork-related variability and the limits of automated machines. The human-machine configurations call for the experience of the senses, at the material-corporeal level, and for the preservation of reference points of the activity, mostly in the operation of seeing the cork stoppers.
CONCLUSIONS:
The competent act of seeing the cork stoppers, as an operational expertise layer, enriches the theoretical allocation of tasks between workers and machines. Future challenges for activity-centred ergonomics and work psychology fields are identified, drawing attention to the sustainable development of work, i.e., work activities where people may learn from experience and remain healthy within automated work environments.
1Introduction
1.1The new forms of division of labour in the debate on the future of work
The recent technological breakthroughs have widened the possibilities for automating tasks of human operators to the degree that automated work systems possess more functionality than ever. Automation is not only envisaged to change the models of productivity and control processes, but also the nature of work and how workers relate to machines in the face of new human-machine configurations. Such transformations are not an entirely new phenomenon [1, 3–5], but the pace and speed of recent progress of automation are [1].
Confronted with the quickening tempo of technological change and ever-growing possibilities for automation in workplaces, a set of issues has fuelled a debate on the future of human work [2] in the face of growing concerns about the apparent obsolescence of human activity in production [4–7]. Such issues have to do with the consequences for workers and their professional activities that could be generated as a result of new forms of “division of labour”, i.e., the allocation of tasks between operators and automated machines, and the real autonomy of workers within this “division” [7–11]. The frontiers between human work activity and automation [3] are therefore called into question.
Whilst the existing literature tries to avoid the optimistic–pessimistic manicheism of previous technological waves in work [12], several authors pointed out that, up to now, the debate has concentrated on predictions of employment trends using quantitative projections [8, 11, 13]. Thereto, they assess the potential for machine substitution, i.e., the number of jobs that will be lost as a consequence of automation, which fuels the so-called “substitution myth” [14]. Despite being extensively cited in the literature, these prospective analyses must be questioned. First, they miss the sphere of work activity or, at least, they reduce it to a set of prescribed tasks whose automation potential depends primarily on technologies [9]. Second, the resulting interpretations tend to be positioned only at the macro-level of the phenomenon, focusing on speculative scenarios of work, and thus contributing to thickening the purported neutrality of technology.
Here, contributions from ergonomics and work psychology fields should be addressed since the reverberations of technological advances are never neutral [12, 14, 15]. Analysing how automation transforms the work requires paying attention to the “workplace level”, i.e., the specific and descriptive level concerning “the worker in a given situation” [16] to understand the factors that determine the activity (tasks, multiple demands, constraints, production goals, technological tools available, rules, norms and values). This micro-level of analysis has been particularly developed in the epistemological universe of work psychology, whose contributions have been mobilised in the scope of the interdisciplinary action of activity-oriented approaches to ergonomics [10, 16–18, 37]. Such a perspective aims at providing a “finer-grained understanding” of the activity by focusing on the concrete experience in real-life work situations and understanding the operating modes developed by workers.
1.2Reconfiguring the frontiers between workers and automation: A key moment to discuss the operating modes
The purpose of this paper is to present an ongoing study that seeks to explore the emerging frontiers between workers and automated machines [2], based on the activity approach both work psychology and ergonomics share. To do so, the first point of the study deals with the reconfigurations of work occurring in small-sized cork companies that belong to the main “industrial cork district” in the world (located in Portugal). The growing number of automated machines adopted led to the analysis of main changes taking place, exploring what fractions of work have been automated.
The second point of the study deals with the ways workers activate their know-how (as reserves of expertise) to deal with the constraints within new human-machine configurations. This know-how is based on the development of operating modes as a result of workers’ attempts to reduce the constraints in work situations. The operating modes represent “the ways of doing and organising”, which involve different aspects, such as procedures, tricks of the trade, possible alternatives, ways of using workplace equipment, postures, body movements, reformulation of rules or variations in the sequence of actions [18–20]. For managing the variability in work, workers develop regulation strategies, which reflect how their ways of doing are adjusted to attain production and quality goals while protecting health (the preservation of oneself) [18]. Thereby, the operating modes are adapted to both the variability in working conditions and variations in the person’s condition (e.g., the level of fatigue) thanks to these strategies. For this reason, there is not just one way of doing; rather, the variability of operating modes represents what Schwartz [22] called the “reserves of alternatives”, that is, the field of possibilities developed in practice, and which characterises expertise.
Studying and understanding these “ways of doing” acquired and internalised by expert workers is a pivotal issue due to the difficulties in verbalising know-how that is “embodied” [23–25]. This know-how, often described as tacit or non-formal, is “easier done than said” [25], especially when it has become “second nature”, making experience hard to pin down [20, 21]. Schwartz [22] drew attention to the difficulty to articulate in verbal form know-how that is recorded in the body’s intelligence, given the existence of an indeterminate level comprising synergies, circuits and regulations, which are specific to a body in action. Therefore, the formalisation of this know-how, made possible by “the experience of the body and senses” [26], is a considerable challenge [20, 21, 27, 28]. Ouellet and Vézina [20, 27] put forward two main explanations for this difficulty to put into words “what we know, what we do not know we know, or what we know without ever having been able to describe it” [23]: (i) part of the know-how becomes unspeakable as automatic reflexes are consolidated, thus freeing resources for planning and anticipating critical situations; and (ii) lack of opportunities for workers to discuss, share and formalise their know-how.
This challenge is even greater at a time when automation progress, supported by new technological options in robotics and artificial intelligence (AI), holds the promise of divesting all embodied know-how supposedly by increasing non-manual work [11, 21, 29]. Moricot [30], questioning the place of human beings within automated systems, flagged up the new forms of omission of the body brought about by automatisms in the aviation sector, even though the embodied know-how was key for the system performance and reliability. Also, Anichini and Geffroy [31], drawing on interviews with radiologists, unveiled how clinicians used automation tools (e.g., an AI software) in different ways when reading the images, relying on their experiential know-how, mainly stored in their professional vision.
The demands posed by automation technologies require workers to know how to use their bodies and senses. Thereby, the body’s intelligence and how workers do mobilise it within automated work contexts remain as issues that deserve further research attention [21, 29–31].
This study aims to advance knowledge on these questions, principally how experienced workers activate their embodied know-how within the emerging frontiers between work activity and automation in the cork industry. By presenting two work situations, we shed light on how this know-how related to sensory and proprioceptive mechanisms takes into account the strengths and limits of automation. The presented body of knowledge can then support the construction of a framework for making this workers’ know-how visible, as part of a specific territory as well as a useful reference tool for training new workers in the cork sector. In both cases, it is crucial to make human-machine configurations sustainable in the future. Thus, from the empirical basis of this study, we conclude by putting forward some factors that could threaten the sustainability of work activity within automated work contexts.
2Methods
2.1Research setting
This study is part of a larger research project [32, 33] led by a team of work psychologists in the “cork district of Santa Maria da Feira”. That research project is carried out from day one in partnership with the Portuguese employers’ association of the cork sector (Associação Portuguesa da Cortiça - APCOR) and the Portuguese centre for professional training in the cork industry (Centro de Formação Profissional da Indústria da Cortiça - Cincork).
Cork is an important sector in Portugal since it is the only one in which the country assumes leadership worldwide in terms of production, cork processing and exports [34]. Certain idiosyncrasies of the Portuguese cork sector grant it such a starring role. Firstly, following a continuous process of territorial agglomeration throughout the 20th century, Portuguese cork companies are mainly located in the “industrial cork district of Santa Maria da Feira” (hereafter referred to as the “cork district of SMF”) – a county in the north of Portugal where the cork industry is centred. Here, the companies form a “cluster”, in the sense of an “industrial district”. According to Personnel Records of the Portuguese Ministry of Labour and Social Solidarity, the cork sector accounts for 640 companies, and 487 of which are concentrated in the cork district of SMF [34].
Secondly, it stands out by the fact that micro and small companies are predominant. These companies present a high level of specialisation in the manufacture of cork stoppers; indeed, the transformation of cork planks into natural cork stoppers constitutes the main industrial activity of this region.
