COVID-19: Lessons from a construction site, can we apply one industry safety protocol to another?
Abstract
More than six months after the Shelter-in-Place executive order in the San Francisco Bay Area, this paper analyzes how an essential public works construction project put a COVID-19 safety protocol in place. It describes a four-step protocol, details challenges and successes of implementation, and provides insight for construction as well as other industries, including healthcare.
1.Introduction
In California, the first cases related to the COVID-19 pandemic were confirmed on January 26, 2020. The San Francisco Bay Area was among the first early centers of the pandemic in the state of California. As a consequence, local public and health officials created a mandatory Shelter-in-Place order for the counties of Alameda, Contra Costa, Marin, San Francisco, Santa Clara, Santa Cruz, and San Mateo. Effective immediately on March 17, 2020, companies and businesses were required to shut down their activities. However, essential construction activities were largely limited to healthcare projects directly addressing the COVID-19 pandemic and projects that “provide services to vulnerable populations” [1].
More than six months after these Executives Orders were signed, the construction industry is now allowed to work if all activities follow required COVID-19 infection control protocols [2]. It is informative to evaluate how the health and safety protocols were implemented during the first essential construction projects. These first protocols would then become the norm and the barometer for essential and non-essential work in construction and other industries.
Our case study will be the San Rafael Elementary School Project, located 20 miles north of San Francisco which includes the construction of a new elementary school (K2-5), a multi-purpose room, a warming kitchen and new offices. When Shelter-in-Place was announced in the Bay Area and in Marin County for this particular project, the first question the construction management asked was, “how can you keep the jobsite open and safe for dozens of workers, students, teachers and other school staff?”
On March 19, 2020, Governor Newsom issued Executive Order N 33-20 [3] which issued a list of “Essential Critical Infrastructure Workers.” For a Public Works school project, workers were considered essential since they support the operation, inspection and maintenance of essential public work facilities. In addition, article 10.c of the Bay Area Shelter-in-Place would confirm that building a school is essential since it is “an Essential Infrastructure” including [
This essential project, which did not shutdown when most construction sites closed for several months [3], is located on an existing campus where students with special needs, Special Day Class (SDC) students, were the first to come back to school after their summer break. This required the construction General Contractor (GC) to implement additional safety mea sures to ensure that potential at-risk students could go back to school safely. We will review the different safety protocols, analyze the outcome, and look at potential improvements. These protocols can be applied to other industries, in particular those that provide services to exposed individuals. With COVID-19, everyone is at-risk; students with special needs are particularly vulnerable.
2.Methodology
This section describes the implementation of a COVID-19 protocol on our construction site. With the project deemed essential, we had one day to implement our protocol which consisted of four steps: Prevent, Detect, Address, and Report.
The following section will describe each step in detail.
2.1Prevent
The first step to implement a safe and healthy work environment is to prevent the spread of the virus. Following CDC guidelines [5], the first measures were to:
• Implement a “wear a mask at all time policy.”
• Practice social distancing.
• Resequence the schedule so that fewer employees are working in the same place at the same time.
• Add additional wash stations throughout the jobsite.
• Disinfect the jobsite at least four times a day, including critical areas such as high traffic zones, bathrooms and break zones.
• Disinfect tools and equipment at least four times a day and make sure that no one shares their tools.
• Forbid carpooling if workers are not from the same household.
• Redesign break zones so that workers can socially distance.
• Hold socially distanced safety meetings daily with less than ten people at the beginning of the day to remind all workers about the new rules.
• Keep a clear separation between the construction crew and other people on campus including special needs students, their teachers and the maintenance personnel.
• Share the protocol with all subcontractors and architects so that anyone entering the jobsite has a good understanding of the infection control plan in place.
• Superintendent and Project Engineer walk the jobsite every day and remind personnel of the protocol and enforce it if need be.
• Reserve ADA paths of travel (ramps in particular) for the most at-risks people on campus so that they can maintain social distancing.
2.2Detect
Once precautionary measures were implemented, it was essential that COVID-19 cases, if any, were detected as soon as possible so that the situation could be addressed. In order to detect any cases, workers had to scan a QR Code with their phones to access a daily sign-in sheet (see Fig. 1). This was in addition to the daily safety meeting at the beginning of the day.
Figure 1.
Daily sign-in sheet for COVID-19 prevention and detection.
