Industry 4.0 design project based on exposure situations: A case study in aeronautics
Abstract
BACKGROUND:
Industry 4.0 generates risks renewing stakes for design projects integrating work activities, as can be done in activity centred ergonomics and participatory ergonomics.
OBJECTIVE:
This article aims to show the contribution of using typical situations to define requirements for Industry 4.0 design projects from a case study supporting a design project for a plant of the future assembling additive metal manufacturing processes (SLM type) in aeronautics.
METHOD:
The method is based on construction of the approach, the identification of typical exposure or action situations (through video and measurement) on four different company sites, three collective confrontation interviews (using typical situations) similar to reflexive and constructive simulations, and the setting of requirements.
RESULTS:
Results highlights specific exposure situations during the work, which the collective confrontation interviews made it possible to understand, enabling to collectively debate organisational, technical or social determinants, in order to define requirements from the point of view of the work, within the framework of the design project.
CONCLUSION:
Discussion of exposure situation allows an initial framework to discuss way to implement the work differently as a first step to transform the current situations during the design process. The observation of the possible use of requirements in project management can then be carried out. This exploratory work makes it possible to observe the contribution of the use of typical exposure situations as a complement to typical action situations in order to specify exposure situations and identify transformation perspectives.
1Introduction
The Industry of the future induces automation and digitalization of the means of production, leading inexorably to radical transformations of human work. In this context, workers are going to be exposed to emerging hazards. For instance, in the framework of metal additive manufacturing production, unprecedented innovation related to micro and nanotechnologies, workers are exposed to micro and nanoparticles with known health effects such as cancer [1]. These technological and societal innovations bring new challenges to which ergonomics can provide answers.
Today, some safe by design and prevention approaches seek to make innovations (such as those related to nanotechnologies) safer by focusing mostly on the technical dimensions. This technocentric approach are mainly focused on technical and expensive solutions where the actual work and associated potential exposures are sufficiently not taken into account. This approach doesn’t provide an appropriate answer to workers’ real needs [2]. In this context, it seems important to develop an activity-centred ergonomics approach to contribute to better consideration of work activities in design projects. So, the challenge is to promote safe working conditions by taking action as early as possible in the design stages of projects, which will lead to decisions that integrate health issues.
Thus, Industry 4.0 and societal circumstances reshape design projects and the opportunity to strengthen worker participation. Previous seminal works have begun to highlight these links [3]. However, it appears as if Industry 4.0 stays driven by technological innovation in practice and during its deployment, limiting anthropocentric design [4]. An interest of the work presented here is to foster the reflection on how to make participatory design projects and safer Industry 4.0 by integrating real work.
The preliminary results of this article are based on an Industry of the future design project in aeronautics. This design project of the company aims at gathering metal additive manufacturing production equipment in a single plant to print aircraft engine parts in 3D. Worker interventions on these processes lead to potential exposures to micro and nanoparticles. The theoretical framework used in this article is founded on the work carried out over the last 30 years in design ergonomics, to take into account real work situations (typical action/exposure situations and settings of usage) in order to define requirements for design projects [5–10]. More precisely, typical action situation (TAS) is turned in typical exposure situation (TES) to describe how this analysis unit of exposing work activities can help to develop prevention. In this way, the method developed in this article is based on the knowledge of activity-centred ergonomics [11, 12] and ergotoxicology [8, 13, 14] in particular. It seems important to recall that ergotoxicology is deeply embedded in ergonomics by the theories and methods mobilised, by being more specifically focused on exposure situations. In this light, this project and the practice of ergotoxicology are based on multidisciplinary approaches (e.g. ergonomics, metrology, prevention, occupational medicine and industrial hygiene).
The objective of this article is to present a case study on the support of the design project of a metal additive manufacturing Industry 4.0 based on the identification of typical exposure situations in order to set up requirements for Industry 4.0 design projects.
2Theoretical framework
2.1Use of typical action situation in design projects
The literature review carried out is based on work in activity ergonomics, highlighting work analysis units for design. The sources consulted were scientific articles, books and thesis in ergonomics, starting in 1987. The scientific journals Applied Ergonomics, Work, Activités, PISTES, Theoretical Issues in Ergonomics Science, Ergonomics, International Journal of Industrial Ergonomics, International Journal of Occupational Safety and Ergonomics, were consulted with the keywords “typical action situation setting usage reference”. 2631 documents were identified across the bibliographic resources. After a selection, 10 references were retained for an in-depth analysis. More precisely, the cumulative selection criteria were: ergonomics study presenting work activity analysis for design, theoretical or methodological or empirical article building new knowledges or underpinning previous observations, proposed definition of TASs and presentation of their use.
The objective of this literature review was to use these findings to mobilise the typical situations in the context of design projects for the Industry of the future with the potential presence of exposing work situations.
This work on design is part of participatory ergonomics [15–19]. The intervention of the ergonomist in the design thus questions the co-constructed methodology, as well as the spaces [20], the key players and the forms of objects mobilised to support this process.
About the design, Béguin [21] notes that “on the one hand, it is impossible to completely anticipate the work activity: it is therefore necessary to leave the worker the possibility of adapting to the circumstances, and even give him the possibility of finishing the design. But on the other hand, anticipation is a resource". It is with this in mind that the use of TASs has developed in the accompaniment of design projects in ergonomics in order to “foresee the space of possible forms of future activity” [5, 22].
2.1.1Typical action situations (TASs): What is that?
The literature review shows that TASs are commonly defined [5, 6, 22–25] by: the tasks to be carried out; the associated criteria and constraints related to the achievement of these objectives; the workers involved; the sources of information, means and tools needed; the internal or external factors that may influence the achievement of these objectives.
These TASs, based on a global understanding of current work, should help to develop requirements for those involved in design projects [5, 7]. These authors point out that the requirements determined may be technical, organisational or human [26]. In this way, the consideration of TASs is a way of overcoming technical criteria that are far removed from the needs of the work. For other authors, the TASs help to identify operators’ strategies and the future skills needed by future operators [27]. In all these cases, the analysis of the TASs helps to identify critical points (variabilities, etc.), as well as the corresponding room of manoeuvre needed by operators [7, 22, 28].
2.1.2How to characterise typical action situations (TASs)?
For Daniellou [22], reference situations will be identified in contexts that are close to the future work to be designed. Based on these reference situations, TASs will be described. The set of TASs specified forms a library of TASs that will support the design project [29].