Thirdly, over the recent decades, the cork district has undergone important technological changes, mainly in terms of the incorporation of automation applications. Despite being considered a “traditional industry” and whose scale is not generally associated with automation and technological innovation [35], there has been a significant technological evolution through the general increase in automation within the cork industrial chain.
In partnership with the APCOR and the Cincork, a research consortium was set up with 10 small-sized companies located in the cork district of SMF. The present article refers to data collected in the first two companies of this consortium. It is actually where our fieldwork in the cork district began.
Decision-makers from both companies expressed their interest in the study and provided access to the field. Company 1 was founded in early 2012 and employs 12 workers (6 women) in operations. The average age was 53.6 years (range 27–69) and the average seniority in the company was 5.5 years. Nevertheless, they had long seniority in the cork district of SMF (28.4 years). Their work schedule was from 8am to 5pm and, on occasion, overtime was requested to meet production demands. All the workers participated in the study.
Company 2 was founded in 1979 and employs 40 workers, of whom 31 are in operations (20 women). The continuous operation of the company was made possible through a work schedule based on three fixed shifts, from Monday to Friday: morning shift (8am–5pm); afternoon shift (4pm–12am); and night shift (12am–8am). The company allowed the morning shift to participate in the study. This choice was based on the following criteria: (i) in the morning shift, all production sections were running, unlike what happened in the afternoon and night shifts; (ii) consequently, during the morning shift, the company was able to adjust the staff to allow time off for interviews and collective sessions. A meeting was held with the decision-makers to select the participants, following the criterion of diversity in terms of seniority. Nine workers were selected (seven women), all of them working the morning shift, and whose average seniority in the company was 15.2 years (range 3–40) and the average seniority in the cork district of SMF was 20.1 years.
2.2Study design
In both companies, the methodology was drawn from a qualitative approach. It encompassed the analysis of work activity, involving a number of methods that, once triangulated, support the understanding of the determinants behind the operating modes. This “activity approach” is the touchstone in our theoretical affiliation, whose epistemological foundations were detailed by Daniellou [17] or Lacomblez et al. [37].
Following the approach to ergonomic analysis [18], the fieldwork had the following data collection sequence: (i) document analysis; (ii) exploratory interviews with managerial staff; (iii) work activity observations (open and systematic observations), including verbalisations and video recording; (iv) semi-structured collective interviews with the workers; (v) and collective sessions to return and validate the results. Table 1 summarises the methods used in each company and the data collected.
Table 1
Methods and the data collected in the two cork companies
Methods | Data | Company 1 | Company 2 |
Document analysis | - Sociodemographic characterisation of the workers | —————– | - Number of workers, gender, age, seniority, and professional categories - Work schedules |
Exploratory interviews with decision-makers | - Characterisation of the company and its “position” in the cork district of SMF - Identification of the milestones of technological change and their implications for work and employment - Identification of tasks that were automated, and characterisation of the implementation conditions of such technologies | - Two interviews with managerial staff and an additional meeting with the foreman were held (in a total of 4 h) | - Two interviews with managerial staff and two additional meetings with the foreman and the quality manager were held (in a total of 5 h) |
Observations in situ | - Open observations of work activity - Systematic observations of human-machine interaction situations - Video recordings of the work activity to support systematic observations | - The work activity was observed for a total of 30h - The work activity in the selection section was video recorded for a total of 2 h (two 30-minute recordings for each of the two pairs of choosers) | - The work activity was observed for a total of 23 h (in the morning shift) - The work activity in the gluing section was video recorded for a total of 1h30 min (one 30-minute recording for each of the three gluers) |
Collective interviews with workers | - Characterisation of the workers’ career pathways both in the cork district of SMF and in the current company - Definition of task allocation between workers and machines - Characterisation of the human-machine interactions and in which conditions they are requested - Characterisation of the workers’ operating modes and strategies | - Six interviews (two workers per interview), lasted each one, on average, 1h20min | - Three interviews with nine workers participating in the study. In one of these meetings, to assist in verbalisation and collective reflection, the video recordings and photos were used as traces of the activity [18, 20, 27, 42]. Each meeting lasted, on average, 1h |
Group sessions | - Validation of the results | - One group session* to return and validate results of the observations in situ was held with the workers, which lasted 1h | - One final group session to return and validate results with 9 workers and 2 decision-makers (1 h) |
*Two group sessions were scheduled. The first meeting was held in 2020 before the COVID-19 pandemic. Due to the public health crisis, the second meeting has been postponed.
Ethics approval for this study was obtained from the Ethics Committee of the Faculty of Psychology and Educational Sciences of the University of Porto.
2.3Data reduction and analysis
In each company, we observed the activity in all production sections. The permission for observations was requested in person to the workers. The verbalisations collected were then discussed in the context of collective interviews to explore the intentions guiding particular actions (e.g., the interaction with the machine), as well as the factors that influence them (e.g., organisational, technical, material, or spatiotemporal determinants).
After a period of open observations, the researchers carried out a stage of systematic observations at the workstations. To support these observations and their qualitative analysis, the research team videotaped and photographed some events. It should be noted that these procedures took place after the consent of the workers and the foremen, and all material (video and photos) were only kept for analysis after the workers’ approval. To select the events to be recorded, we took into account what the workers identified as reference situations in their activity, that is, situations that appeal to the workers’ expertise in the relationship with the machines (e.g., anticipation of malfunctions and/or incidents; precision in detecting defective cork stoppers). This stage supported the analysis of the observable part of the workers’ know-how. At this point, observation-based data were used to generate chronicles of activity through ActoGraph® software [38] so as to better illustrate the operating modes and their temporal organisation. To this end, each observation treated with ActoGraph® was structured into a plan encompassing [38]: (i) the categories of observable facts and/or events (postures, gestures, movements, sequence of operations; interaction with colleagues; places); (ii) the sequence, or timing of observation; and (iii) the scope of observation.
The observations and the chronicles of activity were complemented with collective interviews. In addition to enabling the validation of our observations, these interviews aimed to collect data on the non-observable dimensions of the activity (e.g., control strategies that are difficult to observe) and to explore determining factors of the operating modes, the reasoning behind them and their potential significance [20, 39]. As alluded to in Table 1, the interview guideline addressed four main topics. Some of the questions asked in these interviews were: (i) What has changed in the way you do the work since the introduction of automation? (ii) What do you have to pay attention to when the machine is working? (iii) What tells you that the machine is working well (e.g., auditory and visual controls)? (iv) What is the machine still not capable to see in the cork stoppers (e.g., quality defects)? (v) What tells you that a cork stopper is a good one? And what are your reference points (e.g., visual, tactile)? (vi) What do you see first when you are looking at the cork stoppers? (vii) What do you tell yourself while doing the work (e.g., in moments when you have multiple requests; or a machine is not working as expected).
The collective interviews were done at the companies during working hours. The interviews were transcribed and coded to describe the workers’ viewpoints about the operating modes and the strategies developed by relating to automated machines. As for the process of coding, patterns in semantic content (or themes) within data were identified in an inductive (data-driven) approach [40]. The first step of the analysis was dedicated to generating the initial codes in our data set. Subsequently, we moved into the second step, when the analysis was dedicated to collating the codes within themes in order to identify determining factors behind the operating modes, bringing to light the reference points used by the workers. The themes were: “technical (machine-related)”, “raw materials”, or “organisational and production determining factors”, “references points (visual, tactile, auditory, olfactory)”, “human-machine interaction modes”. Verbatim excerpts from interviews describing some of these themes are provided in the results section.