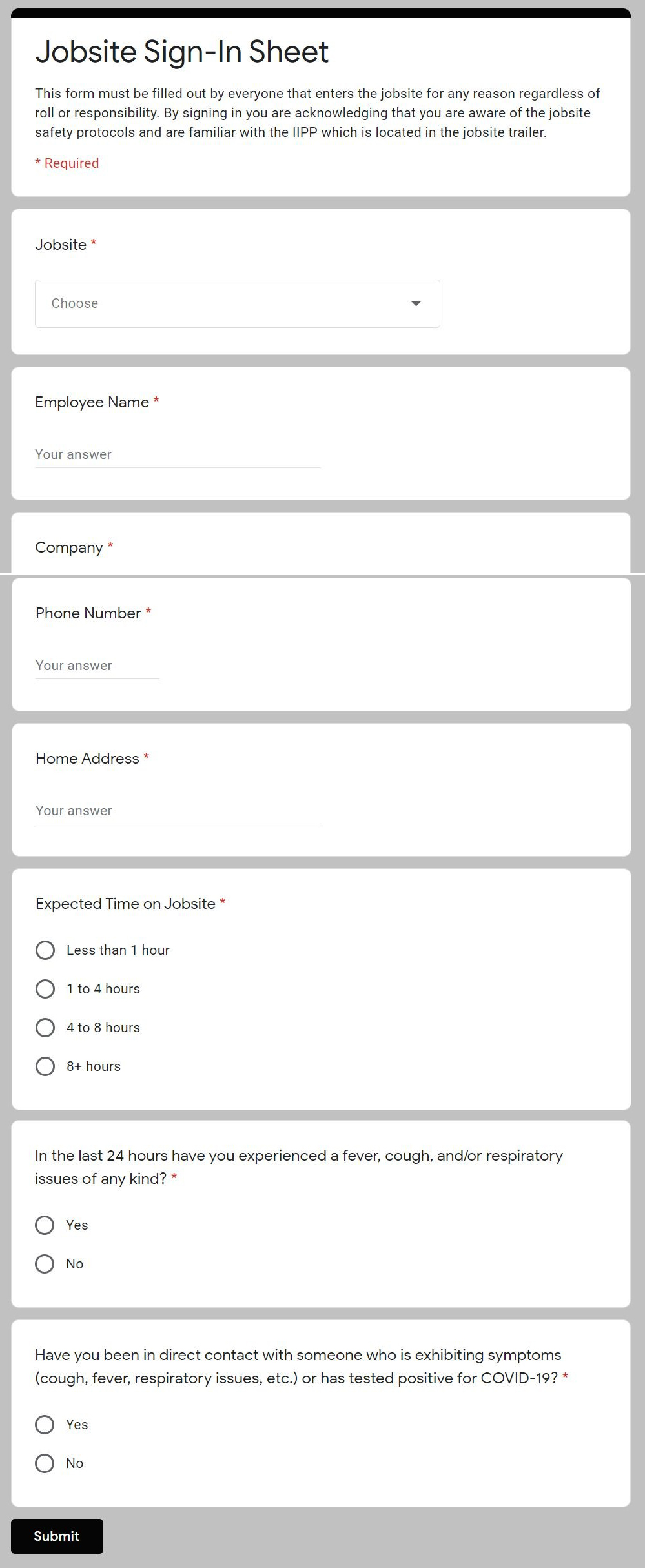
Figure 2.
SCO daily jobsite verification.
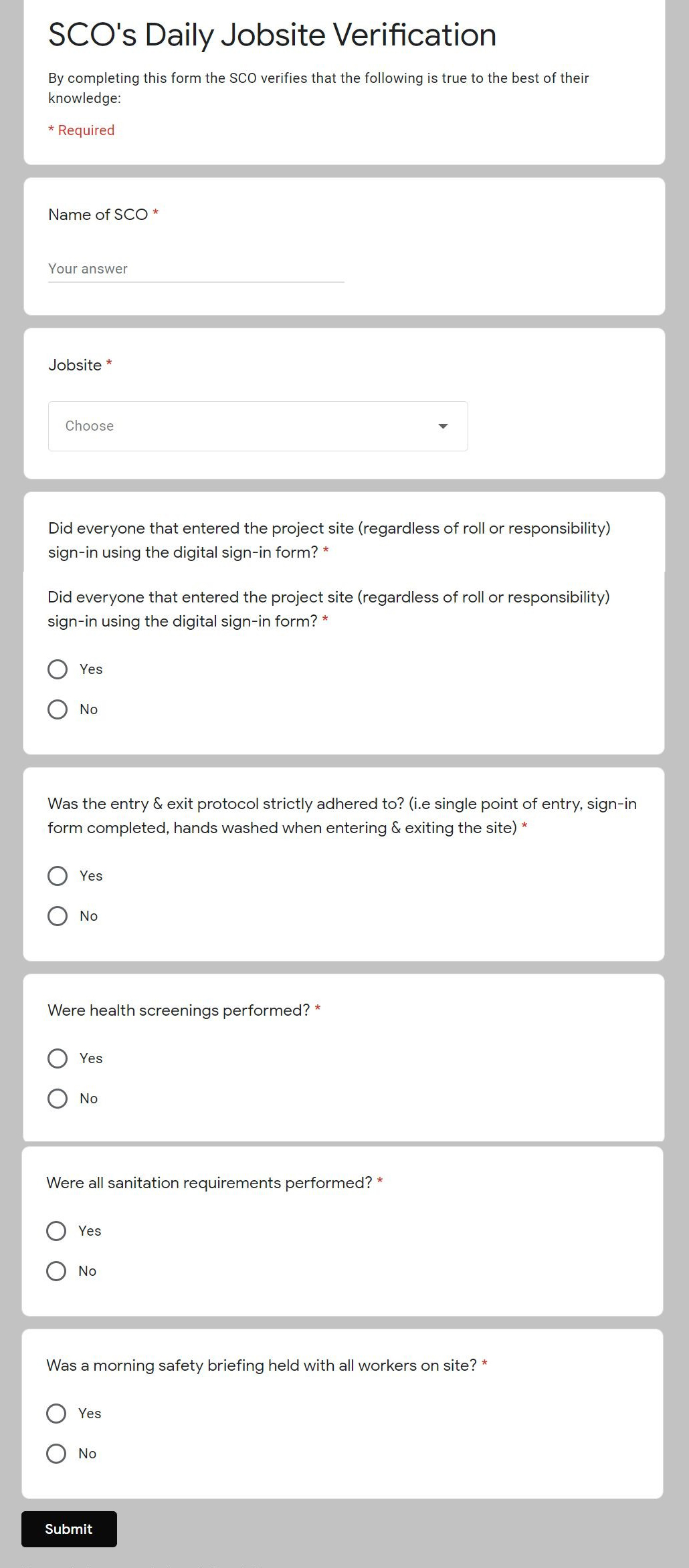
Workers had to sign-in and make a solemn declaration that they hadn’t shown any COVID-19 symptoms in the past 24 hours nor had they had been in contact with someone who had symptoms and/or had tested positive for the virus. This mandatory confidential questionnaire was fundamental to keep track of who was onsite and to quickly remediate if someone showed symptoms of the virus. In order to respect workers’ privacy, personal information was kept confidential and was only visible to one trusted individual within the General Contractor (GC)’s company.
Figure 3.
Weekly JSAS report.

2.3Address
Over the past six months of the study, only one worker replied that he had been in contact with someone exhibiting symptoms of COVID-19. Although it would have been preferable for this worker not to report to work, his honest reply to the declaration of honor was crucial to assess the situation. We assessed with whom he had been in contact. Our actions included isolating the individual, sending him home to self-quarantine for fourteen days, arranging for testing, and disinfecting any areas of potential contact. We also reported this potential exposure to the company safety team.
2.4Report
If there is a suspicion of COVID-19, the last step of the protocol requires the individual to self-quarantine. If they do not show any symptoms, two negative tests within a period of seven days are required in order to be allowed back on the jobsite. Otherwise, they have to quarantine for fourteen days. It is critical to have a COVID-19 Task Force in place within the GC’s company to enable prompt reporting from the jobsite superintendent.
Being factual with the report (including photos, sketches, description of the situation) is critical. A worker who contracted COVID-19 on a jobsite can be entitled to workers’ compensation. Therefore, evidence that the worker contracted the virus outside the jobsite protects the liability and expenses of the GC as well as the entire project.
