3D print material study to reproduce the function of pig heart tissue
Abstract
BACKGROUND:
Three-dimensional (3D) printing technology for heart simulation can be represented as complex anatomical structures, and objective information can be provided.
OBJECTIVE:
We studied 3D print material to find a material with the same elastic coefficient as pig elastic coefficient.
METHODS:
Pig heart sample, Agilus sample, Tango sample, TPU sample, and silicone sample were studied. The elastic coefficient of each specimen was measured using an elastic coefficient measuring instrument. The analysis was performed using the average value of ten specimens of the same size. We suggested an equation to find the elastic coefficient of material by the thickness using the elastic coefficient of Agilus, Tango, and silicone.
RESULTS:
The sample with similar elasticity to the pig sample did not show the same coefficient of elasticity at the same sample size. In Tango, the 0.5 mm high elastic force was about 3 times higher than the pig sample 7 mm elastic force.
CONCLUSIONS:
The study was conducted using 3D print material and silicone which can reproduce the elasticity of pig heart. However, no material is currently available to reproduce pig heart sample of the same size. However, if the heart is developed considering only elasticity, it can be sufficiently reproduced using the research results.
1.Introduction
Three-dimensional (3D) printing technology is rapidly developing in various fields such as clothing, automobiles, military equipment, and medical [1]. As 3D printing technology develops, it is useful in the medical field because it can express complex anatomical structures [2, 3]. In general, when planning surgery, the anatomical structure of the heart is mainly identified through CT and MRI images. However, as the 3D printing technology was recently developed, the 3D printed heart model is used to help understand the heart structure [4]. The advantage of 3D printing is to make the object easily and quickly. As this advantage, 3D printing technology has been expanded in the medical field and related many studies have been conducted [5, 6]. The simulation, which is universal in the medical field is a necessary step before clinical to reduce risk and to improve results [7]. Existing simulation methods are quite limited, so expert skill is important [8]. But when combined with 3D printing technology, complex anatomical structures can be represented, and objective information can be provided [9, 10]. Therefore, surgical simulation using 3D printing technology is an essential procedure. Today, as 3D printing technology advances, it is possible to describe anatomically well when printing the heart. Cardiac printing has been useful for understanding anatomical structures until now, but the actual physical properties for surgery simulation of the heart were not considered [11]. 3D printers are manufactured using a variety of materials. Finding 3d print material such as the heart among the elastic materials can help to print similar model such as the real heart and simulate surgery.
The purpose of this study was to find a material with the same elastic coefficient as the heart. The pig heart was used standard reference and compared with the material of 3D print, and silicone which is a representative material that can express elasticity.
2.Materials and methods
2.1Heart material
IRB approval was not necessary because the heart was used after the pig dies. The pig heart was used a reference standard because it has characteristics very similar to the human heart anatomically and organizationally. The pig heart was carried within 6 hours with 4
2.23D print material
Agilus is a polyjet photopolymer that has excellent tear resistance and is resistant to repeated curve and bending. It is an elastic material suitable for simulating the elasticity of the heart. sample were produced using a Polyjet 3D printer (Object260 Connex, Stratasys, U.S.A). The white liquid resin is mixed with Agilus material to change the hardness. We built a sample using Agilus 100%, which best represents the elasticity.
Tango is a fabricated an elastic sample using a Polyjet 3D printer (J750DAP, Stratasys, U.S.A). 3D printer can adjust hardness by mixing up to 3 kinds of resins. We built a sample using Tango 100%, which best represents the elasticity.
TPU (Thermoplastic Polyurethane) is a kind of thermoplastic elastomer (TPE/Thermoplastic Elastomer), a plastic material with the elasticity of rubber. Elastic samples of TPU materials were produced using FDM 3D printers (CUBICON Single Plus, Cubicon, KOREA). The TPU can be made by adjusting the density in its own software, and we produced a 10% density TPU sample.
2.3Silicone material
Silicone compounds use RTV silicone, which is highly elastic and can create a variety of shapes. Samples were prepared by mixing with a curing agent at a ratio that provided the silicone of the RTV material. (20 (silicone): 1 (hardener) ratio used).