3Results
3.1Factors behind choices of automation: The decision-makers’ viewpoints
In both companies, the processes of technological change have resulted mainly in the introduction of automated machines with the following objectives (i) to increase the speed of production processes; (ii) to meet the growing quality demands and improve the quality of cork stoppers; and (iii) to increase the range of products, beyond cork stoppers for wine. The need to guarantee the quality of cork stoppers was mentioned by the managerial staff of the two companies as a determining factor to invest in technology. Currently, the most significant challenge that this sector must face concerns the cork contamination with trichloroanisole (“TCA”, which is an odour that can contaminate the wine) [35]. Particularly, company 1 has invested in technology intending to prevent the entry of contaminated cork into the production chain and/or identify the cork stoppers with “TCA”.
Such as in other industrial districts, there is an “anchor company” in the cork district of SMF, i.e., the largest cork company in this region, with more than 250 workers and control over distribution channels. The Head of company 1 pointed out the fact that the technological changes occurring should be interpreted in light of the dominant position in the market of this “anchor company”:
“We’ve realised that we couldn’t manufacture just one type of stoppers, and some opportunities to buy machines to produce stoppers for champagne have arisen (...). We need to consider that the market is dominated by the largest company ... Even though what we produce is a crumb compared to them, we are an alternative in the market. We just bought a machine to produce technical stoppers (...) if we don’t sell natural [cork stoppers], then we’ll sell technical stoppers” (Head of company 1).
Another point in which both managers converged regards one of the main “threats” that the cork district has recently faced. In the early 2000 s, the sustainability of the cork district was challenged by the rising market share of companies producing plastic stoppers:
“The sector faced the so-called wave of plastic stoppers. They could be produced much faster and were cheaper too” (Head of company 2).
“In fact, this was a catalyst for us, because it forced us [the cork district of SMF] to produce better, with more quality, to the extent that today the plastic stoppers fashion has died out” (Head of company 1).
As a matter of fact, from the managers’ point of view, the investments in the automated machinery and other technological tools to detect stoppers with “TCA” have contributed to raise the competitiveness of these companies.
3.2What fractions of work were automated?
The production processes in the two companies have some similarities, even though company 2 does not manufacture stoppers from cork strips (the stoppers are bought from suppliers and then introduced into the industrial chain). By contrast, company 1 buys cork planks, which are first hand-cut into cork strips and then perforated with manual drills to give rise to the natural cork stoppers. Table 2 describes the production sections of the two companies.
Table 2
Description of the sections in the cork stoppers production chain
Production section | Main operation | Company 1 | Company 2 |
Cutting | - The cork planks are hand-cut into parallel strips using a knife. | • | |
Punching | - The cork strips are manually punched through a sharp cutting cylinder to form natural cork stoppers. | • | |
Rectification | - The stoppers are counted (through a pre-sorting machine), polished in the bodies, and rectified in the ends by abrasion. Such processes aim at guaranteeing the length and diameter conformity of the stoppers. | • | • |
Selection | - The stoppers are selected - “chosen” - according to quality classes and defective stoppers are separated. This process could be divided into two selection moments: the first is an automated selection, and the second is done manually by workers as the cork stoppers pass on a conveyor belt. | • | • |
Washing, bleaching, and drying | - The stoppers are cleaned from dust and, depending on the customers’ requests, the stoppers are given a lighter colour on the surface by bleaching. | • | • |
Printing | - The stoppers are marked with the customer brand. This process could be done with ink (in the body of the stoppers) or fire (in the ends of the stoppers). | • | • |
Gluing | - Caps (of wood, PVC, porcelain, glass, or metal) are placed in the end of the stoppers (through an automated gluing process) giving rise to the so-called “capped cork stoppers”. These stoppers are usually used with liqueur/fortified wines. | * | • |
Extrusion | - The stoppers for champagne are produced through the agglomeration of cork granules and then the bodies of stoppers are extruded, resulting in rods to be cut in the desired length. | ** | • |
Expedition | - The cork stoppers are packed in bags, which are injected with sulphur dioxide. Before this, the cork stoppers could be subjected to a final visual inspection which is done by two workers (this stage only takes place when the customers demand it). | • | • |
*Company 1 has recently introduced the gluing section, and it is still in the trial stage. In this section, it will be produced one type of the so-called “technical stoppers”, by gluing cork discs onto the ends of cork stoppers (e.g., in the case of stoppers for champagne and sparkling wines). **Company 1 is currently preparing an extrusion section, which is expected to be finished in the last trimester of 2021.
In each company, the cork stoppers production chain may be divided into seven stages (see Table 2). For this study, the analysis was focused on the work activities in the selection section (company 1) and the gluing section (company 2). To select these work situations, we took into account the fact that the work activity was more distributed between human operators and machines. In addition, work activity analyses were carried out in the remaining sections, and they were detailed in the context of other studies [32, 33, 36, 41].
In company 1, the selection section is composed of four automated selecting machines and two manual choosing conveyor belts. Four female employees work in this section (the “choosers”), who work in pairs (two workers per conveyor belt). In terms of role division between workers and machines, the cork stoppers are firstly selected through the automated selecting machines according to nine pre-defined quality classes1 and the defective stoppers are separated (e.g., stoppers with fractures on the surface; or small holes caused by insects when the cork is still on the cork oak). Based on machine vision techniques, the stoppers are classified according to the look of their surface. Then, each basket of cork stoppers classified by the selecting machines is subject to a manual selection on the conveyor belts. Here, the two choosers separate the defective stoppers that were not previously identified by the machines and discriminate the stoppers that must go to an upper, or lower, quality class.
According to the observations, apart from performing the manual selection, the choosers must guarantee (i) the supervision and the feeding of the automated machines; and (ii) the management of incidents, such as stoppers jams and faults in the automated selecting process. Such operations require a pair of choosers to move between the conveyor belt (where they usually work sitting) and the four automated machines. This pair of choosers – who supervise the machines – was formed by two experienced workers.
The automated selecting machines have not eliminated the manual selection. Rather, the process of cork stoppers classification is now faster, since one automated selecting machine can classify up to 12000 stoppers per hour – this process is called “opening the selection”, in which machines discriminate the stoppers into the nine quality classes. Afterwards, the choosers carry out the manual operation known as “fine-tuning the class”, which regards the visual selection of the cork stoppers as they pass on the manual choosing conveyor belt.
The cork stoppers classified by the machines as being defective are also checked by the choosers but at the end of each automated selection process (the choosers check the “defective basket” to spot good stoppers). Nonetheless, these stoppers do not pass on the conveyor belts. This fact is related to what the choosers referred to as “the worst case”: “It’s worse to sell a defective stopper than not selling a good one”.
In company 2, the gluing section has currently six automated gluing machines, which are operated by three female workers (the “gluers”) per shift (two automated machines per worker). Here, the automation of the gluing process was introduced in 2012, with the first machine for placing caps on the end of stoppers. Automation replaced manual procedure, in which the workers manually glued the caps one by one using heated glue, except when some customers require capped stoppers to be manually glued (e.g., in the case of glass caps for premium wines). Conversely to what happened in the manual method, the operators now work the entire shift standing up, and moving constantly between the two automated machines they are in charge of. The process of gluing has been speeded, which has led to an increase in the number of boxes with caps and bags with capped stoppers the gluers have to move. Particularly, the heaviest boxes can weigh up to 30 kg (in the case of wooden caps), and the gluers have to lift them to shoulder level to unload the caps into the machines. On the other hand, by automating, the risk of burns from hot melt glue has decreased, as workers now handle small glue pillows (to feed the machines), instead of directly handling heated glue.
In addition to assure the feeding of the machines (with cork stoppers, caps, and glue pillows) and the pre-emptive handling of incidents and malfunctions during the automated gluing process (e.g., stoppers from smaller calibres get stuck in the gluing mechanism), the workers perform a manual selection of the stoppers right after they have been glued. This visual selection not only aims at ensuring the quality of the gluing but also identifying defective cork stoppers that were not separated in downstream stages. In the collective interviews, the gluers highlighted that their previous work experience as choosers was crucial for performing this final selection. One of the gluers described her perception when a researcher questioned how she identified the defective stoppers at the end of the gluing process:
“I can’t really explain it ... , it’s automatic for me. I see everything, the bodies [of the cork stoppers], the ends, the caps, and the defects show up. If the stoppers have defects, they’ll appear, you look at the stoppers and it appears (...). I was in the selection section for 16 years, so I’m used to choosing” (Worker in the gluing section).