These TASs are identified in similar work situations and specified collectively based on the knowledge of the actors encountered in the work environments. Usual ergonomics methods are used: interviews and observations during visits with workers and management to identify problematic work situations in relation to working conditions or their effectiveness. In-depth analyses of these situations, including typical actions to develop TASs, can be carried out in order to specify the structuring of these activities and their determinants, as well as the way in which the operators organise these activities.
Garrigou [23] illustrates the approach with the following example:
1) In a working group, ergonomists introduce the context by offering descriptions of the current situation.
2) Then the TASs are returned. The working group clarifies, specifies and develops new TASs based on the ergonomist’s questions. These TASs are gradually developed with the involvement of operators and designers. Ergonomists can identify TASs before the company’s players help to specify them.
3) These TASs are then projected by reconstructing the future action by following a temporal sequence and identifying the constraints and resources that appear (e.g. information processing, collaboration modalities, physiological strain).
2.1.3What uses of typical action situations (TASs) in ergonomics?
These TASs feed into the design projects to enrich and clarify requirements at the beginning of the projects. The TASs can follow each other over time or run in parallel. Then, the TASs are assembled into scenarii used to support the simulation of future work [7, 22, 23, 30]. Furthermore, the use of the TASs (during a simulation, in a working group, from a library of TASs, etc.) will contribute to the construction of requirements integrated by the designers. These requirements can be “descriptive” by formulating needs based on the TASs and the variabilities highlighted, “prescriptive” when they are based on recognised knowledge (anthropometry, toxicology [28]...), or “procedural” when they relate to the method to be followed (stages, key players and tools to be mobilised during the design process) [22].
Among the variabilities described by the TASs, chemical exposure is rarely discussed. Attention is drawn to the importance of taking into account the potential presence of dust [28], or exposures from truck exhaust fumes [5], such as health and safety issues discussed in working groups [23].
2.2From the typical action situation (TAS) to the typical exposure situation (TES): definition and use of typical exposure situations (TESs) for prevention-integrated design projects
TESs are defined by the work activities performed, the nature of the exposures and their determinants. The objective is to make visible the TASs leading to exposing work activities.
To formalize TESs, work activities can be described through operating modes, logic of action, temporal continuity and occurrence, event and incident, normal or degraded mode, information sought (formal and informal), contacts and contamination (direct and indirect), respiratory track distance, physical strain, resources and constraints during the activity. The determinants can be for their part characterised through the following dimensions [8]:
- Organizational: objective (task to be done), temporal frame, work organisation, collaborations, standard, regulation and procedure, variabilities (seasonality, team, production planning, ...).
- Human: representations, beliefs and fears, knowledges, perceptions (smells, sensation, ...), know how, training, skills and career path, work commitment, social patterns, variabilities (inter and intra individual).
- Technical: products (manufactured or unintentionally produced), devices used (tools, equipments and technologies), protective equipment, workplace characteristics, atmospheric conditions, industrial variabilities (raw material, ...).
The notion of TAS makes a definite contribution in the context of projects aimed at developing future work situations. In the framework of exposure to chemical products, the TASs appear to be a unit of analysis [21] appropriate for both understanding exposure and establishing requirements for the transformation of current work situations. One of the particularities of the TASs that can be defined with several levels of detail [24] is a resource for finding a suitable scale for the analysis of exposure situations.
In this context, several contributions of ergotoxicology to formalise the TESs should be highlighted:
- Knowledge related to exposure conditions, exposing activities and activity determinants is generated by the ergotoxicology method.
- TESs are potentially more complex to establish than TASs because the conditions of exposure of workers to hazardous substances are sometimes enigmas [31].
- The specification of TESs in comparison to TASs involves both objective (exposure, work demands, etc.) and subjective (representation, etc.) measures.
One particularity between TESs and TASs is that TESs can be applied to current situations instead of future situations, thus partly reducing the paradox of design ergonomics which seeks to transpose partly unique current situations into the future. In this case, we will characterise exposure situations and their determinants when implementing the following method, in the form of TESs, as a unit of analysis of exposing activities.
3Design method developed and implemented in the aeronautic industry
The research was carried out in an aeronautics company as part of a project to design a 10,000 m2 site comprising 50 Sintering Laser Melting (SLM) type metal additive manufacturing machines. The company’s objective is to gather and mutualize the group’s production means spread over five sites in France (15 machines in operation).
The company’s request initially focused on the understanding of exposure situations on a metal additive manufacturing pilot workstation to develop prevention strategy. In the course of the action research, it appeared that the results could make it possible to define preventive actions for similar workstations in other factories of the group as well as within the framework of a project for the design of a 4.0 plant integrating means of production for metal additive manufacturing.
The method implemented in the company relies on participative ergonomics approaches [15, 16, 32] applied to 4.0 design projects.
Figure 1 describes the three steps implemented in the company:
Fig. 1
Method implemented in an aeronautics company to design a metal additive manufacturing plant using typical exposure situations (TESs).