2.4Measure method
SH-500 is a force measuring instrument. SH-500 was used to measure the elastic force of cardiac samples, Agilus, Tango, TPU, and Silicone samples. The sample was fixed to jig and the length change was measured at 5 N.
In the results of measuring Pig sample from 0 to 23 N using SH-500, the elasticity test was performed by fixing 5 N, the largest change in length, as the experimental value. When measuring the elasticity, the degree of sample length increase was measured when the sample was fixed to the SH-500 jig and the force was applied to 5 N.
2.5Elastic experiment method
Pig samples were prepared with a width of 50 mm, a length of 20 mm, and a height of 5, 6, 7, 8, 9, 10, 11 mm. Elasticity tests were performed using a total of 80 samples, 10 for each height. Agilus samples were prepared with a width of 50 mm, a length of 20 mm, and a height of 0.5, 0.6, 0.7, 0.8, 0.9, 1, 2, 3, 4, 5, 6, 7 mm. Elasticity tests were performed using a total of 120 samples, 10 for each height. Tango samples were prepared with a width of 50 mm, a length of 20 mm, and a height of 0.5, 0.6, 0.7, 0.8, 0.9, 1, 2, 3, 4, 5, 6, 7 mm. Elasticity tests were performed using a total of 120 samples, 10 for each height. TPU samples were prepared with a width of 50 mm, a length of 20 mm, and a height of 0.5, 0.6, 0.7, 0.8, 0.9, 1, 2, 3, 4, 5, 6, 7 mm. Elasticity tests were performed using a total of 120 samples, 10 for each height. Silicone samples were prepared with a width of 50 mm, a length of 20 mm, and a height of 0.5, 0.6, 0.7, 0.8, 0.9, 1, 2, 3, 4, 5, 6, 7 mm. Elasticity tests were performed using a total of 120 samples, 10 for each height. Ten sample of the same height were produced and analyzed using the average value of the elastic results of the ten specimens.
(1)
As in Eq. (1), the external force is fixed at
2.6Analysis method
The elasticity test results of Agilus, Tango, TPU, and Silicone were compared using the measurement results of the heart elasticity test. The comparison compared ten average values of the same sample. Agilus height 0.5, 0.6, 0.7, 0.8, 0.9, 1, 2, 3, 4, 5, 6, 7 mm, Tango height 0.5, 0.6, 0.7, 0.8, 0.9, 1, 2, 3, 4, 5, 6, 7 mm, TPU height 0.5, 0.6, 0.7, 0.8, 0.9, 1, 2, 3, 4, 5, 6, 7 mm, Silicone height 1, 2, 3, 4, 5, 6, and 7 mm were found to be similar to the elasticity of the pig heart sample.
2.7Data fitting method
In order to know the linear relationship of the data, we used the “Pearson’s correlation coefficient” statistical method that represents the correlation coefficient. In addition, normality verification was performed to perform the Pearson correlation coefficient statistics. Elastic coefficient data showed a linear relationship. Coefficient of elastic coefficient according to thickness was derived using elastic coefficient data.
Table 1
Pig heart external force unit length change. As a result of comparing the four specimens and finding the external force with the highest change in length, the highest change in length was shown when an external force of 5 N was applied
