Hydrogen-absorbing alloy-based metal-hydride actuation for application in rehabilitative systems
Abstract
BACKGROUND:
A lightweight rehabilitation assisting system is required to help the aged and disabled with daily life activities, thereby improving the quality of their lives.
OBJECTIVE:
This paper discusses the development of a metal-hydride (MH) actuator, with excellent heat transfer performance, for application in a rehabilitative system incorporating an MH module.
METHODS:
The operating mechanism of MH actuators requires that the mechanical power of the pneumatic actuator only be generated via heat transfer through a Peltier element and the absorption/desorption of a hydrogen-contained MH module. To achieve this aim, a 3D model was first designed for two MH modules, and a thermal analysis was carried out according to the type of contact with the Peltier elements to fabricate an MH module with improved heat transfer performance. LabVIEW (National Instruments) was used for automatic temperature control of the Peltier element in the MH actuator driving experiment. Zr
RESULTS:
In addition, the temperature conditions of the MH actuator driving experiment were restricted by two temperature control ranges (30–40
CONCLUSIONS:
These findings indicate that the MH actuator proposed in this paper can be utilized to drive a rehabilitative system for elbow and knee joint exoskeletons.
1.Introduction
As the populations of the aged and disabled increase, various types of rehabilitative systems have been developed for them. Such systems are termed rehabilitation training systems, which are therapy and/or assistive systems designed to support activities of daily life. Patients are typically required to travel to a university or rehabilitation hospital to use the motor rehabilitation-purposed systems. Because therapy is the primary goal, most rehabilitative systems are large and occupy a considerable amount of space. Conversely, an aid system assists activities of daily life (ADL), such as walking, of the aged or chronically disabled both in and out of their homes. This system is composed of an exoskeleton, which is attached to the side of the target upper or lower extremity body part, a curved component, which fixes the exoskeleton to the body of the user, and an actuator to drive movement.
To enhance the comfort of a daily life assistive system, the system needs to be small and light, particularly to ensure high transportability. Existing assistive systems have employed a driving source that drives the motions of each joint by means of pneumatic and hydraulic devices. However, because pneumatic and hydraulic devices require a separate pneumatic generator, or are heavy, implementation in assistive systems is not preferred. Recently, because high-power micro motors have been increasingly developed, most rehabilitative systems have come to incorporate a motor. Unfortunately, electric motors, which generate joint torques sufficient to support the ADL of patients wearing the system on their upper or lower extremities, remain to be heavy for users. In the case of myPro (Mymyo Inc.), which assists flexion-extension elbow motions of the aged, the driving electric motor constitutes 40% of the weight of the entire system. Furthermore, new types of driving units, such as shape memory alloy actuators and series elastic actuators (SEAs), cannot generate sufficient torques to assist motions of upper and lower extremities.
Many researchers have focused on developing medical and rehabilitation equipment using hydrogen-absorbing alloys. As an example, Shimizu et al. used a metal-hydride actuator to determine the forces of elbow joint motions [1, 2]. Wakisaka et al. applied the driving principle of metal-hydride actuators to implement them in various types of medical and rehabilitation equipment [3, 4]. Ino et al. performed a study on a bellow-type soft metal-hydride actuator for use in rehabilitation and aid equipment for those suffering from dyskinesia due to stroke or old age [5, 6, 7]. Kurosaki et al. developed a simple metal-hydride actuator that included a hydrogen-absorbing alloy with a copper plate [8]. Sato et al. utilized the principle of a metal-hydride actuator to develop a mobility assistive system that is able to help a patient stand up from a wheelchair [9]. Ino et al. fabricated a tiptoe passive motion device by implementing a flexible metal-hydride actuator to prevent bedsores [10, 11]. Lloyd and Kim employed hydrogen-absorbing alloy technology and a pneumatic actuator to test a new metal-hydride actuator [12]. Kwon et al. carried out a study to develop a new metal-hydride actuator with a hydrogen-absorbing alloy that joined eight copper pipes via welding [13, 14]. Additionally, Kim et al. designed a new metal-hydride actuator that used copper to improve heat transfer efficiency [15, 16].
Metal-hydride (MH) actuators are being developed to reduce the weight of the driving component in assistive systems that are designed to support activities of daily life. Hydrogen gas contained in MH follows the process of hydrogen absorption-desorption according to the thermal change (heating-cooling) applied to the MH. An MH actuator, which is able to interchangeably use thermal energy and mechanical energy, can store as much as 1,000 times the volume of the alloy; additionally, it has the advantages of being small while also generating high power. However, one absorption-desorption cycle of hydrogen in the existing MH actuator is time expensive, causing it to be a disadvantageous application in a system designed to assist upper and lower extremity joint motions for ADL. Regarding the performance of MH actuators, the heat transfer efficiencies of an MH module and heat source of a peltier device are the primary causes of hydrogen absorption-desorption increase. Thus, fundamental research on the design of the heat source and heat transfer of an MH module is needed to enhance the performance of MH actuators.
In this study, a MH module able to improve heat transfer performance was fabricated, and a MH actuator, which was driven according to a predetermined temperature range of a Peltier element, was developed. The hydrogen-absorbing alloy was selected based on the driving constraints of the rehabilitative system for upper and lower extremity exoskeletons; in addition, the MH actuator driving experiment was performed according to the constraints of the temperature range.
Figure 1.
PCT curve of selected hydrogen-absorbing alloy.