In fact, company 2 has adopted such a criterion since the introduction of automation in the gluing section. Thus, new gluers hired firstly work as choosers, at least, for one month, a period during which they learn the nine quality classes and have the possibility of doing the manual selection. Through this initial stage in the selection section, the company tries to set an opportunity for the (new) gluers to learn from the experienced choosers. It is crucial for the company that the choosers and the gluers share, as much as possible, a “common representation” about each possible defect in the cork stoppers.
In terms of training, in both work situations analysed (the selection and the gluing), the workers were given a short training to work with the machines led by the machinery suppliers (an initial training was provided about the mechanisms of the machines).
The introduction of automation has generated new rhythms for the activities, which are now carried out under time constraints imposed by the automated functioning of the machines. Besides the pace of work, other demands have arisen, according to the workers’ standpoints. Table 3 describes the sequence of core operations in each work activity, as well as the sources of complexity that the workers have to handle.
Table 3
Characteristics of the work situations from the workers’ perspective [2]
Section | Automated machines | Core operations in the worker activity | Sources of complexity | |
Company 1 | Selection | Four automated selecting machines | - Feeds machines’ pockets with stoppers - Programmes machines for the automated selection according to different quality classes - Supervises the automated selection of stoppers and identifies deviations or faults - Manages cork stoppers jams - Cleans the automatic vision cameras of the machines (including the chains where the cork stoppers pass) - Fine-tunes the class after the automated selection | - Cork stoppers jammed in the machines’ pockets - Cork stoppers jammed in the automatic vision cameras of the machines - Washed cork stoppers cause more machine stoppages - Deviations and errors in the automated selection carried out by the machines (compared to the sample of cork stoppers of that quality class. This sample is manually chosen by the most experienced chooser) |
Company 2 | Gluing | Six automated gluing machines | - Feeds the machine’s pockets with cork stoppers, caps, and glue - Manages cork stoppers jams in gluing mechanism of the machines (when the stoppers get stuck in the mechanism) - Adjusts and tests the automated machines according to different sizes of cork stoppers and caps - Checks the stoppers (after the gluing) to detect the defective stoppers (defects that were not previously identified) - Packs the capped cork stoppers | - Variability associated with different caps sizes (the machines must be adjusted and tested for each cap size) - Smaller calibre stoppers lead to more jams (requiring continuous vigilance) - Cork stoppers jammed in the gluing mechanism of the machines (after clearing, this mechanism must be manually adjusted) |
These situations entail different causes of trouble related to the variability in the cork stoppers, and which the automated machines are unable to deal with (e.g., different calibre stoppers lead to jams or incidents). In the face of the lack of conformity between materials and machine tolerances, the workers’ knowledge of the characteristics of the cork and their ability to early recognise, prevent, or remedy incidents in the machines, reduce the gap between theoretical definitions of work and the real work. In a particular work environment, which is always partially unanticipated and non-standardised, the work activity, therefore, defines compromises to manage different demands (related to the raw materials and automation operation) and to keep the efficiency and a sense of a job well done [2].
3.3Setting a good milieu for the machine
To better illustrate the operating modes the workers have developed in their relationship with the machines, we analysed observation-based data. Here, we present an excerpt from a chronicle of the activity treated with ActoGraph®. The chronicle presented in Fig. 1 refers to the work activity in the selection section (company 1).
Fig. 1
Chronicle of the activity of two workers (a pair of choosers working in the selection section – company 1).
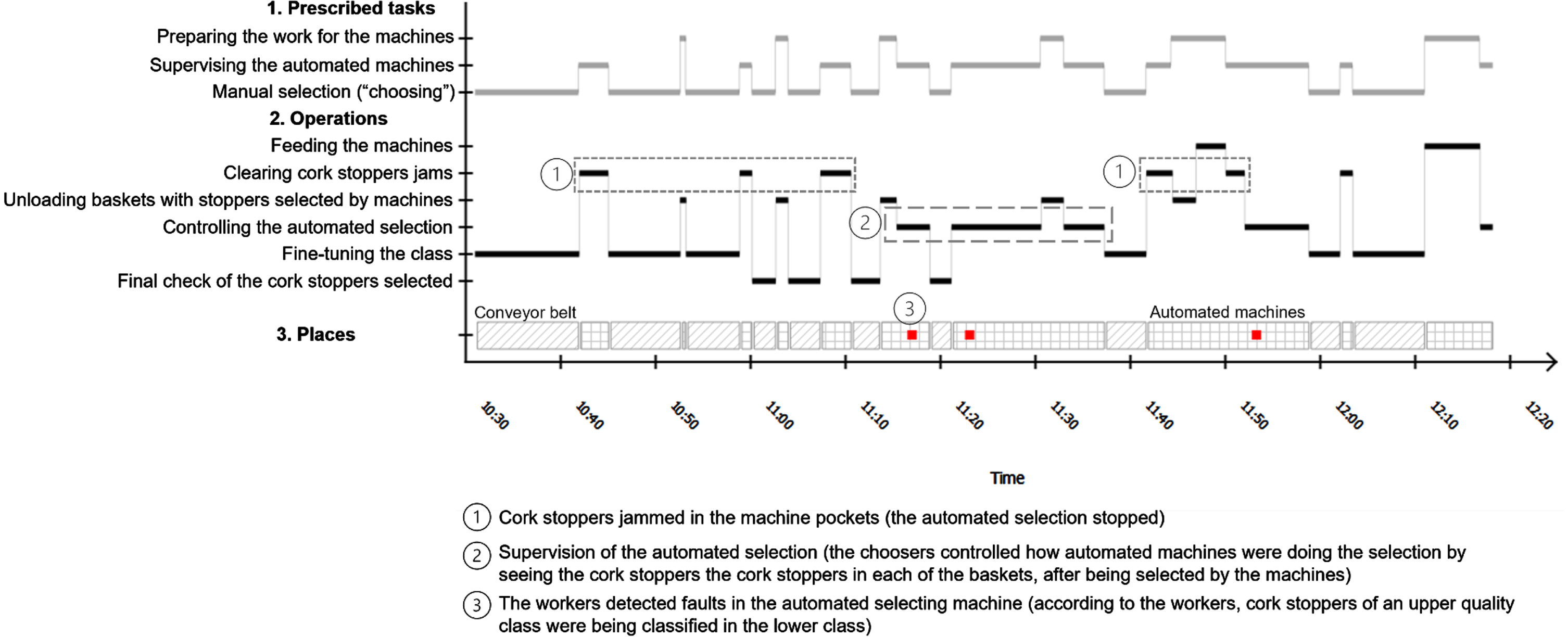
This chronicle was generated from a systematic observation plan with the structure which follows: (i) observation of two choosers who are responsible for the automated selecting machines; (ii) three categories of observables – tasks, operations (observable actions in carrying out the tasks), and places; and (iii) the sequence observed (lasting approximately 2 hours) regards a moment when the choosers were performing the manual selection (“fine-tuning the class”) on the conveyor belt and the machines were classifying the stoppers into three quality classes (between “extra”, “superior”, and “first”). In the analysis, the observation data were complemented with workers’ verbalisations during the observation and interview.
According to Fig. 1, the choosers must face two main temporal frameworks with different situational requirements. The first framework refers to the management of cork stoppers jams (stoppers jammed in the machine’s pockets or the machine vision area). Indeed, the variability of cork stoppers (mostly, in terms of sizes, but also differences in surface treatments) leads to more machine stoppages. In these circumstances, the choosers’ activity is interrupted by the need to manage these incidents. The four automated machines are placed right behind the manual choosing conveyor belts. Yet, the frequency of jams requires several movements between the two places, which in turn has costs in terms of fatigue, as stated by one of the choosers (when reaching the conveyor belt after setting free the machine) during the observation:
“I’m already tired ... Some days they jam for anything and everything (...) It’s hair-raising!” (Worker in the selection section).