Force (N) | 1 | 2 | 3 | 4 | ||||
---|---|---|---|---|---|---|---|---|
Length of sample | Length change | Length of sample | Length change | Length of sample | Length change | Length of sample | Length change | |
0 | 79.01 | 0 | 78.19 | 0 | 74.97 | 0 | 77.29 | 0 |
1 | 80.07 | 1.06 | 79.23 | 1.04 | 76.05 | 1.08 | 78.37 | 1.08 |
2 | 81.05 | 0.98 | 80.33 | 1.1 | 77.14 | 1.09 | 79.54 | 1.17 |
3 | 82.23 | 1.18 | 81.5 | 1.17 | 78.31 | 1.17 | 80.62 | 1.08 |
4 | 83.34 | 1.11 | 82.53 | 1.03 | 79.4 | 1.09 | 81.77 | 1.15 |
5 | 84.52 | 1.18 | 83.81 | 1.28 | 80.69 | 1.29 | 82.98 | 1.21 |
6 | 85.61 | 1.09 | 84.91 | 1.1 | 81.68 | 0.99 | 84.01 | 1.03 |
7 | 86.5 | 0.89 | 85.89 | 0.98 | 82.7 | 1.02 | 85 | 0.99 |
8 | 87.54 | 1.04 | 86.93 | 1.04 | 83.43 | 0.73 | 85.72 | 0.72 |
9 | 88.13 | 0.59 | 87.72 | 0.79 | 84.12 | 0.69 | 86.42 | 0.7 |
10 | 88.94 | 0.81 | 88.53 | 0.81 | 84.73 | 0.61 | 87.08 | 0.66 |
11 | 89.68 | 0.74 | 89.21 | 0.68 | 85.19 | 0.46 | 87.72 | 0.64 |
12 | 90.27 | 0.59 | 89.97 | 0.76 | 85.62 | 0.43 | 88.33 | 0.61 |
13 | 90.96 | 0.69 | 90.41 | 0.44 | 86.08 | 0.46 | 88.81 | 0.48 |
14 | 91.6 | 0.64 | 90.98 | 0.57 | 86.47 | 0.39 | 89.21 | 0.4 |
15 | 92.34 | 0.74 | 91.29 | 0.31 | 86.79 | 0.32 | 89.68 | 0.47 |
16 | 93.07 | 0.73 | 91.79 | 0.5 | 87.02 | 0.23 | 90.07 | 0.39 |
17 | 93.95 | 0.88 | 92.31 | 0.52 | 87.37 | 0.35 | 90.48 | 0.41 |
18 | 94.68 | 0.73 | 92.78 | 0.47 | 87.72 | 0.35 | 90.91 | 0.43 |
19 | 95.12 | 0.44 | 93.12 | 0.34 | 87.99 | 0.27 | 91.38 | 0.47 |
20 | 95.64 | 0.52 | 93.54 | 0.42 | 88.49 | 0.5 | 91.77 | 0.39 |
21 | 96.1 | 0.46 | 93.98 | 0.44 | 88.81 | 0.32 | 91.98 | 0.21 |
22 | 96.66 | 0.56 | 94.37 | 0.39 | 89.13 | 0.32 | 92.22 | 0.24 |
23 | 97.08 | 0.42 | 94.8 | 0.43 | 89.5 | 0.37 | 92.59 | 0.37 |
Table 2
Average values of 10 same sample of the pig, Agilus, Tango, and Silicone. The size of the sample was measured by changing the height with width 50 mm and length 20 mm
Sample height (mm) | Length change (mm) | Elastic coefficient (Mpa) |
---|---|---|
Pig | ||
11 | 5.71 | 0.1992 |
10 | 6.48 | 0.1933 |
9 | 7.3383 | 0.1895 |
8 | 8.7067 | 0.1796 |
7 | 10.8881 | 0.1646 |
5 | 16.33 | 0.1531 |
Agilus | ||
7 | 1.05 | 1.701 |
6 | 1.23 | 1.694 |
5 | 1.52 | 1.645 |
4 | 1.92 | 1.628 |
3 | 2.58 | 1.615 |
2 | 3.88 | 1.611 |
1 | 7.88 | 1.586 |
0.9 | 8.92 | 1.557 |
0.8 | 10.14 | 1.541 |
0.7 | 11.65 | 1.533 |
0.6 | 13.71 | 1.520 |
0.5 | 16.52 | 1.513 |
Tango | ||
7 | 1.71 | 1.0443 |
6 | 2.3 | 0.9058 |
5 | 3.07 | 0.8143 |
4 | 4.15 | 0.7530 |
3 | 6.76 | 0.6164 |
2 | 12.61 | 0.4956 |
1 | 26.81 | 0.4662 |
0.9 | 33.37 | 0.4162 |
0.8 | 38.6 | 0.4048 |
0.7 | 44.23 | 0.4037 |
0.6 | 51.66 | 0.4033 |
0.5 | 62.11 | 0.4025 |
Silicone | ||
7 | 1.37 | 1.303 |
6 | 1.65 | 1.263 |
5 | 2.43 | 1.029 |
4 | 3.29 | 0.950 |
3 | 4.92 | 0.847 |
2 | 7.63 | 0.819 |
1 | 15.41 | 0.811 |
0.9 | 17.19 | 0.808 |
0.8 | 19.35 | 0.807 |
0.7 | 22.2 | 0.804 |
0.6 | 25.97 | 0.802 |
0.5 | 31.26 | 0.800 |
Figure 1.