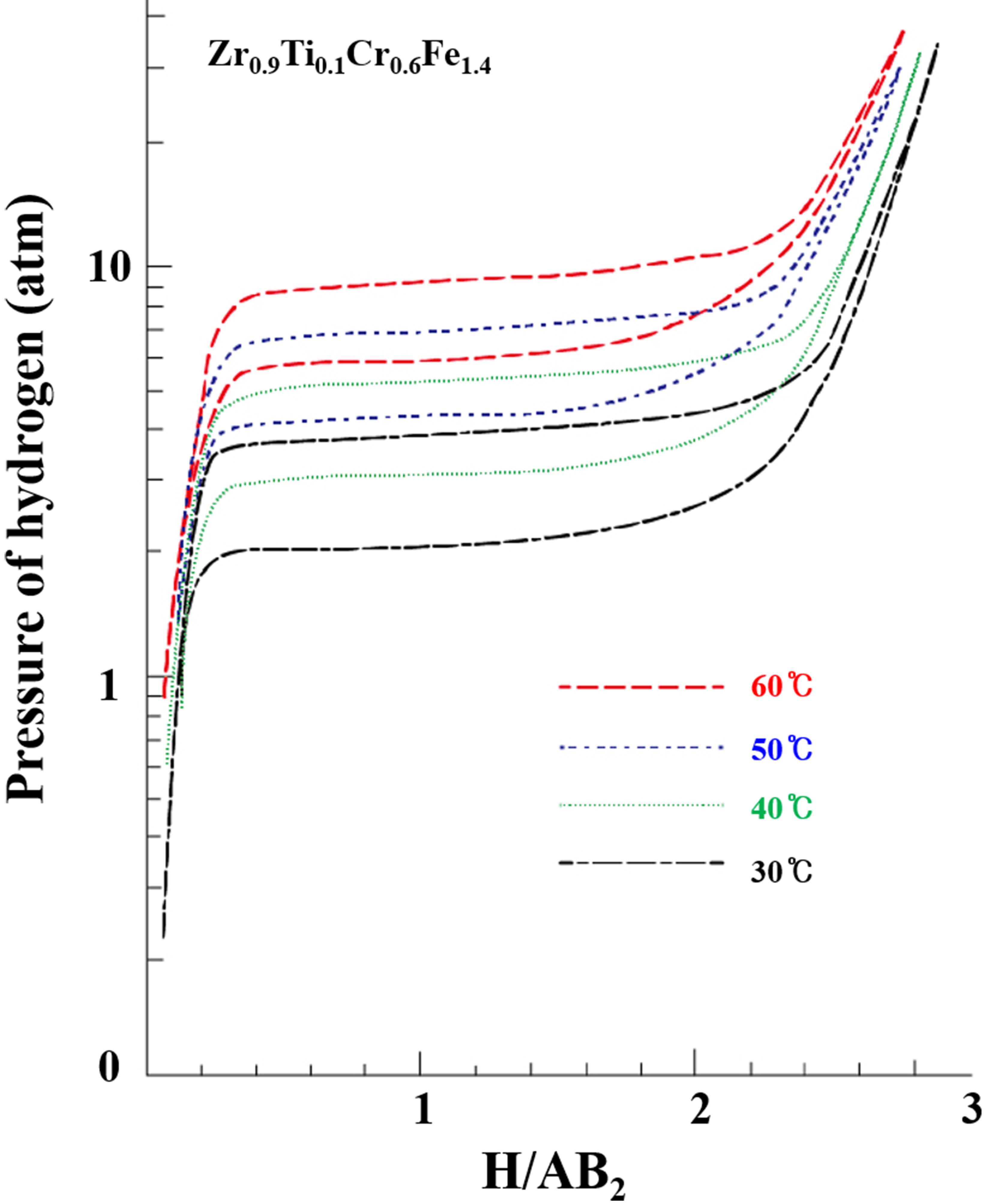
2.MH selection and MH module design
2.1Selection of hydrogen-absorbing alloy
Because hydrogen-absorbing alloys possess a significantly higher hydrogen storage capacity per unit volume than liquid or gaseous hydrogen, a micro MH actuator, which is driven by a small amount of hydrogen-absorbing alloy, can be developed. Furthermore, the hydrogen absorption and desorption of hydrogen-absorbing alloys can be controlled by implementing a PCT curve with varying pressure and temperature. As a result, the hydrogen-absorbing alloys can be used as a rehabilitative system power source. To drive a rehabilitation system exoskeleton designed to assist joint movements of upper and lower extremities such as elbow and knee joints, a safe four-component hydrogen-absorbing alloy was selected for used in this study because it satisfies the low temperature (temperature range: 30–60
Figure 2.
MH module concept; (a) line contact, and (b) face contact.
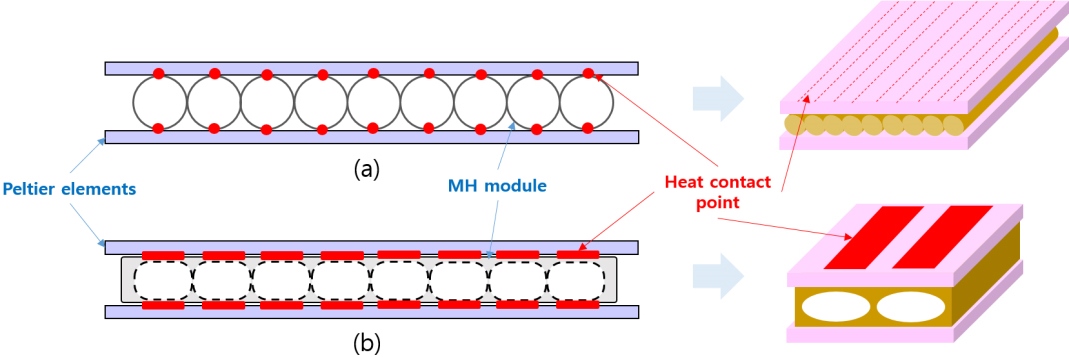
Figure 3.
MH module with (a) line contact (Type 1) and (b) face contact (Type 2).