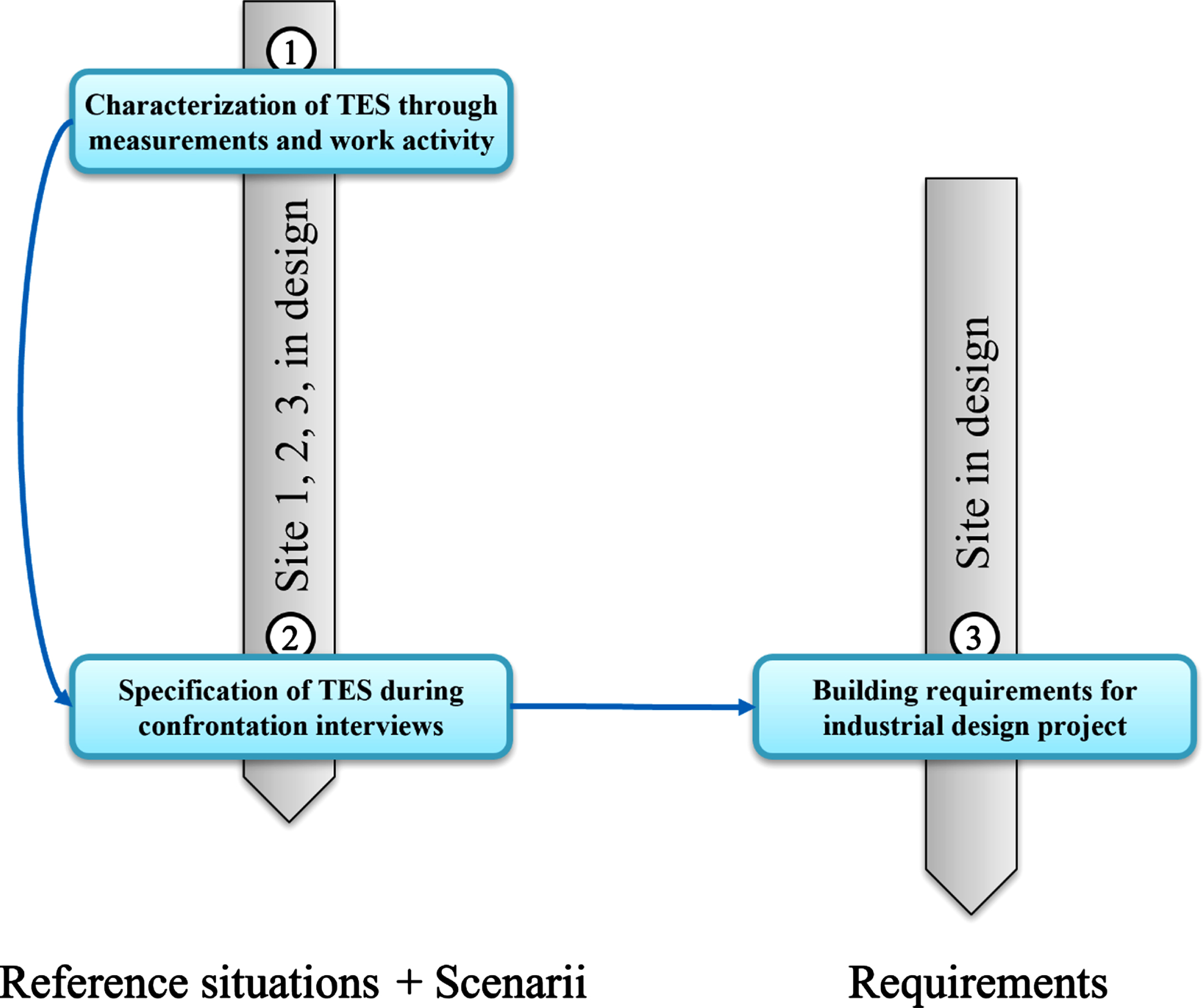
1- After construction of the approach [14] with the company’s stakeholders, reference situations were analysed at four of the group’s sites.
Reference situations (site 1), one with a SLM type machine EOS M280 and another with a SLM280, were analysed with the use of videos of the work activity and real time aerosol exposure measurement [33, 34] during the stages of human work on the additive manufacturing machine. The duration of these work activity observations and exposure measurement was 8 h, involving 2 workers.
Complementary reference situations (site 2, 3 and site in design) made it possible to identify similar potentially exposing actions on additive manufacturing machines of the same manufacturer and process (EOS M290) based on observations. The duration of these work activity observations was 21 h, involving 6 workers.
A detailed presentation of the exposure measurement method is available [34]. The synchronization of real-time aerosol measurements with videos of the work activity [35] allowed the identification of several TESs [8]. Variations in exposure could be associated with the workers’ actions.
2- Then, collective confrontation interviews were conducted with the management (2h09 min), the health and safety committee (1 h), and the workers (1h46 min) of the site 1. These interviews consisted in presenting to company stakeholders excerpts describing TESs based on videos of the work activity and exposure measurements.
All interviews were recorded and transcribed. The analysis of the interview data focused on the verbatims dealing with the specification of TESs, and the nature of the resulting design requirements. The excerpted sections from interviews presented in this article have been translated from French to English.
3- Building and transfer of design requirements into the design project of the new company site are constructed. A presentation of TESs specified has been done with the project team designing the new factory. While a part of confrontation interviews was focused on the understanding of exposure situations, another part was similar to “reflexive and constructive” simulations [36].
The aim of these simulations was also to collectively build design requirements for the choice of future machines and the organization of future work situations. In other words, this step contributes to the genesis of the development of requirements.
4Results
4.1Characterisation of TESs through measurement and work activity
TESs have been identified within these reference situations and among the TASs. These situations are detailed in Table 1 according to the TASs observed.
Table 1
Typical action situations (TASs) and typical exposure situations (TESs) identified in the reference situations
Category of TASs | TASs | TESs |
Powder sieving | Sieving of metal powder | Sifts powders |
Machine preparation | Entering settings at the control station | |
Adjusting and checking on the condition of the fusion chamber components | ||
Machine loading | Loading the tray | |
Powder loading | Transfers powders manually | |
Supervision | Supervising the operation of the machine | |
Unloading and cleaning machine | Powder recycling | Recovers powders from the printer |
Vacuuming of waste | ||
Manually recovering of powders | Collects powders in a bucket | |
Removing the part tray | ||
Cleaning part/tray | Cleaning of the part tray assembly | Uses a blower to remove powders |
The main TESs identified in this aerospace company occur when the operator recovers powders from the printer by dropping them through an opening inside the printer, collects powders from the powder pots into a bucket, sifts the powders by opening a window to observe the sieving, and manually transfers the sieved powders into the machine’s main tank to reload the machine, uses a blower to remove residual powders under a fume hood (see Fig. 2).
Fig. 2
Typical exposure situations identified during metal additive manufacturing operations.