In the collective interview, one of the choosers also explained the implications of machine stoppages for the activity:
“If the machines ain’t running well, we’re always stopping the conveyor belt to go there, and then we’re struggling between the two places [the conveyor belt and the machines]” (Worker in the selection section).
Faced with these constraints, the choosers explained how they attempt to set a proper milieu for the machines, and thus reduce the probability of stoppages (a flawless and uninterrupted production):
“The machine can stop more often when it’s dirty with cork dust. We know whether the machine is selecting unwashed stoppers, it can jam many times (...). Here, we’re always looking at them [machines]. Whenever we go there [to the machines] we try to clean it with the air blown gun” (Worker in the selection section).
The second temporal framework revealed by this chronicle (see Fig. 1) is related to the operation of supervising the automated selection. According to the choosers, this is a core operation in which they check how the machines are classifying the cork stoppers in order to identify deviations (e.g., stoppers from an upper class selected as belonging to a lower class). In case of faults detected, the choosers may compare the automated selection with a sample of stoppers. For each quality class of cork stoppers, the workers have a “sample” (manually made by the most experienced chooser), which they use to program the automated machines according to the workers’ criteria on what is a stopper for each class. As illustrated in Fig. 1, there were three moments in which the choosers detected deviations in the automated selection, as explained by one of the choosers during the observation:
“It’s not right, look at the sample [one chooser says to her colleague], it’s different. (...) The machine should be taking more stoppers to ‘superior’ ... There are many stoppers in the basket of ‘first’ [quality class]” (Worker in the selection section).
In this case, and after comparing with the sample and asking the foreman’s opinion, the choosers decided to stop the machine to calibrate it. In the interview, the chooser explained that:
“The machines don’t always choose well. (...) sometimes we have to talk to them [machines], I mean, ask for taking more stoppers out ... After all, the stoppers have to be chosen our way” (Worker in the selection section).
Hence, the choosers highlighted the importance of detecting these faults in the automated selection to then program the machines (“talk to them”) using their criteria for each class of cork stoppers. It should be noted that the choosers’ ability to calibrate and program the selecting machines was learnt, mainly, by doing (e.g., as workers progressively discovered the characteristics of the machine).
The choosers also pointed out that there are some defects that the automated selecting machines cannot see, and, for this reason, the defective stoppers are not separated. Here, the choosers’ know-how plays a crucial role during the manual selection:
“[The machine] doesn’t catch defects in the ends of the stoppers because the machine vision reads the bodies [of stoppers] (...). Other defects have the same colour as cork, and the machine lets the stoppers pass” (Worker in the selection section).
These stoppers are then manually selected by the choosers on the manual choosing conveyor belt, in a process that appeals to the workers’ expertise. In fact, the workers’ criteria on quality classes are based on their knowledge about the cork and the evolution of its defects, as a “memorised repertoire of defects” possible by the experience, inasmuch as some defects are relatively emergent compared to others due to the recent evolution of cork in the forest.
Finally, another frontier between the work activity and the automated selecting machines concerns the operation of “fine-tuning the class”, an operation in which the customers’ demands intervene, as mentioned by one of the choosers:
“The boss says: ‘this customer wants the class to be cleaner’ [i.e., stoppers of that class should be as homogeneous as possible], and then we have to remove more stoppers, letting only the good ones go through. (...) We know some customers ... The selecting machines don’t know this, for them, a stopper seems to have a defect or not, and it moves forward” (Worker in the selection section).
Such arbitrations made possible by the choosers’ activity are important for the company, insofar as they contribute to enhance the quality of cork stoppers selection, and thus the stability of business relationships. As a matter of fact, that is why this company has kept the manual selection on the conveyor belts as fundamental:
“Whether we like it or not, given the defects that cork presents today, the cork stoppers have to be passed on the conveyor belts [to be manually selected]. There are some defects that machines simply don’t see” (Head of company 1).
3.4“Finding the sound of my machines”: A diagnosis in advance
The observations in the gluing section (company 2) revealed the workers’ strategies to reconcile the demands that the introduction of automated machines has posed. Here, the workers have to manage overlapping temporal frameworks associated with the automated process of gluing, with the aim of attaining the objectives in terms of quality and quantity. A worker in this section mentioned in the interview:
“Having two machines means we’re always running from one side to the other. We supervise the gluing, feed the machines with stoppers and caps, do the selection for catching some defect that has passed [after the gluing], and pack ... It’s really very demanding. It’s tiring, not only physically, but also by the attention I have to pay (...). If the machine collaborates, the shift will run better” (Worker in the gluing section).
The automated machines altered the gluing procedure, which has led the workers to set up other strategies to adjust their operating modes. In the collective interview supported by video recordings of the work activity, the gluers explained an anticipatory strategy that enables to forestall the automated gluing machines from stopping. More precisely, the workers revealed how they have developed a sensitivity to the change in sound relating to their machines, by collecting and filtering signals, as explained by a worker while watching a video tape of herself:
“I had to learn to find the sound of my machines in amidst all the noise from the factory. Without looking at the screen [positioned on the back of the machines], you know the problems are coming (...). When you catch it [the sound], firstly, you’ll hear the caps in the machine’s pocket, with a little slower pace, and shortly after it’s the speed of the stoppers passing by in the gluing mechanism, look, it’s different, isn’t it? So, we need to act fast” (Worker in the gluing section).
Apart from perceiving accurately even the smallest changes in the background noise, the workers revealed that, in their “sensory awareness” [21], it is also decisive the ability to classify and integrate such changes while they are occurring (e.g., without seeing the stoppers inside the machines, the gluers can mentally visualise the processes occurring). However, in some cases, due to the multiplicity of demands, it is not possible to impede the problems or diminish their importance, and the automated gluing machines stop. Here, this temporal framework becomes a priority, as explained by the gluers:
“The priority is always to set the machines free, ever. We have to have production, if they’re stopped, we aren’t producing, we can’t simply glue caps manually”; “My priority is to clear the jam and restart, and only then to see the defects and pack (...)” (Workers in the gluing section).
Therefore, the anticipations to prevent stoppages or to rapidly repair the situation by calibrating the machines constitute important elements of the workers’ expertise. In company 2, a mechanic (a machine setter) assisted in the calibration and adjustment of the machines. The gluers pointed out that some tweaks performed by them were partially learnt by “peering over the mechanic’s shoulder”:
“I learnt by watching how the mechanic did it. Later on, it was by trial and error (...) This machine isn’t easy to handle. But, at one point, I got the trick, and finally got calibrated it by myself. It looks like that, from that moment on, I have my hands on the gluing mechanism” (Worker in the gluing section).
Key here is that this embodied expertise is developed in action, i.e., as the workers elaborate procedures while appropriating the automated operation of the gluing machines and constitute representations – as an operative image – about its functioning. According to the workers’ views, this know-how is decisive to confer a sense of control in performing the activity [2, 36].
4Discussion
4.1“The defect shows up”: The expertise of seeing and choosing
Despite belonging to a traditional industry with a small scale of technological transformation, the two cork companies have upgraded their productive capacity by implementing automated machines, whose functioning is largely supported by a “heritage of specialisation” constituted thanks to human work activity.
We found that, in the analysed work situations, the main operation of the activity has not been divested by automation: seeing the cork stoppers to choose the quality classes and look for the defects. Cork is a raw material in permanent evolution, whose physical characteristics are not changeless, and new defects are emerging linked, for instance, to forest exploitation. Given the variability of defects, and with which machines vision cannot fully cope, we found that the choosers’ activity considers the strengths and limits of machines in facing the current demands of production. The automated selecting machines can identify the most visible defects (e.g., fractures). Nevertheless, other defects are much more difficult to detect. For example, the “dry year” is a defect that may be inferred by the presence of two parallel lines from the top to the end of a cork stopper. According to the choosers, this is the most difficult defect to see, and the machines cannot spot it (consequently, the stoppers are not rejected by the machines). In these circumstances, when seeing the stoppers on the conveyor belts, the choosers’ attention and handling dexterity are directed to “see the invisible”. This dexterity calls on all the senses for handling and processing the cork stoppers, involving not just precision (in detecting the defect), but also speed and rhythmical coordination (between the two choosers).