The sample of width 50 mm, length 20 mm and height 7 mm was made using the pig heart.
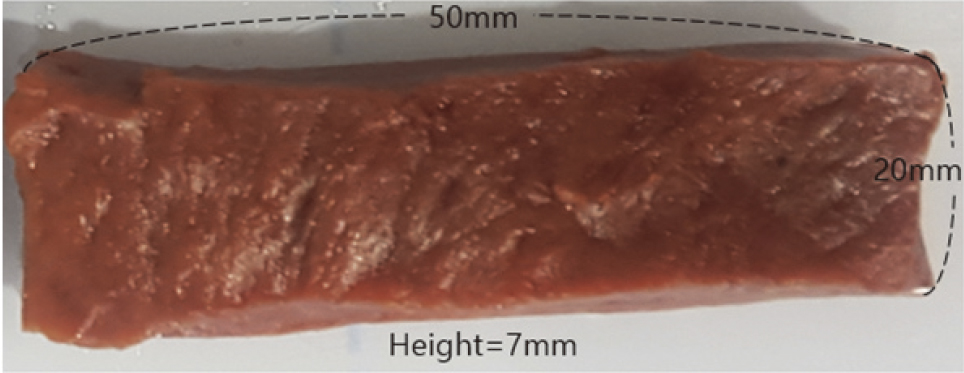
Figure 2.
Agilus, Tango, and TPU sample (A) Agilus sample are 50 mm wide, 20 mm long, and 7 mm height (B) Tango sample are 50 mm wide, 20 mm long, 7 mm height (C) TPU sample are 50 mm wide, 20 mm long, and height 7 mm.
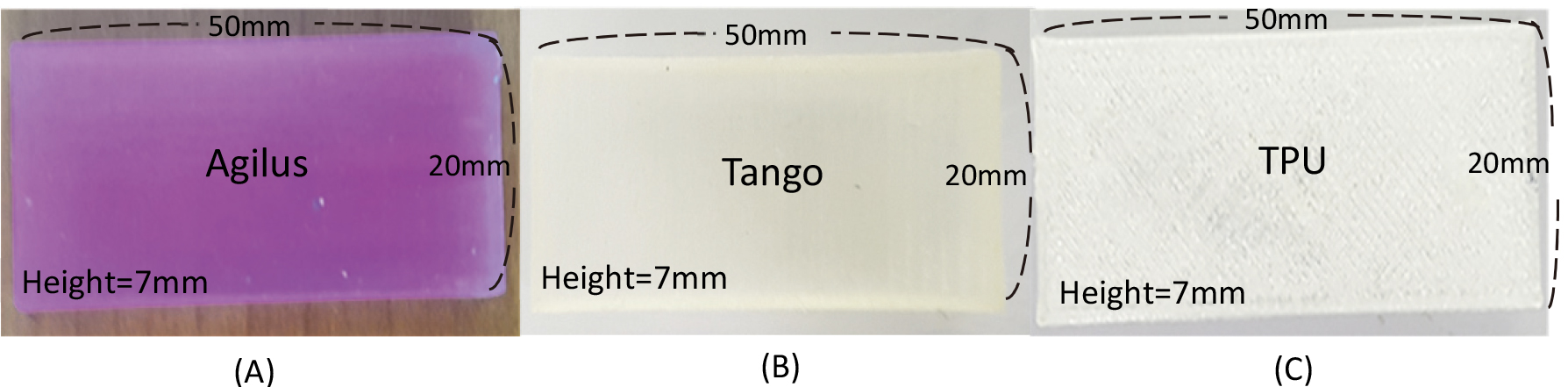
Figure 3.
Silicone Materials and Silicone Sample (A) RTV-2400 Silicone Materials (B) Hardener for Curing RTV-2400 Silicone Materials (C) Silicone Sample Width 50 mm, Height 20 mm, Height 7 mm.