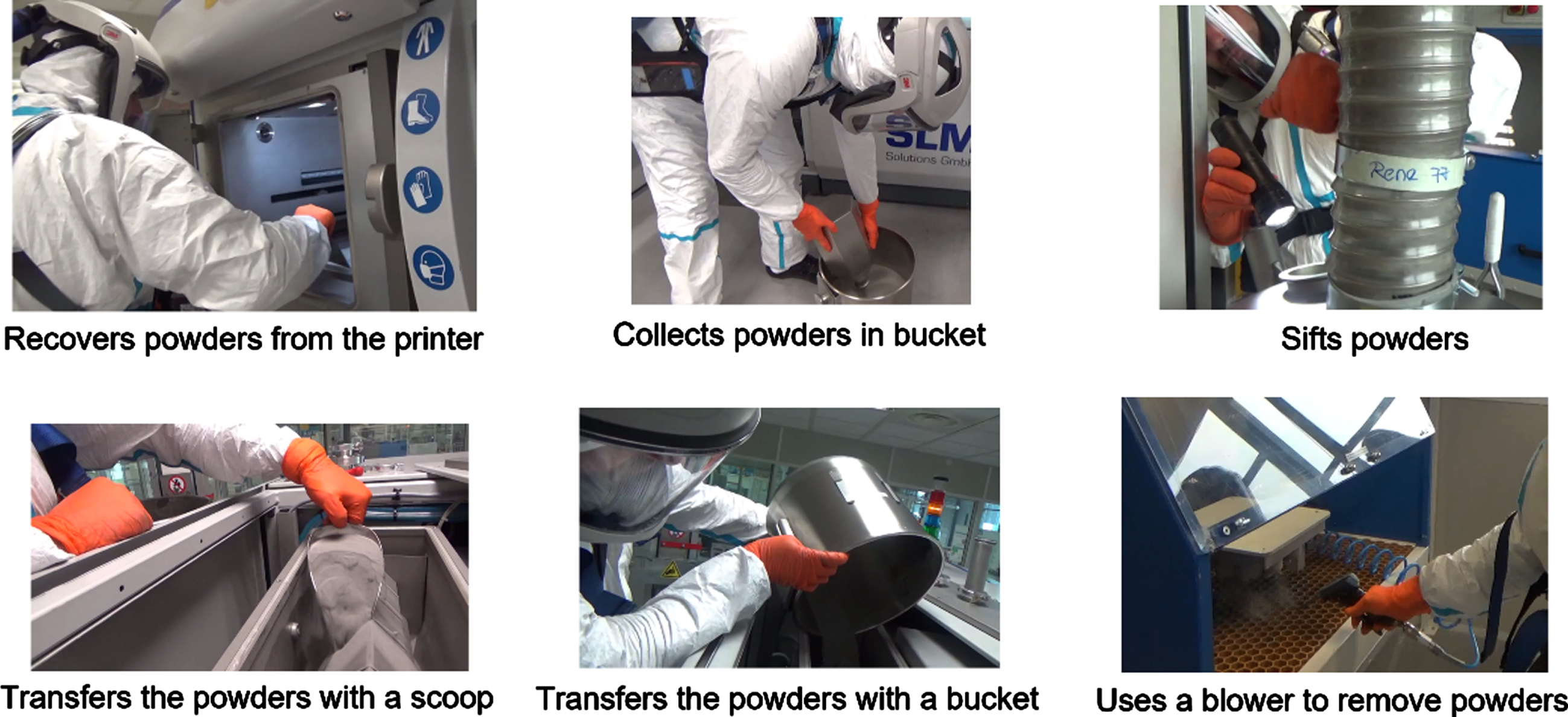
Similar situations have been identified in other work contexts as highlighted by a recent literature review [37].
4.2Specification of TES during confrontation interviews
Confrontation interviews based on these TESs helped to understand several determinants of these exposure situations. These determinants are notably associated with the choice of machines and their techno-centric design, the organization of work, and the perceptions and representations of risks by operators leading to exposing work activities.
Worker: [...] To make the piece to be produced from A to Z, but how long will it take? I don’t know. |
Researcher: Yeah, because today it’s not the case. |
Worker: For the moment it’s a cleaning lady... That’s how we feel But there will always be that powder thing that will hold it back. |
Researcher: Yes? You think... |
Worker: Yeah yeah yeah. That coverall is scary. We were again talking about it with the guys this morning. Because they know that at some point they’re going to take me off. So they’re all asking themselves the question: “Who’s going to go, who’s going to go? And this morning, they said: “this bloody powder". |
[...] |
Yeah, then be careful: I think. Be careful, as I told you, I realized that since July, I’ve been there once, I don’t have them [chapping]. So ... This winter, I didn’t worry, for me, it was the cold ... Then come June, July ... Some chapping ... Then it hurt! It was open, just a little bit like this, there. And the same thing, the next day I wake up, chapping from ... from there to there! |
The confrontation interview with the operators allows understanding of the operating mode chosen by another operator in order to save time when reloading the machine, resulting in the TESs “transfers the powders with a scoop” and “transfers the powders with a bucket". Removing the printer cover allows 90 kg of powder to be reloaded directly instead of reloading from 10 kg sealed pots. This advice on the operating procedure leading to these TESs was exchanged with the manufacturer of the additive manufacturing machine (SLM 280HL).
Researcher: This is how it loads. |
Worker: Because he doesn’t put 10 kg by 10 kg, he fills it up. Because the capacity of the thing must be at least 30 or 40 kg. Oh no, he shovels even like that. He dismantles the plate where the canister [pot] is supposed to be hung and he fills it directly. Ah well, on the one hand it’s not stupid. In this way, he doesn’t kill himself because he uses the trolley to... So no, that’s fine. No, I think it’s not bad to do it like that. He did it in one go. I do the same to load mine, I don’t know if you remember, except that we’re not high up. |
Researcher: Can there be no exposure for you there? |
Worker: Yes, of course, automatically, as the powder falls, it makes a little cloud, but then it’s gone. You have to see the particles and then you can tell us. Because for me, the particles don’t contaminate the face, but the fine particles I don’t know how they behave. That’s exactly where it would be interesting to know. It’s good to do it like that, I think it’s the easiest way. In any case, I would do it like that. In terms of posture, he’s not too bad, he doesn’t hurt himself when he’s carrying loads. If I had to load 90 kg I think I’d do it like that too. |
All the data collected (interviews, measurements and observations) allow us to specify the TESs. An example is detailed in Fig. 3, where the operator transfers the powders with a scoop. The work activity is described in the centre of the figure, supplemented by technical, human and organisational determinants.
Fig. 3
Formalisation of a specified typical exposure situation when a worker transfers the powders with a scoop.