The act of looking at the stoppers is rooted and informed by the experience, namely, concerning the expected configurations of some defects on the surface of the stoppers. For example, the “bug” is a defect characterised by a small hole caused by an insect. Unlike the machine vision that may confuse this defect with cork pores, the choosers mobilise other criteria for a proper interpretation. By seeing the stoppers, the choosers usually detect the “bug” not by the presence of a hole, but by two small holes: one is the point of entry of the insect in the cork, and the other is the point of exit. Additionally, other defects are identified by making use of other forms of sense perception, such as the smell (e.g., to infer the presence of TCA) and the touch. For instance, the “woody” is a defect characterised by the presence of sharp nodes in the body of the stoppers; in case of doubt, the choosers detect this defect by passing their fingers on the rough surface of the stoppers. The choosers’ know-how is expressed as knowing how to look at the stoppers, in an embodied expertise wherein talk (between the two choosers in the pair), touch, vision, gesture dexterity (involving hand-eye coordination) and at times the smell are bound up in the act of interpreting the stoppers. Thus, “there is no seeing per se” [43] detached from other embodied practices, which imply the preservation of “perceptual-motor reference points” in carrying out the activity [27].
The “ways of seeing” in professional activities have been investigated in various contexts from the anthropological works of Goodwin and Goodwin [44] on the professional vision and extended in different fields. The work situations investigated range from the most traditional industries to the most technological tools-saturated environments, of which airports [44] and health contexts [31, 43, 45] are examples. Particularly, Goodwin and Goodwin [44] illustrated that the competent gaze is always part of larger courses of activity, and these are indeed the focus of workers’ attention. The choosers and the gluers do not see an isolated object with some attributes (e.g., a cork stopper with one defect); instead of that, there is a larger framework that is not extrinsic to the act of seeing, encompassing the quality classes of cork stoppers; the automated selection previously made by the machines; the size of the stoppers; or the customers’ demands. This contingent framework establishes the ground and relevance for the act of seeing and choosing the cork stoppers.
In this vein, according to Tomás et al. [45], by analysing the constitutive practices of the professional ways of seeing, it is possible to affirm the social nature of perception and, more generally, of cognition. The act of seeing in professional activities therefore neither occurs in a social vacuum [43] nor is it an entirely individual process [45]. It means that the expertise in seeing is weighted by the professional paths (and even the history of the profession) in which the workers may be confronted with other “ways of seeing” when interacting with their pairs, other customers’ demands, or even other criteria for each quality class of cork stoppers (depending on the company they work for).
4.2Regulations and “anticipations of the body” in the face of the unexpected
The introduction of automation in the two work situations has defined new temporal frameworks for the activity, which are particularly visible when recovering the automated operation, detecting errors in the automated selection (and mitigating these consequences), and preventing stoppages in the gluing machines by collecting hearing signals. The workers play thus an essential role in the system performance and reliability.
Woods and Dekker [14] summarised a pattern of reverberations after the deployment of new technology in work contexts. Concretely, the authors flagged new complexities requiring from human operators sensitive strategies to avoid failures and tailor the human-machine architectures envisioned so as to meet the operational and production targets. Also, in the field of work psychology, Faverge [46], and later other authors [e.g., 6, 47, 48], pointed out this pivotal role performed by operators within automated work systems. More precisely, Faverge [46] highlighted the regulation strategies made of work experience, through which workers recover from disturbances, or unpredictable events, and regain the normal functioning of the system. In addition, in his study in a small company of the food industry, Clot [6] demonstrated how the work activity involved several recovering actions towards optimising the conditions of the machines operation. And the author concluded that “the work consists in creating a milieu that is somewhat favourable to the operation of the machine given the permanent variability of raw materials and, more generally, the instability of the work environment” [6, p. 32]. This “favourable milieu” was visible in the chronicle we present in Fig. 1: several movements between the manual choosing conveyor belt and the automated selecting machines; actions to recover the system after successive jams; visual control to prevent deviations in the automated selection. In the case of the gluers, the recovery actions are largely grounded in anticipations that allow not only to identify the possible causes of trouble but also to integrate them and to act accordingly, avoiding disruptions. Poizat [29], reflecting on the role of the body techniques within automated work settings marked by repetitive tasks, underlined the complex “anticipations of the body” that workers set up to deal with the imponderables of work situations, contributing to the efficiency of the system.
Yet, acknowledging the positive effects on the system made possible by human activity implies, in the psychological analysis of work, understanding the conditions under which such successful performance takes place [48], as well as the new challenges for work activity (e.g., in terms of job demands and resources) and the effects on workers’ health [15, 53, 54]. This stance contrasts with who has ventured the existence of neutrality associated with automation technologies in work.
4.3The sustainability of human-machine configurations: Future challenges for activity ergonomics and work psychology
In the face of operational constraints, cork-related variability and machines failures, the workers developed strategies that are out of the prescribed frontiers between human activity and automation. While the machinery is renewed by incremental automation solutions, these workers in the cork industry have maintained “sensory reference points” [15, 20] of their activity. This expertise, as a “body-memorised feel” [21] for handling and processing the cork stoppers and all the variations in the work environment, rests on interactional and physical/haptic material bases, linking precision and speed, quality and quantity. An “operational expertise layer” in the manufacture of cork stoppers is thus cardinal, enriching the theoretical allocation of tasks between human operators and machines.
However, the evolution of industrial systems in terms of automation raises some issues that challenge the “durability” of work activity [49], i.e., its future sustainability taking into account the constraints and difficulties posed to the workers within these work settings and the impacts for occupational health. Fadier and De La Garza [50] reminded us that a set of modifications takes place with automation: growing cognitive constraints related to human-machine interactions and the need to anticipate incidents; injunctions to intervene in degraded modes; or difficulties in understanding how automation works (an “opaque” work). More recently, Bobillier Chaumon [15] reflected on the possible effects for workers’ health when in human-machine systems it is the worker “who is the variable of adjustment and it is up to him/her to find an acceptable compromise of functioning” [15, p. 14]. Examples of these effects are:
• the sense of loss of control over the activity. For instance, when workers are deprived of the ability to control their work pace. It happens in particular with the deployment of automation technologies whose pace of functioning is quite distinct from the pace of the human being. Thus, the pace of human operations and the pace of machines evolve towards an asynchronous mode [9].
• a narrow operational leeway to put in practice the strategies developed with work experience [19], which can lead to the subordination of workers to automation and undermine human autonomy [7, 10].
• the invisibility of activity. When the activity becomes more distributed between human-machine systems, workers may find difficulties to assess what their contribution to work is. In these circumstances, it is the meaning of work that is at issue [6, 42], since the workers could experience difficulties in carrying out a work in which they recognise themselves and for which they are recognised [15]. This professional recognition plays an important role in the construction of health.
Faced with these implications, the question is: how could the renewal of human-machine interaction modes brought about by technological progress support sustainable work situations in the future? Here, sustainability should be understood over the life course, a work where people may remain healthy, integrated, and efficient throughout their career paths [51]. According to Thatcher et al. [52], this implies considering the forms of work organisation, the physical environment, the social environment, the work intensification, or the learning opportunities. The theoretical and practical challenges ahead for ergonomics and work psychology communities are therefore related to the analysis of how automation technologies are integrated into professional activities, how they constitute resources and constraints for work activities and, finally, how workers can healthily construct an effective experience with these technologies.