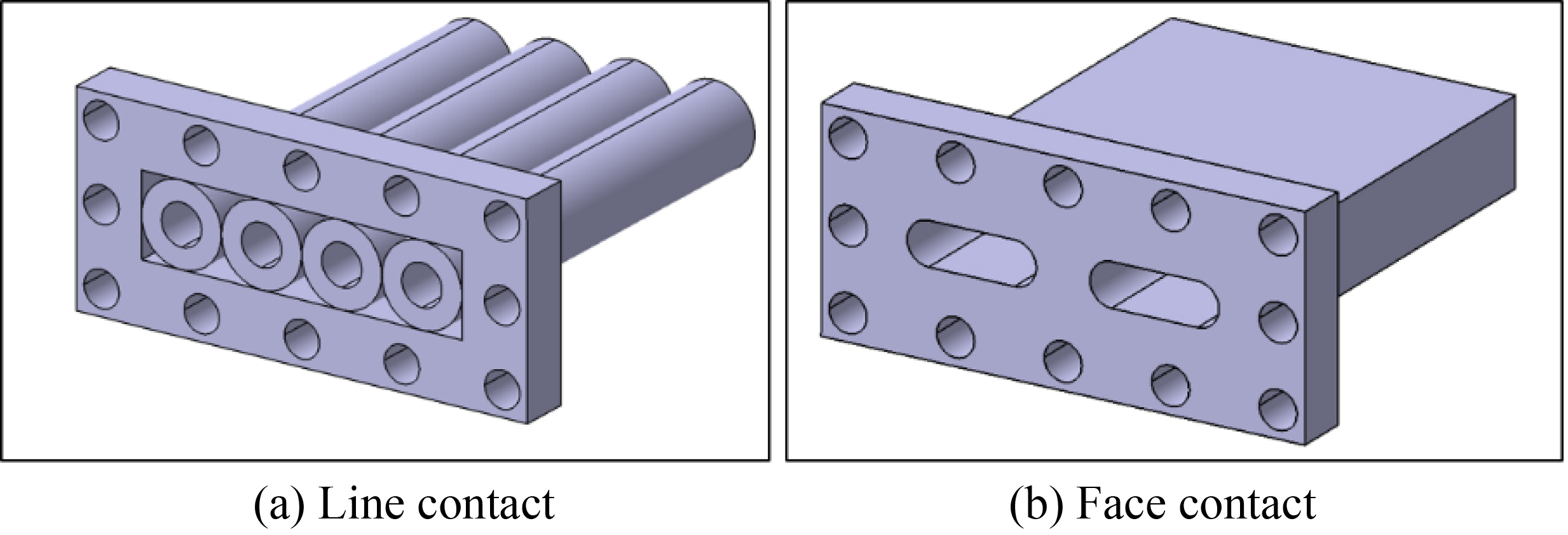
2.2Design of metal-hydride module
The hydrogen-absorbing alloy utilized in the MH module absorbs heat from two Peltier elements contacting both sides of the module. Hydrogen gas is heated and cooled by the heat from the Peltier elements, and is stored within the MH module. This hydrogen gas drives a rehabilitative system by generating an absorption-desorption mechanism.
To improve heat transfer performance, a MH module was fabricated to suit a conventional MH actuator by welding nine copper tube cylinders. The MH module and Peltier elements were in line contact, as shown in Fig. 2a above [15]. Considering the MH module of the conventional MH actuator, an improved MH module with enhanced heat transfer performance needs to be designed to sufficiently support a rehabilitative system. This new hydrogen-absorbing alloy-containing MH module alloy should be designed to have face contact with Peltier elements, as shown in Fig. 2b; in addition, the difference in heat transfer efficiency between this new face contact and the conventional line contact needs to be analyzed.
Because the MH module of the conventional MH actuator comprises eight welded copper cylinders, the module has a line contact with Peltier elements. The MH alloy in the cylinders of each MH module drives the MH actuator as hydrogen is absorbed or desorbed by the heat transfer through the line contact with Peltier elements. As shown in Fig. 3a, a 3D model of the line contact-type MH module was designed to analyze the heat transfer efficiency of the module, which is regulated by the heating and cooling of the Peltier elements. The MH module had dimensions of 40 mm
To enhance the driving performance of the MH actuator, a face contact design was incorporated to increase the contact area with the Peltier elements. Figure 3b shows an MH module designed to have a size identical to that of the conventional line contact-type MH module; it also comprised two holes for the hydrogen-absorbing alloy. This face contact-type MH module was a plate-shaped rectangular parallelepiped with a reduced number of holes and a face with dimensions of 40 mm
Figure 4.
Temperature change-induced progression of heat transfer in line contact condition.
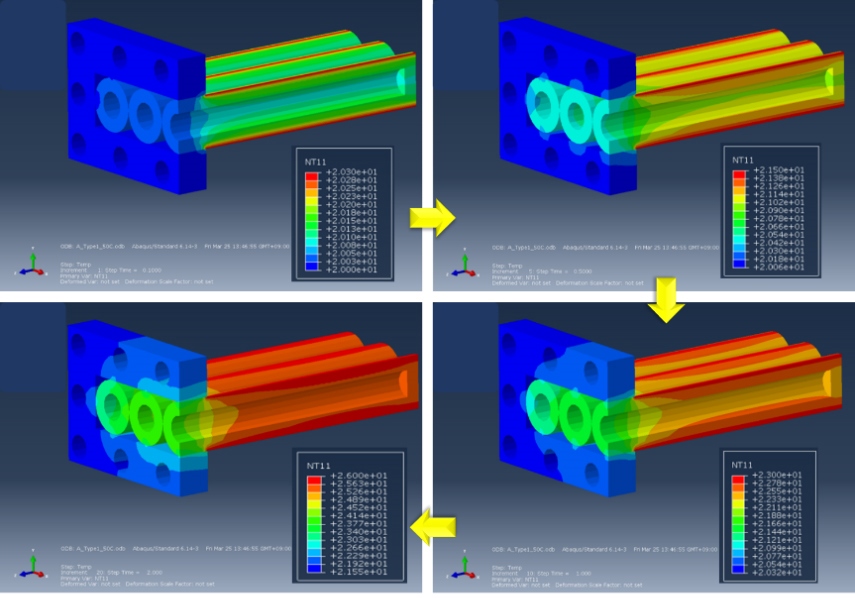
Figure 5.