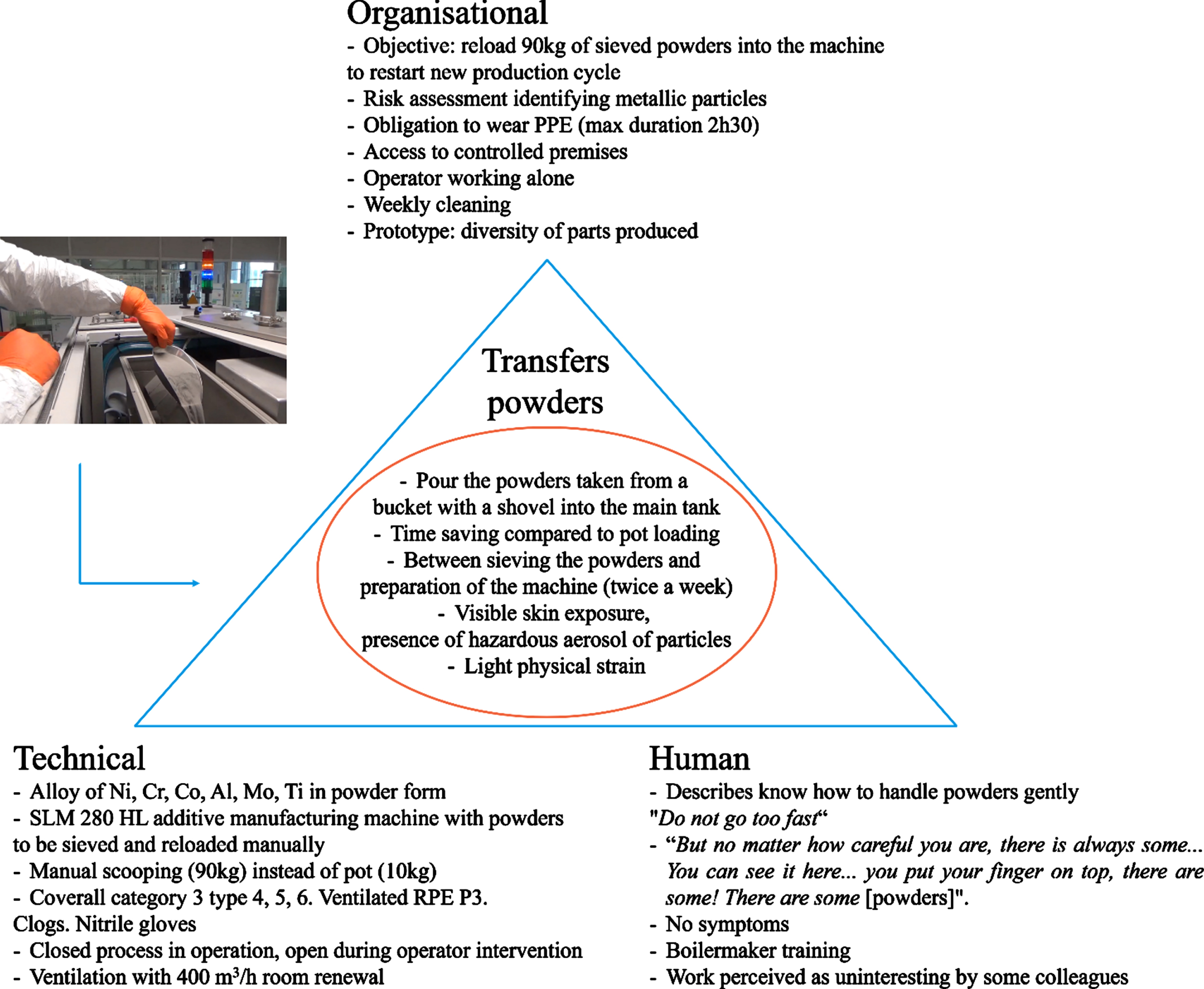
4.3Design requirements
At this stage of the design project, several requirements for the future plant have been collaboratively constructed during these collective confrontation interviews, as illustrated by these verbatim statements by the initial site risk prevention officer.
The risk prevention officer explains the choice to replace the serial additive manufacturing machine with a machine with an option to automate the sieving of powders in order to control an exposure situation.
“Then it’s the that will change, with more capacity, I think. From memory, from memory, we were told that there would be an automatic sifting... But from memory we will have more, when we reload, we won’t have to compact the powder as we used to do.” |
Then, the exposure situations presented are highlighted as having to be carried out with the recommended PPE. This transmission of requirements through rules and practices to be implemented in the design project for new work situations based on the understanding of exposure situations is part of a process of developing occupational safety.
Group toxicology manager: Ah well, you can’t put the tap in the room, that’s it... |
Risk prevention officer site 4: So, a washbasin outside A computer inside and a computer... We thought of a computer outside as well to manage, to avoid going inside all the time... |
Risk prevention officer site 1: PPE outside, that’s clear... . There’s dressing and undressing... |
Risk prevention officer site 4: Yeah, well, the correct practice says that you have to dress in the exposure phases during... but it’s not described [precisely when]. |
This interview with the management is a space for discussion on the safety practices developed by the company’s stakeholders to control the risk linked to the new additive manufacturing process in the context of the factory of the future. The presentation of results, supported by intermediate objects describing the identified exposure situations, becomes a support for the construction of prevention, both for the site 1 of the company and at a more global level, through the transfer of design requirements.
A final type of prevention requirement developed concerns the transformation of current situations by their design based on the material available in site 1 of the company, which served as a reference situation.
Company ergonomist: No, but it’s mainly that manufacturers today offer the solution... they free themselves from this kind of activity... |
Group toxicology manager: Of course, of course, but today you have... you have the equipment today. |
Risk prevention officer site 1: So it’s that [prototype operator] does his little operations, we can see that despite everything... Well, you are more exposed because of the design of the machine [...]. |
Regarding the lack of interest in these activities, several development perspectives are discussed during the interviews:
Quality Manager: They do the cleaning, they do the cleaning and they do the handling, all in suits. |
Group toxicology manager: Oh yeah, right. |
Quality Manager: The future is to automate, it’s not, the process... |
Company HSE Manager: You won’t find many people telling you that it’s interesting today [...]. |
Researcher: Oh no, but it’s out there, at each interview and the person who remains [a series additive manufacturing worker], he also has the question of being able to increase his skills, he has visions of progressing on the... the management of this type of position... |
Risk prevention officer site 1: So, after [additive manufacturing project manager], who is the project manager on this line of the future, it won’t be a 100% robotic line, it will be a line where we have additive manufacturing, a line where we have a wire cutting machine next to it, a line where we have a MMT which will probe, etc., a line where we have... and a machine where we have a grinding machine to rectify the trays. So the operator will have his... his own U-shaped line where he will intervene, he will not just be cleaning his additive manufacturing machine... |
In summary, these requirements concern the choice of additive manufacturing machines to automate stages of the work activity leading to exposure; the separation of production areas; or the involvement of operators in the design of the plant and in training courses for this new profession, as well as organizational matters in relation to work. The installation of sensors in the future plant to monitor in real time variations in particle concentrations has also been discussed.
The project in progress does not yet allow observation of the final impact on the work of the integration of the design requirements into the overall plant construction project. However, we observe that the exposure situations were made visible and the development of associated requirements have been transferred from the reference situations to the management team of the new plant design project. More generally, we note that the Industry of the future will lead to the disappearance of certain machining trades (turners, millers) and the appearance of new trades (additive manufacturing technician).