4.4Further research perspectives
This study has limitations with respect to the scarcity of data on the evolution of risks factors and the workers’ health. These issues should be considered systematically in future research. In the case of the gluing section, the risk of burns from glue has decreased by automating the process. However, our study enabled us to collect initial data regarding other risks with consequences in terms of occupational health [36, 41]. In both work situations, the workers are exposed to cork dust, which is even greater in the case of the choosers (frequently, these workers have to smell the stoppers to detect the presence of TCA). Also, by automating, the number of bags with cork stoppers and boxes with caps the workers have to move per day has increased. Even though the weight of these loads might vary (according to the stoppers calibres, or the type of caps – of plastic, glass, metal, or wood), the workers revealed health complaints related to back and shoulder pains. In the case of the choosers [41], these complaints are aggravated by the postures required at the conveyor belts. Here, the main health complaints have to do with pain in the cervical spine, tendonitis (arms and shoulder area), and pain in the wrists.
As well as that, the automated machines have imposed periods of continuous cognitive demands associated with the need to supervise these automated processes, to “see the invisible”, and to anticipate stoppages (e.g., to mitigate the consequences for production, but also to protect one’s health, since a machine stoppage requires the gluers to remove all the stoppers and caps from the machine, which is physically demanding).
These factors can help with the understanding of work sustainability. Therefore, as future work, we intend to orientate the study in this direction. This choice finds support on the systemic approach implemented since the beginning of the larger research project in which this study is framed – involving the participation of all stakeholders in the cork district of SMF: workers, companies’ decision-makers, the union for the cork sector, the APCOR and the Cincork.
5Conclusions
This study aimed to shed light on the emerging frontiers between work activity and machines, at a time when automation seems to be a resource for the cork companies in order to face some challenges in this Portuguese cork district. In the macroscopic inquiries, while some reveal a general tone of optimism asserting that new complementarities between human operators and automation will emerge, others foresee “dystopic” scenarios by announcing the complete substitution of human work (a “workless” future). Our goal was not to formulate a refutation of such theses, but rather investigate the phenomenon from its micro-level, without decoupling it from a larger sectorial context (an industrial district), though. From the activity level, this study reveals how experienced workers, in their relationship with automated machines, mobilise embodied reference points of know-how, which are inscribed in the experience of the senses. Nonetheless, the possibilities to make such know-how visible are infrequently, not only by the nature of this expertise (that goes unsaid) but also due to the lack of opportunities for workers to exchange, demonstrate and discuss their ways of doing. This takes time, different mediations [55] (e.g., formative mediations provided by experienced workers who guide learners as they do the work) and opportunities for doing the work in concrete situations. However, these assumptions are operationally conditioned in these small-sized companies in the cork district, given the time pressure to finish the orders and the little margin to hold training sessions to address content representative of the real work activity [e.g., 20] without interfering with the production levels. In both companies, the workers’ own learning is done by doing the job and much less through formal training. By trying to describe and understand the multiple components of these two work activities, our research findings could provide important clues to develop a reference tool for training new workers in the cork industry. This possibility should be further explored with the actors of the APCOR and the Cincork.
Finally, we sketched some future research avenues on the factors that can affect the sustainability of work activities. This way of analysis could be useful by challenging those very deterministic approaches that dictate a neutral “mutualisation” of the activity between humans and machines.
Acknowledgments
The authors thank the workers and the companies involved in the study for their participation and collaboration.
Conflict of interest
The authors declare that they have no conflict of interest.
Funding
This work was supported by the FCT - Portuguese Foundation for Science and Technology under grant SFRH/BD/139135/2018 and by the FCG - Calouste Gulbenkian Foundation (“CORK-In” project).
References
[1] | Eurofound. The digital age: Implications of automation, digitisation and platforms for work and employment. Luxembourg: Publications Office of the European Union; (2021) . |
[2] | Silva D , Cunha L . Automation and the Future of Human Work: An Everlasting Debate Renewed by the Work Activity. In: BlackN, NeumannW, NoyI, editors. Proceedings of 21st Congress of the International Ergonomics Association (IEA 2021). Springer; (2021) , pp. 273–81. |
[3] | de Terssac G , Soubie J-L , Neveu J-P . Systèmes experts et transferts d’expertise [Expert systems and transfer of expertise]. Sociol Trav. (1988) ;3: (88):461–77. |
[4] | Cavestro W . Automation, skills and the content of work. Int J Syst Sci. (1988) ;19: (8):1407–18. |
[5] | du Tertre C , Santilli G . Automatisation et travail. Utopies, réalités, débats: Des années cinquante aux annés quatre-vingt-dix [Automation and work. Utopias, realities, debates: From the fifties to the nineties]. Paris: PUF; (1992) . |
[6] | Clot Y . Le travail sans l’homme? Pour une psychologie des milieux de travail et de vie [Work without people? For a psychology of work environments and life]. Paris: La Découverte/Poche; (1995) . |
[7] | Parker S , Grote G . Automation, algorithms, and beyond: Why work design matters more than ever in a digital world. Appl Psychol. (2020) ;1–45. |
[8] | Gamkrelidze T , Zouinar M , Barcellini F . Working with artificial intelligence systems: Workers’ viewpoints and experiences. In: Proceedings of the European Conference on Cognitive Ergonomics (ECCE 2021): Siena, Italy. New York: Association for Computing Machinery (ACM); (2021) , pp. 1–7. |
[9] | Coron C , Gilbert P . Technological change. London: ISTE Ltd; (2020) . |
[10] | Barcellini F . Industrie du futur: Quelle place pour le travail et ses trasnformations? [Industry of the future: What place for work and its transformations?]. In: BourduE, LallementM, VeltzP, WeilT, editors. Le travail en mouvement. Paris: Presses des Mines; (2019) , pp. 136–47. |
[11] | Zouinar M . Évolutions de l’Intelligence Artificielle: Quels enjeux pour l’activité humaine et la relation Humain-Machine au travail? [Evolutions of Artificial Intelligence: What issues for human activities and Human-Machine relationships at work?]. Activités. (2020) ;17: (1):1–39. |
[12] | Howcroft D , Taylor P . “Plus ca change, plus la meme chose?” – Researching and theorising the “new” new technologies. New Technol Work Employ. (2014) ;29: (1):1–8. |
[13] | Shestakofsky B . Working algorithms: Software automation and the future of work. Work Occu. (2017) ;44: (4):376–423. |
[14] | Woods D , Dekker S . Anticipating the effects of technological change: A new era of dynamics for human factors. Theor Issues Ergon Sci. (2000) ;1: (3):272–82. |
[15] | Bobillier Chaumon M-E . Emerging technologies and issues for activity and occupational health. In: Bobillier ChaumonM-E, editor. Digital transformations in the challenge of activity and work: Understanding and supporting technological changes. London: ISTE Ltd; (2021) , pp. 3–15. |
[16] | De Keyser V . L’ergonomie et l’Europe en 2016 [Ergonomics and Europe in 2016]. In: Actes du 51ème de la Société d’Ergonomie de Langue Française (SELF 2016); 2016 Sep 21– 23; Marseille, France. Société d’Ergonomie de Langue Française;. (2016) , pp. 232–48. |