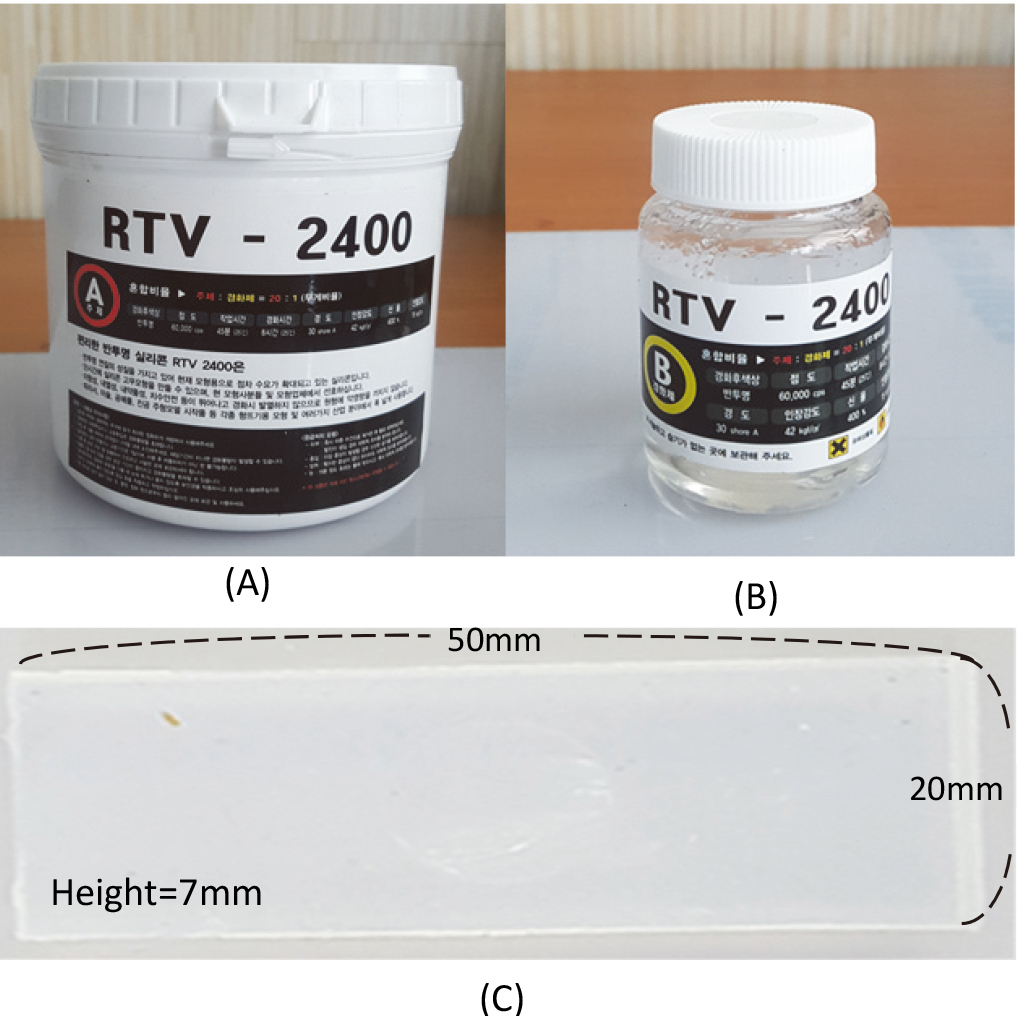
Figure 4.
It is a force measuring device by SH-500 (Digital force gauge, Sundoo, China). Force is measured from 1 to 50 N.

Figure 5.
Measure the change in length using a force of 5N (A) Pig heart elasticity experiment (B) Agilus elasticity experiment (C) Tango elasticity experiment (D) TPU elasticity experiment (E) Silicone elasticity experiment.