5Discussion
The theoretical and methodological lessons of this action research for design ergonomics can be summarised in several points. First, it is necessary to start from existing work situations in order to define typical situations. By making these situations and their determinants visible through exchanges with operators, it becomes possible to specify these typical situations. This process is based on a confrontation with real exposure situations. Then, reflexive practices (simulations, confrontation interviews, debate spaces, etc.) are the basis for understanding exposure situations, the comparison of situations, the projection of the work activity, and design choices. The temporal dimensions are mobilised by these approaches [38]. The discussion of current situations reveals past work situations, perceived exposures, and their determinants, influencing current situations and future projections according to the subjects. Prospects for re-constituting past situations appear. Following this, a projection into future work activity is promoted, based on the characteristics of the project and the nature of current work activities. The future activity is mainly based on the discussions of the transformation of current determinants and associated design choices. Finally, it will be necessary to accompany the work of the designers, the implementation by the project management, the start and the design in the use of these work situations whose determinants may still be brought to evolve (see Fig. 4). The transformation of determinants is symbolised by the mathematical symbol of the derivative in Fig. 4.
Fig. 4
Process of designing prevention or new work situations.
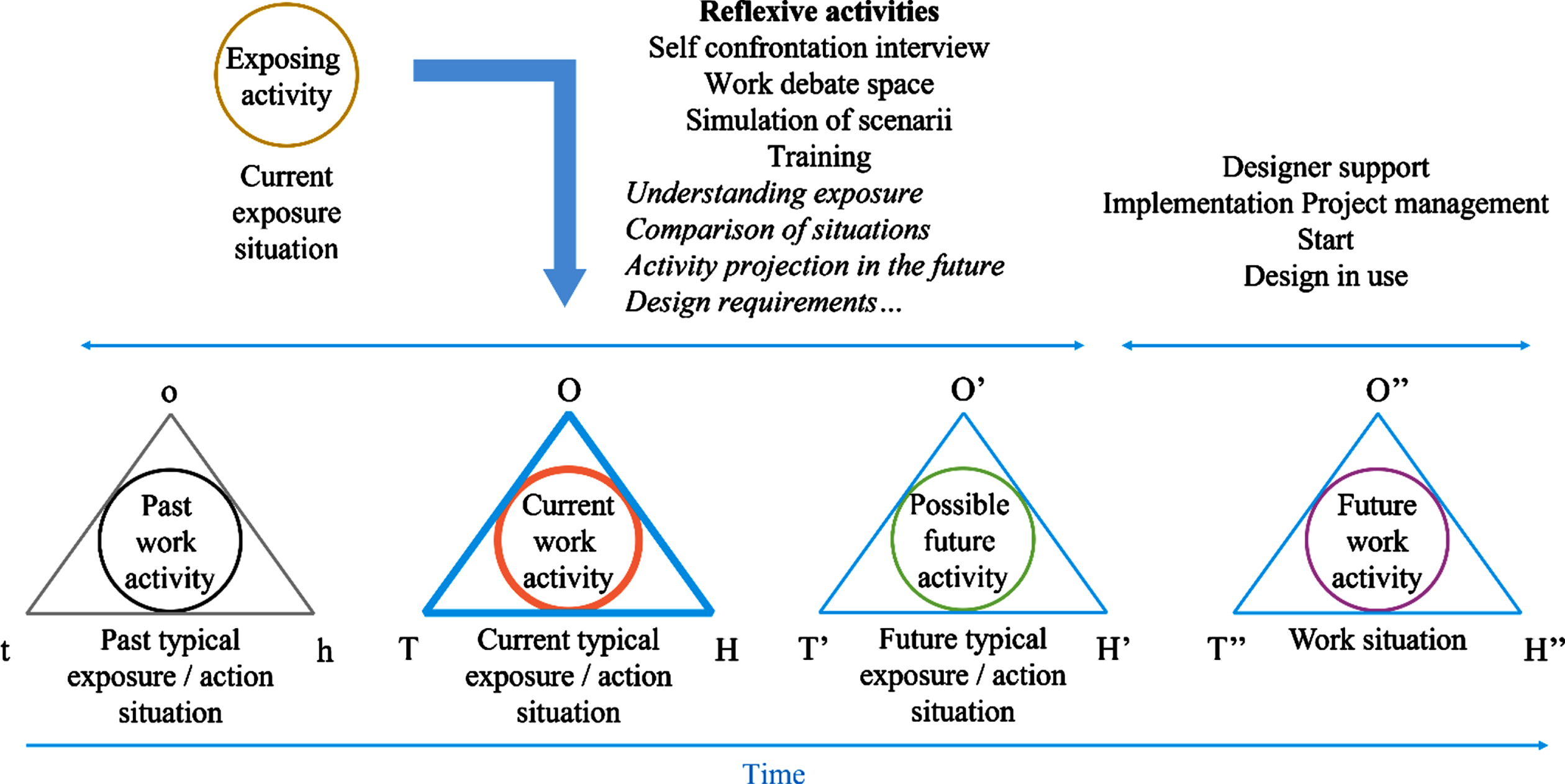
This kind of methodology is also the occasion to identify the determinants which are designed by remote stakeholders of the work situation. It is also a way to anticipate the actions to be taken by these actors. Indeed, the understanding of all the determinants involved in the situations of exposure to chemical substances is essential in order to consider more global transformations of work situations. Moreover, these transformations must be addressed with all the actors concerned by work situations, including those who are spatially and temporally distant from these.
This contribution is based on the proposals of precursors concerning the conduct of design projects in ergonomics [5, 7] and applies the foundations of participatory approaches as the nine dimensions of the participatory ergonomics framework [15].
The transformations brought about by Industry 4.0 have consequences on both the work of operators and the nature of the work of ergonomists. In addition to exploring the how and the why [39], it seems that Industry 4.0 is an opportunity to question the where and the when of work activities.
5.1Limitations
This notion of typical situation raises a question: when does a situation become typical? The literature does not address this point much. According to the original understanding of the TASs, the term “typical” implies that the situation: is reproduced several times with certain common characteristics allowing a generalization [29], retains characteristics that are transferable when applied to a new system [22], allows an abstraction of the parameters of this situation [5], and results from a typical action [23]. With regard to chemical exposures, situations can be considered typical when they occur or are likely to occur, exceptionally or regularly, and can be identified by measurement or observation. The use of the term “typical” in this literature is also conditioned by the addition of circumstantial information on the context of the action. Thus, the mere description of an action by reference to the operating mode is not sufficient to make it a typical situation.
Limitation of this work is that it relies on the qualitative approach, implying a small sample. In order to reinforce consideration of real work, new work observations in diversified reference situations, as well as simulations with the design project stakeholders, should be carried out. Due to the potentially rapid evolution of metal additive manufacturing processes, it is important to consider the models observed in this study.