The company also followed the Appendix B-2 of the Large Construction Project Safety Protocol [6] which became effective on May 4, 2020. The jobsite had a Safety Compliance Officer (SCO) whose duties included completing a daily report detailing 100% compliance with the daily sign-in form, entry and exit protocol, heath screening, sanitation requirements, and morning safety briefing (see Fig. 2). Every two weeks, a Jobsite Safety Accountability Supervisor (JSAS), who was a Carpenter Union representative, was onsite to inspect and confirm that all safety protocols were in place per Appendix B-2. The GC had to report weekly to the JSAS (see Fig. 3).
3.Discussion
Implementing all of these protocols over a very short period of time was not easy. The goal of this section is to identify the challenges and how they were overcome. Due to the inherent nature of construction activities, some of these measures can be difficult to implement and require specific managerial skills so that they can be understood and respected by everybody on the jobsite.
On March 19, 2020, face covering was not mandatory throughout the Bay Area. This Essential Public Works project was among the first to have a face covering policy, which can be challenging on a construction site. Simply wearing a facemask can be uncomfortable during construction activities; it limits breathing, visibility, and communicating with others. To mitigate the impact of wearing a facemask during construction activities, the jobsite superintendent and other company managers must continually educate, communicate, and enforce safety measures on a daily basis. Reinforcing safety measures needs to be done on a daily basis, and it is not just a job for one individual (the Safety Compliance Officer). The company has to create a culture where everyone is responsible for each other’s health and safety, particularly in the face of the COVID-19 pandemic.