Temperature change-induced progression of heat transfer in face contact condition.
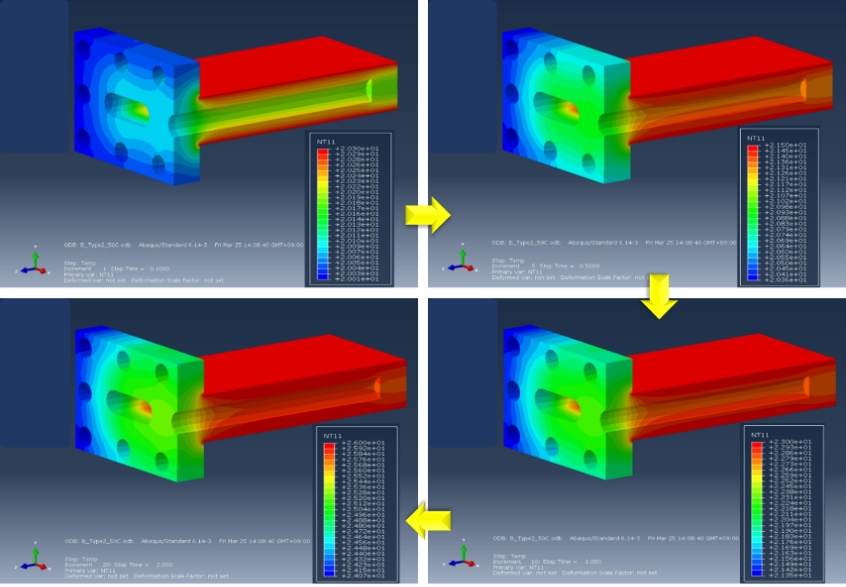
Figure 6.
Experimental setup.
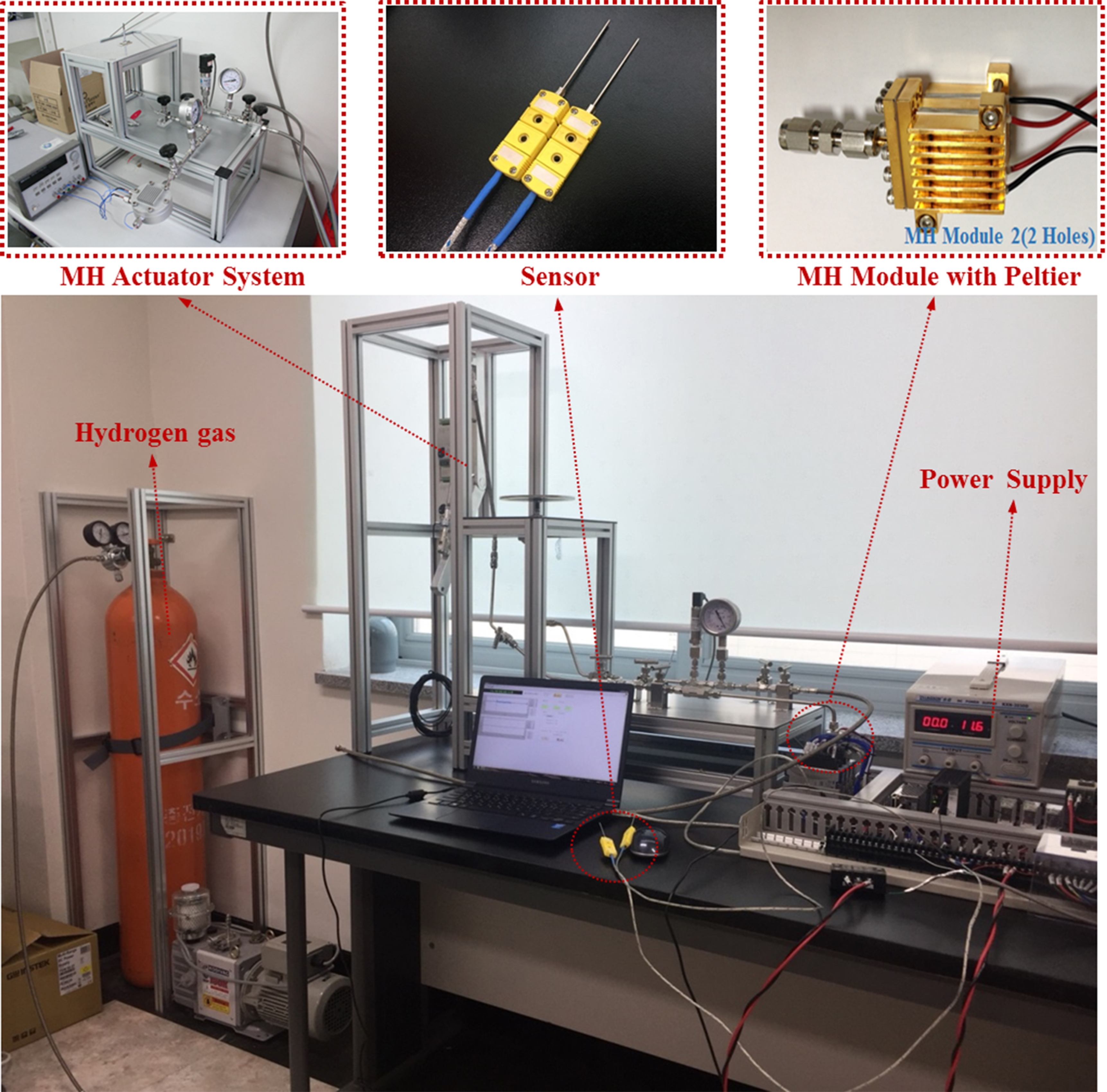
Figure 7.
Software used to drive the MH actuator.