On the other hand, this work makes it possible to better define the typical situations on the basis of previous work and to develop the use of TESs when occupational exposures occur, complementing TASs.
5.2Perspectives
With regard to TESs, their use could be appropriate to characterise all the work situations that may expose workers to various hazards during their work activities in order to take preventive or design action. Various types of hazards could then be considered: exposure to toxic products, electromagnetic radiation, noise, awkward postures or physically intense activity [8], shift work, accidental situations, psychological strain, impossibility to act, loss of meaning of work for example. In addition, understanding the complexity of workplace exposures and their determinants is a step toward describing an occupational exposome [40–42].
In this case, the use of these situations can serve as a development of the activity by taking into account the diachronic or historical-cultural dimensions of the activity. These spaces of development of the activity could be defined in intermediate spaces of prevention [14] or by seeking to investigate controversies about the quality of work, for example [43]. What these methods have in common is that they draw on the real work activity to build resources to contribute to the development of safe and sustainable work activities.
In this sense, when specifying the TESs, it seems important to describe the resources in addition to the determinants of these situations in order to make them visible to the project actors.
In addition, the development of prevention project management using TESs is a way of taking work activities into account. TESs could help to develop homogeneous exposure groups, which are frequently used in chemical risk prevention approaches in particular [44, 45] or more globally [46].
One perspective of this work is to deepen the understanding of the elaboration of the TESs and their formalisation and integration into the design projects. It remains to be understood how the prevention requirements developed during the interviews, which are similar to simulations, are actually formalised into choices integrated into the specifications and implementation of design projects.
The use of TESs is also an opportunity to promote the articulation between technocentric and anthropocentric approaches so that the solutions proposed during design projects are both in line with technical requirements and the real needs of workers. At this level, the design of work situations should be seen as an opportunity to take account of the real activity of workers, by integrating the possibilities of developing this activity. Taking this activity into account must involve the mobilisation of inventiveness and creativity in a participatory logic [47]. In this context, simulations with (and without) exposure measurements in new work situations could be carried out.
6Conclusion
This study shows the challenge of pursuing a better integration of real work in the Industry of the future design projects. Indeed, risk situations that did not exist before the advent of the industry 4.0 may be generated, requiring discussion and mobilization of specific stakeholders in design projects. However, the automation and real-time monitoring of work environment characteristics opens new perspectives for the development of favourable working conditions. A better consideration of real work can therefore be achieved using new exposure characterization techniques, without forgetting to systematically involve stakeholders with knowledge of real work in the project.
The challenge is to make the work situations involving exposing activities visible, their determinants and their resources. The work on the development of the notion of TES constitutes a contribution to understanding exposures and designing new work situations without exposure. Including these TESs should form the basis for the development of future safe work situations where exposures are controlled. In addition to supporting design processes, the underlying issues of these methods are those of developing work activities and safe work. This action research, which will be complemented by other work in progress, is a step towards a global representation of the design process of Industries 4.0, in which design choices can contribute to generating or acting on causes of occupational risks.
Conflict of interest
The authors declare that they have no conflict of interest.
Acknowledgments
The authors would like to thank the workers and the company involved in this study.
Funding
The research leading to these results has received funding from the Aquitaine Region (grant number 2015-1R30504), the ANSES (grant number PNR EST-2014/1/162), and the INRS.
References
[1] | CIRC. Arsenic, Metals, Fibres and Dusts. IARC Monographs on the Evaluation of Carcinogenic Risks to Humans, No. 100C. Lyon: International Agency for Research on Cancer; 2012. |
[2] | Rabardel P , Beguin P . Instrument mediated activity: From subject development to anthropocentric design. Theor Issues Ergon Sci. (2005) ;6: (5):429–61. |
[3] | Broday EE . Participatory Ergonomics in the context of Industry 4. A literature review. Theor Issues Ergon Sci. (2021) ;22: (2):237–50. |
[4] | Barcellini F . What designs for human-robot collaborative cooperation? An experience of participation in a collaborative robotics demonstrator design project. Activités [Internet]. 2020;17(1). Available from: http://journals.openedition.org/activites/5007 |
[5] | Garrigou A , Daniellou F , Carballeda G , Ruaud S . Activity analysis in participatory design and analysis of participatory design activity. Int J Ind Ergon. (1995) ;15: (5):311–27. |
[6] | Duarte F , Lima F . Anticipating activity through use configurations: Methodological proposal for project management. Activités [Internet]. (2012) ;09(2). Available from: https://activites.revues.org/314 |
[7] | Barcellini F , Van Belleghem L , Daniellou F . Design projects as opportunities for the development of activities. In: FalzonP, editor. Constructive Ergonomics [Internet]. CRC Press; (2014) , pp. 187–204. |
[8] | Galey L , Audignon S , Witschger O , Bau S , Judon N , Lacourt A , et al. What does ergonomics have to do with nanotechnologies? A case study. Appl Ergon [Internet]. (2020) ;87: (103116). Available from: https://www.sciencedirect.com/science/article/pii/S0003687018305647 |
[9] | Souza da Conceição CS , Broberg O , Duarte F . A six-step model to transform an ergonomic work analysis into design guidelines for engineering projects. Work. (2020) ;66: (3):699–710. |
[10] | Kadir BA , Broberg O . Human-centered design of work systems in the transition to industry 4.0. Appl Ergon. (2021) ;92: :103334. |