Social distancing is another challenge on the jobsite. The nature of construction activities makes it difficult to social distance because workers from different teams are often in close contact and often work in binoms. For example, a journeyman and an apprentice may work together for 8 hours in a given day. Following CDC guidelines for social distancing, workers could not be less than 6 feet apart for more than 15 minutes at a given time and both workers had to wear a mask. After 15 minutes in close proximity, both workers had to step apart to at least 6 feet for 10 minutes before they could be less than 6 feet away again.
Consequently, the work sequence had to be reconfigured. Reconfiguration included dividing the employees between different shifts, so that there were fewer in a designated area at a given time, and using different tools to achieve the same results.
Another challenge we encountered was the actual cost of implementing these safety protocols. Buying extra wash stations, bathrooms, cleaning tools, and having personnel responsible for disinfecting the areas at least four times a day (2 hours per day) had a substantial cost on the GC’s budget. This resulted in having a discussion with the owner about a change order for the added cost. Thus, the cost of the protocols should be included in future bids.
Moreover, this project was challenging because it was located on an existing school campus. At the beginning of Shelter-in-Place, teachers and students were staying at home. However, after Summer Break, some teachers went back to school to teach remotely from their classrooms. First and second graders began in-person class September 5, 2020 and students with special needs (Special Day Class) also came back to the campus [7]. It was critical to keep clear separation between workers, students, and teachers to ensure social distancing was respected everywhere, including American with Disabilities Act (ADA) requirements for paths of travel. By having designated parking spots and new fences, the separation helped with having an infection-free construction project.
4.Conclusion
After six months of COVID-19 protocol implementation, these measures proved successful. No one tested positive on the jobsite. In addition, even though this construction project was among the first to have these protocols in place, they are now the norm in the Bay Area (see Appendix B). Using the PREVENT, DETECT, ADDRESS, and REPORT safety protocol, clear guidelines can be set for appropriate safety protocols that mitigate the spread of COVID-19. New protocol implementation can be challenging due to the nature of construction and its long-standing culture; upper management must be supportive and involved in communication to workers, subcontractors, and clients. Construction is specific project location based; in this instance in an active, existing school which poses additional challenges. These challenges may be applicable to other industries, including health care, and require supportive upper management that is transparently involved with frequent and clear communication to staff, patients, families, and other stakeholders to ensure adherence to appropriate safety protocols in a variety of hospital and other clinical settings.
Technology introduction, such as social distancing sensors or automatic sign-in devices, may enable improved adherence to safety protocols. The cost of implementation of safety protocols must be considered; in construction, different options to mitigate cost include change orders, time extensions, and contingency use which may not be available to other industries. Reconfiguring work sequencing by utilizing different shifts, decreasing workforce in designated areas, and using different tools to achieve the same results are ideas that may be applicable to lower costs of implementation.
In conclusion, this case study shows that using the PREVENT, DETECT, ADDRESS, and REPORT protocol, avoided COVID-19 infection on the construction jobsite. This safety protocol is proposed for use in other industries, including healthcare.
Conflict of interest
The author has no conflict of interest to report.
References
[1] | Waxxman L. Most Bay Area Construction Banned under revised shelter-in-place order. San Francisco Business Times. [Cited 2020 October 1]. [internet]. Available from: https://www.bizjournals.com/sanfrancisco/news/2020/03/31/most-bay-area-construction-prohibited-under.html. |
[2] | SF.gov. Information on Construction During the Coronavirus Pandemic. [Cited 2020 October 1]. [internet]. Available from: https://sf.gov/information-construction-projects-during-coronavirus-outbreak. |
[3] | Covid19.ca. Executive Order N-33-20. [Cited 2020 October 1]. [internet]. Available from: https://covid19.ca.gov/img/Executive-Order-N-33-20.pdf. |
[4] | Order of the Health Officer of the County of Santa Clara. March 16th 2020. [Cited 2020 October 1] .[internet]. Available from: https://www.sccgov.org/sites/covid19/Pages/order-health-officer-031620.aspx. |
[5] | CDC. What Construction Workers Need to Know about COVID-19. [Cited 2020 May 19]. [internet]. Available from: https://www.cdc.gov/coronavirus/2019-ncov/community/organizations/construction-workers.html. |
[6] | Appendix B-2 for Marin Health Order effective May 4, 2020. [Cited 2020 October 1]. [internet]. Available from: https://coronavirus.marinhhs.org/appendix-b-2-marin-health-order-effective-may-4-2020. |
[7] | Fensterwald J. California schools allowed to open for small groups with ‘acute’ needs under new guidance. EdSource. [Cited 2020 October 1] [internet]. Available from: https://edsource.org/2020/california-schools-allowed-to-open-for-small-groups-with-acute-needs-under-new-guidance/638337. |