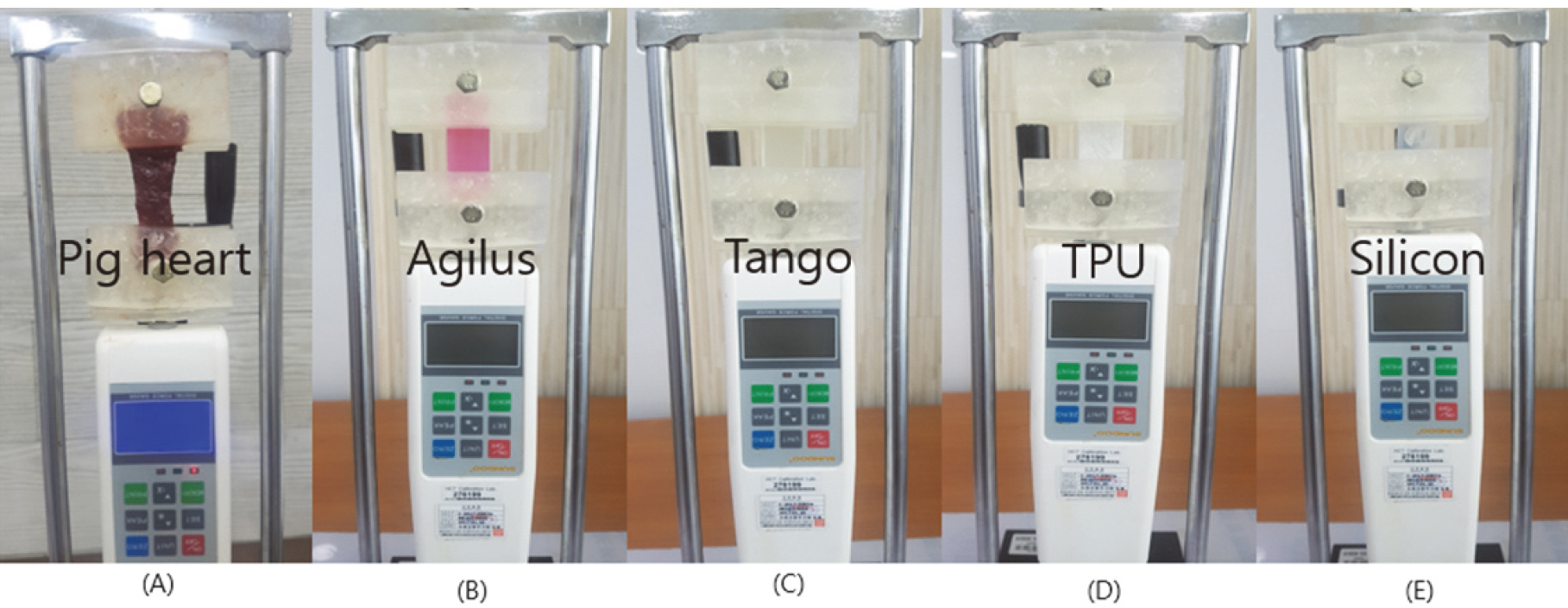
3.Results
Table 2 shows the elastic coefficient of the pig, Agilus, Tango, and Silicone sample. Agilus, Tango, and silicone did not show the same elastic coefficient when compared to the pig sample with a sample size of width 50 mm, length 20 mm and height 7 mm. In Tango, the elastic coefficient of height 0.5 mm was about 3 times higher than the pig sample of height 7 mm. Tango shows the closest elastic coefficient. TPU adjusts elasticity using density control. As an FDM method, the inner space is changed when manufacturing the TPU sample and the outer wall is the same. Therefore, the elasticity could not be measured.
(2)
(3)
(4)
(5)
The formula was obtained through data fitting using the elastic coefficient of each material. Pig heart has the Eq. (2), Agilus Eq. (3), Tango Eq. (4), and Silicone Eq. (5). Each formula can be used to make a heart model using pig heart, Agilus, Tango, and Silicone elasticity results.
4.Discussion
The elasticity test was conducted by comparing 3D printing material and silicone with a pig heart as the standard reference. The sample was compared based on the size of width 50 mm, length 20 mm and height 7 mm. The elastic coefficient of the pig sample was 0.1646, and the same elasticity could not be found at a sample of the same size. In the case of the Tango model, the difference of elastic coefficient is about three times at height 0.5 mm of the sample. When creating a heart model considering only elastic coefficient, Tango can be used to find the most similar elastic coefficient. In the 3D print study of the medical field, to study the modeling of the heart with complex anatomical structures is ongoing [3]. But only the structure of the heart is important. In the case of surgical simulator models, not only is the anatomy of the heart important, but it is also important to model similar to the physical properties of the heart. If the heart model is made using material of suitable elasticity using the results of this paper, the model can be made similar to a real heart. However, this study did not find any material exhibiting the same elasticity in the same sample size as the heart. Although various 3D print materials are being developed, it is not easy to reproduce the same elasticity at the same size as the heart. If the heart is modeling considering only elasticity, we will be able to easily reproduce the elasticity of the heart using Eqs (2)–(5). Previous work has been done using 3D heart models [12]. Although 3D heart models using 3D printers are helpful, they say that 3D printer models are different from actual heart elasticity [13]. The Agilus, Tango, and Silicone elastic formulas in this study will help to create a heart model.