[11] | Daniellou F . The French-speaking ergonomists’ approach to work activity: Cross-influences of field intervention and conceptual models. Theor Issues Ergon Sci. (2005) ;6: (5):409–27. |
[12] | Daniellou F , Rabardel P . Activity-oriented approaches to ergonomics: Some traditions and communities. Theor Issues Ergon Sci. (2005) ;6: (5):353–7. |
[13] | Garrigou A , Baldi I , Le Frious P , Anselm R , Vallier M . Ergonomics contribution to chemical risks prevention: An ergotoxicological investigation of the effectiveness of coverall against plant pest risk in viticulture. Appl Ergon. (2011) ;42: (2):321–30. |
[14] | Judon N , Galey L , Saint Dizier de Almeida V , Garrigou A . Contributions of participatory ergonomics to the involvement of workers in chemical risk prevention projects. Work. (2019) ;64: (3):651–60. |
[15] | Haines H , Wilson JR , Vink P , Koningsveld E . Validating a framework for participatory ergonomics (the PEF). Ergonomics. (2002) ;45: (4):309–27. |
[16] | Morris W , Wilson JR , Koukoulaki T . Developing a participatory approach to the design ofwork equipment: Assimilating lessons from workers’ experience. TUTB. Belgium; (2004) . |
[17] | Broberg O , Andersen V , Seim R . Participatory ergonomics in design processes: The role of boundary objects. Appl Ergon. (2011) ;42: (3):464–72. |
[18] | Bolis I , Brunoro CM , Sznelwar LI . Work for sustainability: Case studies of Brazilian companies. Appl Ergon. (2016) ;57: :72–9. |
[19] | Paravizo E , Braatz D . Using a game engine for simulation in ergonomics analysis, design and education: An exploratory study. Appl Ergon. (2019) ;77: :22–8. |
[20] | Carroll JM . Five reasons for scenario-based design. Interact Comput. (2000) ;13: (1):43–60. |
[21] | Béguin P . Taking into account the work activity to design. Activités [Internet]. (2007) ;4: (2). Available from: https://journals.openedition.org/activites/1719 |
[22] | Daniellou F . Ergonomics in the conduct of work system design projects. In: [Ergonomics]. 1st ed. Presses Universitaires de France; (2004) , pp. 359-73. Available from: http://www.cairn.info/ergonomie–9782130514046-page-359.htm |
[23] | Garrigou A . The contributions of socio-cognitive orientation confrontations within participative design processes: The role of ergonomics. [Doctoral thesis]. Paris, Cnam; (1992) . |
[24] | Daniellou F . The status of practice and knowledge in ergonomic design intervention. [Habilitation to direct research]. Université Victor Segalen-Bordeaux 2-ISPED, Laboratoire d’ergonomie des systèmes complexes; (1992) . |
[25] | Daniellou F , Garrigou A . Human factors in design: Sociotechnics or ergonomics? In: Design For Manufacturability: A Systems Approach To Concurrent Engineering In Ergonomics. Taylor and Francis, London: NagamachiM. and HelanderM.; (1992) , pp. 55–63. |
[26] | Dutier J , Guennoc F , Escouteloup J . The ergonomist: A full design actor example of an ergonomic action. Procedia Manuf. (2015) ;3: :5830–7. |
[27] | Grosjean J , Neboit M . Ergonomics and prevention in the design of work situations. Hygiène Et Sécurité Du Travail. (2000) ;179: (ND 2127-179-00). |
[28] | Garrigou A , Thibault JF , Jackson M , Mascia F . Ergonomics contributions and approaches to design processes. Perspect Interdiscip Sur Trav Santé [Internet]. (2001) ;3: (2). Available from: https://pistes.revues.org/3725 |
[29] | Jeffroy F . Controlling the operation of a microcomputer system by non-computer users: Ergonomic analysis and cognitive process. [Doctoral thesis]. Paris 13; 1987. |
[30] | Maline J . Simulating work. ANACT. 1994. (Tools and methods). |
[31] | Teiger C . The ergonomic approach: From human work to the activity of men and women at work. Educ Perm. (1993) ;3: (116):27. |
[32] | Burgess-Limerick R . Participatory ergonomics: Evidence and implementation lessons. Appl Ergon. (2018) ;68: :289–93. |
[33] | CEN. pr EN 17058 - Workplace exposure - Assessment of inhalation exposure to nano-objects and their agglomerates and aggregates. CEN; 2018. |
[34] | Galey L , Audignon-Durand S , Brochard P , Debia M , Lacourt A , Lambert P , et al. Towards an operational exposure assessment strategy to airborne nanoparticles by integrating work activity analysis and exposure measurement. Arch Mal Prof Environ. (2020) ;81: (6):838–50. |
[35] | Rosén G , Andersson IM , Walsh PT , Clark RDR , Säämänen A , Heinonen K , et al. A review of video exposure monitoring as an occupational hygiene tool. Ann Occup Hyg. (2005) ;49: (3):201–17. |
[36] | Bobillier Chaumon MÉ , Rouat S , Laneyrie E , Cuvillier B . From activity OF simulation to activity IN simulation: Simulating to stimulate. Activités [Internet]. (2018) ;15: (1). Available from: https://journals.openedition.org/activites/3136 |
[37] | Leso V , Ercolano ML , Mazzotta I , Romano M , Cannavacciuolo F , Iavicoli I . Three-dimensional (3D) printing: Implications for risk assessment and management in occupational settings. Ann Work Expo Health [Internet]. (2021) ;(wxaa146). Available from: https://doi.org/10.1093/annweh/wxaa146 |
[38] | Chizallet M , Prost L , Barcellini F . Supporting the design activity of farmers in transition to agroecology: Towards an understanding. Trav Hum. (2020) ;83: (1):33–59. |
[39] | Béguin P , Duarte F , Sznelwar LI . Introduction to the special section on activity theory for work analysis and design. Production. (2015) ;25: (2):255–6. |
[40] | Faisandier L , Bonneterre V , De Gaudemaris R , Bicout DJ . Occupational exposome: A network-based approach for characterizing Occupational Health Problems. J Biomed Inform. (2011) ;44: (4):545–52. |
[41] | Tissier-Raffin M , Morin D , Galey L , Garrigou A . Making the right to a healthy environment effective: The scientific and legal challenges raised by the exposome concept. Rev Jurid Environ. (2020) ;(HS20):39–80. |
[42] | Roquelaure Y , Luce D , Descatha A , Bonvallot N , Porro B , Coutarel F . An organisational model of the occupational exposome. Médecine/Sciences. (2022) ;38: (3):288–93. |
[43] | Clot Y . Work and power to act. Presses Universitaires de France;. (2008) , p. 302. |
[44] | Rappaport SM , Kromhouta H , Symanski E . Variation of exposure between workers in homogeneous exposure groups. Am Ind Hyg Assoc J. (1993) ;54: (11):654–62. |
[45] | Mäkinen M , Kangas J , Kalliokoski P . Applicability of homogeneous exposure groups for exposure assessment in the chemical industry. Int Arch Occup Environ Health. (2000) ;73: (7):471–8. |
[46] | Miguez SA , Hallbeck MS , Vink P , Rodrigues PVC . Ergonomic risk and homogeneous exposure groups. Proc Hum Factors Ergon Soc Annu Meet. (2014) ;58: (1):1551–5. |
[47] | Abraçado MP , Duarte FJ de CM , Béguin PD , Fontainha TC , Oggioni BP , de Almeida WSS . Designing for unpredictable uses: A case study on cargo handling. Work. (2021) ;70: (3):861–73. |