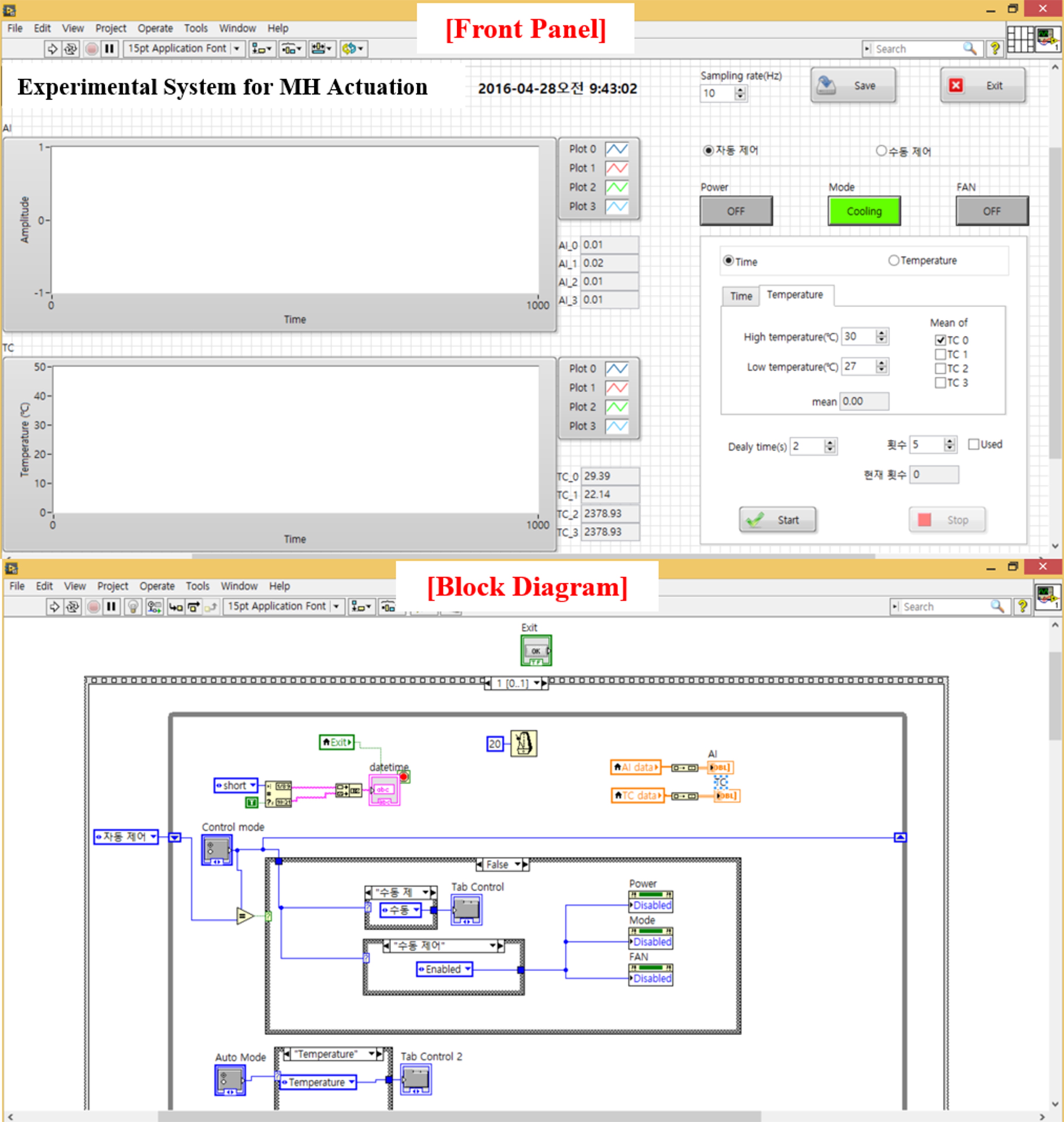
2.3Design of metal-hydride module
The two types of MH modules were compared in terms of heat transfer efficiency, which was based on the heating and cooling conditions of the Peltier elements, to analyze their respective heat transfer ability. The temperature range for the thermal analysis according