5.Conclusions
The study was conducted using 3D print material and silicone, which can reproduce the elasticity of a pig heart. There is currently no material that can reproduce the elasticity of the pig heart at the same sample size. However, if the heart is manufactured considering only elasticity, it can be sufficiently reproduced using this study result. When developing 3D print materials, medical 3D print materials should be developed considering the characteristics of the tissue.
Conflict of interest
The authors declare that they have no conflict of interest.
Funding
This study was supported by a grant from the Korea Health Technology R&D Project through the Korea Health Industry Development Institute (KHIDI), funded by the Ministry of Health & Welfare, Republic of Korea (grant number: HI17C2594).
References
[1] | Klein GT, Lu Y, Wang MY. 3D printing and neurosurgery–ready for prime time? World neurosurgery. (2013) ; 80: (3–4): 233-5. |
[2] | Tappa K, Jammalamadaka U. Novel biomaterials used in medical 3D printing techniques. Journal of Functional Biomaterials. (2018) ; 9: (1): 17. |
[3] | Yoo S-J, Thabit O, Kim EK, Ide H, Yim D, Dragulescu A, et al. 3D printing in medicine of congenital heart diseases. 3D Printing in Medicine. (2016) ; 2: (1): 3. |
[4] | Markert M, Weber S, Lueth TC, eds. A beating heart model 3D printed from specific patient data. 2007 29th Annual International Conference of the IEEE Engineering in Medicine and Biology Society; IEEE: (2007) . |
[5] | Banks J. Adding value in additive manufacturing: researchers in the United Kingdom and Europe look to 3D printing for customization. IEEE Pulse. (2013) ; 4: (6): 22-6. |
[6] | Schubert C, Van Langeveld MC, Donoso LA. Innovations in 3D printing: a 3D overview from optics to organs. British Journal of Ophthalmology. (2014) ; 98: (2): 159-61. |
[7] | McMenamin PG, Quayle MR, McHenry CR, Adams JW. The production of anatomical teaching resources using three-dimensional (3D) printing technology. Anatomical Sciences Education. (2014) ; 7: (6): 479-86. |
[8] | Ziv A, Wolpe PR, Small SD, Glick S. Simulation-based medical education: an ethical imperative. Academic Medicine. (2003) ; 78: (8): 783-8. |
[9] | Costello JP, Olivieri LJ, Krieger A, Thabit O, Marshall MB, Yoo S-J, et al. Utilizing three-dimensional printing technology to assess the feasibility of high-fidelity synthetic ventricular septal defect models for simulation in medical education. World Journal for Pediatric and Congenital Heart Surgery. (2014) ; 5: (3): 421-6. |
[10] | Costello JP, Olivieri LJ, Su L, Krieger A, Alfares F, Thabit O, et al. Incorporating three-dimensional printing into a simulation-based congenital heart disease and critical care training curriculum for resident physicians. Congenital Heart Disease. (2015) ; 10: (2): 185-90. |
[11] | Michalski MH, Ross JS. The shape of things to come: 3D printing in medicine. Jama. (2014) ; 312: (21): 2213-4. |
[12] | Jacobs S, Grunert R, Mohr FW, Falk V. 3D-Imaging of cardiac structures using 3D heart models for planning in heart surgery: a preliminary study. Interactive Cardiovascular and Thoracic Surgery. (2008) ; 7: (1): 6-9. |
[13] | Yoo S-J, Spray T, Austin EH, III, Yun T-J, van Arsdell GS. Hands-on surgical training of congenital heart surgery using 3-dimensional print models. The Journal of Thoracic and Cardiovascular Surgery. (2017) ; 153: (6): 1530-40. |