[17] | Daniellou F . The French-speaking ergonomists’ approach to work activity: Cross-influences of field intervention and conceptual models. Theor Issues Ergon Sci. (2005) ;6: (5):409–27. |
[18] | St-Vincent M , Vézina N , Bellemare M , Denis D , Ledoux E , Imbeau D . Ergonomic Intervention. Montréal: IRSST; (2014) . |
[19] | Coutarel F , Caroly S , Vézina N , Daniellou F . Marge de manoeuvre situationnelle et pouvoir d’agir: Desconcepts à l’intervention ergonomique [Operational leeway and power to act: Theoretical issues of ergonomics intervention]. Trav Hum. (2015) ;78: :9–29. |
[20] | Ouellet S , Vézina N . Activity analysis and workplace training: An ergonomic perspective. In: FilliettazL, BilletS, editors. Francophone perspectives of learning through work: Conceptions, traditions and practices. Springer; (2015) , pp. 241–56. |
[21] | Pfeiffer S . Robots, industry 4.0 and humans, or why assembly work is more than routine work. Societies. (2016) ;6: (2):1–26. |
[22] | Schwartz Y . Quel sujet pour quelle expérience? [Whose for which experience?]. Trav Apprentiss. (2010) ;6: :11–24. |
[23] | Falzon P , Teiger C . Construire l’activité [Building the activity]. Performances Humaines & Techniques. (1995) ;34–9. |
[24] | Leplat J . Skills and tacit skills: A psychological perspective. Appl Psychol. (1990) ;39: (2):143–54. |
[25] | Savoyant A . Quelques réflexions sur les savoirs implicites [Some thoughts about implicit knowledge]. Trav Apprentiss. (2008) ;1: :92–100. |
[26] | Judon N , Galey L , de Almeida V , Garrigou A . Contributions of participatory ergonomics to the involvement of workers in chemical risk prevention projects. Work. (2019) ;64: (3):651–60. |
[27] | Ouellet S , Vézina N . Professional know-how and MSD prevention: Conceptual and methodological reflection leading to their identification and the start of their construction. Perspectives interdisciplinaires sur le travail et la santé. (2008) ;10: (2):1–35. |
[28] | Le Bellu S , Lahlou S , Nosulenko V , Samoylenko E . Studying activity in manual work: A framework for analysis and training. Trav Hum. (2016) ;79: :7–30. |
[29] | Poizat G . Technique(s) et engagement du corps au travail [Technique(s) and engagement of the body at work]. In: DurandM, HauwD, PoizatG, editors. L’apprentissage des techniques corporelles. Paris: PUF; (2015) , pp. 223–36. |
[30] | Moricot C . Resistances of the body. The presence of the human body in the automated world. In: PiraniB, VargaI, editors. Acting bodies and social networks: A bridge between technology and working memory. University Press of America; (2010) , pp. 261–84. |
[31] | Anichini G , Geffroy B . L’intelligence artificielle à l’épreuve des savoirs tacites. Analyse des pratiques d’utilisation d’un outil d’aide à la détection en radiologie [Artificial intelligence and tacit knowledge. A case study on the use of a new tool for detecting abnormalities in radiology]. Sci Soc Santé. (2021) ;39: (2):43–69. |
[32] | Cunha L , Silva D , Lacomblez M . A transformação da cortiça como património de um território e a construção de um “projet-héritage” a partir do legado da atividade [The cork processing as a territory’s heritage and the development of a “projet-héritage” from the activity’s traces]. Ergologia. (2021) ;25: :159–70. |
[33] | Cunha L , Silva D , Macedo M . “This Is a Job for Women, Isn’t It?”: The Evolution of a Traditional Gendered Occupational Segmentation in a Portuguese Industrial Cluster. In: BlackN, NeumannW, NoyI, editors. Proceedings of 21st Congress of the International Ergonomics Association (IEA 2021). Springer; (2021) , pp. 429–37. |
[34] | APCOR - Associação Portuguesa da Cortiça. The APCOR’s Cork Yearbook 2020. Santa Maria de Lamas: APCOR; (2020) . |
[35] | Centro de Estudos de Gestão e Economia Aplicada. The cork industry: From the forest to the consumer. Santa Maria de Lamas: APCOR; (2020) . |
[36] | Silva D , Cunha L . Entre o recurso à automação e a experiência de uso de si: O que faz património? [Between automation and the experience of the use of oneself: What makes the heritage?]. In: CunhaL, Di RuzzaR, LacomblezM, SchwartzY, SilvaD, editors. Trabalho, Património e Desenvolvimentos - Travail, Patrimoine et Développements - Trabajo, Patrimonio y Desarrollos. Porto: Universidade do Porto. FPCE; (2021) , pp. 222–9. |
[37] | Lacomblez M , Bellemare M , Chatigny C , Delgoulet C , Re A , Trudel L , Vasconcelos R . Ergonomic analysis of work activity and training: Basic paradigm, evolutions and challenges. In: PikaarR, KoningsveldE, SettelsP, editors. Meeting Diversity in Ergonomics. Boston: Elsevier; (2007) , pp. 129–42. |
[38] | Boccara V , Delgoulet C , Zara-Meylan V , Barthe B , Gaillard I , Meylan S . The role and positioning of observation in ergonomics approaches: A research and design project. In: BagnaraS, TartagliaR, AlbolinoS, AlexanderT, FujitaY, editors. Proceedings of the 20th Congress of the International Ergonomics Association (IEA 2018). Springer; (2019) , pp. 1821–28. |
[39] | Barcellini F . Quelles conceptions de la cooperation humains-robots collaboratifs? Une expérience de participation au projet de conception d’un démonstrateur de robotique collaborative [Conceptions of human-robot collaborative cooperation. A case of participation in a collaborative robot design process]. Activités. (2020) ;17: (1):1–29. |
[40] | Braun V , Clarke V . Using thematic analysis in psychology. Qual Res Psychol. (2006) ;3: (2):77–101. |
[41] | CunhaL, SilvaD, MacedoM, LacomblezM. “My whole body is atwork”: the silence of gendered body techniques in cork industry in an era of automation. Ergonomics. (2022) ;1–13. |
[42] | Clot Y , Kostulski K . Intervening for transforming: The horizon of action in the clinic of activity. Theory Psychol. (2011) ;21: (5):681–96. |
[43] | Styhre A . Knowledge work and practices of seeing: Epistemologies of the eye, gaze, and professional vision. Cult Organ. (2010) ;16: (4):361–76. |
[44] | Goodwin C , Goodwin MH . Seeing as a situated activity: Formulating planes. In: EngeströmY, MiddletonD, editors. Cognition and communication at work. Cambridge University Press; (1996) , pp. 61–95. |
[45] | Tomás J-L , Ianeva M , Simonet P , Clot Y . Activité et vision professionelle [Activity and professional vision]. Rev Antropol Connaiss. (2020) ;14: (3):1–14. |
[46] | Faverge J-M . Le travail en tant qu’activité de récupération [Work as a recovery activity]. Bull Psychol. (1980) ;344: (33):203–6. |
[47] | Leplat J . La notion de régulation dans l’analyse de l’activité [The concept of regulation in activity analysis]. Perspectives Interdisciplinaires Sur Le Travail Et La Santé. (2006) ;8: (1):1–30. |
[48] | Re A , Macchi L . From cognitive reliability to competence? An evolving approach to human factors and safety. Cong Technol Work. (2010) ;12: :79–85. |
[49] | Béguin P , Duarte F , Lima F , Pueyo V . Activity at work, innovation and sustainable development. Work. (2012) ;41: :89–94. |
[50] | Fadier E , De La Garza C . Safety design: Towards a new philosophy. Saf Sci. (2006) ;44: :55–73. |
[51] | Volkoff S , Gaudart C . Working conditions and “sustainability”: Converting knowledge into action Noisy-Le-Grand: Centre d’études de l’emploi; (2015) . |
[52] | Thatcher A , Zink K , Fischer K . How has HFE responded to the global challenges of sustainability? In: ThatcherA, ZinkK, FischerK, editors. Human factors for sustainability: Theoretical perspectives and global applications. Boca Raton: CRC Press; (2020) , pp. 1–31. |
[53] | Guérin F , Pueyo V , Béguin P , Garrigou A , Hubault F , Maline J , Morlet Th . Concevoir le travail, le défi de l’ergonomie [Designing work, the challenge of ergonomics]. Toulouse: Octares; (2021) . |
[54] | Bobillier Chaumon M-E . Emerging technologies and digital transformations of the activity: Challenges for activity and health at work. Psychol Trav Organ. (2021) ;27: (1):17–32. |
[55] | Vidal-Gomel C , Delgoulet C . Analysing relationships between work and training in order to prevent psychosocial risks. Saf Sci. (2022) ;145: :1–9. |
Notes
1 In the cork industry, the stoppers can be discriminated into nine quality classes. The choosers classify the cork stoppers into a range of quality that goes from the highest qualities (“flower”, “extra”, and “superior”) to lower qualities (from “first” up to “sixth”).