to the PCT curve of the selected hydrogen-absorbing alloy was 30–60
Figure 8.
Temperature variation during cooling-only fan ON state.
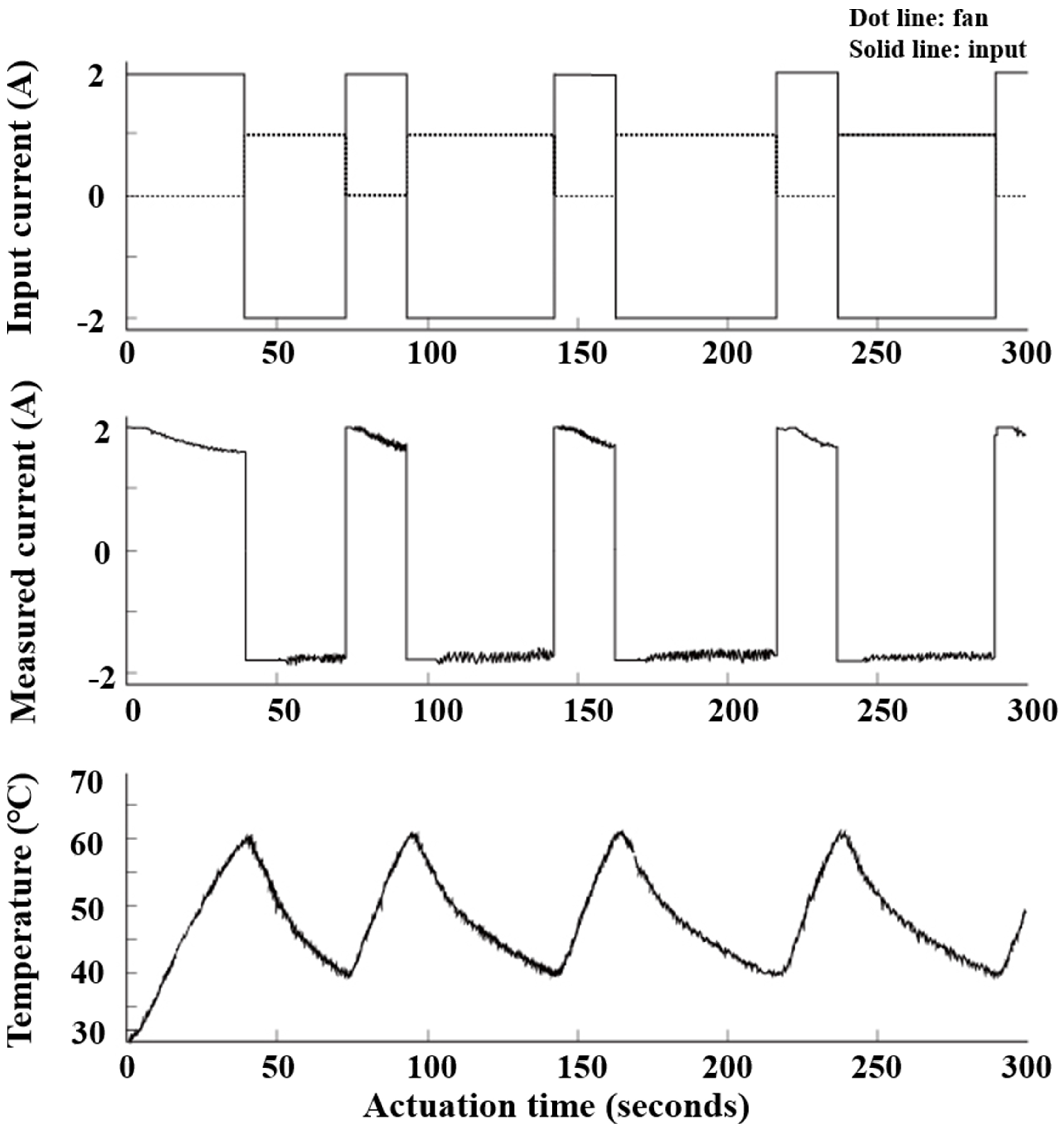
Figure 9.
Temperature variation during heating and cooling fan ON state.

Figure 10.
MH actuator results (30–40
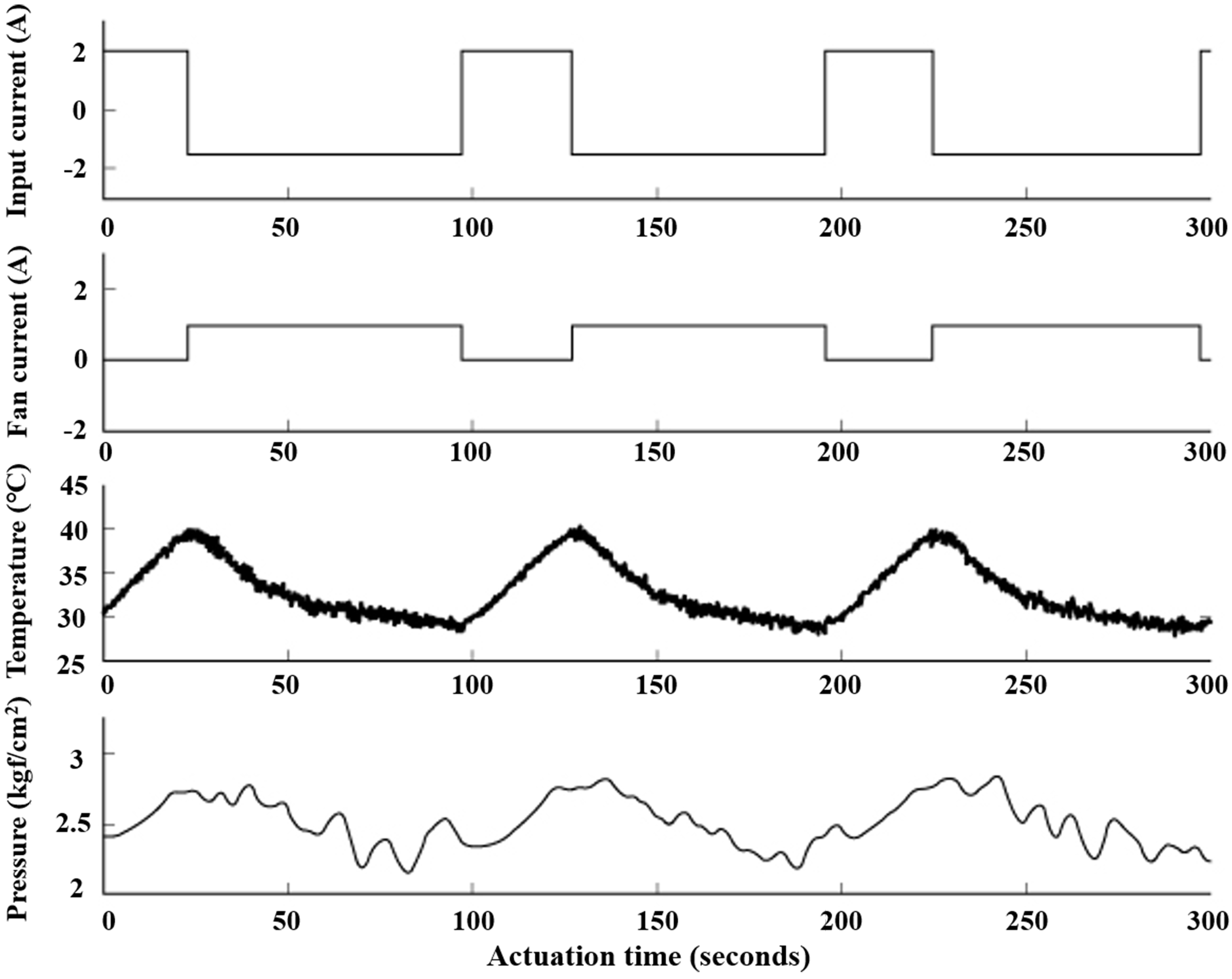
Figure 11.
MH actuator results (30–50
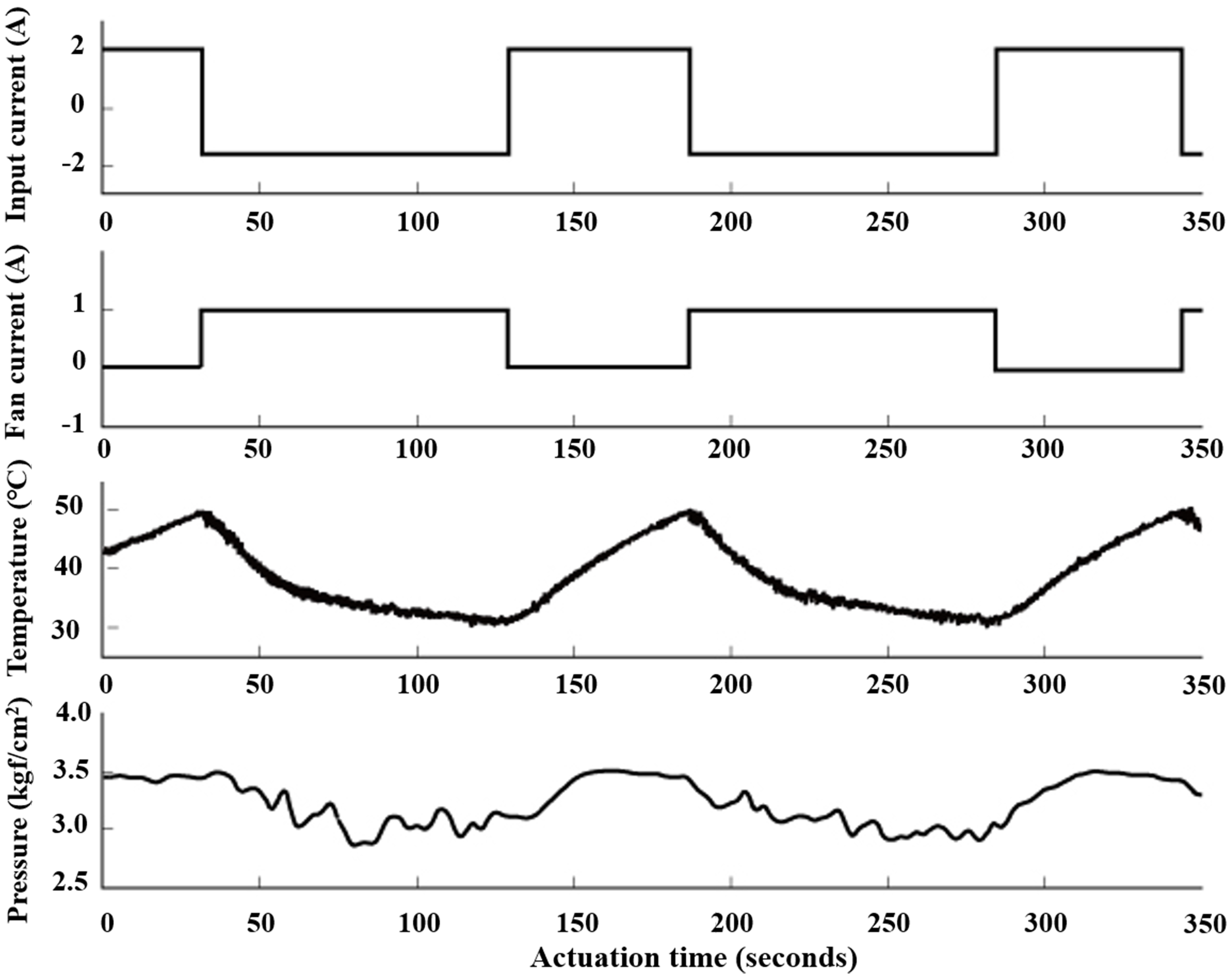
3.Experimental method
The time required to cool down the MH module to the target temperature depends on the operating conditions of the MH actuator cooling fan. The MH module used in this study was fabricated to have a 3D structure that improved the heat transfer performance via thermal analysis. A radiating fan and a cooling fan were added to further improve the cooling efficiency. To compare the results on temperature control, which were based on the operating conditions of a cooling fan, the following two cases were compared: 1) both heating and cooling control the operation of a cooling fan, and 2) only cooling controls the operation of a cooling fan. The temperature was maintained between 40 and 60
The hydrogen gas contained in the hydrogen-absorbing alloy of the MH module drives a pneumatic actuator via an absorption-desorption process, which operates according to the heating and cooling performance of the Peltier element. More explicitly, the temperature-controlled Peltier element causes hydrogen gas to leave the MH module and enter the actuator, thereby driving an MH actuator. An experimental environment was constructed for the actuation of the MH actuators in Fig. 6. As shown in Fig. 7, software used to control the Peltier elements was also implemented for automatic and manual control of an MH actuator. In the automatic control mode, the MH actuator operated according to a specified temperature range. In the manual control mode, MH actuator operation was controlled by an operator. Each control mode was programmed to include optional items such as a heating/cooling mode, ON/OFF function for the cooling fan, and the time/temperature range/number of repetition. LabVIEW (National Instruments), a commercial program, was used to design and implement the Peltier element and MH actuator controls.
The performance of the MH actuator, which drives a rehabilitative system for upper and lower extremities, was evaluated by carrying out an experiment applying two different constraints on temperature. More specifically, the driving experiments for the MH actuator were performed by regulating the heating and cooling to ensure that the temperature was maintained within the following temperature ranges: 1) 30–40
4.Experimental results
The experiment to verify the efficiency of the cooling fan, which was proposed to improve the cooling performance of the MH actuator, compared the performance under the following conditions: 1) both heating and cooling fan operation, and 2) only cooling fan operation. In Fig. 8, the graphs illustrate the fan operation during the process of cooling, whereas Fig. 9 presents the results of fan operation during processes of heating and cooling. The results shown in Figs 8 and 9 indicate that there are temporal variations of input current, measured current, and temperature. When the heating and cooling of a Peltier element was controlled via the
The hydrogen-absorbing alloy exhibited stable operation at or below 10 atm when the actuator temperature was maintained between 30 and 60
5.Conclusion
A MH module able to improve heat transfer performance was fabricated, and a MH actuator, which was driven according to a predetermined temperature range of a Peltier element, was developed.
The objectives of this research were to fabricate an MH module that had face contact with the Peltier elements, thereby improving heat transfer performance, and to develop a new type of MH actuator that effectively utilized the hydrogen mechanism to assist a motion of rehabilitation system. To achieve these objectives, fan operation was only permitted during cooling to select an appropriate hydrogen-absorbing alloy for a low-temperature and low-pressure rehabilitative system, and the variation in MH actuator driving pressure was determined according to the PCT curve of the selected alloy that resulted from restricting temperature to within two different ranges. As a result, the range of temperature control of Peltier elements can be customized to achieve the appropriate assistive torques of elbow and knee joints, which are the primary joints of upper and lower extremities. In a future study, the performance of an upper/lower extremity rehabilitative system will be validated by directly implementing a pneumatic actuator in the system.
Acknowledgments
This material is based upon work supported by the Ministry of Trade, Industry and Energy (MOTIE, Korea) under Industrial Technology Innovation Program (10068076) and supported by Basic Science Research Program through the National Research Foundation of Korea (NRF) funded by the Ministry of Education (2015R1D1A1A01059525, 2015R1D1A1A01057463).
Conflict of interest
None to report.
References
[1] | Shimizu S, Ino S, Sato M, Odagawa T, Izumi T, Takahashi M, Ifukube T. A basic study of a force display using a metal hydride actuator. 2nd IEEE International Workshop on Robot and Human Communication (1993) Nov. 3-5; Tokyo, Japan. |
[2] | Shimizu S, Ino S, Sato M, Izumi T, Ifukube T, Muro M, Takeda H, Wakisaka Y. A new method of variable compliance for a force display system using a metal hydride actuator. 3rd IEEE International Workshop on Robot and Human Communication (1994) July 18-20; Nagoya, Japan. |
[3] | Wakisaka Y, Muro M, Kabutomori T, Takeda H, Shimizu S, Ino S, Ifukube T. Application of hydrogen absorbing alloys to medical and rehabilitation equipment. IEEE Trans Rehab Eng (1997) ; 5: (2): 148-157. |
[4] | Tsuruga T, Ino S, Ifukube T, Sato M, Tanaka T, Izumi T, Muro M. A basic study for a robotic transfer aid system based on human motion analysis. Advanced Robotics (2000) ; 14: (7): 579-595. |
[5] | Ino S, Hosono M, Sato M, Nakajima S, Yamashita K, Izumi T. A soft metal hydride actuator using LaNi5 alloy and a laminate film bellows. IEEE International Conference on Industrial Techonology (ICIT) (2009) ; Feb 11-13; Victoria, Australia. |
[6] | Ino S, Sato M, Hosono M, Nakajima S, Yamashita K, Tanaka T, Izumi T. Prototype design of a wearable metal hydride actuator using a soft bellows for motor rehabilitation. 30th Annual International IEEE EMBS Conference (2008) Aug 20-25; Vancouver, BC, Canada. |
[7] | Ino S, Sato M, Hosono M, Izumi T. Development of a soft metal hydride actuator using a laminate bellows for rehabilitation systems. Sensors and Actuators B: Chemical (2009) ; 136: : 86-91. |
[8] | Kurosaki K, Maruyama T, Takahashi K, Muta H, Uno M, Yamanaka S. Design and development of MH actuator system. Sensors and Actuators A (2004) ; 113: : 118-123. |
[9] | Sato M, Ino S, Yoshida N, Izumi T, Ifukube T. Portable compressor system using MH alloys, employed as assistive devices. IEEE Region 10 Conference (TENCON 2006) (2006) Nov 14-17; Hong Kong, China. |
[10] | Ino S, Sato M, Hosono M, Nakajima S, Yamashita K, Izumi T. Preminary Design of a simple passive toe exercise apparatus with a flexible metal hydride actuator for pressure ulcer prevention. 32nd Annual International Conference of the IEEE EMBS (2010) Aug 31-Sep 04; Buenos Aires, Argentina. |
[11] | Hosono M, Ino S, Sato M, Yamashita K, Izumi T. A system utilizing metal hydride actuators to achieve passive motion of toe joints for prevention of pressure ulcers: A pilot study. Rehab Res Practice (2012) ; 1-7. |
[12] | Lloyd GM, Kim KJ. Smart hydrogen/metal hydride actuator. Intl J Hydrogen Energy (2007) ; 32: : 247-255. |
[13] | Kwon TK, Pang DY, Choi KH, Kim YY, Lee SC, Kim NG. Development of a SMH actuator system using hydrogen-absorbing alloys. Smart Mater Struct (2006) ; 15: : 1-7. |
[14] | Kwon TK, Hong KJ, Kim K, Jeon WS, Pang DY, Lee SC, Kim NG. Development of SMH actuator system using hydrogen-absorbing alloy. J Control Autom Syst Eng (2007) ; 13: (11): 1067-1073. |
[15] | Kim K, Kim SH. Analysis of heat transfer characteristic of metal-hydride module for the actuation of a rehabiliation system. Journal of Rehabilitation Welfare Engineering and Assistive Technology (2017) ; 11: (2): 165-171. |
[16] | Kim K, Kim JJ, Kim JN, Chong WS, Yu CH, Kwon TK. Suggestion of novel actuator for assitive and rehabilitative device of the elderly and people with disability. 37th Annual International Conference of the IEEE EMBS (2015) Aug 25-29; Milan, Italy. |
[17] | Park JM. A study on the hydrogenation characteristics of Zr-based laves phase intermetallic compounds. Daejeon (ROK): KAIST; (1990) . |